One of the relatively new Non-Destructive Testing techniques is Thermography in the aerospace industry , it is important to periodically evaluate the integrity of the composite materials used in the aerospace industry to guarantee their safety and reliability.
Composite materials are widely used in the aerospace industry due to their high strength and stiffness relative to their weight. These materials can be used to make structural parts like wings, fuselages, and engine components. However, the quality of these materials can deteriorate over time due to factors such as exposure to high temperatures, vibration, and fatigue.
With the increase in the use of composite materials in the aeronautical industry, it is necessary to implement new inspection techniques to ensure that the structures made with these materials are properly inspected. In general, major flight parts, such as ailerons, rudders, elevators, and fairings, are made of structural composite materials, such as solid laminates and sandwich panels.
Modern aircraft, such as the B787, can have the fuselage made of carbon fiber reinforced plastics (CFRP), which means that inspection and damage analysis programs must include non-destructive detection (NDT) techniques capable of identifying damage. such as delaminations, detachments and the presence of humidity. For A310 aircraft, the rudder is made of a panel of carbon fiber layers oriented in the 0, 45 and 90 directions, reinforced with a polyamide (NOMEX) core in honeycomb configuration.
One of the most used techniques in the failure analysis of these materials in the Aerospace industry is Thermography , which is used to evaluate the integrity of composite materials. This technique is based on the measurement of the temperature distribution on the surface of the material. Variable that can be influenced by the presence of defects in the material, such as cracks, delaminations and air bubbles. These defects can cause changes in the way the material’s surface temperature is distributed, and these changes can be detected.
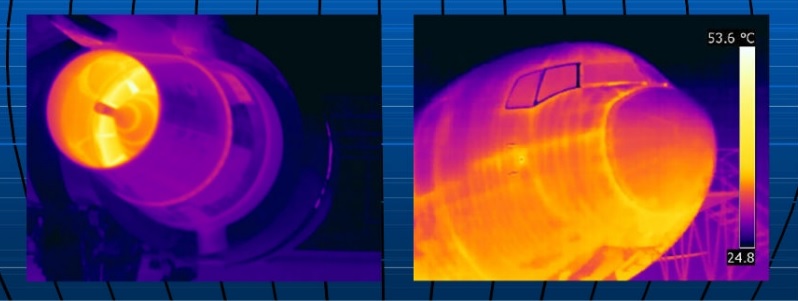
Most used thermographic techniques:
Infrared thermography: This technique uses infrared cameras to measure the temperature distribution on the surface of the material, it is used to detect defects on the surface of the material, such as cracks, stress areas, and it is also used to evaluate the quality of the bond between two different materials, as in the weld between two plates of metallic materials.
Thermal Pulse Thermography: Used to measure the thermal conductivity and diffusivity of materials, using a pulse of heat to heat the surface of an object, and then measuring the temperature distribution as the object cools
Laser scanning thermography: Uses a laser to scan the surface of an object and measures the temperature distribution of the surface as the object cools. It is also used to measure the thermal conductivity and diffusivity of materials.
Application of Thermography in the aerospace industry
Thermography is used in a wide variety of applications, including:
Structural Integrity Assessment: Used to detect defects in composite materials, such as cracks, delaminations, and air bubbles. Early detection of these defects can prevent catastrophic failure of the structure.
Evaluation of the quality of welds: It is used to evaluate the quality of the weld between two plates of material, through its use the temperature distribution is measured and any defect is detected, such as air bubbles or lack of union.
Detection of damaged areas during service: It is also used to detect damaged areas in composite materials during service. For example, if a structural part is exposed to high temperatures or vibrations, it may suffer damage that is not visible to the naked eye. Through this technique, these damages can be detected and their severity evaluated.
Evaluation of the quality of the manufacturing process: Early detection of defects in the manufacturing process can prevent problems in the structural integrity of the composite material. Thermography is used to assess the quality of the manufacturing process of composite materials.
Spare Parts Inspection: To inspect spare parts prior to installation. This helps ensure that replacement parts are of the same quality as the original parts and are free of defects.
Inspection of aeronautical structures
In the aeronautical industry, specifically, the best-known applications of infrared thermography as non-destructive testing are:
Discovery of inclusion of water in the aerodynamic surfaces of airplanes.
Inspection of aircraft fuselages, Dynamic fatigue analysis.
Lack of adhesion in composite materials and evaluation of spot welding.
Impact damage in composite materials
Porosity and Thickness measure of depth in composite materials.
Paint adhesion, Corrosion under paint.
Vacuum, air entrapment and deformations in plastic material (polymer)
Benefits of thermography in the aerospace industry
Thermography has several benefits in the aerospace industry, including:
It is a non-destructive testing technique that does not damage the material during evaluation.
Detect defects in composite materials before they cause structural failure.
It allows to reveal defects that are difficult to detect by other means, such as visual inspection.
Reduces costs, since it allows to evaluate large areas of material in a short time
Challenges of thermography in the aerospace industry
Despite the benefits of thermography in the aerospace industry, there are also challenges, including:
Interpretation of thermography results can be difficult. It is necessary to have personnel trained in the interpretation of thermographic images to obtain accurate results.
It can only detect defects on the surface of the material. It cannot detect defects inside the material.
Environmental conditions, such as temperature and humidity, can affect thermography results. It is necessary to take measures to control the environmental conditions during the evaluation.
Conclusion
Thermography is a non-destructive testing technique used in the aerospace industry to assess the integrity of composite materials. Thermography is based on the measurement of the temperature distribution on the surface of the material, which can be influenced by the presence of defects in the material. Thermography is used to assess the structural integrity of composite materials, the quality of the adhesive bond, the detection of areas of damage.
Bibliographic references
ASTM D4788-13(2019), Standard Test Method for Detecting Delamination in Bridge Decks Using Infrared Thermography, ASTM International, West Conshohocken, PA, 2019, www.astm.org.
Buss, K., & Baqersad, J. (2017). NDT Applications for Composites in the Aerospace Industry. Materials Evaluation, 75(11), 1314-1321.
Ghazi Wakili, K., Gharibdoust, SA, & Roshani, H. (2016). Nondestructive evaluation of composite materials: A review. Journal of Reinforced Plastics and Composites, 35(22), 1661-1677.
DD Dillard, WP Winfree, TE Jenkins, DA Felton, TW Jackson, and JC Duke, “NDE of Adhesive Bonded Composite Aircraft Structures Using Active Thermography,” in Nondestructive Evaluation of Aging Aircraft, Airports, and Aerospace Hardware II, vol. 3399, L. P. Sadler and J. D. Lindley, Eds. SPIE, 1998, p. 81-91.