Introduction
A turbogenerator is a large electric generator driven by a steam turbine, water turbine or gas turbine to generate electrical power. Turbo generator applications are fundamental to the functioning of contemporary society, as the production of electricity is essential. This process converts a variety of energy forms into usable electricity, ensuring a constant and efficient supply for various industrial, commercial and residential sectors.
The large-scale generation of electricity is through the use of steam turbines connected to electrical generators, particularly in power plant infrastructure. In this article, the basic and fundamental concepts about what is a turbo generator type and its operation by which mechanical energy is harnessed to transform it into electrical energy. It also develops which are the applications of turbo generators in different sections and the technological advances that drive innovation in this field.
Theoretical concepts and fundamentals of turbo generators
What is a turbo generator?
A turbo generator, also known as a turbo-alternator, is an electrical generator that converts mechanical energy into electrical energy by connecting to the shaft of a gas or steam turbine. These machines are used in a wide range of residential and industrial applications and can be configured to run on different types of fuels, such as steam, electricity and various biofuels.
The following is WEG SA’s new technological innovation in 62.5 MVA ST 40 axial flow turbo generators, hydraulics, control panels, and automation. This solution will increase the energy efficiency of the plants.
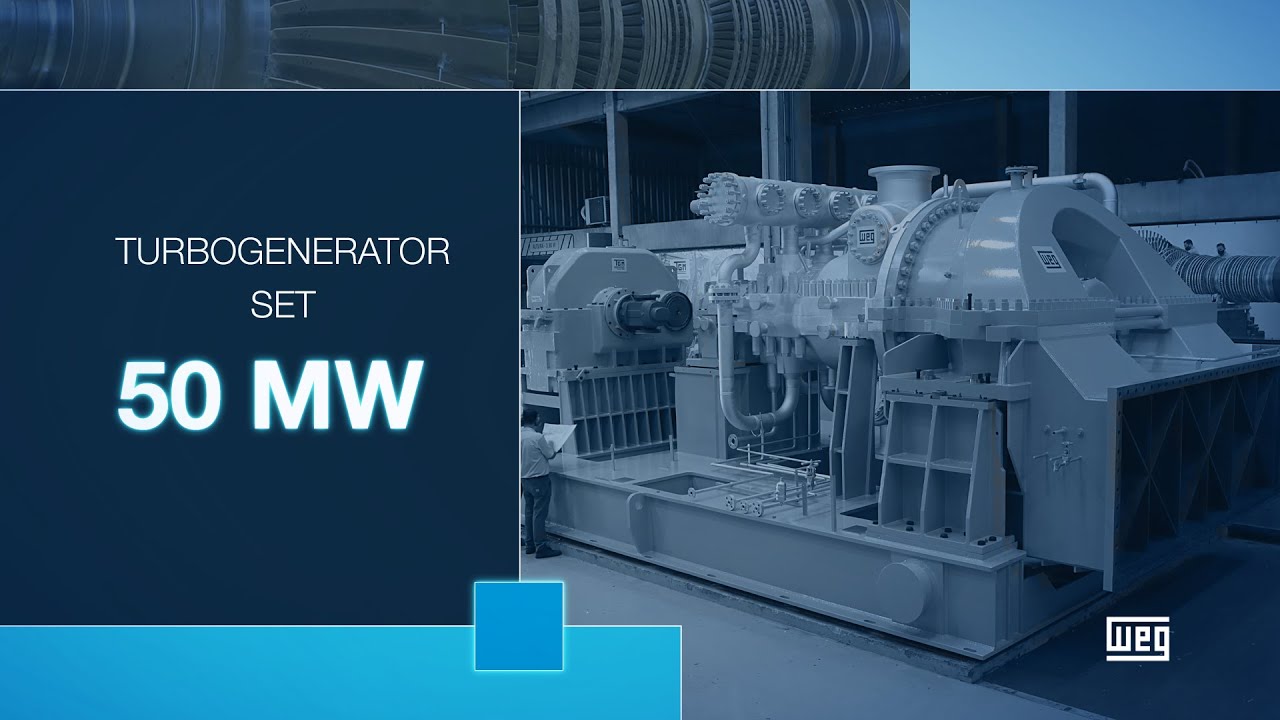
ST 40 62.5 MVA axial flow turbogenerator.
Components of a turbo generator
The turbo generator consists of several components, including:
- Stator: the fixed part of an electric generator, responsible for creating the magnetic field in which the rotor rotates. It is composed of a core of high quality steel lamination, usually silicon steel, which minimizes eddy current losses and improves efficiency.
- Stator core: Thin lamination that reduce eddy currents and provide efficient mechanical support when carrying magnetic flux.
- Stator frame: Heavy part that reduces vibration and withstands thermal gas pressure.
- Stator winding: Includes a three-phase, double-layer winding to reduce harmonics.
- Rotor shaft: Solid piece of vacuum-cast steel with slots for field winding.
- Bearing: Mechanical elements that support the rotor, allowing its smooth and stable rotation inside the stator. They play a determining factor in alignment, friction reduction, load absorption, and heat dissipation. In addition, they provide voltage isolation between the three-phase winding and the stator frame, protecting the system from possible failures due to parasitic currents.
- Rotor wedges: Protect the winding from the effects of centrifugal force.
- Rotor fan: Disperses cooling air by means of axial fans.
- Excitation system: The set of components and devices that supply the necessary direct current to the rotor winding of a synchronous generator to create the magnetic field required for electricity generation. It generates a magnetic field with a suitable electric current.
- Cooling system: Its function is to dissipate the heat generated by internal energy losses during the operation of the equipment, to maintain operating temperatures within permissible and safe ranges. Thus prolonging the life of insulating materials and other critical components, and ensuring efficient and reliable operation of the turbo generator.
How does a turbo generator work?
The turbo generator is a machine that harnesses the kinetic energy of steam to generate electricity. It works on the principle of electromagnetic induction, which is fundamental in the production of electricity. When high-pressure steam is directed towards the turbine blades, its kinetic energy causes them to rotate. These blades are connected to a shaft, which, when rotating, activates the rotor of the electric generator.
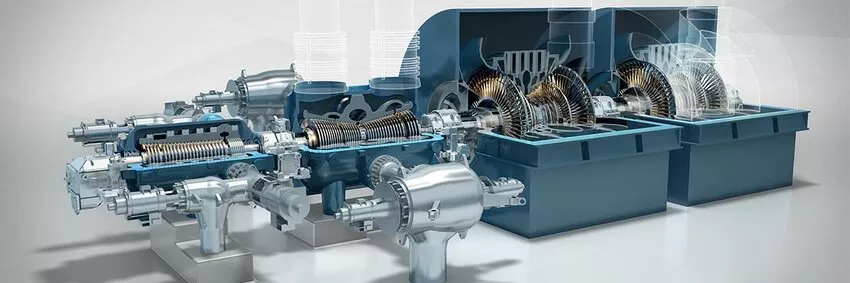
Inside the generator, this rotor motion interacts with a stationary magnetic field, which induces electric current in the stator coils, thus producing electricity. Both the turbine and the generator convert the mechanical energy of the fluid in motion into electrical energy, adapting to various applications and types of energy.
The rated speed of the turbo generator is usually 1500 rpm/3000 rpm with a minimum of 2 or 4 poles for a frequency of 50 Hz, and 1800 rpm/3600 rpm with 2 or 4 poles for a frequency of 60 Hz. The rotating parts of this generator can generate high mechanical pressures due to the higher operating speed. The rotor of these generators is typically manufactured by forging with solid steel and alloys to ensure structural strength.
Turbo generator types
Different types of turbo generators are available and are discussed below.
Advances in turbo generator technology have resulted in the development of various types tailored to specific applications and operational requirements. This section describes the key types of turbo generators prevalent in contemporary power generation:
- Conventional steam turbo generators: identified by the use of high-pressure steam to drive turbine blades, conventional steam turbo generators are key elements in the production of electricity in coal, natural gas, and nuclear power plants.
- Combined cycle turbo generators: Leveraging the integration of gas and steam turbines, combined cycle power plants exhibit superior efficiency by harnessing waste heat from the gas turbine exhaust to generate additional steam for the steam turbine.
- Geothermal turbo generators: In geothermal power plants, steam or hot water extracted from the earth’s crust serves as the primary energy source to drive steam turbines, offering a renewable and environmentally sustainable alternative to fossil fuel-based electricity generation.
Turbo generator applications
Turbo generators were developed for applications in thermoelectric power plants and have a wide range of power ratings, defined based on experience in the supply and sizing of turbo generators, to be applied in steam and gas turbines.
These units, which combine a turbine and an electric generator, are essential in several industrial and infrastructure applications. The main applications of turbo generators and their relevance in different sectors are explored below.
Thermal power plants
- Coal: In coal-fired thermal power plants, turbo generators are the central component for electricity generation. Coal is burned to heat water and produce high-pressure steam, which drives turbines connected to electric generators.
- Natural gas: Combined cycle power plants use turbo generators to harness natural gas. These plants combine gas and steam turbines to maximize energy efficiency, generating electricity in two stages with a single fuel.
- Nuclear power: In nuclear power plants, turbo generators convert the thermal energy generated by nuclear fission into electrical energy. Steam produced in nuclear reactors is used to drive turbines, which are connected to generators.
Renewable energy
- Geothermal power plants: Geothermal power plants use turbo generators to convert heat from the Earth’s interior into electricity. Geothermal steam drives the turbines, generating electricity in a continuous and sustainable manner.
- Biomass plants: In these plants, organic waste is burned to produce steam driven by turbo generators. In addition to generating electricity, this process also helps to manage waste and reduce greenhouse gas emissions.
Industrial sector
- Cogeneration: This is an industrial application of turbo generators where electricity and useful heat are produced simultaneously. This technology is used in industries that require large amounts of thermal and electrical energy, such as petrochemical and paper manufacturing.
- Hydrocarbon processing plants: In refineries and gas processing plants, turbo generators are used to convert excess steam and gas into electricity, improving energy efficiency and reducing operating costs.
Critical Infrastructure
- Data centers: Data centers require a continuous and reliable source of power. Turbo generators can provide backup power in the event of grid failures, ensuring continuity of operations.
- Hospitals and healthcare complexes: Turbo generator applications in these facilities rely on emergency power systems. Turbo generators are essential to ensure uninterrupted power supply during emergencies or power outages.
Transportation
- Ships and submarines: In the naval field, turbo generator applications are used on ships and submarines to generate electricity and propulsion. These systems are especially common on military ships and nuclear submarines.
- High-speed trains: Some high-speed trains use turbo generators to convert thermal energy into electricity, driving electric motors and improving the energy efficiency of rail transport.
Distributed energy projects
- Microgrids: In microgrids, turbo generators can be used to generate electricity locally, improving energy resilience and reducing dependence on the main grid.
- Remote communities: For isolated communities, turbo generators can provide a reliable and continuous source of energy, using local resources such as natural gas or biomass.
Conclusion
The applications of turbo generators in electricity generation and power supply in diverse applications from large power plants to industrial facilities and transportation systems. Their ability to convert thermal energy into electrical energy makes them an indispensable technology in the modern world. The adoption and applications of turbo generators not only improve energy efficiency but also contribute to the sustainability and resilience of energy systems globally.
References
Own source