Introduction
Wet and dry magnetic particles are key methods for inspecting ferrous parts, allowing the detection of both surface and subsurface defects. The main difference lies in the state of the particles used: dry particles are in powder form, while wet particles are applied suspended in a liquid medium, usually water or oil.
Magnetic Particle Inspection (MPI) is one of the most widely used nondestructive testing (NDT) methods for detecting surface and near-surface discontinuities in ferromagnetic materials. When considering wet vs. dry magnetic particles, the choice depends on various factors such as the type of material, the surface condition and the nature of the discontinuities to be detected. This article explores the characteristics, advantages, and limitations of both methods to guide the selection of the most appropriate option.
What is magnetic particle inspection?
Before addressing the comparison between wet and dry particles, it is necessary to understand the basic principle of MPI. This method involves magnetizing a ferromagnetic material to induce magnetic flux lines. When there is a discontinuity, such as a crack or a cavity, a magnetic leakage field is generated that attracts ferrous particles. These particles, visible under white or fluorescent light, make it possible to identify and locate imperfections.
In general, there are two ways of applying magnetic particles; the wet way, where the particles are suspended in liquids such as water or oil, and the dry way, where they are dispersed in the air. Also, both are classified into particles as visible under white light, and fluorescent particles, detectable under ultraviolet light.
Each method and type of particle has advantages and limitations, and their choice depends on factors such as the size and area of the parts, the environment, the discontinuities to be detected and the cost. By analyzing these factors, the most appropriate choice for each application can be determined.
Wet magnetic particles
The wet magnetic particles are suspended in a liquid, usually water or oil, and applied to the surface of the inspected material, making it suitable for certain applications.
Advantages
- Improved sensitivity: Wet particles are smaller than dry particles, so they can detect finer discontinuities.
- Uniform coverage: The liquid helps distribute particles evenly over complex surfaces, ensuring a more consistent inspection.
- Fluorescent applications: In combination with UV light, fluorescent wet particles stand out noticeably in low-light areas.
- Ideal for smooth surfaces: Wet particles adhere better to materials with fine surface finish, such as machined components or polished parts.
Limitations
- Require prior preparation: The surface must be well cleaned and free of contaminants to prevent the liquid from affecting the detection.
- Less effective in adverse conditions: Not ideal for field inspections or environments with wind or high humidity.
- Associated costs: The use of specialized equipment, such as suspension tanks and UV lights, increases operating costs.
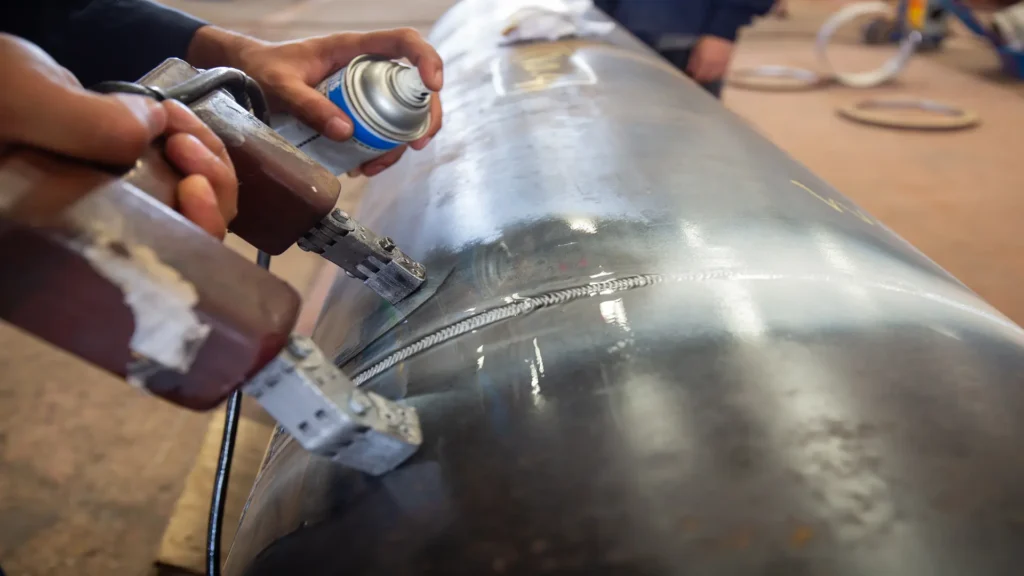
Dry magnetic particles
Dry magnetic particles are applied in powder form directly to the magnetized surface. This method is most often used in specific applications where wet particles are impractical.
Advantages
- Field application: They are ideal for inspections in outdoor environments and adverse conditions, such as wind, dust or low temperatures.
- Improved adhesion to rough surfaces: They easily attach to discontinuities in materials with rough finishes, such as castings or welded parts.
- Fast application: No additional liquids or equipment are required, which speeds up the inspection process.
- Efficiency in deep discontinuities: They are more visible in wide cracks or subsurface discontinuities.
Limitations
- Lower sensitivity: Dry particles, due to their larger size, are less effective in detecting very small defects.
- Uneven application: On complex surfaces, it can be difficult to achieve uniform particle distribution.
- Difficult visual detection: Visibility of dry particles is highly dependent on illumination and contrast.
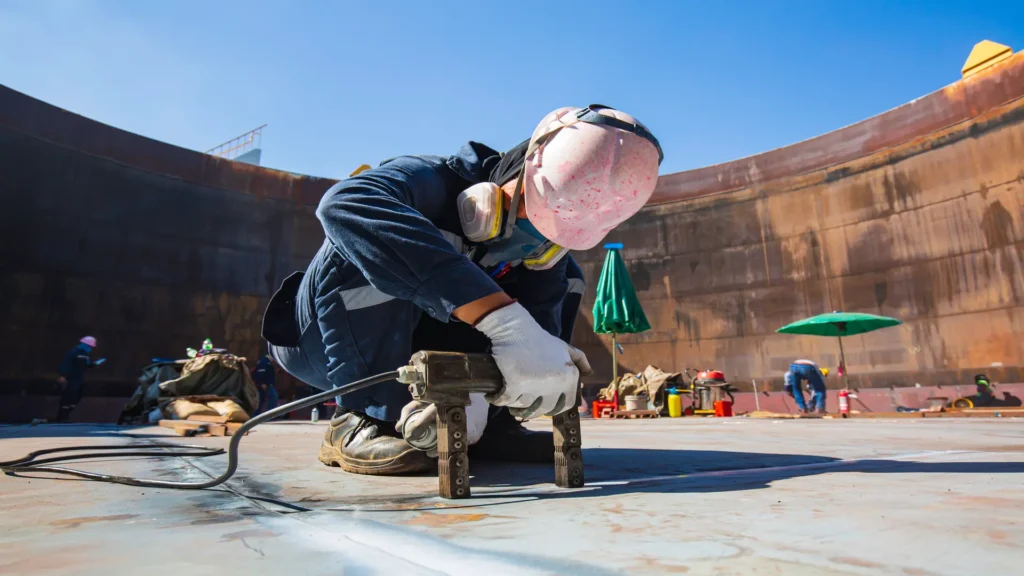
Technical comparison between wet vs. dry magnetic particles
Criteria | Wet Particles | Dry Particles |
---|---|---|
Particle Size | Smaller, higher sensitivity | Larger, lower sensitivity |
Surface Condition | Best for smooth or polished surfaces | Suitable for rough surfaces |
Environmental Conditions | Limited in wind or high humidity | Effective outdoors |
Ease of Use | Requires specialized equipment | Simple direct application |
Defect Detection | Excellent for fine discontinuities | Efficient for deep flaws |
Selection based on material and environment characteristics
Although both methods work well on ferromagnetic materials, the following conditions should be considered to influence the choice.
- Rough materials or castings: On materials with rough surfaces, such as castings or welded structures, dry particles are most effective. These particles are best set in wide cracks and surface defects.
- Smooth and machined materials: For components with fine finishes, such as machine parts or shafts, wet particles are the best choice because they flow easily over smooth surfaces, ensuring better coverage and more accurate detection. Also, their ability to adhere to small discontinuities ensures accurate and uniform detection.
- Large materials or in the field: For inspections on large parts or performed outdoors, dry particles excel due to their resistance to adverse conditions and ease of application.
- Smaller and deeper defects: Liquid-suspended particles are finer and have greater sensitivity, making them ideal for identifying small or deeper defects in the material.
- Uniform coverage: The liquid suspension allows for uniform application, ensuring that the magnetic particles completely cover the inspected area.
- Budget: Dry particles are typically more economical in terms of equipment and preparation.
- Ambient conditions:
- Dry particles are more suitable for outdoor inspections or in conditions where the use of liquids is impractical, for example, in extreme climates.
- In conditions where the liquid may evaporate quickly or mix with contaminants, the dry method is more practical.
- Controlled environments: In laboratories or workshops, where conditions can be controlled, the wet method is usually more effective.
Common Industrial Applications
- Aerospace: Fluorescent wet particles are preferred due to their high sensitivity and ability to detect critical microcracks in aircraft magnetic components.
- Automotive: Dry particles are often used to inspect engine blocks and castings due to their effectiveness on rough surfaces.
- Oil and gas: Both methods are commonly used to inspect welds in pipelines and pressure vessels.
- Railway sector: On rails and train wheels, dry particles allow the detection of discontinuities in difficult environmental conditions.
Conclusion
The decision between wet and dry magnetic particles must be based on a detailed analysis of the specific needs of each application. Evaluating factors such as the type of material, the nature of the discontinuities, and the operating conditions allows the most effective method to be selected. This enables companies to optimize defect detection, enhance safety, the quality of inspections, and the efficiency of their industrial processes.
References
Own source.