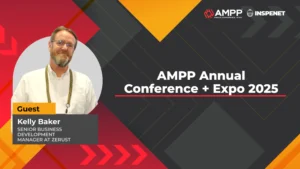
VCI corrosion inhibitor as an effective alternative in industrial protection
At the AMPP event in Nashville, the Inspenet team spoke with Kelly Baker, Senior Business Development Manager at Zerust Integrity Solutions, who explained how VCI corrosion inhibitor (Vapor Corrosion Inhibitor) is changing the way the industry combats corrosion in its critical assets.
Replacing wax with VCI corrosion inhibitors in pipe coatings
For decades, the industry has used wax to fill the interstitial spaces in pipe casing to prevent the ingress of contaminants. However, this method presents significant challenges, such as the fact that, once installed, the wax is difficult to remove. If a failure occurs, operators are forced to drill again, resulting in high costs and operational delays.
Kelly explained that VCI, unlike wax, chemically treats the environment by altering the pH, which neutralizes any contaminants present. Furthermore, it can be easily removed or re-injected, facilitating maintenance without the need for physical intervention in the structure. This approach is not only more versatile, but also represents significant savings in time and resources.
Combination of VCI and cathodic protection in tank bottoms
The use of cathodic protection (CP) under tank bottoms has been an industry standard for over half a century. However, its effectiveness depends on physical contact between the steel and the substrate. This is where VCI complements CP, by diffusing through voids or air spaces between the soil and the steel, it provides coverage that electricity cannot.
Kelly noted that VCI, in addition to protecting these blind spots, also modifies the electrical resistance of the soil, facilitating the even distribution of the CP current and allowing for more complete asset protection. Although implementing both systems may represent an additional cost, the benefit outweighs the investment by significantly reducing the risk of localized corrosion.

VCI in hydrostatic testing projects
In hydrostatic testing, whether on pipelines, tanks, or heat exchangers, the use of untreated water can cause corrosion and generate iron oxide deposits. This complicates cleaning and can affect critical components such as filters.
According to Kelly, applying VCI to the test water reduces the formation of oxides on the system's internal walls, making it easier to clean. Furthermore, in the case of gas pipelines, it reduces the time required for gas re-odorization, a mandatory process after testing. This optimization translates into shorter downtimes and lower maintenance costs.
Zerust: Global Technology Serving Industrial Integrity
Zerust Integrity Solutions, a division of Northern Technologies International Corporation (NTIC), operates in more than 60 countries offering advanced chemical solutions. Its VCI corrosion inhibitors based approach has proven effective in industries such as oil & gas, petrochemicals, marine, and mining, with clients such as Chevron, BP, and Equinor.
According to Kelly, while corrosion can't be completely stopped, it can be slowed, increasing asset uptime and reducing maintenance costs. This is precisely Zerust's mission, to extend the lifespan of industrial infrastructure through smart, adaptable solutions.
For more AMPP 2025 content, visit our YouTube channel and LinkedIn profile.
Source: Inspenet.