Table of Contents
- Introduction
- What is a flanged joint?
- Most common causes of flanged joint failures
- Inspection of flanged joints and applicable standards
- Maintenance of flanged joints
- Best practices to prevent flanged joint failures
- Risks due to flanged joint failures
- Best practices to prevent flanged joint failures
- Conclusion
- References
Introduction
Flanged joints are key elements in process piping systems, allowing secure and flexible connections for ease of maintenance, inspection, and system modification. Despite their importance, these joints are prone to various failures that can significantly compromise the safe and efficient operation of industrial facilities.
This article details the common causes of flanged joint failures, examines best practices for their prevention and maintenance, identifies the risks associated with their failure, and answers key questions about their management and diagnosis.
What is a flanged joint?
A flanged joint is a connection system used to join pipe sections and install fittings and equipment such as valves or pumps to these pipes. This consists of two mating flanges, a gasket that seals the joint, and a set of screws, bolts or studs that secure the flanged joints, as shown in Figure 1. This configuration allows easy disassembly and access for inspection or maintenance.
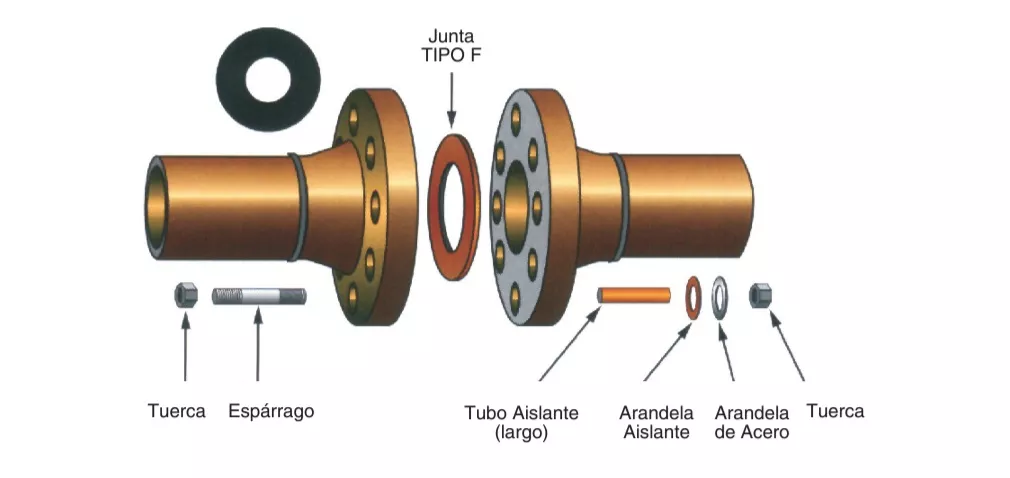
Most common causes of flanged joint failures
In addition to the previously mentioned causes, cause-effect analysis of flanged joint leaks reveals that lack of attention to detail during material selection and installation can have disastrous consequences, such as:
- Non-compliance with standards: Failure to adhere to established standards for design, installation, and maintenance of flanged joints greatly increases the risk of failure.
- Inadequate inspection and maintenance: Lack of regular inspections and poor maintenance allow minor problems to evolve into critical failures.
- Improper material selection: Choosing flanges, gaskets or fasteners that are incompatible with the process fluid or operating conditions can lead to corrosion, erosion, elongation, and, ultimately, failure.
- Damage to the finish or roughness on the flange face: The different types of roughness on the flange faces are determined for an optimum and reliable seal. One of the most common damages in the flange is the loss or damage of this finish, caused during the disassembly of the flanges, misuse of the wedges and by blows or fission that diminish the quality of the seal and originate product leakage.
- Elongation of screws, bolts or studs: This is usually caused by poor fit and the use of inadequate material.
- Assembly error: Incorrect alignment, uneven or inadequate tightening of bolts and improper use of tools can generate uneven stresses in the joint, causing leaks or structural damage.
- Wear and fatigue: The continuous cycling of fluctuating pressures, vibrations and temperatures can fatigue materials, leading to misalignment, cracks and leaks.
- Corrosion: Exposure to corrosive environments, both internal and external, can deteriorate flanges, gaskets and fasteners, reducing their service life and effectiveness.
Inspection of flanged joints and applicable standards
Inspection of flanged joints should be performed according to non-destructive testing criteria such as those established by the American Society for Nondestructive Testing (ASNT) and verify that design criteria are met in accordance with international and local standards and recommended practices. These include the standards of the American Society of Mechanical Engineers (ASME), American Society for Testing and Materials (ASTM) and the International Organization for Standardization (ISO).
These inspections should focus on identifying signs of wear, misassembly, deformation, inadequate materials and out-of-design sizing of parts, corrosion and structural damage.
Maintenance of flanged joints
Preventive maintenance is vital to prolong the life of flanged joints and avoid premature failure, including:
- Periodic inspections to identify early signs of problems.
- Replacement of worn or damaged components.
- Retighten screws according to specifications.
How do I know if a flange is damaged?
Identifying a damaged flange requires visual inspection and, in some cases, more advanced techniques such as ultrasound or radiographic testing. Common signs of damage include:
- Deformation: Changes in the shape of the flange may indicate excessive stresses or improper installation.
- Corrosion: The presence of corrosion on the flange surface or near the gasket, as shown in Figure 2, suggests poor sealing or inadequate material selection.
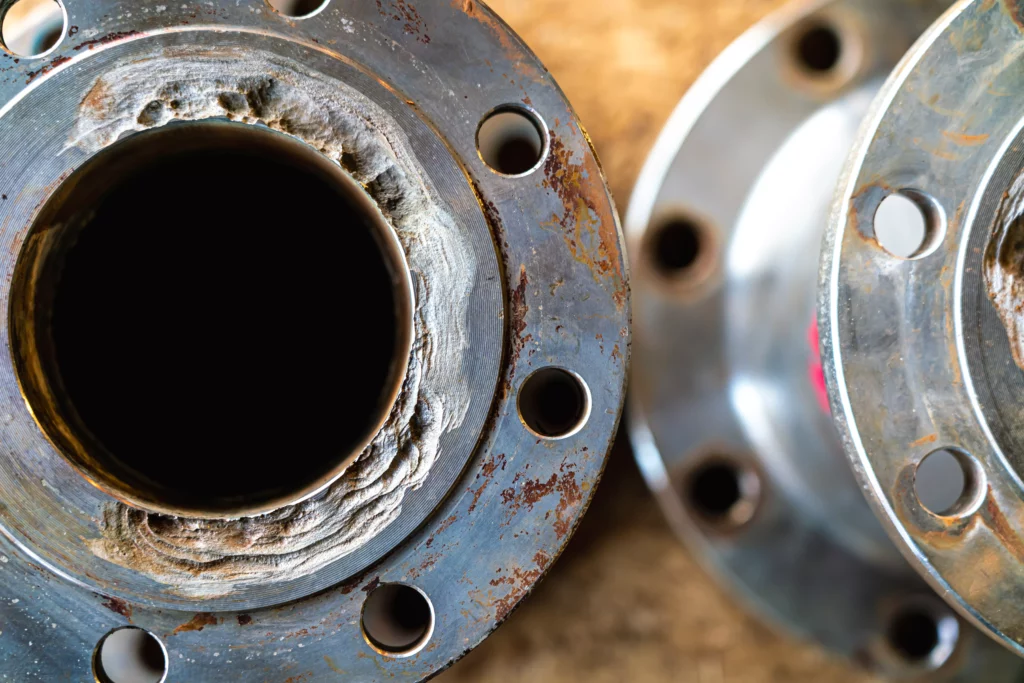
- Visible leaks: The presence of moisture, condensation or deposits around the joint may indicate an active leak.
Best practices to prevent flanged joint failures
Incorporating standards and regular inspection as crucial components of best practices reinforces the importance of:
- Adherence to standards: Strictly follow applicable standards in the design, material selection, installation, and maintenance of flanged joints.
- Detailed inspections: Verify that each of the flanged joint parts before and during assembly meet the design and installation specifications, also perform regular and thorough in-service inspections to detect any signs of wear or damage, applying non-destructive and advanced testing techniques such as the phased array ultrasound (PAUT) as shown in Figure 3.
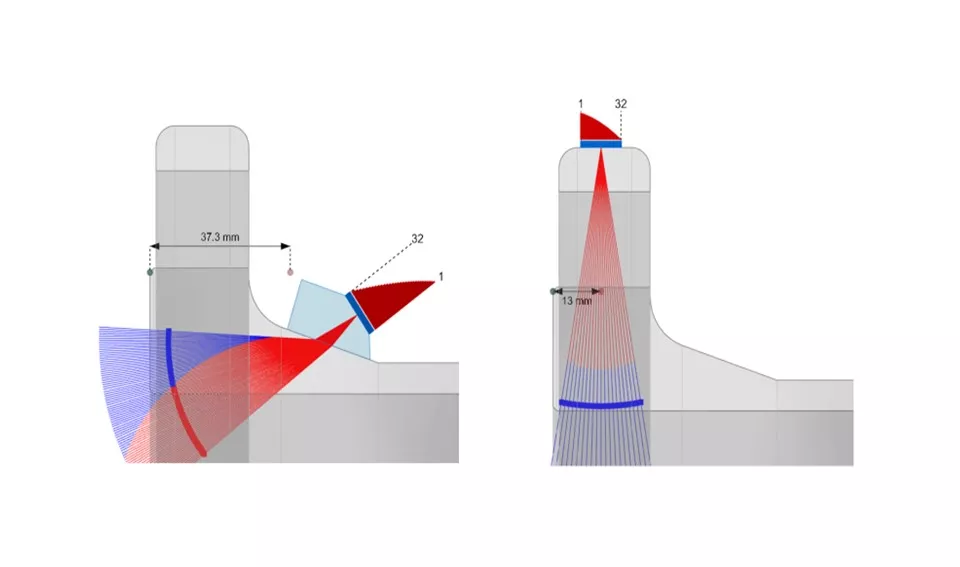
Risks due to flanged joint failures
Flanged joint failures can have serious consequences, including:
- Fluid leaks: Can cause environmental damage, health risks and significant economic losses.
- Fires and explosions: In case of leakage of flammable or toxic fluids, the risk of fire or explosion increases considerably (Figure 4).
- Unscheduled shutdowns: Failures can lead to emergency shutdowns, affecting production and generating high costs.
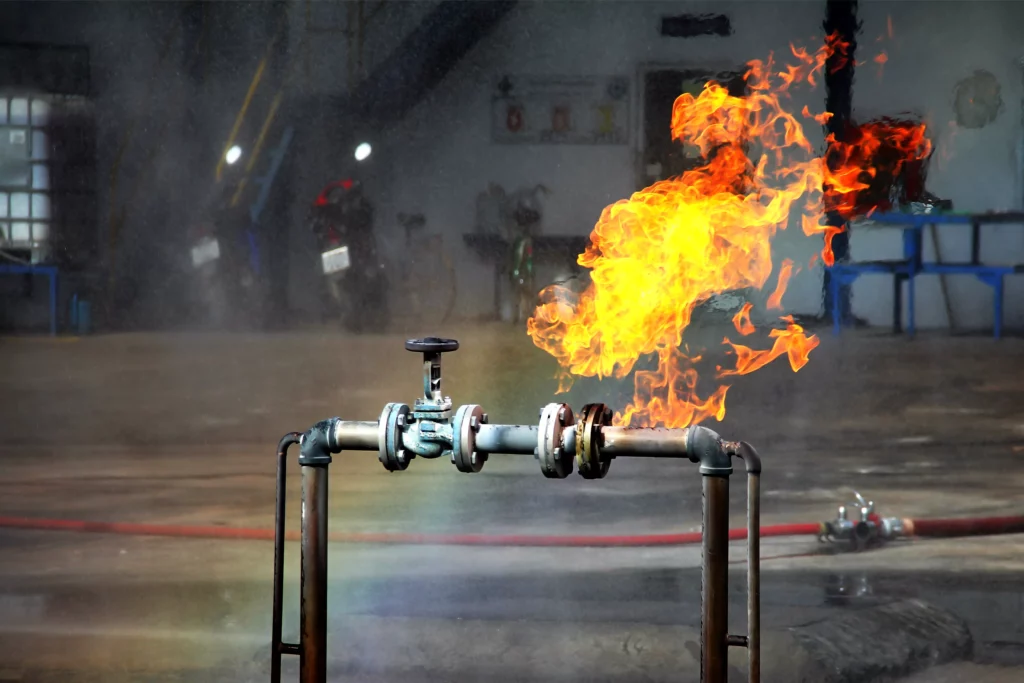
Best practices to prevent flanged joint failures
To mitigate the risk of flanged joint failures, a number of best practices should be adopted in their design, selection, installation and maintenance:
- Careful selection of materials: Ensure compatibility of all joint components with the process medium and operating conditions.
- Accurate installation: Follow recommended specifications and tightening sequences, using calibrated tools and ensuring correct alignment.
- Proactive inspection and maintenance: Perform regular inspections looking for signs of wear, corrosion or fatigue failures, and carry out preventive maintenance.
- Continuous training: Train personnel in the correct installation and maintenance practices of flanged joints to avoid human error.
Conclusion
Flanged joints are critical to the integrity and efficiency of process piping systems. Through a detailed understanding of what constitutes a flanged joint, the common causes of its failure, and the implementation of best practices for its selection, installation, and maintenance, it is possible to significantly mitigate the associated risks. Adherence to established standards and meticulous inspections are essential to ensure the safe and reliable operation of these critical connections.
References
Own source