Table of Contents
- The Challenge of under pipe support inspection
- Principles of Short-Range Guided Wave Testing (SRGWT)
- Benefits of Short-Range Guided Wave Testing
- Limitations of Short-Range Guided Waves
- Electromagnetic Acoustic Transducers (EMATs): Enhancing under pipe support inspection
- Advantages of using EMAT transducers
- Integrating Short-Range Guided Wave Testing with EMAT for under support inspection
- What are the applications of Short-Range Guided Waves?
- Future of SRGWT with EMATs
- Conclusion
- References
The integrity of pipeline systems is paramount to ensure the safety, reliability, and efficiency of various industries, including oil, gas, and chemical processing. One of the challenges in maintaining the integrity of these conduits is under pipe support inspection, prone to external corrosion and mechanical wear due to their contact or proximity to support structures. Traditional inspection methods often fall short in effectively assessing these areas due to accessibility issues and the complex nature of the damage.
This article delves into an innovative approach using Short-Range Guided Wave Testing (SRGWT) combined with Electromagnetic Acoustic Transducer (EMAT) technology for inspecting pipelines under support, highlighting the principles, advantages, and applications of this methodology.
The Challenge of under pipe support inspection
Corrosion under supports poses a significant challenge to pipeline integrity, particularly in those exposed to aggressive marine environments and extreme weather conditions. This issue is exacerbated when moisture accumulates at the interface between the support and the pipeline, accelerating corrosion deterioration. Surface preparation required by different Non-Destructive Testing (NDT) methodologies—including coating removal—can increase the vulnerability of pipelines to this phenomenon.
Conventional techniques, such as Ultrasonic Testing (UT) and visual inspections, present considerable limitations due to restricted direct access in areas under support. However, technological advancements in the field of NDT have led to the development of systems capable of generating and detecting guided waves, as well as efficiently directing their propagation. These advances have established specialized transducers as optimal tools for evaluating previously inaccessible areas, such as supported pipe contact points, offering a promising solution to overcome challenges associated with corrosion under supports.
Principles of Short-Range Guided Wave Testing (SRGWT)
Guided Wave Testing (GWT) is an advanced NDT method that uses low-frequency ultrasonic waves and differs from conventional ultrasonic waves. Guided Wave Testing (GWT) is an advanced NDT method that uses low-frequency ultrasonic waves. GGT differs from conventional ultrasonic waves in that it uses the medium in which it propagates as a waveguide and the rules of interaction with defects are different from conventional ultrasonic waves.
In the well-known technique of Long-Range Guided Waves or LRGWT, much lower frequencies are used, resulting in much longer propagation distances. However, when focusing on applications such as inspection under support, Short-Range Guided Wave Testing (SRGWT) becomes particularly relevant.
SRGWT is a short-range technique that allows the use of higher-frequency sound waves, resulting in much greater sensitivity and resolution, capable of detecting defects within a shorter range, typically up to a few meters from the transducer. The use of short-range guided waves allows for the detection of corrosion, cracks, and other forms of damage with high resolution and accuracy.
Benefits of Short-Range Guided Wave Testing
The benefits of SWGWT for inspecting pipelines under support include:
- Accessibility: Enables inspection of hard-to-reach areas without the need for extensive excavation or support removal.
- Efficiency: Large pipe sections can be inspected quickly, reducing downtime and inspection costs.
- Sensitivity: High-resolution detection of small defects, ensuring early intervention and repair.
- Thickness Range: This technique can be used on wall thickness ranging from 6 mm to 25 mm.
- Temperature Range: Can be used up to 200 °C (392 °F).
Limitations of Short-Range Guided Waves
Like Long-Range Guided Waves, SRGWUT has the following limitations:
- This method can only be performed at room temperature.
- It cannot distinguish between a discontinuity in the I.D. and a discontinuity in the O.D. In other words, it cannot indicate the depth of the discontinuity.
- The inspection surface must be a clean metal base and as smooth as possible to avoid ultrasonic wave diffraction.
- The instrument and its accessories are very expensive.
- Extensive training and experience in UT are required.
Electromagnetic Acoustic Transducers (EMATs): Enhancing under pipe support inspection
Electromagnetic Acoustic Transducer (EMAT) technology represents a significant advance in the field of ultrasonic testing. Unlike conventional piezoelectric transducers that require a liquid couplant to transmit ultrasonic waves, EMAT generates ultrasonic waves directly in the material through electromagnetic induction, making it highly suitable for inspecting pipelines under support where couplant application is impractical.
This technique can generate ultrasonic waves with minimal surface contact, while in motion, allowing the inspector to scan rough surfaces without significantly affecting guided wave properties. The technology is used more efficiently in hard-to-reach areas that require a more comprehensive analysis, complemented by other techniques1.
New EMAT technologies have been developed to generate horizontal shear waves at each scanned axial position that propagate in the circumferential direction of the pipe and are received by the receiving sensor. The three main measurement results include the average wall thicknesses in the upper and lower paths, and the minimum remaining wall thicknesses, indicated by A, B, and D1 respectively. In Figure 1, the GUL’s QSR1 equipment designed specifically for inspecting pipelines under supports is shown2.
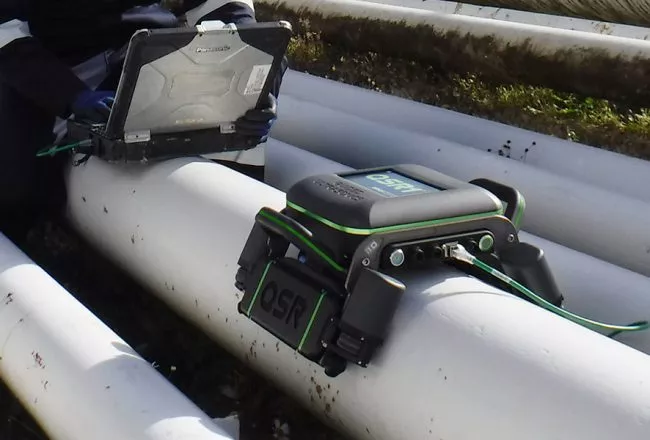
Advantages of using EMAT transducers
EMAT offers several advantages for pipeline inspection:
- Dry coupling: Eliminates the need for a liquid couplant, facilitating inspections in challenging environments.
- Versatility: Can generate various wave modes, including shear waves, which are particularly effective in detecting cracks and other types of defects.
- Durability: Resistant to adverse environmental conditions, making them ideal for field applications.
- Generation of horizontal shear waves: Horizontal shear waves, in practice, can only be generated through EMAT technology3, specifically through the use of Periodic Permanent Magnet (PPM) – EMAT. This type of wave is highly useful, for example, in inspecting welds of austenitic material with a highly attenuating and anisotropic structure. Figure 2, illustrates a horizontal shear wave4.
- Temperature range: Can be used up to 200 °C (392 °F).
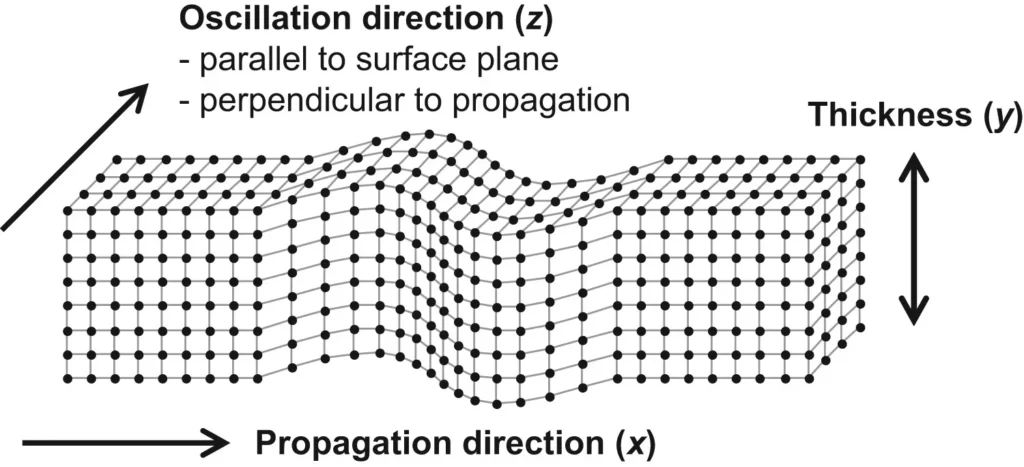
Integrating Short-Range Guided Wave Testing with EMAT for under support inspection
Integrating short-range guided wave testing with EMAT technology offers a powerful solution for under-support pipe inspection. This approach combines the high-resolution detection capabilities of short-range guided waves with the practical benefits of EMAT transducers, providing a comprehensive assessment of pipe integrity without the need for direct access or contact.
What are the applications of Short-Range Guided Waves?
Several case studies have demonstrated the effectiveness of using short-range guided wave testing with EMAT transducers for under-support pipe inspection in various industries. For example, in the oil and gas sector, this approach has successfully identified corrosion under pipe supports on offshore platforms, leading to timely repairs and an extension of service life. Similarly, in chemical plants, it has been used to detect progressive cracking under high-temperature pipe supports, preventing potential failures.
Below is a demonstration of how corrosion under pipe supports (CUPS) can be sized using the QSR1, courtesy of: GUL – Guided Ultrasonics Ltd.
Corrosion under pipe support inspection (CUPS).
Future of SRGWT with EMATs
The Short-Range Guided Wave Testing (SRGWT) technique has recently seen significant advancements through the utilization of phased array technology. This innovation is manifested in specialized instruments employing linear array probes with elements to be activated in phase, enabling more precise and detailed inspections.
With the introduction of Electromagnetic Acoustic Transducers with Periodically Permanent Magnets (PPM – EMAT) technology, horizontal shear waves are generated, minimizing complexities in the inspection of austenitic stainless steel welds, thereby expanding the spectrum of possibilities of SRGWT. This represents an extraordinary breakthrough in what has been a challenge for decades in the inspection of such materials.
Looking ahead, it is anticipated that the evolution of SRGWT technique will be oriented towards the implementation of automated scanning systems alongside Automatic Defect Recognition (ADR) algorithms. This transition towards automation aims to minimize operator expertise dependency, thereby increasing the objectivity and accuracy of inspections.
The development and implementation of these advanced technologies hold the promise of significantly transforming the inspection process, making it more efficient and reliable.
Conclusion
Under pipe support inspection presents significant challenges for pipeline integrity management. The integration of short-range guided wave testing with EMAT technology offers a promising solution, overcoming accessibility issues and providing accurate, high-resolution assessments of pipe condition. As industries continue to recognize the benefits of this innovative approach, it is poised to become a standard practice in pipeline maintenance and safety protocols, ensuring the reliable operation of critical infrastructure worldwide.
References
- JOHN BOYLE, ERIC SJERVE. EMAT Ultrasonic Guided Wave Inspection of Simple Pipe Supports; Accessed on April 9, 2024; https://es.scribd.com/document/475970494/EMATUltrasonicGuidedWaveInspectionofSimplePipeSupports-pdf
- Guided Ultrasonic Limited. QSR1. Accessed on April 9, 2024. https://www.guided-ultrasonics.com/inspection/scanning/qsr-system/qsr1/
- AZHAR M. MEMON, LUAI M. ALHEMS. Applications of EMAT Generated Guided Waves in Pipes: A Review; Accessed on April 10, 2024. https://www.ndt.net/article/ndt-canada2023/papers/EMAT_Generated_Guided_Waves_in_Pipes.pdf
- P.A. PETCHER, S. DIXON. Weld defect detection using PPM EMAT generated shear horizontal ultrasound; Accessed on April 11, 2024. https://www.sciencedirect.com/science/article/pii/S0963869515000572