Table of Contents
- What are vibration tests?
- Advanced methods and current trends in vibration testing
- Methodology for vibration testing of rotating equipment
- Industrial applications of vibration analysis
- Fixed sensors and continuous monitoring
- Key benefits for analysts and specialists in predictive maintenance
- SKF @ptitude Analyst software for vibration analysis
- Example of vibration analysis with SKF @ptitude Analyst
- Conclusions
- Referencias
Vibration testing of rotating equipment (such as engines, turbines, pumps and compressors) is essential for predictive maintenance and early failure detection. These tests can identify problems such as unbalance, misalignment, bearing failures, resonance and mechanical clearances.
Vibration analysis is a fundamental tool in industrial maintenance, for engineers and predictive maintenance specialists, in order to detect problems and mechanical failures in time.
What are vibration tests?
Vibration tests can detect a wide variety of faults in rotating equipment. Below, I explain the main failures and how they are identified by vibration analysis:
1. Imbalance:
Cause: Uneven mass distribution in the rotor, which generates centrifugal forces. Indicators in vibration analysis:
- Increase in vibration amplitude at 1x the rotational speed (fundamental frequency).
- Consistent patterns in the time and spectral domain.
- Increased vibration in radial direction.
2. Misalignment:
Cause: When the shafts of two or more components are not correctly aligned. Indicators in vibration analysis:
- Increase in the frequencies 1x and 2x the rotational speed.
- Vibrations in axial and radial direction.
- Possible additional harmonics.
3. Mechanical clearances:
Cause: Wear in bearings, bearings or loose joints. Indicators in vibration analysis:v
- Occurrence of multiple low frequency harmonics (1x, 2x, 3x….).
- Nonlinear patterns in the time domain.
- Random noise in the vibration signal.
4. Bearing failures:
Cause: Wear, poor lubrication or contamination of bearings. Indicators in vibration analysis:
- Increase in bearing characteristic frequencies (BPFO, BPFI, BSF, FTF).
- Increased envelope analysis.
- High frequency noise and peaks in the time domain.
5. Structural resonance:
Cause: When the excitation frequency coincides with the natural frequency of the system. Indicators in vibration analysis:
- Exponential increase of the vibration amplitude at certain speeds.
- Pronounced peaks in the frequency spectrum.
- Changes in the response when the operating speed is modified.
6. Gear problems:
Cause: Wear, tooth defects or poor lubrication. Indicators in vibration analysis:
- Gear Mesh Frequency (GMF).
- Peaks at multiples of the meshing speed.
- Increase in the envelope signal.
7. Electrical problems in motors:
Cause: Shorted rotor, phase unbalance or stator problems. Indicators in vibration analysis:
- Vibrations at pole step frequency (2x the line frequency, 100 Hz or 120 Hz in 50/60 Hz systems).
- Modular waves in the vibration signal.
- Peaks at frequencies related to electrical harmonics.
8. Cavitation in pumps:
Cause: Formation and collapse of vapor bubbles in the fluid. Indicators in vibration analysis:
- High frequency noise signal with random peaks.
- Increased vibration in the broadband spectrum.
- Characteristic “knocking” or “squeaking” sound.
Advanced methods and current trends in vibration testing
- Frequency analysis (FFT – Fast Fourier Transform): Still the most accepted and widely used standard for decomposing vibration signals and detecting specific faults.
- Envelope analysis: Ideal for detecting bearing and gear failures at early stages.
- Modal and operational analysis (ODS – Operational Deflection Shape): Allows to visualize how the structure deforms and vibrates under operational loading.
- Shock Pulse Method (SPM): Very useful for evaluating bearing and lubrication conditions.
- Order Vibrations (Order Tracking Analysis): Used on variable speed machinery to detect problems based on the number of rotation orders.
- Transient and start-up analysis (Run-Up/Coast-Down Tests): Evaluates the vibration behavior in speed variations, useful in turbomachines.
- Machine learning and artificial intelligence: More and more tools are incorporating AI algorithms to detect failure patterns automatically.
Methodology for vibration testing of rotating equipment
A structured vibration analysis process allows early detection of faults, avoiding costly repairs. By systematically collecting, processing and interpreting vibration data, vibration analysts can detect mechanical problems and take proactive maintenance measures.
Vibration analysis steps
Effective vibration analysis follows a structured approach to detect, diagnose and treat rotating equipment problems before they cause failures or unscheduled downtime:
- Establish a baseline: Where vibration data is recorded when the equipment is operating under normal conditions to create a reference point for applying comparisons.
- Measure vibration: Use sensors to capture real-time vibration signals from critical equipment.
- Convert the data: Apply the fast Fourier transform (FFT) to convert raw vibration signals into a frequency spectrum for detailed analysis.
- Detect and identify abnormality: Compare the new data with the baseline to detect deviating vibration patterns.
- Make your diagnosis: Make comparisons of frequency peaks with mechanical failures, such as bearing defects, misalignments or clearances.
- Apply solutions: Based on the results, schedule maintenance, or repairs to be performed to prevent failures.
The application of rotating equipment vibration analysis ensures that these benefits are fully realized through strategic sensor placement, accurate data analysis and interpretation, and integration of the results into maintenance workflows.
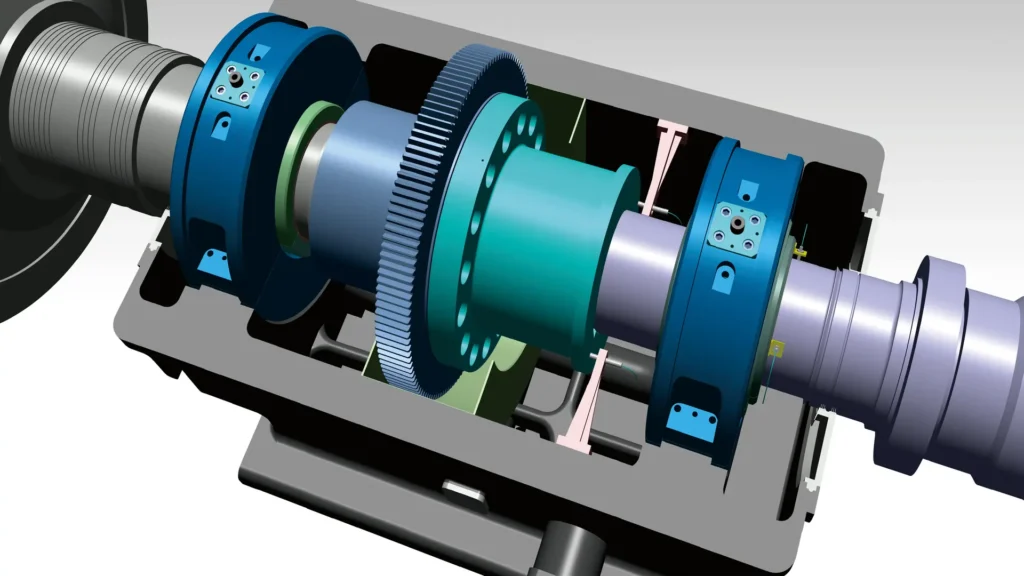
Industrial applications of vibration analysis
The application of rotating equipment vibration analysis ensures that these benefits are fully realized through strategic sensor placement, accurate data analysis and interpretation, and integration of the results into maintenance workflows.
Bearings are a crucial component for rotating machinery, and vibration analysis helps detect wear, lubrication problems and incipient stage failures before catastrophic failure occurs.
Detects gear misalignment, broken teeth and lubrication failures, preventing machine underperformance and mechanical failure.
Ensures trouble-free operation by detecting imbalances, resonances and mechanical clearances, which can cause excessive vibrations and energy waste.
In rotating equipment of utmost importance for the processes they handle and work at high speed (turbines, turbogenerators, compressors), vibration analysis helps to avoid rotor unbalance, blade damage and misalignment that could cause major unscheduled shutdowns.
Continuous vibration monitoring is a key tool in the application of predictive maintenance, providing technical and economic benefits by transforming industrial asset management.
Their main advantages are presented below, explained in a more technical and dynamic way:
Proactive detection of incipient failures
Real-time monitoring makes it possible to identify anomalies in the characteristic frequencies of critical components such as bearings, gears or shafts. This enables early detection of problems such as misalignments, imbalances or lubrication defects before they evolve into catastrophic failures.
This predictive approach minimizes unplanned downtime and reduces costs associated with emergency repairs.
Equipment life extension
By dynamically correcting adverse operating conditions (excessive vibration, backlash or resonance), mechanical stress on components is reduced.
This not only extends the service life of the equipment, but also optimizes its operating performance under controlled conditions.
Significant reduction in operating costs
Continuous analysis allows the implementation of condition-based maintenance (CBM) strategies, avoiding unnecessary interventions and maximizing the efficient use of resources. Studies show that this approach can reduce maintenance costs by up to 50% by eliminating superfluous expenses and preventing major failures.
Increased industrial safety
Continuous monitoring mitigates risks associated with excessive vibrations that could compromise the structural integrity of equipment or facilities. Detecting and addressing these anomalies significantly reduces the risk of workplace accidents, environmental damage and regulatory sanctions.
Improved energy efficiency
Excessive vibrations are often associated with energy losses due to friction or mechanical misalignment. Timely correction of these inefficiencies not only optimizes energy consumption, but also improves the productivity of the entire system.
Predictive maintenance optimization
Integration with advanced systems such as IoT and artificial intelligence makes it possible to analyze a large volume of data in real time, generating more accurate predictive models. This facilitates strategic maintenance scheduling and ensures greater operational availability.
Fixed sensors and continuous monitoring
Fixed sensors for vibration monitoring allow real-time analysis without the need for manual inspections.
Main sensors and technologies used
- Industrial accelerometer sensors
- Leading brands: SKF, Emerson, PRUFTECHNIK, Hansford Sensors.
- Benefit: They capture vibrations in real time and send data to a central system.
- Displacement and proximity sensors (eddy current probes)
- Used in turbomachines and large bearings.
- Benefit: Detect variations in high-speed shafts.
- Triaxial vibration sensors
- They capture data in three axes simultaneously.
- Benefit: Increased accuracy in structural analysis.
- Wireless sensors (IoT)
- Example: SKF Enlight Collect, Erbessd WiSER.
- Benefit: No wiring required, ideal for hard-to-reach areas.
Key benefits for analysts and specialists in predictive maintenance
- Reduced diagnostic time: Advanced software identifies problems before catastrophic failures.
- Remote and real-time monitoring: With IoT sensors, analysts can receive alerts without being on site.
- Increased diagnostic accuracy: AI-based algorithms improve the detection of failure patterns.
- Maintenance cost optimization: Avoids unplanned downtime and improves maintenance planning.
- Advanced analysis on variable speed machines: Thanks to techniques such as order analysis.
- Integration with other machine parameters such as temperature, pressure and load for more complete analysis.
SKF @ptitude Analyst software for vibration analysis
- Features:
- Integration with fixed sensors and portable devices.
- Advanced analytical algorithms and predictive trending.
- Diagnosis based on AI and historical patterns.
- Benefits:
- Allows on-site diagnostics with specific recommendations.
- Ideal for condition monitoring in critical industries such as oil, gas and power generation.
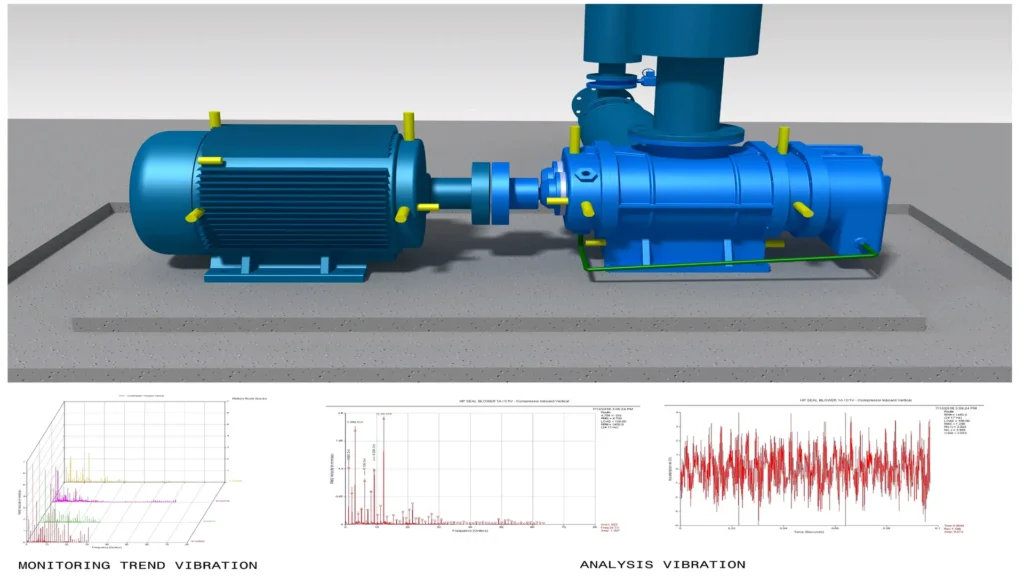
Example of vibration analysis with SKF @ptitude Analyst
To illustrate how a predictive analyst can use SKF @ptitude Analyst software quickly and accurately, let’s review a real case of fault detection and diagnosis on an electric motor coupled to a centrifugal pump.
Configuration and data acquisition
- Equipment: 75 kW electric motor coupled to a centrifugal pump. Sensors used:
- SKF CMSS 793-4 (100 mV/g accelerometer) in motor and pump bearing housings.
- SKF Wireless Machine Condition Sensor (WMCD) in the motor housing for continuous monitoring.
- Sampling frequency: 25 kHz.
- Measurement mode: FFT + Vibration envelope analysis.
Data transmission: Wireless sensors send data to SKF IMx-8, which transmits it to SKF @ptitude Analyst via Ethernet.
Automatic analysis with SKF @ptitude Analyst
Step 1: Display of the FFT frequency spectrum
- A vibration spectrum is generated and unusual peaks are detected at 1x, 2x and 3x engine RPM.
- A “Medium Severity Alarm” alert is activated for high vibrations in the motor bearing.
Step 2: Application of envelope analysis
- The envelope filter is used to isolate high frequency vibrations.
- Peaks are detected at 3.2 kHz and 4.6 kHz, indicating incipient motor bearing failure (SKF 6313).
Step 3: Evaluation of vibration levels (ISO 20816)
Sensor location | Vibration measurement (mm/s RMS) | ISO 20816 Limit | Status |
---|---|---|---|
Motor bearing (DE) | 5.2 mm/s | 4.5 mm/s | Critical |
Motor bearing (NDE) | 3.8 mm/s | 4.5 mm/s | Warning |
Pump bearing | 2.2 mm/s | 4.5 mm/s | Normal |
Automatic diagnosis and recommendation
SKF @ptitude Analyst generates an automatic report with the following conclusions:
- Failure detected: defective motor bearing (SKF 6313).
Probability of failure: 90% (according to historical patterns in SKF database).
Estimated time to critical failure: 3 weeks.
Probable cause: Poor lubrication or bearing fatigue.
Automatic recommendation:
- Immediate action: Schedule replacement of SKF 6313 bearing at next planned shutdown.
- Corrective action: Implement automatic lubrication with SKF SYSTEM 24.
Automatic report generation
SKF @ptitude Analyst generates an automatic PDF report, including:
- Vibration spectra (FFT and envelope).
- Vibration trends over the last 6 months.
- Fault diagnosis based on SKF database.
- Recommendations with maintenance priority.
The report is automatically sent to the maintenance department and recorded in the CMMS (SAP PM).
Benefits of analysis with SKF @ptitude Analyst
- Early detection with 90% accuracy in diagnosis.
- Reduction of analysis time (from hours to minutes).
- Automation of reports and connection with the maintenance system.
- Avoid unplanned downtime and optimize maintenance planning.
This example shows how the use of SKF @ptitude Analyst, combined with advanced sensors, enables fast, accurate and AI-based diagnosis, with automatic recommendations and a high reliability rate.
Conclusions
Vibration analysis is a powerful tool for predictive maintenance, allowing to detect faults before they become critical problems. Each failure has specific patterns in the vibration spectrum, so the combination of different techniques such as FFT, envelope analysis and continuous monitoring with fixed sensors helps to improve diagnostic accuracy.
Continuous vibration monitoring is not just a technological investment; it is a strategic shift that transforms industrial maintenance into a more efficient, safe and cost-effective model. Its implementation offers a tangible return by reducing operating costs, increasing asset reliability and ensuring operational continuity in highly demanding industrial environments
Referencias
- https://www.skf.com/group/products/condition-monitoring-systems/software/aptitude-analyst
- https://upkeep.com/es/learning/reduce-spend-preventive-maintenance/
- https://inspenet.com/articulo/vibraciones-equipos-rotativos-como-indicador/