Bearings are critical components of machinery and are specially designed to reduce friction and provide a bearing surface, allowing rotating equipment components to rotate or move effortlessly. By minimizing friction and wear, bearings ensure that hydraulic power is converted into precise, smooth movements, improving overall equipment performance.
Over time, bearings wear out and require replacement or reconditioning to maintain efficiency and reduce downtime. This article aims to provide information on when to replace bearings in rotating equipment through risk assessment, ensuring operational efficiency and minimizing downtime. In addition, the cost-effectiveness of bearing reconditioning compared to total bearing replacement is evaluated, highlighting the economic benefits.
What is a risk analysis?
Risk analysis is a systematic process used to identify, evaluate and manage potential risks that may affect an existing facility or a project under development. It consists of a careful study of potential hazards, both internal and external, and their possible consequences. This process allows the establishment of appropriate prevention and protection measures to mitigate or eliminate these risks1.
It is important to keep in mind the difference between hazards and risks. A hazard is any event that can cause harm, including workplace accidents, emergency situations, toxic chemicals, employee conflict, stress and more. A risk is the potential for a hazard to cause harm. As part of a risk assessment plan, you must first identify potential hazards and then estimate the risk or probability of those hazards occurring.
This technique does not focus directly on determining when to replace a bearing in rotating equipment specifically, but rather on assessing the potential hazards associated with the continued operation of worn or defective bearings.
Risk assessment in the context of bearings in rotating equipment helps to identify potential hazards arising from bearing malfunction. This includes risks such as unexpected failures that could result in unplanned downtime, equipment damage, or even risks to worker safety if a bearing fails during operation. By assessing these risks, informed decisions can be made about when bearings need to be replaced.
For example, risk assessment can consider factors such as the frequency and severity of past bearing failures, the criticality of the equipment in the production process, and the potential economic and safety impacts associated with a bearing failure. These analyses help establish criteria for determining when to schedule preventive bearing replacement before critical failures occur.
Risk assessment does not directly provide the exact replacement date of a bearing, it does provide important information to manage the risks associated with its continued operation and establish appropriate preventive maintenance strategies to minimize these risks. From a predictive maintenance analyst’s point of view, the focus would be more on using specific techniques and tools to monitor the condition of bearings and predict when replacement is needed before failure occurs. The following are the characteristics of these two procedures:
Risk Assessment
- Scope: This approach assesses the risks associated with bearing malfunction, but does not provide a detailed methodology for determining the exact timing of replacement. It focuses on identifying the potential impacts of a failure and establishing general criteria for risk management.
- Usefulness: Useful for understanding the safety and operational implications of maintaining worn bearings, but does not provide specific data on the condition of the bearing or detailed recommendations on the optimum time for replacement.
Predictive analysis
- Scope: This type of predictive analysis uses techniques such as vibration monitoring, oil analysis, thermography, among others, to evaluate the current condition of bearings and predict their remaining service life.
- Utility: It provides concrete and specific data on the current condition of the bearing and its gradual deterioration. It allows identifying early failure patterns and planning replacement more accurately and efficiently, minimizing the risk of unplanned downtime and optimizing maintenance costs.
Risk matrix model for rotating equipment
Quantitative risk prioritization
- Implement a multifactor risk scoring system.
- Use Monte Carlo simulations to account for uncertainties in risk factors. Monte Carlo simulations are a mathematical technique that predicts the possible outcomes of an uncertain event. Computer programs use this method to analyze past data and predict a range of future outcomes based on a choice of action. A Monte Carlo simulation is a probabilistic model that may include an element of uncertainty or randomness in its prediction. When a probabilistic model is used to simulate an output, different results are obtained each time.
R = C * P * D
Where:
R = Risk score
C = Severity of consequences (scale 1-10)
P = Probability of failure (scale 0-1)
D = Detectability factor (scale 1-5)
Dynamic decision support system
- Develop a real-time risk dashboard integrating:
- Live sensor data from the equipment.
- Historical failure data.
- Maintenance records.
- Implement machine learning algorithms for predictive risk analysis:
- Random forest for failure mode classification.
- LSTM neural networks for equipment degradation time series prediction.
Adaptive risk matrix customization
- Employ hierarchical risk matrices:
- Level 1: General equipment category.
- Level 2: Specific equipment type.
- Level 3: Individual component.
- Implement automated recalibration of the matrix based on collected data and identified trends.
Integrated approach to safety-critical systems
- Incorporate Fault Tree Analysis (FTA) and Event Tree Analysis (ETA) into the risk assessment process.
- Implement Layer of Protection Analysis (LOPA) for high-risk scenarios.
- Use bowtie diagrams for comprehensive risk visualization and barrier analysis.
Cost-benefit optimization
- Develop a dynamic cost model integrating:
- Direct maintenance costs.
- Indirect costs (e.g., downtime, lost production).
- Risk mitigation costs.
- Implement Genetic Algorithms for multi-objective optimization of maintenance schedules and resource allocation.
6. Compliance and standardization engine
- Create a rules-based engine to ensure alignment with standards such as:
- ISO 31000 (Risk Management)
- IEC 60812 (FMEA): IEC 60812: 2018 explains how Failure Mode and Effects Analysis (FMEA) is planned, performed, documented, and maintained, including the Failure Mode, Effects and Criticality Analysis (FMEA) variant. The purpose of failure mode and effects analysis (FMEA) is to establish how elements or processes may fail to perform their function so that any required treatment can be identified.
- API 581 (Risk Based Inspection).
- Implement automated compliance reporting and gap analysis.
Integration of predictive and prescriptive maintenance
- Develop a hybrid model combining:
- Physics-based models (e.g., finite element analysis for stress prediction).
- Data-driven models (e.g., gradient increase for remaining life estimation)
- Implement Digital Twin technology for equipment condition monitoring and real-time scenario analysis.
Causes of bearing failures and how to identify them
Bearings can fail for a variety of reasons. Identifying the cause of the failure is important to implement effective corrective measures and prevent recurrences. The following are the main causes of bearing failures and how to identify them2.
- Lack of lubrication: Most premature bearing failures are caused by poor lubrication. Factors such as inadequate lubricants, excessive or insufficient amounts, and lubricant degradation contribute to this problem. Lack of lubrication manifests itself as abrasive wear, adhesive and raceway fatigue, with signs such as scratching and discoloration. To prevent this failure, it is essential to use the right lubricant in the right amount and at the right frequency.
- Contamination: Contamination by foreign substances in the lubricant or during the operating process can cause bearing failures. Signs include indentations in raceways and rolling elements, formation of microcraters and fan-shaped tracks. Prevention involves rigorous storage, filtering and cleaning procedures, as well as improvements in sealing systems.
- Fretting corrosion: Fretting corrosion occurs due to inadequate machining of the mating surfaces, especially when one of the rings does not allow axial expansion. This failure presents itself as oxidation and micro-movements that cause loss of material. Prevention requires accurate measurement of the shaft and housing during bearing replacement.
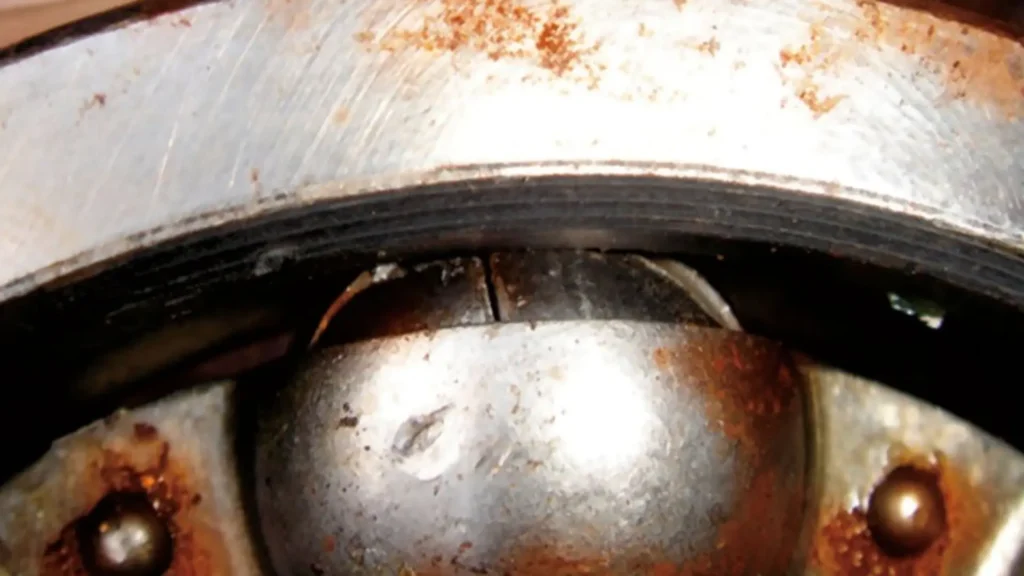
- Overloading or improper mounting: Incorrect mounting of bearings, and using improper methods, cause overloading and damage to raceways. To prevent this failure, it is recommended to apply the mounting force correctly, following the specific instructions.
- Overheating: Of bearings, at temperatures above 125°C, affects dimensional stability and metallurgical properties, causing deformations and fractures. To prevent this, induction heaters should be used and personnel should be trained in the correct use of tools.
- Moisture corrosion: Moisture corrosion occurs during prolonged storage or seal failure, causing rust and bearing damage. Prevention requires regular maintenance, the use of appropriate lubricants, and improvements in sealing systems.
- Misalignment: Misalignment, due to loss of collinearity between equipment, causes overloading and premature wear. It is identified by uneven wear on raceways. Prevention involves improving machining processes, implementing proper assembly procedures, and training personnel in shaft and sheave alignment.
- Storage and handling: Improper storage of bearings, exposed to external vibration, moisture, and contaminants, causes abrasive wear and damage. Prevention includes training of warehouse personnel, control of environmental conditions and proper protection of bearings.
When should bearings be replaced?
Bearings condition monitoring
The time between initial bearing damage and total bearing failure can vary considerably. In high-speed conditions, this period may be only a few seconds, while in large, slow-rotating equipment, it can extend for months. The key to determining the right time to replace a bearing is continuous monitoring of its condition3.
Importance of early diagnosis
Monitoring bearing condition is essential to detect damage before catastrophic failure occurs. If the damage is not diagnosed early and the bearing is not replaced in a timely manner, there is a risk of secondary damage to the equipment and its components. Catastrophic failures can result in prolonged and costly downtime and make it difficult or even impossible to identify the root cause of the problem.
Monitoring techniques
There are several techniques for monitoring the condition of the bearing, among which the following stand out:
- Vibration analysis: Allows the detection of irregularities in bearing operation, identifying anomalous patterns that indicate wear or damage.
- Oil analysis: Evaluates the presence of metallic particles and contaminants in the lubricant, which may indicate bearing wear.
- Thermography: Uses thermal imaging to identify areas of excessive heat, indicative of abnormal friction or impending failure.
Replacement criteria
The decision to replace a bearing should be based on precise technical criteria, considering factors such as:
- Degree of wear: measured by visual inspection and surface analysis.
- Vibration levels: Compared with established standards to determine the severity of damage.
- Lubricant condition: Evaluated for signs of degradation or contamination.
Consequences of not replacing on time
Failure to replace a damaged bearing in time can have serious consequences, including:
- Secondary damage: To other equipment components, which can increase repair and maintenance costs.
- Catastrophic failures: Which can result in unplanned downtime, lost production and increased operational risks.
- Difficulty in diagnosis: Further diagnosis of the root cause of the failure, complicating corrective and preventive actions.
Bearing replacement cost-benefit analysis
It is important to recognize that while bearing reconditioning can offer significant economic and environmental benefits, it also carries potential risks to the mechanical integrity of the equipment. The decision to recondition or replace a bearing should be based on a detailed evaluation of factors such as equipment criticality, operating conditions and safety standards.
Implementing rigorous quality control procedures is essential to mitigate the risks associated with refurbishment. In some cases, especially on critical or high-load equipment, replacement should be preferred to ensure long-term reliability and minimize the risk of catastrophic failure.
Based on experience and present observations, bearing reconditioning is not always the most economical or safest option. The decision to recondition or replace should be based on a detailed cost, risk and benefit analysis. In many cases, replacing the bearing may be a safer and more economically viable option, ensuring the mechanical integrity of the equipment and minimizing downtime.
Conclusions
Timely bearing replacement in rotating equipment is crucial to maintaining operational efficiency and minimizing downtime. Bearing condition monitoring is the best tool to determine the right time for replacement, avoiding secondary damage and catastrophic failures. Implementing a condition-based maintenance program and using advanced monitoring techniques will ensure longevity and optimal equipment performance.
Identifying and understanding the causes of bearing failures is critical to the implementation of preventive and corrective measures. Bearing condition monitoring and adherence to best practices will ensure longevity and optimal equipment performance.
References
- Diego Santos; “What is and how to do a risk analysis (with examples).”
- https://brr.mx/10-fallas-en-los-rodamientos-y-sus-causas/
- Bearing Damage and Failure Analysis.