Table of Contents
Introduction
CO2 corrosion in hydrocarbon pipelines is a critical phenomenon that can compromise the structural integrity and safety of the facilities. CO2 is a byproduct generated in oil and gas production and refining processes, which interacts with metal in pipelines, triggering corrosive mechanisms that must be addressed effectively.
CO2 corrosion
CO2 corrosion is one of the most aggressive and frequent forms of corrosion in hydrocarbon industry facilities. This product is very corrosive when it chemically reacts with an aqueous phase, which is normally present in petroleum production. This reaction forms carbonic acid, which is very aggressive for carbon steels.
The most general forms of CO2 corrosion in carbon steel materials is localized corrosion in the form of pits, as shown in Figure 1. The table type, in some cases, can occur in the form of parallel channels that They extend in the direction of flow and are known as localized flow-induced corrosion.
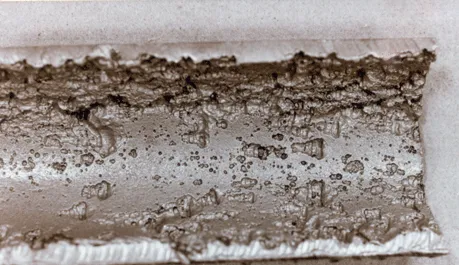
Classification of CO2 corrosion
The type of CO2 corrosion on carbon steel could be classified in three ways:
- Pitting: Pitting can occur throughout the temperature range in low flow, stagnant to moderate flow operation. Pitting can also occur near the dew point, related to condensation. Pitting decreases with increasing temperature and partial pressure of CO2.
- Table type attack: It is a form of localized CO2 corrosion that occurs under medium flow conditions, due to the instability of protective iron carbonate layers. It is the type most found where there is high fluid turbulence, such as welding and changes in fluid direction, among others.
- Localized flow-induced corrosion: It is an extension of pitting and table attack above the critical flow (greater than 5 m/sec). The attack propagates by the local turbulence created by the pits and the table that act as a disturbance of the flow, forming parallel channels that extend in the direction of the flow.
Factors affecting CO2 corrosion
CO2-induced corrosion is a complex process, generated by the following factors: aqueous humidity, pH, temperature (T) and partial pressure of carbon dioxide (p CO2 ), flow rate, CO2 concentration. Below is a brief description of some aspects related to these parameters:
- Water content: Water content is a determining factor in metal corrosion. The variation of corrosion rates increases with increasing humidity. Excessive water content will cause electrochemical corrosion, which will severely corrode the pipeline, decreasing the service life of the pipeline.
- CO2 concentration: The higher the concentration of carbon dioxide in the environment, the faster the corrosion process.
- Partial pressure of CO2: The partial pressure of carbon dioxide can also influence CO2 corrosion, as this variable increases, the corrosion process accelerates. The partial pressure in the gas phase is considered directly proportional to the concentration of CO2 in the gas phase. This pressure is determined by analyzing the content of a gas sample and making the calculation using the following equation: Once the mol% of the CO2 gas is measured, in relation to the complete gas sample, this concentration in moles is Multiply by the total pressure to calculate the partial pressure of CO2.
p CO2 = P x mol % CO 2
Where: P is the pressure in the well, p CO2 is the partial pressure of CO 2 and mol% is the concentration of CO 2 in the mixture, measured in mole percent.
- Temperature: When the temperature changes, parameters are affected that in turn affect CO2 corrosion. of carbon steel. In general, the corrosion rate increases with increasing temperature. However, in some cases, very low temperatures can also increase the risk of corrosion.
- Presence of impurities: The presence of impurities in CO2, such as organic acids or sulfides, increases the aggressiveness of the corrosive medium.
- Flow speed: The flow speed can affect the corrosivity in the pipes, since the permanence of the protective film on the walls of the pipes largely depends on it. When the fluid velocity is below 1 m/s, the corrosion rate increases in media with CO2, due to a mass transport mechanism, but if the velocity is slightly above 1 m/s, the increase in the Corrosion is not as accelerated when the speed of the electrochemical reaction controls the corrosion. If the fluid velocity is very high, above 5 m/s, an erosion-corrosion phenomenon may occur due to the removal of the protective iron carbonate films and the corrosion inhibitors that are present.
- pH of the medium: In environments with an acidic pH, corrosion can be more aggressive. pH has a significant effect on corrosion from the point of view of its impact on the solubility of iron carbonate. The solubility of the corrosion products decreases when the pH increases, producing a supersaturation of the iron carbonates, which in turn allows the acceleration of precipitation and formation of protective films on the metal substrate.
Evaluation of the corrosivity of CO2 in hydrocarbon pipelines
How corrosive is CO2 really? To answer this question, it is necessary to analyze the operating conditions, CO2 concentration and other environmental factors. Temperature and pressure, and the presence of contaminants in the gas, play an influential role in the aggressiveness of CO2 in terms of corrosion.
CO2 Corrosion Mitigation Strategies
Preventing CO2 corrosion It is imperative to ensure the long-term integrity of hydrocarbon pipelines. The following mitigation strategies have been developed and refined to address this challenge:
- Corrosion Inhibitors: The application of corrosion inhibitors is used to protect metals from CO2 corrosion. These chemicals are added to the medium, generating a protective film on the walls of the pipe. Among the most used corrosion inhibitors in the hydrocarbon industry are amines, amides, and imidazolines as nitrogenous compounds. Its protection mechanism basically consists of the adhesion of the inhibitor on the surface of the metal, creating barriers that prevent the action of corrosive agents.
- Coatings: The application of corrosion-resistant coatings on the internal surface of pipes is a commonly used control method. These coatings act as physical barriers, protecting the metal from direct exposure to CO2 and the corrosive environment. These coatings are manufactured based on epoxy compounds, urethanes, polyurethanes and other polymeric compounds.
- Metallurgy of materials: A quite successful, but expensive alternative to resist the aggressiveness of CO2, is the use of materials resistant to this type of corrosion. Nickel or chromium alloys offer greater strength , greatly reducing the vulnerability of pipes to corrosive effects.
- Control of operational variables: Maintaining strict control over the operational variables that can affect the corrosivity of CO2 is one of the most important forms of preventive control. If the operational variables are kept within the design parameters of temperature, humidity, fluid velocity, pressure and fluid characterization, the corrosion rate would be kept in control within the parameters considered in the design.
- Design: From the design, all the parameters that affect CO2 corrosion must be taken into consideration. The designer must work together with corrosion engineers and understand the factors that contribute to CO2 corrosion, which is very important to design equipment with adequate corrosion protection, so that its life is not less than its cycle. of life. Material selection, environment, control measures, welding and treatment procedures must be addressed early in the design phase to establish an optimal and reliable solution.
Continuous research and development
The understanding of CO2 corrosion continues to evolve, and continued research is significant to develop more effective mitigation strategies. Investing in research and development is essential to advance corrosion management practices. This includes developing innovative corrosion-resistant materials, exploring new inspection and monitoring techniques, improving corrosion modeling and prediction. Collaborative efforts between industries, academic institutions and research organizations can lead to the development of sustainable and effective corrosion management solutions.
Prevention of CO2 corrosion and associated risks
Effective prevention of CO2 corrosion not only involves the application of mitigation strategies, but also the evaluation and management of associated risks. Early identification of areas susceptible to corrosion and implementation of preventive measures are important to minimize the impacts of this corrosion. Periodic inspection and monitoring, applying Non-Destructive Testing techniques, and measuring the corrosion rate are essential to detect corrosion damage, likewise the implementation of remote monitoring systems and sensor technologies allows the collection of data in real time, which improves corrosion management practices and facilitates predictive maintenance.
Conclusion
CO2 corrosion in hydrocarbon pipelines is a significant technical and operational challenge. Understanding corrosive mechanisms, implementing mitigation strategies and continuous research are essential to preserve the integrity of infrastructure and ensure the safe and efficient management of hydrocarbons.
References
Own source