Table of Contents
Introduction
In the manufacturing and construction industry, welds in piping and process equipment are an indispensable part; however, during the application of welds, residual stresses and changes in the microstructure of the material are generated that can compromise the quality and durability of the joints if they are not properly controlled.
To mitigate these effects and ensure optimum performance under demanding operating conditions, various heat treatments are applied. These treatments, which involve controlled heating and cooling of the material, not only relieve stresses, but also optimize properties such as hardness, ductility, and corrosion resistance. In addition, there are specialized heat and surface treatments that improve the external characteristics of materials to withstand friction and abrasive environments.
In this article, we will explore the types of heat treatments applied to welds in piping and process equipment, detailing their benefits, procedures, and the regulations governing their correct application in the industry.
What are heat treatments in welding?
Heat treatments in welding are processes by which scale-controlled heating, holding, and cooling heat is applied to a weld to modify the structure of the base material and the filler material, thus achieving specific mechanical and physical properties. These treatments seek to relieve internal stresses, improve strength or harden the material, depending on operational needs.
Common types of heat treatments in welding
- Annealing: It is used to relieve internal stresses generated during the welding process, reducing hardness and improving ductility. It is common in pipelines carrying corrosive fluids to ensure a homogeneous structure.
- Normalizing: Used to refine the grain structure of the material and improve its mechanical strength. This process is vital for pipes and equipment that work at moderate temperatures and require a uniform and stable metallographic structure.
- Quenching and tempering: These two processes combined are used to increase the hardness and strength of the welded material. Quenching consists of heating the part and quenching it rapidly (usually in water or oil), followed by tempering, which heats the part to a lower temperature to relieve the stresses induced by quenching, improving toughness without sacrificing hardness.
- Hydrogen removal: It can be considered as a heat treatment, but with a specific objective; to remove the hydrogen trapped in the material. It is not a heat treatment in the classical sense, such as annealing or quenching, which seek to modify the mechanical properties or microstructure of the material. But it does involve the controlled application of heat to achieve a desired effect. The main objective is to prevent hydrogen-induced cracking, which occurs when trapped hydrogen combines with residual stresses and/or susceptible microstructures in the weld, which could lead to failure.
- Solubilization treatment: Applied mainly to austenitic stainless steels, this heat treatment eliminates carbides and restores the homogeneous composition of the alloy, preventing intergranular corrosion in aggressive environments.
- Surface heat treatments: Surface heat treatments are essential to improve the characteristics of the outer layer of the material, without affecting its core. These treatments are applied when welds or process piping and equipment need a hardened surface to resist wear or corrosion. The most common methods are:
- Carburizing: Applied to steels to increase their surface carbon content, followed by quenching to harden the outer layer. It is ideal for equipment exposed to continuous wear, such as pumping parts and valves.
- Nitriding: A treatment where nitrogen is diffused into the surface of the steel, increasing its hardness and wear resistance. This process is performed at lower temperatures than case hardening and is less likely to deform the structure of the part.
Heat treatment application
Heat treatments on welds are performed using the furnace and electric resistance methods. Each method is explained below:
Furnace treatment
It is used for parts that can be moved to a large oven, ideal for processes that require precise temperature control. The part is introduced into the furnace (gas or electric), programmed to heat gradually according to the material and treatment required. Once the temperature is reached, it is held for the time necessary to transform or stabilize the microstructure of the material, and then slowly cooled to reduce stresses and prevent cracking or deformation.
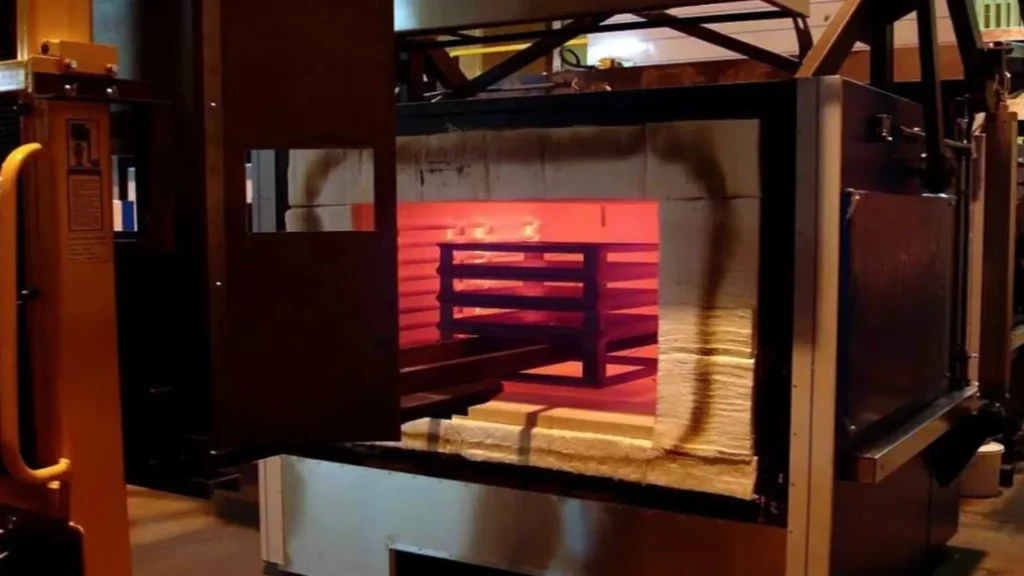
Electrical resistance treatment
It is a field standard, especially when parts cannot be moved. It is ideal for welding on piping, structures, and other fixed components in plant. Electric heaters are flexible devices with internal heating elements that are placed around the welded area, adapting to different shapes and sizes for localized area treatment.
To monitor and control the temperature in real time, thermocouples are connected to the solder area, and the electrical resistors are operated by a control panel that allows temperature regulation. The operator adjusts the heating following a specific heat treatment curve, ensuring that the solder and the adjacent area are heated uniformly. Once the treatment temperature is reached, it is maintained for the required time and then a controlled cooling is performed, reducing the temperature gradually to avoid thermal stresses.
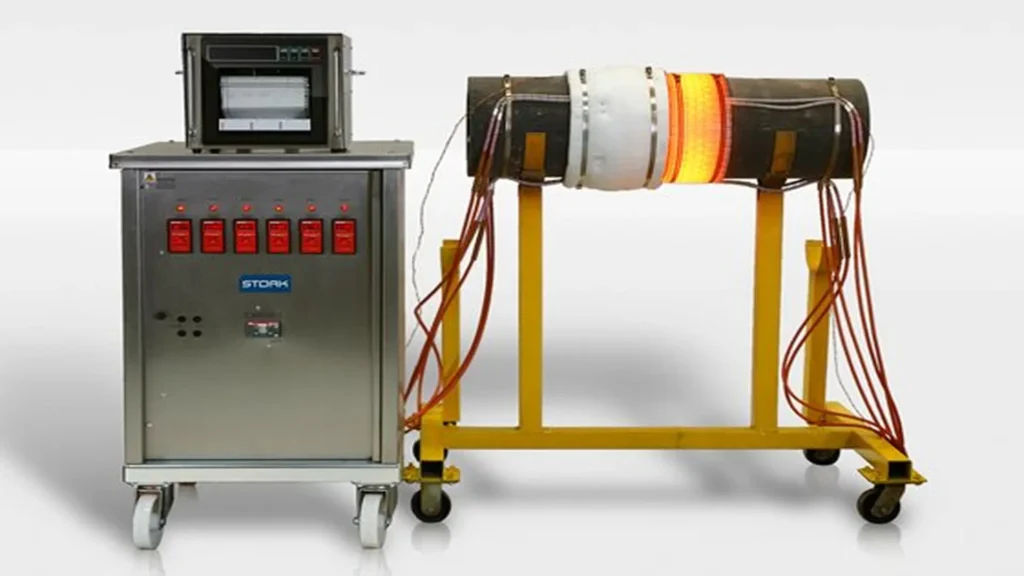
The main advantages of this method are its flexibility for field work and for treating components that cannot be moved, its quick installation and application, and the possibility of treating welds in specific areas without affecting other areas of the equipment. However, it has limitations, such as lower accuracy in uniform heat distribution compared to a furnace and the need for constant monitoring to ensure that temperatures are maintained within specified parameters.
Advantages of heat treatments on industrial welds
The main advantages are:
- Residual stress reduction: Heat treatments relieve stresses generated during welding, which reduces the possibility of premature deformation and failure. This is especially important in long pipes, where accumulated stresses could cause distortions.
- Mechanical strength improvement: Normalizing and quenching significantly improve material properties, optimizing fatigue and wear resistance. This is vital in process equipment that undergoes intense thermal and mechanical cycling.
- Weld defect prevention: Applying proper heat treatment minimizes common defects such as cracks and other irregularities that could compromise the integrity of the welded joint, thus improving the final quality of the product.
Key considerations for heat treatment implementation
Selection of the appropriate treatment: The choice of heat treatment depends on the type of material and the specific application. For example, carbon steels require a different type of annealing than stainless steels, which may require quenching and tempering to optimize strength.
Parameter control: To ensure the effectiveness of the treatment, the heat treatment curve must be followed and it is essential to precisely control the temperature, holding time, and cooling rate. These parameters must be carefully monitored to avoid defects such as embrittlement or undesired changes in the mechanical properties of the material.
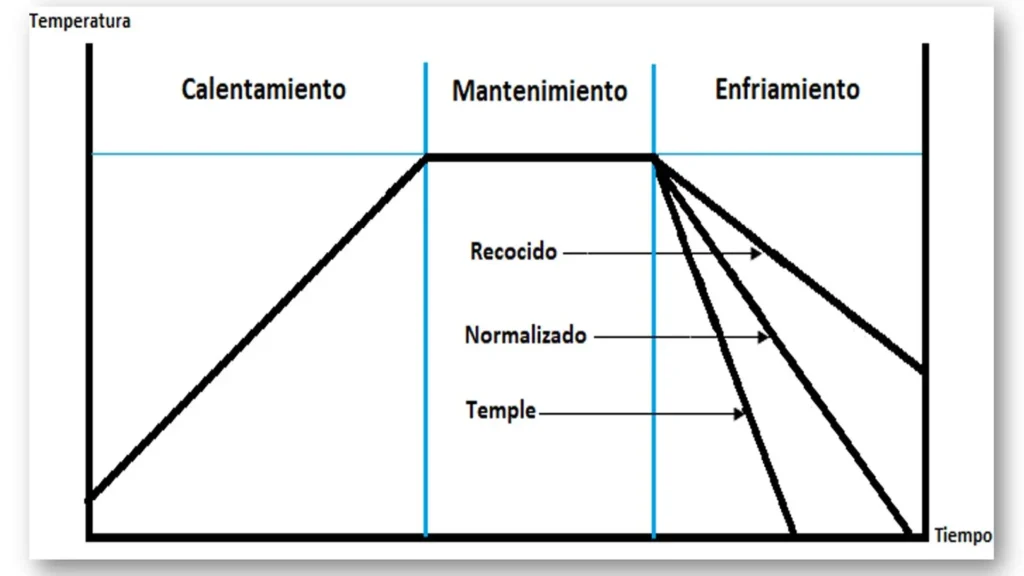
Equipment and techniques used: In the industry, portable equipment and advanced monitoring and precision furnaces are used to apply heat treatments in a uniform and controlled manner. Modern technologies allow parameters to be adjusted in real time, ensuring accurate and effective treatment.
Challenges and best practices in heat treatment
- Common challenges: One of the biggest challenges is to avoid deformation and unwanted changes in material properties. Materials with high thermal sensitivity require extremely precise temperature control to avoid damage.
- Best practices: It is advisable to use precision furnaces that offer accurate temperature control and real-time monitoring systems to record treatment parameters. In addition, it is crucial to perform post-treatment inspection tests to ensure the quality of the welds.
Conclusion
Heat treatments on pipeline and process equipment welds are critical to ensure safety and operational efficiency in industries such as petrochemicals and refineries. These treatments improve the durability of welded joints, and minimize defects and residual stresses that compromise the structural integrity of components.
References
- https://caltherm.co.uk/heat-treatment-furnaces-and-ovens/
- https://www.stork.com/en/capabilities/equipment/heat-treatment-equipment
- https://badgatostudios.com/en/normalizado-la-clave-para-fortalecer-tus-materiales#google_vignette