At the Agritechnica machinery fair, New Holland (NH) officially presented the CR 11, which stands out not only for being the largest combine harvester in the world, but also for being the only one awarded the gold medal by the Agritechnica organization this year due to its features and manufacturing process.
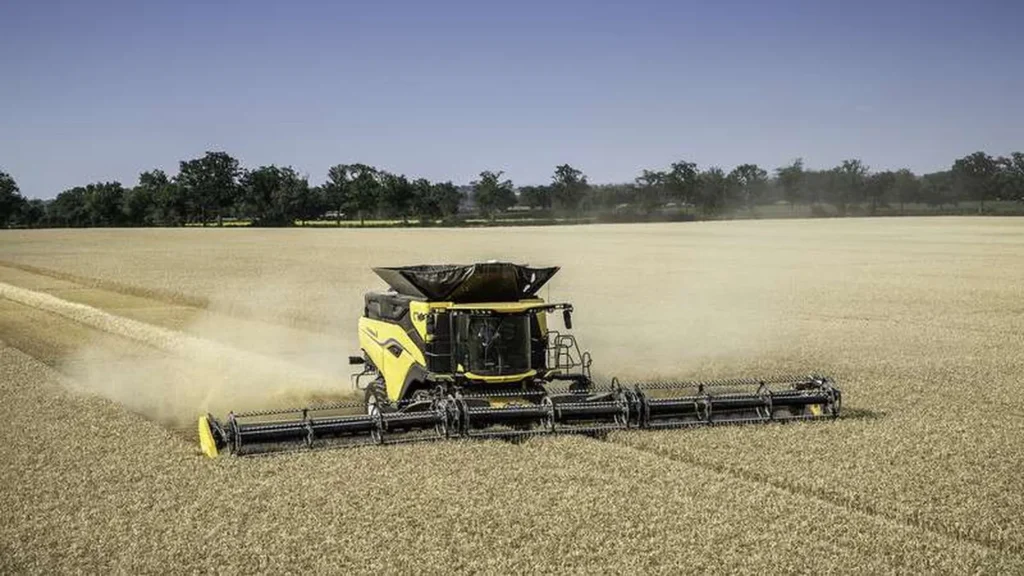
This machine will be produced exclusively at NH’s Harvest Center of Excellence in Zedelgem, Belgium and will begin its introduction in Europe and the United States, with future plans to reach South America in the medium term.
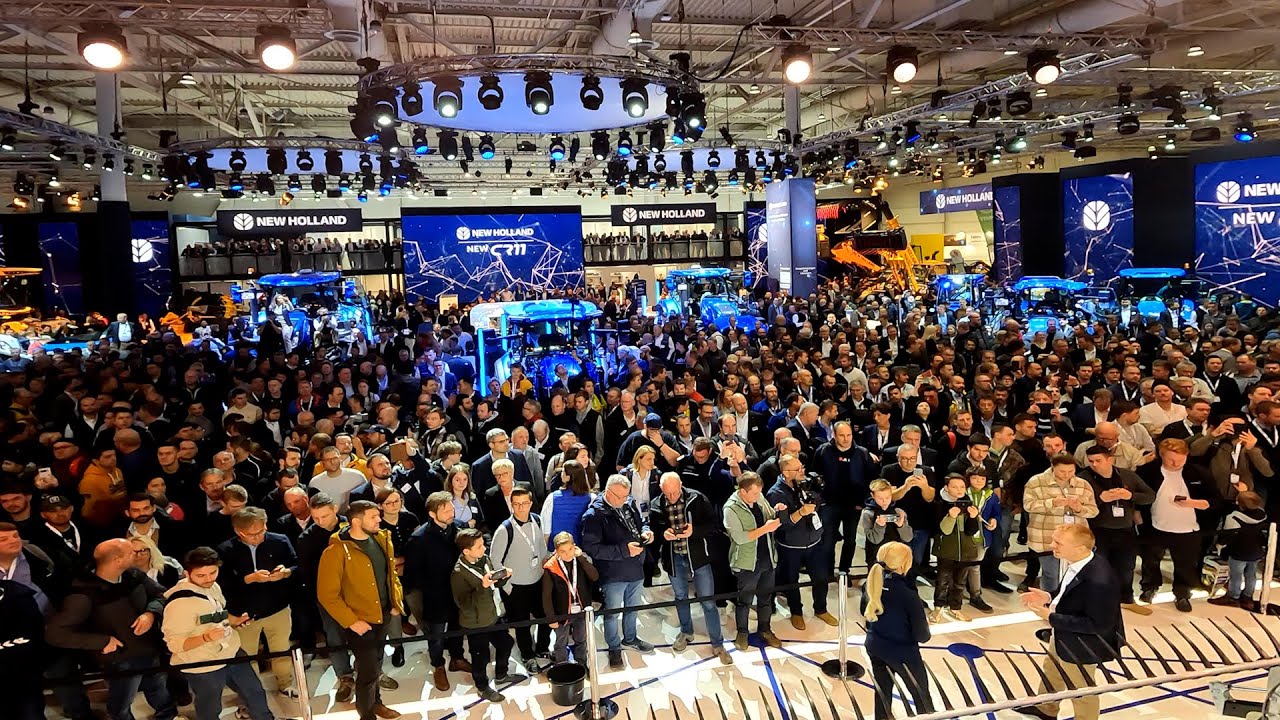
Presentation of the combine harvester during the Agritechnica 2023 trade fair. Source: New Holland Agriculture
CR 11: The largest combine harvester in the world
It is important to note that, until now, the largest combine harvester on record also belonged to New Holland: the CR 10.90, recognized for setting the world record for the largest amount of wheat harvested in eight hours, reaching 797,656 tons.
NH projections indicate that CR 11 increases this capacity by 30% . It is not only about its size, but also about the new productivity standards it offers, its focus on sustainability by reducing grain losses to virtually zero, improving grain quality and efficiently managing waste.
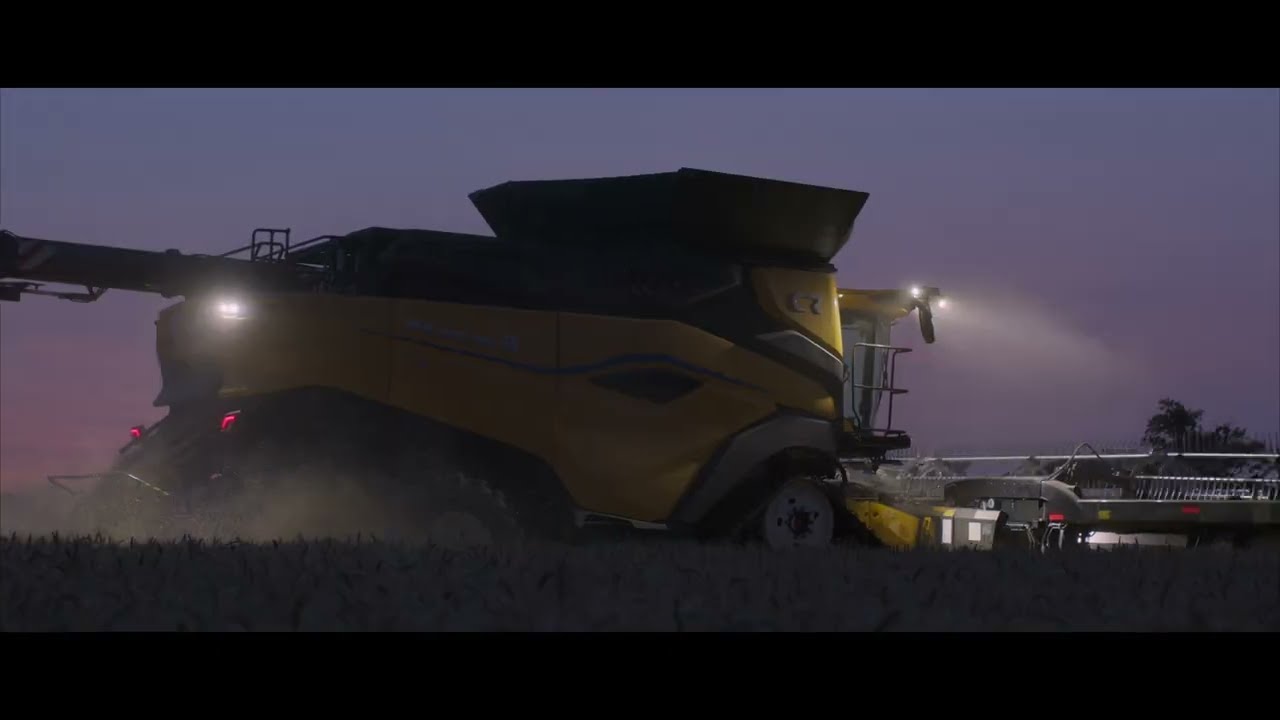
Official presentation of CR 11. Source: New Holland
This is the launch of a new family of combines, the largest in the world, with a header of up to 61 feet. In addition, it stands out for its high capacity and its artificial intelligence system. artificial intelligencesystem, in which all adjustments are made automatically.
mentioned Flavio Mazzetto, one of the brand’s executives.
More details about the CR 11 combine
Thanks to its powerful 775 HP C16 engine, 2×24 inch rotors, a 20,000 liter grain tank and a discharge flow rate of 210 l/second, the largest combine harvester in the world significantly increases productivity, reaching unprecedented levels.
Importantly, New Holland engineers were dedicated to developing a highly efficient harvesting machine, focusing their efforts on the creation of a double cleaning shoe. The innovative Twin Clean cleaning shoe features two consecutive cleaning systems, with 2 upper screens, 2 lower screens, 2 clean grain augers and 2 sets of pressure sensors to evaluate the cleaning shoe load.
The waste residue management completely refurbished incorporates a chopper and straw spreader mechanism designed to ensure superior chopping and uniform residue distribution over a cutting width of up to 60 feet.
Meanwhile, the Intellispread radar system automates spread management to ensure comprehensive and uniform residue coverage at the rear of the combine, regardless of the effects of wind, crop type or moisture conditions. In addition, a new automated method of slug removal has been developed to minimize downtime.
In an industry first, the new Twin Clean is fully automated, ensuring homogeneous cross-distribution of the cleaning shoe, resulting in virtually zero loss levels.
Machinery challenges
Although the new CR11 combine is designed to operate at maximum capacity, New Holland recognizes that it is impossible to completely eliminate the risk of clogging. In the unlikely event that an obstruction occurs, the automatic clearing procedure will guide the operator through a disengagement process to clear the combine in minutes instead of hours, without requiring the operator to leave the cab or exert any effort. physical.
By significantly reducing the downtime associated with such situations, the automatic reverser makes it easy and encouraging the operator to make the most of the combine’s capacity without the fear of getting stuck. Additionally, this feature improves safety by eliminating the need for a person to exit the cab during the automated disconnection process.
Don’t miss any of our posts and follow us on social media!
YouTube LinkedIn Facebook Instagram
Source and photos: New Holland