Table of Contents
- What are vibrations in rotating equipment?
- Fundamental concepts of vibration: Resonance, damping, and harmonics
- What is vibration analysis?
- Causes of vibration in rotating equipment
- Understanding vibration analysis in rotating equipment
- The critical need for early detection
- Online vibration monitoring
- Computer-aided design and simulation
- Vibration isolation solutions
- Vibration isolation systems: a strategic approach
- The innovation of additive manufacturing
- The holistic approach to vibration mitigation
- Conclusions
- References
Machine vibration is a fundamental aspect of rotating equipment operation, and to understand it in depth it is necessary to go beyond simple definitions to explore the underlying dynamics, causes, effects, and diagnostic techniques associated with these vibrations.
In the context of rotating equipment, such as turbines, pumps, and engines, vibration arises due to the dynamic forces generated as these machines operate. These forces can cause components to move back and forth or oscillate around their equilibrium positions. The complexity of this motion can vary; it can be a simple, repetitive motion, or it can be more chaotic, involving multiple frequencies and directions.
What are vibrations in rotating equipment?
Machine vibration refers to the oscillatory motion of machine components, a phenomenon that can manifest itself in a variety of ways depending on the nature of the equipment and the forces at play. This vibration can be intentional and serve specific purposes, as in vibratory conveyors, where controlled vibrations facilitate material handling or compaction. More commonly, however, vibration in machines is unintentional and undesirable, often indicating underlying mechanical problems that, if left unchecked, can lead to significant damage or even catastrophic failure.
Fundamental concepts of vibration: Resonance, damping, and harmonics
To fully understand the implications of vibration in rotating equipment, it is important to delve into the concepts of resonance, damping, and harmonics. Resonance occurs when the frequency of an external force matches the natural frequency of the machine or its components, leading to a significant increase in vibration amplitude.
This can be particularly dangerous in rotating equipment, where resonance can cause rapid wear or even structural failure. Damping, on the other hand, is the process by which vibratory energy is dissipated, usually through friction or material deformation, which reduces the amplitude of vibrations and protects the machine from damage. Harmonic vibrations are oscillatory movements around an equilibrium point, subjected to a force proportional to the distance to that point, has a simple harmonic vibratory motion. A spring that is made to vibrate by a force that moves it away from equilibrium is a good example of harmonic vibration.
Machine vibration can be characterized by several key parameters: amplitude, frequency, and phase. Amplitude refers to the magnitude of the vibration, which can indicate the severity of the problem. Frequency is related to the speed of oscillation and can help identify specific sources of vibration, such as unbalance or misalignment in rotating components. Phase, which describes when the vibration occurs relative to a reference point, is crucial for diagnosing problems related to the interaction between different machine parts.
What is vibration analysis?
Vibration analysis is a technique used to monitor and evaluate the condition of machinery and rotating equipment by studying the data of each rotating equipment observed and monitored.
It consists of measuring and analyzing vibrations to detect anomalies, failures, or signs of wear in machinery components. By examining vibration patterns and frequencies, maintenance professionals obtain information about the condition of the equipment.
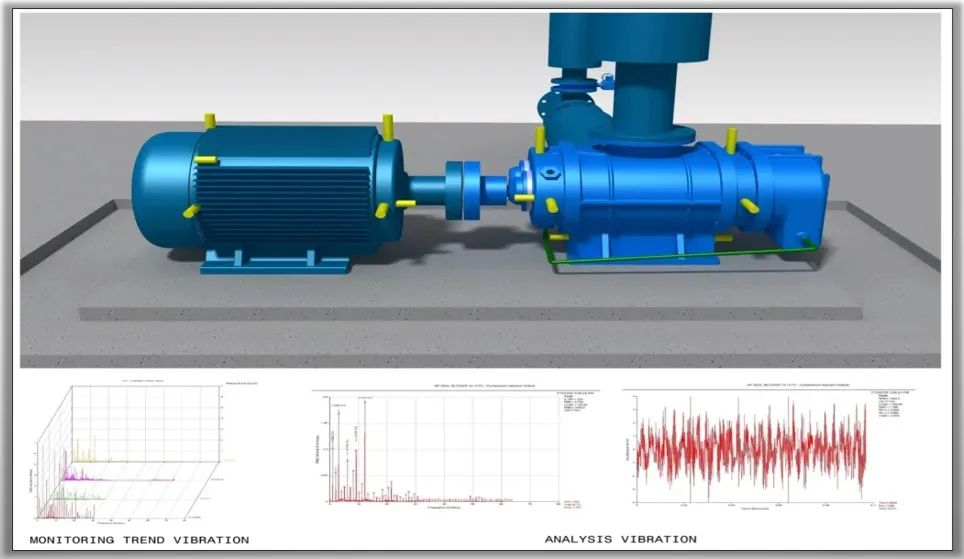
Causes of vibration in rotating equipment
The most common causes of vibration in rotating machinery include:
- unbalance: occurs when the center of mass of a rotating component is not aligned with its axis of rotation, resulting in centrifugal forces and vibration. Unbalance can be due to manufacturing defects, material buildup, or wear over time.
- Misalignment: This occurs when the rotational axes of the connected components are not properly aligned. Misalignment can be parallel, angular, or a combination of both, resulting in significant vibration and increased wear.
- Loose or worn parts: Components such as belts, chains, couplings, or bolts that are loose or worn can cause vibration and noise.
- Bearing problems: Bearing problems, including misalignment, lubrication problems or wear, can cause excessive vibration.
Understanding vibration analysis in rotating equipment
Vibration analysis is a sophisticated and essential technique in the field of mechanical engineering, particularly when dealing with the complexities of rotating equipment. The term “vibration” refers to the oscillatory motion experienced by mechanical components during operation. These vibrations can be both a symptom and a cause of various mechanical problems.
Therefore, studying and analyzing these vibrations allows engineers to monitor the mechanical integrity and performance of systems in a non-invasive manner, ensuring that they perform as expected.
Modern vibration analysis relies heavily on sensors, which are meticulously integrated into machinery to capture real-time data on the operational status of the equipment. These sensors, often accelerometers, are strategically placed to detect even the slightest vibrations, which are then analyzed to identify potential anomalies.
The ability to collect, analyze, and interpret this data in real-time is what makes vibration analysis such a powerful tool. It allows the detection of problems that might not be detected with the naked eye but can cause significant damage if left unchecked.
The critical need for early detection
One of the main objectives of vibration analysis on rotating equipment is the early detection of mechanical problems. In rotating equipment, anomalies such as unbalance, misalignment, or bearing and bearing failures manifest themselves as changes in vibration patterns. By continuously monitoring these patterns, engineers can identify difficulties long before they cause serious damage or equipment failure. This proactive approach not only helps reduce maintenance costs but also plays a crucial role in ensuring the safety and quality of end products.
The following video shows how to perform vibration measurements on rotating equipment. Source: Fluke Corporation.
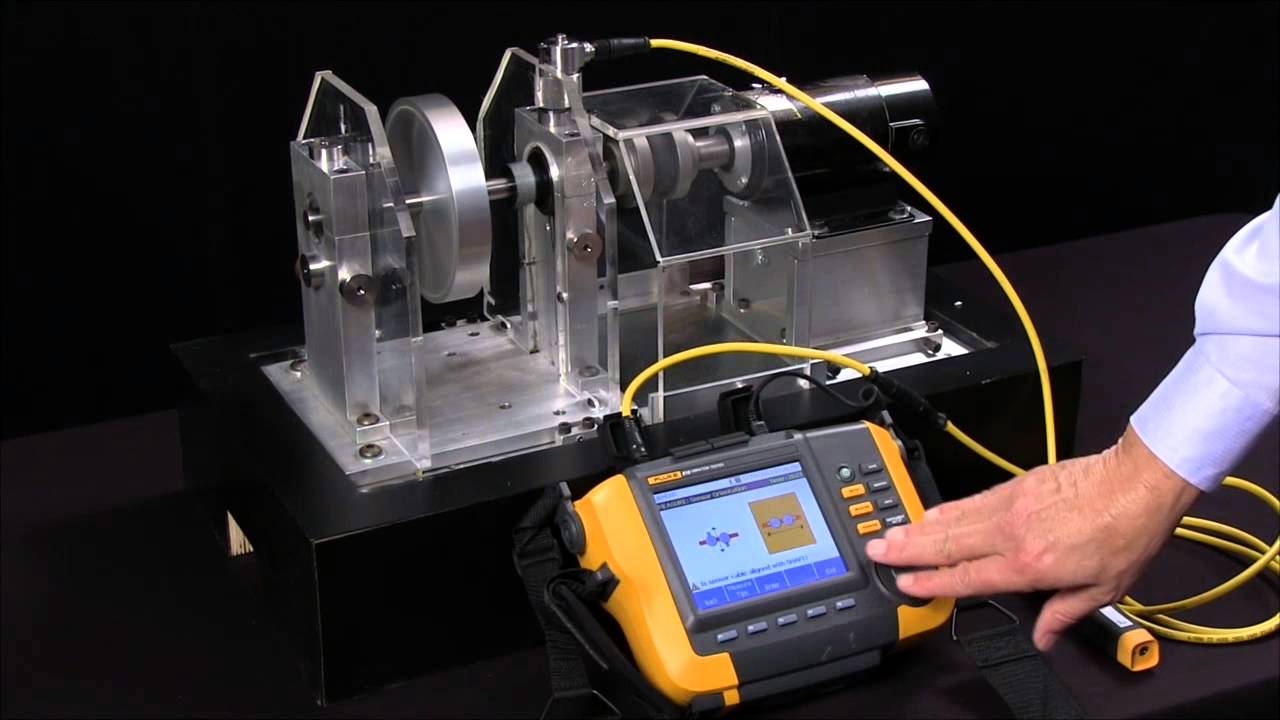
How to Measure Vibration with the Fluke 810 Vibration Tester.
Online vibration monitoring
Online vibration monitoring has become increasingly crucial in industrial environments, driven by the growing emphasis on predictive maintenance and operational efficiency. One of the most significant trends is the integration of Industry 4.0 principles and Internet of Things (IoT) technologies into vibration monitoring systems ( smart sensors). This integration enables real-time data collection from industrial machinery, which is then analyzed using advanced algorithms to detect patterns and potential problems before they cause failures.
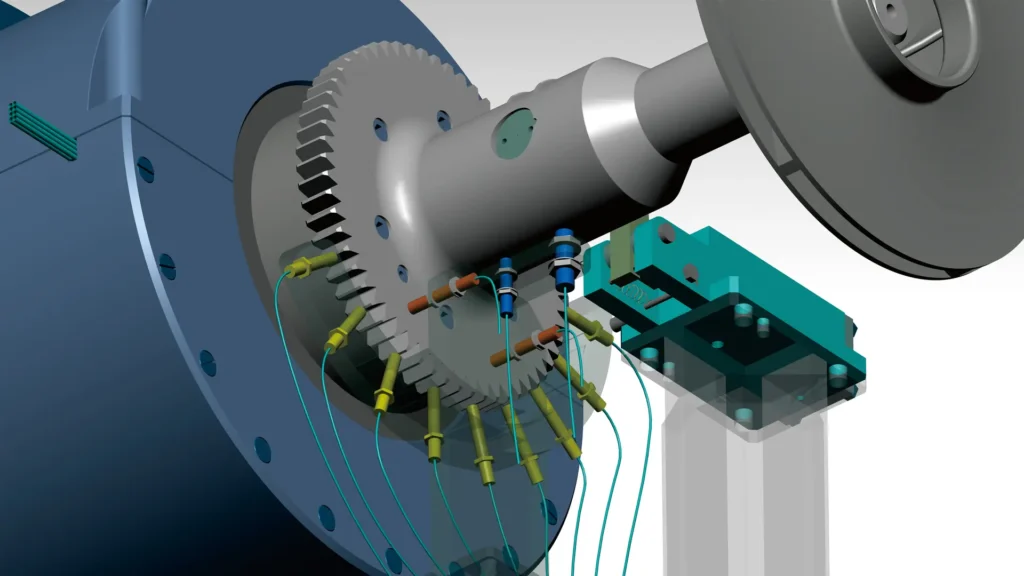
Computer-aided design and simulation
One of the most significant advances in this area is the use of computer-aided design and simulation. With these tools, engineers can create detailed models of machinery and simulate their behavior under various operating conditions. This simulation process includes dynamic analysis, in which the vibrational characteristics of the design are tested in real-world situations.
For example, finite element analysis (FEA) is widely used to predict how components will respond to operational stresses, including vibrations. FEA breaks down the structure into small elements, allowing engineers to understand how each part contributes to the overall vibration profile.
Another key innovation is topological optimization, which involves designing structures that are inherently more resistant to vibration while meeting their functional requirements. Topological optimization algorithms can suggest material distributions within a given design space that minimize vibration without compromising strength. For example, in rotating machinery, where weight and balance are critical, topological optimization can ensure that components are lightweight and vibration-resistant.
Vibration isolation solutions
In the past, addressing vibration problems was often a reactive process, with engineers responding to problems after they occurred. However, advances in design techniques and technologies have shifted this paradigm to a more preventative approach. Computer-aided design (CAD) and simulation tools now allow engineers to predict and mitigate vibration problems during the design phase itself.
One of the most significant contributions to vibration mitigation comes from materials science. Traditional materials, which have been the backbone of manufacturing for decades, are increasingly being replaced or supplemented by advanced composites and metamaterials.
- Advanced composites: these materials are designed by combining two or more constituent materials with different physical or chemical properties. The resulting composite material often exhibits superior vibration-damping characteristics compared to traditional metals or plastics. For example, carbon fiber composites, widely used in the aerospace and automotive industries, offer a high strength-to-weight ratio and excellent vibration absorption properties.
- Metamaterials: Taking innovation a step further, metamaterials are artificially structured materials designed to exhibit properties not found in natural substances. These materials can be designed to manipulate waves, including mechanical vibrations, in very specific ways. For example, a metamaterial could be designed to redirect vibrational energy away from sensitive components, effectively isolating them from the source of vibration. This specific approach allows unprecedented control over how vibrations propagate through machinery.
Vibration isolation systems: a strategic approach
Instead of attempting the often impossible task of completely eliminating vibrations, modern engineering has shifted the focus to isolating sensitive components from these vibrations. This strategy is implemented through advanced vibration isolation systems, which can be passive or active:
Passive isolation systems: these systems generally involve the use of damping materials that absorb the vibrational energy. For example, rubber mounts or specialized damping pads can be placed between the vibrating component of a machine and the rest of the equipment to prevent vibration transmission.
Active control systems: More sophisticated than passive systems, active control systems use sensors and actuators to counteract vibrations in real-time. Sensors detect unwanted vibrations and actuators generate opposing forces to cancel them, similar to noise-canceling headphones. In extreme cases, technologies such as magnetic or electrostatic levitation can be employed to completely isolate a component from any physical contact with vibrating surfaces.
The innovation of additive manufacturing
Additive manufacturing, commonly known as 3D printing, has introduced a novel approach to equipment design, particularly in the context of vibration mitigation. Traditional manufacturing techniques often impose significant limitations on the complexity of internal structures within components. However, additive manufacturing breaks these limitations, allowing engineers to design and produce complex internal geometries that were previously impossible.
The holistic approach to vibration mitigation
While each of these techniques (advanced materials, isolation systems, and additive manufacturing) offers significant benefits, the most effective vibration mitigation strategies are often holistic. This means that engineers do not rely on a single technique, but rather integrate multiple approaches, customized to the specific needs of the equipment and its operating environment.
The old practice, when engineers addressed vibration problems reactively, often after the equipment was already in use. This could involve making post-production modifications or operational adjustments, which could be costly and less effective.
However, with the advent of these advanced design techniques and materials, engineers can now address potential vibration issues during the design phase. This proactive approach not only leads to better-performing equipment but also extends its operational life and reduces the need for maintenance.
Conclusions
In conclusion, the study of mechanical vibration in rotating equipment is not just about identifying problems; it is about understanding the underlying mechanics that drive these vibrations and using this knowledge to design better, more reliable machinery. As technology continues to evolve, the tools and techniques available to engineers for vibration analysis and mitigation will only become more sophisticated, making this an exciting and constantly evolving field of study.
Recent advances in materials science, isolation systems, and manufacturing technologies have fundamentally transformed the way engineers approach vibration mitigation in manufacturing equipment. By addressing these issues at the root during the design phase, we can now produce machinery that is not only more stable and accurate but also more durable and requires less maintenance.
Adopt proactive strategies for a vibration-free manufacturing environment and lead the way to future innovations.
References
- https://www.linkedin.com/pulse/common-causes-vibration-rotating-equipment
- https://micromega-dynamics.com/applications/rotating-machinery-vibration-reduction/
- https://reliability.ae/2024/07/28/common-causes-of-vibration-in-rotating-equipment/