In today’s dynamic business scenario, where quality is the hallmark that separates successful organizations from others, the role of leaders in quality management takes on unprecedented relevance. They not only define the strategic direction of their organizations but are also the guardians of operational excellence and customer satisfaction.
In this context, specialized training emerges as the solid foundation on which sustainable success is built, as the indispensable route for the development of leaders in quality management, examining the tangible benefits, innovative tools, and case studies that demonstrate their transformative impact.
Join us on a journey through the very essence of business quality and discover how specialized training becomes the master key to successfully leading in this challenging landscape.
The evolution of quality management: A transformative journey
From its emergence at the dawn of the Industrial Revolution to today’s complex global business network, quality management has undergone a fascinating evolution. This section immerses us in a journey through time, exploring the various stages that have marked the development of this discipline crucial for business success.
This tool finds its roots in inspections of manufactured products during the Industrial Revolution. In this pioneering era, quality was primarily associated with the physical conformity of products, and manual inspections were the norm. The rudimentary standards laid the foundation for a nascent understanding of the importance of consistency in production.
Subsequently, the introduction of statistical methods by visionaries such as Walter A. Shewhart and W. Edwards Deming marked a milestone in the evolution of quality management 2 . The era of statistical process control (SPC) was born, moving attention beyond post-production inspection to defect prevention. This paradigm shift laid the foundation for the modern approach.
After the 1970s and 1980s, the total quality philosophy emerged, driven by post-war Japanese quality, which transformed this set of actions into a holistic approach that involved all levels of an organization. Quality certification, with standards such as ISO 9001 , provided a structured framework creating a globally recognized standard1 (see figure 1).
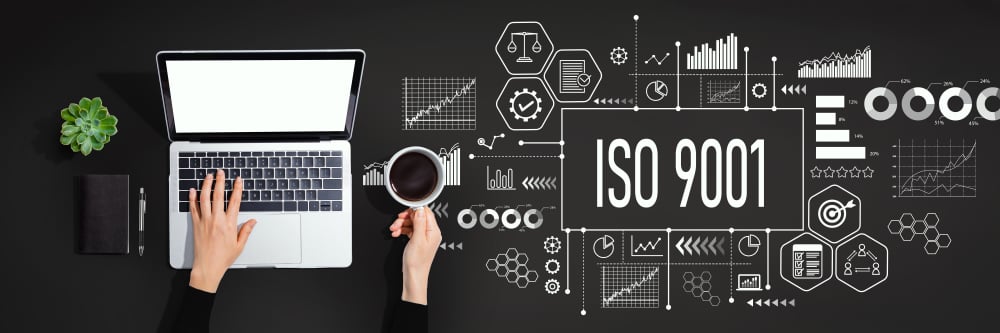
At the end of the 20th century, we find the convergence of Lean Manufacturing and Six Sigma, approaches that introduce unprecedented efficiency. Eliminating waste and reducing variability became central objectives, leading to significant improvements in product quality and operational efficiency.
With the era of digitalization we arrive at Quality Management 4.0, where technologies such as the Internet of Things, advanced data analysis and artificial intelligence are integrated to provide unprecedented visibility and control over quality processes. Global connectivity enables instant collaboration and informed decision making.
Current challenges in quality management: Perspectives and visionary leadership
Quality Management, although it has experienced significant advances over the decades, is today in the midst of complex and dynamic challenges. These current challenges require a visionary leadership approach to ensure that organizations not only maintain but also improve their quality standards in an ever-changing business environment.
Globalization and complexity of the supply chain
With the expansion of global markets, supply chains have become more complex and extensive. Quality management leaders face the challenge of maintaining consistency and quality across these chains, often across multiple time zones and regulations. The need for global coordination and effective supplier management have become imperative.
Adaptation to 4.0 technology
The fourth industrial revolution, characterized by digitalization and the integration of advanced 4.0 technology, presents opportunities and challenges. Leading in this environment requires a deep understanding of emerging digital tools, as well as the ability to strategically implement them to improve quality and efficiency.
Data management and cybersecurity
Managing large volumes of data is essential to evaluate and improve quality. However, this also poses challenges related to privacy and cybersecurity. Leaders must ensure critical data is protected from digital threats, while harnessing its potential to inform data-driven decisions.
Changes in consumer expectations
In an increasingly interconnected world, consumer expectations are evolving rapidly. Quality is no longer measured only by the absence of defects, but also by sustainability, transparency and social responsibility.
Climate change and sustainability
Pressure to operate sustainably and reduce environmental footprint has intensified. This affects quality management in terms of materials used, manufacturing processes and operational practices. Leaders must integrate sustainability into their quality strategies to align them with current and future demands.
The Role of Visionary Leadership
In the face of these challenges, visionary leadership involves the ability to anticipate trends, foster innovation, and guide organizations to higher standards. They must cultivate adaptive teams, foster resilience in the face of uncertainty, and establish a culture that embraces change as an integral part of the path to continuous improvement. Additionally, they must be committed to constant training and updating skills to lead in a constantly evolving business environment.
Ultimately, meeting today’s challenges requires leadership that not only responds to the problems of the present, but also models excellence and vision for the future. Visionary leaders are the architects of resilient, quality organizations, capable of thriving in a constantly changing business world.
Specialized training in quality management
- Towards Trained and Resilient Leadership: In the constant search for excellence in quality management, the transformative role of specialized training stands as a fundamental pillar. Training not only becomes a strategic tool for the development of leaders, but also acts as the engine that drives innovation, adaptability and continuous improvement in the field of quality.
- Development of Specific Competencies: Quality management is not a static task; evolves over time and adapts to emerging challenges. It allows the development of specific skills, from the interpretation of regulations to the application of advanced methodologies. Trained leaders are able to guide their teams with up-to-date knowledge and specialized skills.
- Adoption of Best Practices and Innovative Methodologies: Covers the latest trends, best practices and innovative methodologies. The adoption of advanced approaches, such as Lean or Six Sigma, becomes possible through training, allowing proven strategies to be applied to optimize processes and improve efficiency.
- Promotion of a Culture of Quality: Training is not only limited to the acquisition of technical knowledge, but also influences the organizational culture. The training fosters a culture of quality rooted in continuous improvement, accountability and commitment to excellence at all levels of the organization.
- Resilient leadership in the face of challenges: Challenges are inevitable, and specialization acts as a resilient shield, to face known challenges, but also develop agility to address unexpected situations. Training acts as a catalyst for proactive leadership and informed decision making.
- Driving continuous innovation: Quality management is not only about meeting existing standards, but leading in the creation and adoption of new practices, nurturing the innovative mindset, equipping you with the tools and critical thinking necessary to drive innovation continues in its processes and products.
- The cycle of continuous improvement: Specialized training in quality management is not conceived as a single event, but as a continuous cycle of improvement. Training is essential for constant updating and adaptation to the changing dynamics of the business environment. This cycle of continuous improvement translates into agile, competitive organizations with the ability to lead at the forefront of quality.
Tangible benefits of quality management training
Training in quality management emerges as a fundamental pillar in the development of organizations that aspire to excellence and sustainability. The benefits derived from specialized training in this area not only boost the quality of products and services, but also strengthen the competitive position and financial health of the company.
- Optimization of Operational Processes: Training in quality management enables professionals to analyze, evaluate and improve the organization’s operational processes. The application of methodologies such as Six Sigma or Lean allows us to identify and eliminate inefficiencies, resulting in more agile, profitable operations that are aligned with strategic objectives.
- Cost and Waste Reduction: Specialized training enables teams to implement practices that reduce operating costs and minimize resource waste. The identification and elimination of unnecessary or defective activities contributes directly to financial efficiency and the maximization of available resources.
- Rigorous Compliance with Regulations and Standards: Quality management training ensures that professionals are up to date with industry regulations and standards. This knowledge not only ensures regulatory compliance, avoiding potential sanctions, but also establishes a framework for continuous improvement and proactive adoption of best practices.
- Continuous Improvement and Adaptability: The mentality of continuous improvement, promoted by training, allows the organization to quickly adapt to changes in the market and business environment. The ability to evolve and adjust to new circumstances is essential to maintaining long-term relevance and competitiveness.
- Increased Customer Satisfaction: The quality of the product or service is a central element for customer satisfaction. Quality management training empowers teams to understand customer expectations, exceed their needs, and build long-term relationships. Customer loyalty and positive recommendations translate into sustainable growth.
- Goal Alignment and Collaborative Efficiency: Training promotes a shared understanding of goals between different departments. Teams trained in quality management work more cohesively, sharing information efficiently and collaborating effectively to achieve common goals.
- Improved Business Image and Reputation: An organization committed to quality, supported by trained teams, builds a solid brand image. The reputation for offering high-quality products or services translates into a competitive advantage, attracting customers and business partners.
- Developing Competent Leaders: Training not only benefits employees in operational roles, but also contributes to competent development, and enables them to lead their teams towards excellence, promoting a culture of quality throughout the organization.
Conclusion
Ultimately, the tangible benefits of quality management training go beyond operational processes. They contribute to financial efficiency, strengthen the company’s reputation and position the organization as a benchmark in its industry. Investment in quality training is therefore a strategic investment that drives the long-term success of the organization.
References
- INNNOVA ESG GROUP ; “All the news about the ISO 9001:2015 standard”; published August 25, 2020; https://www.nueva-iso-9001-2015.com/
- Cortés Esteban A, Navarro José L, Jiménez José M, Vargas Vargas Manuel, “Statistical quality control: A brief historical review”; Rresearchgate.net, published January 2004.