Introduction
The functionality of service stations depends to a great extent on fuel storage tanks, since these elements guarantee the continuous availability of fuel for vehicles, maintaining reserves in optimal conditions and contributing to ensure efficiency and safety in their handling.
This article analyzes fuel storage tanks, their characteristics, their importance in service stations, the types that exist, technological innovations to improve their safety and efficiency, and how to maintain them properly.
What are fuel service stations?
These are commercial facilities dedicated to the supply of different types of vehicle fuels, such as gasoline and diesel. These stations are made up of a series of components and equipment that enable fuel storage, distribution, and safe dispensing, ensuring efficient and safe operation for users and personnel.
Among the main elements that make up a service station are the fuel storage tanks, the dispensers that measure and supply fuel to vehicles, the piping system and valves that connect the tanks to the pumps, and the safety systems.
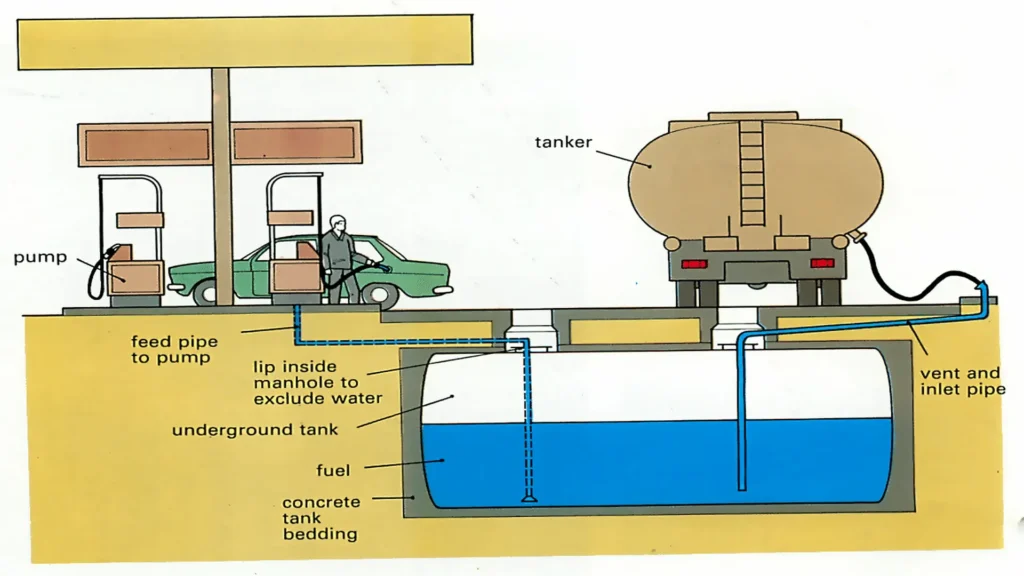
What are fuel storage tanks for service stations?
These are containers specially designed to efficiently and safely store liquid fuels such as gasoline and diesel for vehicle fueling. These fuel tanks, which may be installed subway or above ground, are generally made of steel or fiberglass and may have internal compartments for storing different products with different characteristics.
They incorporate sensors for low and high product level control, ventilation to control pressure and prevent vapor accumulation, as well as advanced safety systems, such as leak detectors that help prevent accidents and protect the environment by avoiding spills or leaks. In addition, they are connected to the dispensers by supply lines, allowing a controlled and safe flow of fuel.
Main characteristics of storage tanks
They have different technical characteristics depending on the type of installation and the applicable safety regulations. Among these characteristics, the following stand out:
Types of fuel storage tanks for service stations
There are two main types; subway and aboveground fuel tanks. Their characteristics are described below.
Subway tanks: They are the most common type in service stations due to their ability to maximize available space. These tanks are buried underground, in order to protect them against physical damage and reduce fire hazards, and are manufactured as single or double-wall tanks.
- Single-walled: They are made of a single wall and have a corrosion-resistant coating. Although they are economical, they present the risk of fuel leakage to the ground in case of breakage of the single wall.
- Double-walled: Double-walled tanks have two walls, one internal and one external, which provide greater safety by preventing leaks from reaching the environment. Between the two walls there is a space where the leaked product is retained, which is detected by the safety systems, allowing the appropriate actions to be taken. Although they are more expensive and require more space, they have better impact protection and less risk of contamination.
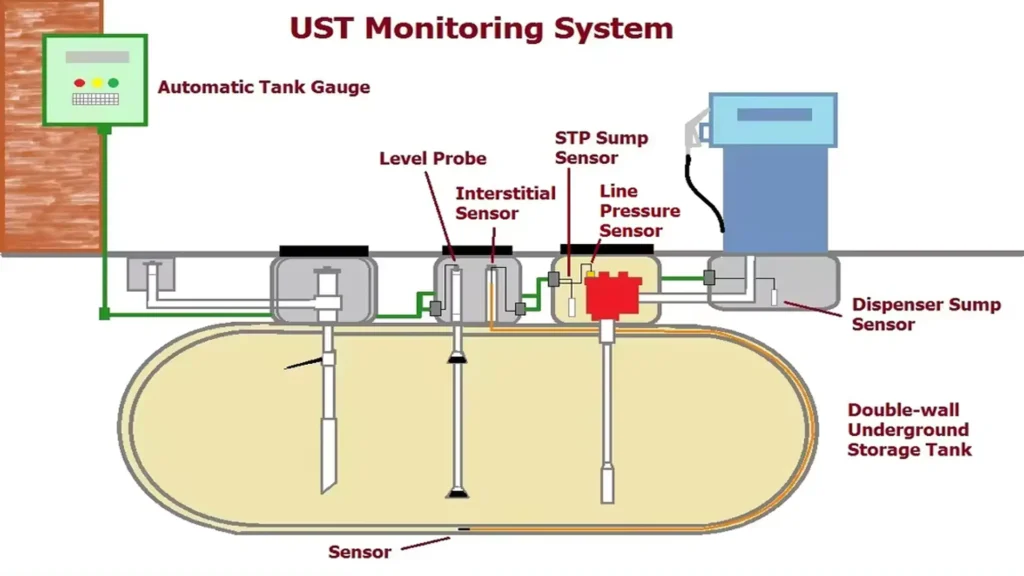
- Aboveground tanks: Aboveground tanks are installed above ground, making them easily accessible for inspection and maintenance. They are more common in areas where subway space is limited or where soil conditions do not permit the installation of buried tanks. Their cost is lower, but they have greater exposure to physical damage and higher risk of fire due to direct exposure.
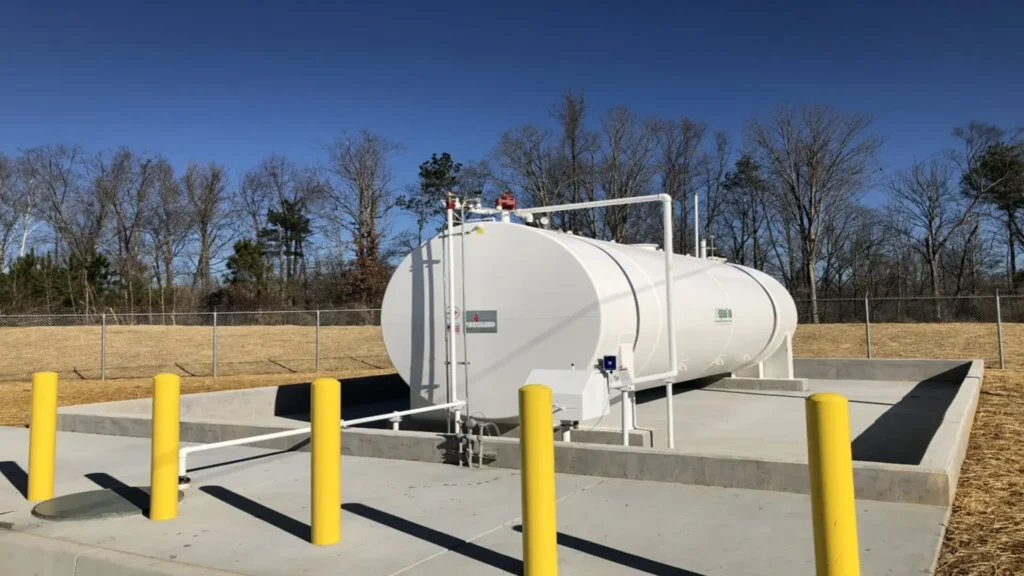
Storage capacity It depends on several factors such as:
- Fuel demand: In areas with higher traffic, storage capacity tends to be higher to meet supply needs without interruption.
- Supply frequency: If the station receives frequent supplies, it may operate with smaller capacity tanks. On the other hand, stations in remote areas tend to have larger tanks.
- Local rules and regulations: Tank capacity and construction standards are regulated by environmental and operational safety laws and regulations in each country or region.
- Physical space available: Space limitations at the service station may affect the number and size of tanks that can be installed.
- Construction material: The materials used in the manufacture of fuel tanks and their accessories must be compatible with the products to be stored. Generally, they are made of steel or fiberglass-reinforced polymers (GRP).
- Steel tanks: They are welded equipment resistant to external loads from soil and traffic, but susceptible to corrosion, so internal and external anti-corrosion coatings must be applied to protect the subway tanks from the aggressiveness of the soil, groundwater, and stored products. For external corrosion control, sacrificial anode or impressed current cathodic protection systems are used.
- Fiberglass reinforced polymer (GRP) tanks: They tend to have higher initial costs than steel tanks, however, installation and maintenance costs are lower, as they are lighter to assemble and do not require cathodic protection or corrosion coatings. They are very resistant to corrosion, but more flexible than steel and more susceptible to deformation under excessive pressure, therefore, they need to distribute loads uniformly. In addition, fiberglass, being lighter, increases the risk of flotation in areas with high groundwater.
Installation and characteristics of soil for subway tanks
The installation of subway tanks must be done in stable soils that can support the weight of the tank and the fuel, considering the construction materials of the tanks. It is important to consider that the soil has good drainage capacity to avoid water accumulation and also, depending on the construction material, the following should be considered:
- For steel tanks: Backfill should be granular, such as sand, fine gravel or soil mix that does not contain large stones or hard materials that could damage the corrosion-resistant coating of the tank. Compaction should be uniform, using light machinery or hand compactors in the vicinity of the tank to avoid applying direct compressive loads that may affect the shape of the tank.
- For fiberglass tanks: The backfill material should preferably be clean, fine sand or gravel, free of stones or fragments that could cause wear or damage to the tank walls. The backfill should be dense enough to provide structural support and compaction requires even more care than for steel tanks, as it is more susceptible to deformation under excessive pressure. The compaction process should be done with light equipment or manually near the tank to avoid generating excessive lateral pressure.
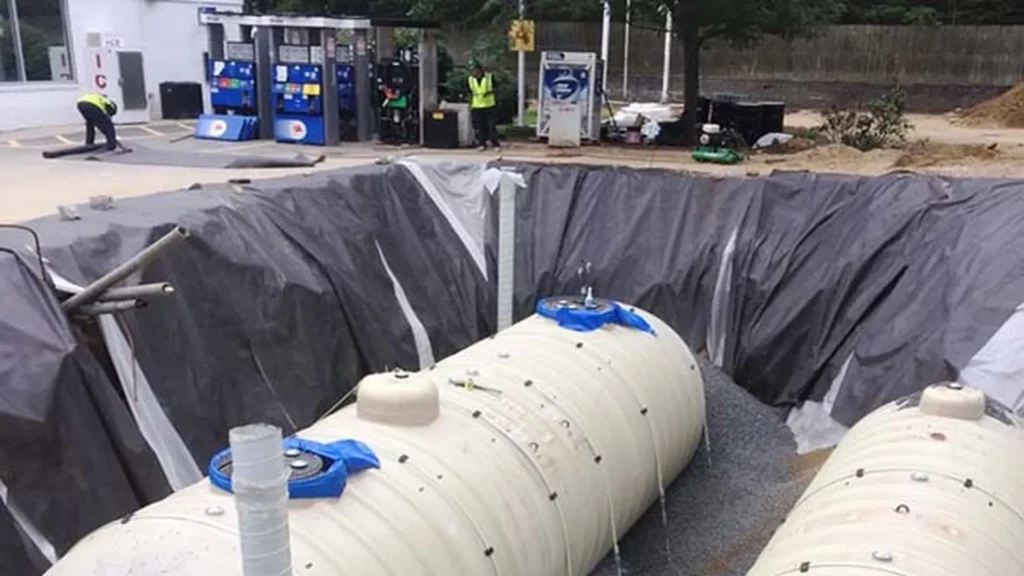
Technological innovations to improve safety and efficiency
- Advanced monitoring and leak detection systems: Technological innovations have enabled the development of advanced monitoring systems in fuel storage tanks that accurately detect any possible leaks. These systems include interstitial sensors in double-walled tanks and automated alerts that allow for rapid intervention in the event of any anomaly.
- Product automation and inventory control: Enables service stations to efficiently manage their fuel stocks. Automated systems can measure fuel levels in real time, helping to avoid stock-outs and maintain tight inventory control.
- Sensors for leak detection: Sensors installed in the tanks can detect any leaks in their early stages, alerting operators to take immediate corrective action. This is essential to avoid serious environmental problems.
- Ventilation systems: Storage tanks have venting systems that allow for the controlled release of vapors to prevent the accumulation of flammable gases and reduce the risk of explosions.
- Piping: The piping used to connect tanks to service stations has improved thanks to new materials with fiberglass that better resist corrosion and temperature changes and do not allow static electricity buildup that could cause a fire.
Subway pit
Traditionally, a sand or soil backfill system has been used around tanks to provide structural support and minimize the risk of leaks. However, the following more advanced and safer options are available to provide a greater barrier against potential leaks.
Geosynthetic membranes
These are synthetic layers designed to be impermeable and retain any possible hydrocarbon seepage. It is placed at the base and sides of the excavation, creating an additional barrier that prevents fuel from seeping into the subsoil.
Concrete walls
They act as a physical barrier to retain the fuel in case of leaks. They can be built on the perimeter of the pit or as an additional barrier in the area where the tank will be located. The concrete used should be of high density, with specific additives to resist contact with hydrocarbons, and reinforced with an additional waterproofing layer applied on the surface of the concrete.
System combination
In some installations, both a geosynthetic membrane and concrete walls are used, known as a double containment system. This method provides an additional level of safety and is highly recommended in environmentally sensitive areas or where there are stricter regulatory requirements.
Subway and aboveground tank maintenance
Regular maintenance of fuel storage tanks is crucial to ensure their long-term safety and efficiency. For subway tanks, it is important to regularly inspect corrosion protection systems as well as leak detection systems. For aboveground tanks, structural integrity, piping connections, and venting systems should be checked periodically. In addition, internal tank cleanings are essential to prevent the accumulation of residues that can compromise fuel quality.
Standards and regulations
Underwriters Laboratories (UL) establishes requirements for the safety, construction, installation, and use of storage tanks for flammable and combustible substances. Each standard has a specific focus:
- UL-58: Applies to steel subway storage tanks for flammable and combustible liquids. Specifically, it establishes design, construction, and testing requirements for subway tanks.
- UL-142: Specifies designs and fabrication of aboveground tanks for flammable and combustible liquids.
- UL-1746: Focuses on subway steel tanks with corrosion-resistant protective coatings. Covers both the fabrication and installation of steel tanks protected with corrosion-resistant coatings for flammable and combustible liquids.
- UL-1316: This standard regulates fiberglass-reinforced tanks for subway storage of flammable and combustible liquids.
Conclusion
Fuel storage tanks are significant components in the safe and efficient operation of a service station. The correct choice, installation, and maintenance of these systems, together with the implementation of technological innovations, ensures not only the protection of the environment, but also the safety of the people who interact with them on a daily basis.
References
- How a petrol station Works (s,f). https://www.howacarworks.com/illustrations/how-a-petrol-station-works
- UST Monitoring Systems – How They Work and Why Every Tank Owner Needs Them (s,f). https://www.commtank.com/tank-articles/underground-storage-tank-monitoring-systems/
- Fueling System Design: Aboveground vs Underground Fuel Storage Tanks. 2023. https://unitedpump.com/fueling-system-design-aboveground-vs-underground-fuel-storage-tanks/
- Mobil Gas Service Station – Underground Storage Tank, Dispenser and Product Piping Installation. (s,f). https://www.commtank.com/projects/commercial/mobil-gas-station-underground-storage-tank-and-dispenser-installation/