Table of Contents
- Introduction
- Thickness measurement methods on various components
- ECT Eddy Current Testing Principles
- Factors influencing Eddy Currents
- Eddy Current thickness gauge applications
- Methods of coating thickness measurement by ECT
- Advantages of ECT thickness gauging
- Limitations of Eddy Current thickness measurement
- Conclusion
- References
Introduction
Thickness measurement is an inspection evaluation to determine the actual thickness of a material used in different industrial applications, subject to quality control, material characterization, and maintenance operations. One of the most effective non-destructive tests for thickness measurement is the use of the non-destructive Eddy Current Testing (ECT) technique. This technique is widely recognized for its accuracy, efficiency, and ability to measure non-magnetic conductive materials without physical contact.
This article discusses the different methods of thickness measurement, and the technique based on the Eddy Current Testing (ECT), the principle behind the Eddy Current Thickness Gauge, the various applications of the technique, and its advantages and limitations.
Thickness measurement methods on various components
Assets in industries, such as: pipelines, vessels, and storage tanks, require the checking, inspection, and corrosion monitoring of wall thickness, and the determination of the thickness of non-conductive coatings on magnetic and non-magnetic substrates such as paints. The thickness of metallic coatings for protection against corrosion and internal erosion such as cladding inside pressure vessels and bimetallic pipelines. Several Non-Destructive Tests are applied for these purposes, among which the following are mentioned:
- Ultrasound (UT): Effective and the best option in the evaluation of wall thicknesses in pressure vessels, pipes, tanks, among other components, and ideal for corrosion mapping using the Ultrasonic Phased Array technique. There are also instruments based on the principle of this test to measure coating thicknesses.
- Radiology (RT): Of little use for this application and for specific cases such as the measurement of thicknesses of insulated pipes. A technique based on X-ray fluorescence is used to measure coating thicknesses, with the advantage of simultaneously serving the instrument as an alloy analyzer.
- Eddy currents (ECT): Eddy current thickness gauges are used to measure thicknesses of thin films and tubes, and metallic coatings on metallic substrates with a notable difference in conductivities. They are ideal and the best choice for thickness measurements of coatings on magnetic and non-magnetic (ferrous and non-ferrous) substrates.
ECT Eddy Current Testing Principles
The principle of ECT is based on Faraday’s Law of Electromagnetic Induction, which states that a changing magnetic field induces an electromotive force (EMF) in a conductor. When the coil in the eddy current probe is placed near a conductive surface, the magnetic field of the coil induces eddy currents in the material.
These eddy currents, in turn, generate their own magnetic fields, which oppose the original or inducing magnetic field by creating an additional resistance to the coil conductor’s own electrical resistance (R) known as inductive reactance (Xl). The vector sum of both oppositions to the current constitutes the impedance of the coil (Z). Figure 1 shows the impedance plane with these parameters1.
Any failure or change in the electrical properties of the material produces an alteration of the Eddy currents and these in the impedance of the coil. Variations in the impedance of the coil can be related to changes in the material properties, presence of faults, its thickness, or separation of the probe from the surface of the inspected component. This is due to the presence of an intermediate material of certain thickness (e.g., a coating).
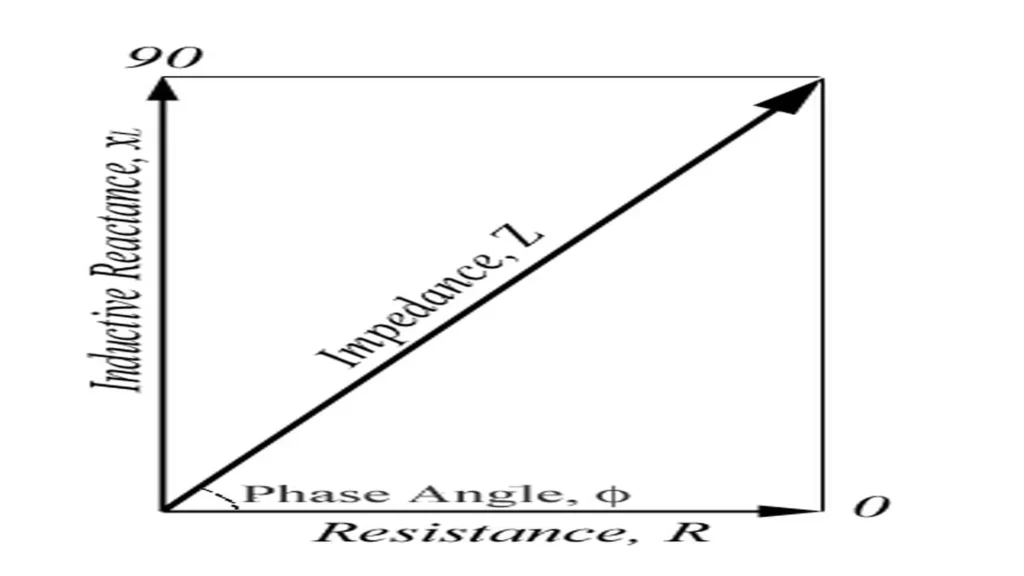
By analyzing the variations in coil impedance, i.e., through the change in voltage measured with a second coil and the phase angle of the impedance vector. Changes in material properties can be detected, faults can be detected, the thickness of the material or coating on the material can be measured through the use of an eddy current thickness gauge. More advanced variants of the test, such as Eddy Current Array (ECA), offer plan or C-Scan views for easier test interpretation and more efficient application.
Factors influencing Eddy Currents
Several material factors affect the Eddy Current behavior and, therefore, the accuracy of thickness measurements:
- Conductivity: Highly conductive materials, such as copper and aluminum, allow eddy currents to flow more easily, resulting in stronger opposing magnetic fields and more significant changes in coil impedance.
- Permeability: The magnetic permeability of the material also influences eddy currents. Ferromagnetic materials, with high permeability, increase the interaction between the material and the magnetic field, which can complicate the measurement process.
- Thickness: The thickness of the material is directly related to the distribution of Eddy currents and their phase shift, affecting these parameters in the impedance of the inductor coil. As the depth advances there is less density in the flow of currents so the signal decreases in amplitude, on the other hand, the Eddy Currents are progressively out of phase and therefore vary the phase angle of the signal (viewed in an impedance plane), this being one of the fundamentals for measuring thicknesses or determining the depth of defects such as pitting.
- Probe lift-off: It is defined as the separation between the sensor probe and the conductive surface. It is a factor that has a major impact on the ECT2 test. This separation can be provided by the thickness of a coating, so it can be used as a principle for the determination of its thickness of a current thickness gauge.
Eddy Current thickness gauge applications
The Eddy Current thickness gauge is used in a wide range of industries due to its non-destructive nature and its ability to measure materials that are difficult or impossible to measure with other techniques.
- Coating thickness measurement: One of the most common and ideal applications of thickness measurement by ECT is the determination of the thickness of non-conductive coatings on conductive and non-conductive substrates. For example, in the automotive industry, this technique is used to measure the thickness of paint, enamel or plastic coatings on metal surfaces; the ability to measure without damaging the coating is critical for quality control during the manufacturing process. Figure 2, shows an Eddy Current coating thickness gauge.
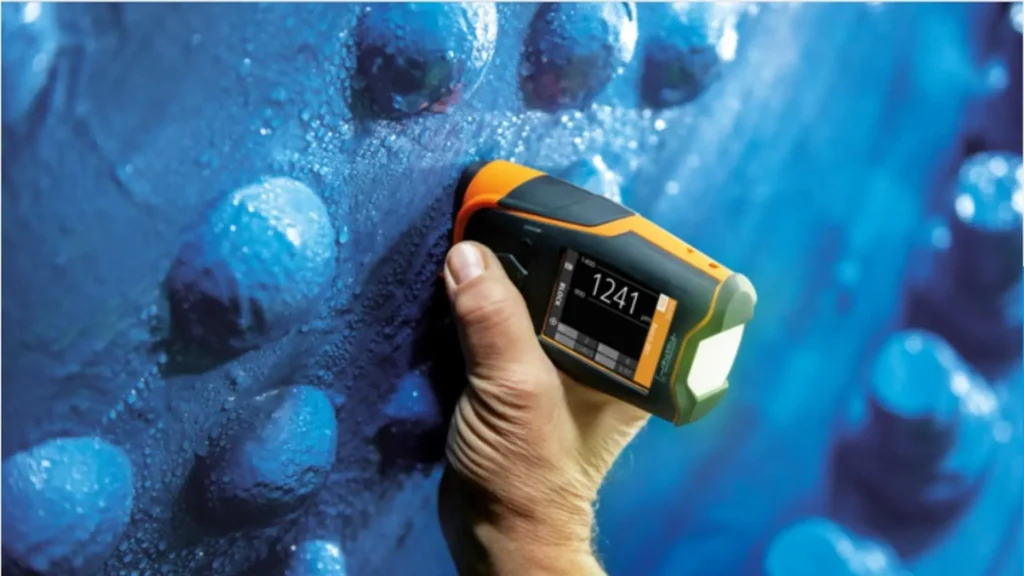
- Thickness measurement of metal sheets and foils: In the production of metal sheets and foils, maintaining a constant thickness is essential to ensure product quality. Eddy current thickness measurement provides a fast and accurate method for measuring the thickness of thin metallic materials. This is particularly important in industries such as aerospace, electronics, pressure vessel construction, and packaging, where accurate material dimensions are critical.
- Thickness measurement of thin conductive layers: It is also possible to measure the thickness of a thin layer of metal on a metallic substrate, provided that the two metals have very different electrical conductivities (e.g, silver on lead). A frequency must be selected such that there is complete penetration of Eddy currents into the layer, but not into the substrate itself4.
- Thin Pipe and Tube Inspection: The ECT is widely used in the inspection of thin pipes and tubes, especially in the oil and gas industry. It is effective in measuring the wall thickness of conductive materials and detecting corrosion or thinning in metallic pipes, such as heat exchanger tubes. This application is vital to ensure the integrity of pipelines and prevent leaks that could cause unplanned shutdowns.
- Quality control in manufacturing: In many manufacturing processes, maintaining the correct thickness of materials is crucial to product performance and durability. ECT thickness measurement systems are integrated into production lines to continuously monitor the thickness of materials, ensuring that they meet specified tolerances. This application is common in the production of components such as sheet metal, wire, and extrusions.
Methods of coating thickness measurement by ECT
For the measurement of coatings on conductive and non-conductive substrates, use is made of a probe. It consists of an iron core around which an excitation or induction coil and a second measuring coil are wound, passing an alternating current in the excitation coil. For the eddy current method, a single coil can be used.
When the iron core with the two coils is brought close to a magnetizable object such as iron, the iron strengthens the alternating magnetic field. The measuring coil registers this gain as a voltage5. The greater the distance between the pole and the piece of iron, the greater the potential difference. This separation corresponds to the thickness of the coating on the workpiece. Figure 3, shows the measuring principle.
Depending on the substrate on which the coating is applied, there are two measurement methods:
- Magnetic-inductive effect: When the field coil is excited at a very low test frequency, the magnetic permeability of the ferromagnetic base material is used to measure the thickness of non-ferromagnetic coatings such as copper and zinc5.
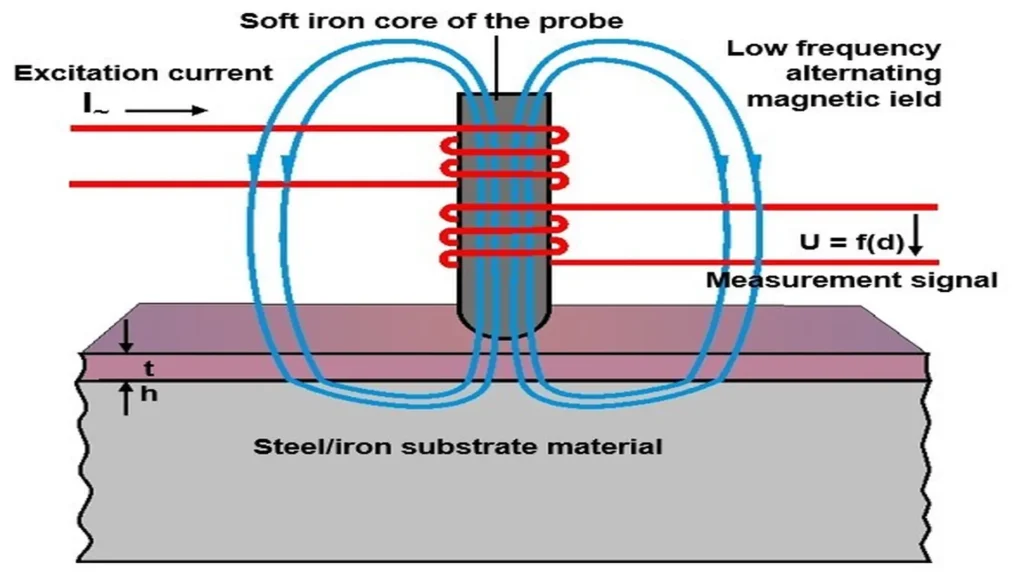
- Eddy current effect: When the field coil is excited with a high test frequency, the electrical conductivity of electrically conductive base materials is used to measure the thickness of non-electrically conductive coatings such as paint, varnish, anodizing, etc3. In this method, a single coil can be used.
The two different methods used are the magnetic-inductive principle and the eddy current principle. Both principles are explained in the following video. Courtesy of PHYNIX GmbH & Co. KG.

Measurement principles for coating thickness gauges.
Advantages of ECT thickness gauging
The Eddy Current Thickness Gauge offers several advantages over other thickness measurement techniques, making it a preferred choice in many applications:
- Non-contact measurement: One of the main benefits of ECT is that it does not require physical contact with the material, i.e. without the application of a coupling medium as in the case of Ultrasonic Testing (UT) and the use of piezoelectric transducers. This is particularly useful for measuring delicate or coated surfaces where contact could cause damage.
- High accuracy and resolution: Eddy current-based devices can measure thickness with high accuracy, often down to micrometers, making them suitable for applications requiring precise measurements.
- Fast and efficient: The technique enables fast measurement, which is ideal for use on automated production lines or for inspecting large areas quickly.
- Ability to measure non-conductive coatings: ECT is particularly effective for measuring the thickness of non-conductive coatings on conductive substrates, a task that is challenging for other measurement methods.
Limitations of Eddy Current thickness measurement
Although eddy current thickness measurement is a powerful technique, it has certain limitations:
- Material dependence: The accuracy of the measurement is highly dependent on material properties such as conductivity and permeability. Variations in these properties can lead to measurement errors.
- Limited penetration depth: Eddy currents are confined to the material surface, making it difficult to measure the thickness of thick materials or to detect defects at depth.
- Calibration requirements: Eddy current devices require careful calibration to ensure accurate measurements. This can be a time-consuming process, especially when measuring different types of materials.
- Sensitivity to surface conditions: The presence of surface roughness, contaminants or coatings can affect measurement accuracy, as these factors influence eddy current distribution.
Conclusion
Thickness determination through the use of the Eddy Current Thickness Gauge is a versatile and widely used technique in various industries for non-destructive inspection and material characterization. Its ability to provide accurate, fast, and non-contact measurements makes it indispensable in applications ranging from coating thickness measurement to thin-walled pipe inspection.
However, the method’s dependence on material properties and surface conditions requires careful consideration and calibration to ensure accurate results. Despite its limitations, eddy current thickness measurement remains a critical tool for maintaining quality and safety in numerous industrial processes.
References
- https://www.nde-ed.org/NDETechniques/EddyCurrent/Graphics/ImpedancePlane.gif
- QIUPING MA, GUI YUN TIAN, BIN GAO, XIANGYU ZHAO, GAIGE RU, HAORAN LI. Lift-off suppression based on combination of bridge and transformer signal conditionings of eddy current testing; Consulted on August 12, 2024.
- https://www.sciencedirect.com/science/article/pii/S0963869522001232#:~:text=Lift%2Doff%20is%20defined%20as%20the%20distance%20between%20the%20sensor%20probe%20and%20the%20conductive%20surface.%20It%20is%20a%20prominent%20impaction%20factor%20in%20the%20electromagnetic%20non%2Ddestructive%20testing%20and%20evaluation%20field%20(NDT%26E)
https://world.helmut-fischer.com/es/tecnicas/medicion-de-espesor-de-revestimiento-inductivo-magnetico - UNIVERSIDAD DEL ESTADO DE IOWA. Eddy Current Testing; Consulted on August 13, 2024. https://www.nde-ed.org/NDETechniques/EddyCurrent/Applications/thicknessmeasurements.xhtml#:~:text=It%20is%20also,ferromagnetic%20metal%20bases.
- Marc Oliver Albrecht. What is Eddy Current Testing?; Consulted on August 13, 2024. https://blog.foerstergroup.com/en/component-testing/what-is-an-eddy-current-test#:~:text=When%20the%20iron%20core%20with%20the%20two%20coils%20approaches%20a%20magnetizable%20object%2C%20iron%2C%20the%20iron%20strengthens%20the%20alternating%20magnetic%20field