Table of Contents
Introduction
In many industrial components, the generation and distribution of heat provides information about their good performance or any anomaly in its operation, so the temperature is an important variable for monitoring and predicting the behavior and information of the physical condition of these assets in order to plan the best time for maintenance work.
Predictive maintenance is a procedure by which, through the use of non-destructive analysis tools and techniques, detects anomalies in the operation and possible defects in equipment and processes, in order to reduce downtime and operating costs by anticipating failures before they occur.
Among the various tools and techniques used in predictive maintenance, thermography has become, over the years, an efficient and non-invasive method to identify problems before they become critical by monitoring the distribution of temperatures. This article delves into the role of thermography in the optimization of predictive maintenance, highlighting its benefits, applications and best practices for implementation.
Understanding predictive maintenance
Predictive maintenance consists of monitoring the condition of equipment during its regular operation to detect possible failures and consequently schedule maintenance activities. This strategy contrasts with traditional maintenance approaches, such as corrective maintenance, where repairs are performed after a failure occurs, and preventive maintenance, where maintenance is scheduled at regular intervals regardless of the condition of the equipment.
The main objective of predictive maintenance is to improve equipment reliability and efficiency, minimize unexpected downtime and extend equipment life. By considering advanced data and technologies, predictive maintenance enables organizations to make informed decisions, optimize resource allocation and improve overall operational performance.
Non-destructive analysis through infrared thermography
Thermography is a non-destructive testing method which, through the use of infrared radiation, generates images of the distribution of temperatures on the surface of an object. Through non-destructive analysis, these variations can indicate problems or anomalies associated with overheating, external insulation or internal refractory problems, electrical failures, mechanical wear, among others. Thermal imaging cameras detect electromagnetic radiation in the infrared spectrum emitted by objects and convert it into visible images, allowing technicians to visualize and analyze temperature patterns.
Thermography is a significant technique in predictive maintenance because it provides a non-destructive and non-invasive means of analysis to assess the condition of equipment. By identifying abnormal temperature patterns, this technique helps to detect potential problems early, allowing timely intervention and preventing costly failures.
Benefits of using thermography in predictive maintenance
Early detection of problems
One of the most significant advantages of thermography is its ability to detect problems at an early stage. By identifying abnormal heat patterns through nondestructive analysis, thermography can reveal problems such as poorly fastened electrical connections, bearing failures, insulation problems, poor flame distribution inside a furnace firebox, clogged pipes, among others, long before they cause equipment failure or collapse. Early detection allows maintenance personnel to address problems proactively, reducing the risk of unexpected downtime and costly repairs.
Non-destructive and non-intrusive method
Thermography is a non-destructive testing method (NDT) and a predictive maintenance technique (PDM), which means that it does not damage or alter the equipment being inspected and a predictive maintenance method. This feature is of great importance in predictive maintenance because it allows continuous monitoring and non-destructive analysis without interrupting normal operations. In addition, thermographic inspections can be performed from a safe distance, reducing the need for direct contact with hazardous equipment.
Complete inspections
Thermal imaging cameras can quickly scan large areas and multiple components, providing a complete visualization of equipment status. This procedure is particularly useful in complex industrial environments where it is essential to identify problems in various systems and components. Through non-destructive analysis, thermography allows maintenance teams to prioritize inspections and focus on areas requiring immediate attention.
Cost savings
The implementation of thermography in predictive maintenance can lead to significant cost savings. By detecting and addressing problems early, organizations can avoid costly unplanned downtime, reduce the frequency of major repairs and extend the life of critical equipment. In addition, thermographic inspections can optimize maintenance schedules, ensuring that resources are allocated efficiently and minimizing unnecessary maintenance activities.
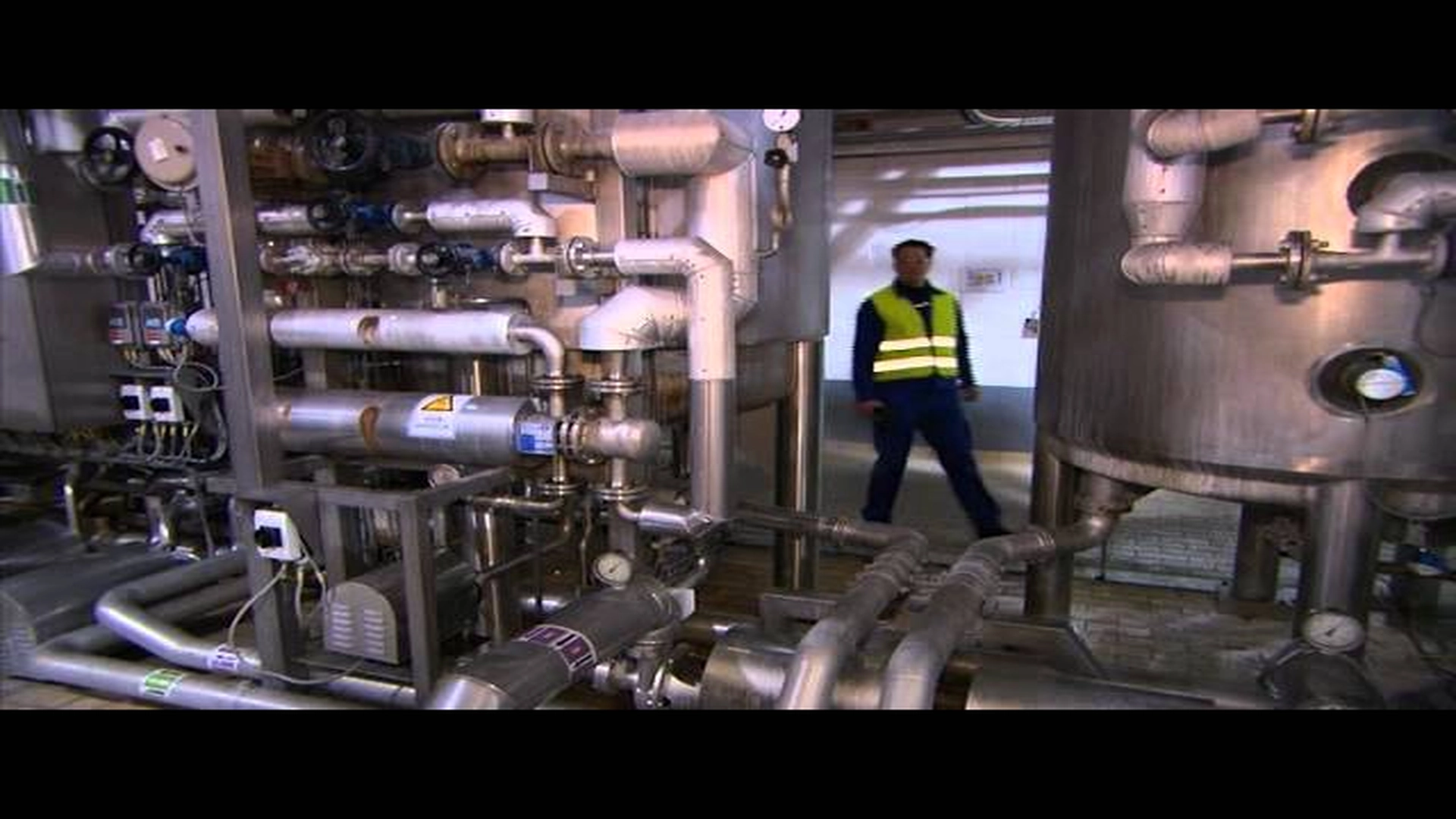
Infrared thermography for maintenance.
Thermography applications in predictive maintenance
Electrical systems
Electrical systems are prone to a variety of problems, such as poorly fixed connections, overloaded circuits and insulation damage. These problems generate increased heat, leading to equipment failure and potential safety hazards. Thermography is very effective in identifying abnormal heat patterns in electrical components, even in small deviations or changes, allowing maintenance teams to address problems before they become serious. Common applications include the inspection of transmission networks, transformers, circuit breakers, and electrical panels.
Mechanical systems
Mechanical systems, such as motors, bearings and gearboxes, can also benefit from and are a major application area for thermographic inspections. Excessive friction, misalignment and lubrication problems can cause abnormal heat generation, leading to mechanical failure. Thermography can detect these heat patterns, allowing maintenance teams to perform targeted interventions. For example, thermographic inspections of rotating equipment can identify hot spots that indicate bearing wear or misalignment, enabling timely maintenance.
Combustion furnaces
Tubes in the radiant zone of a furnace firebox overheat causing ruptures, resulting in uncontrolled fire and other collateral damage. Damage to the refractory material and improper burner alignment can also cause overheating and ruptures in specific areas, resulting in downtime and risk to personnel working nearby.
The above demonstrates the importance of nondestructive thermography analysis to externally monitor the firebox walls to anticipate damage to the internal refractory, as well as to monitor the tubes inside to determine if localized internal coking or poor flame heat distribution is occurring, shortening the life of the tubes and potentially causing breakage.
On the other hand, the visualization through thermographic images of the pipes of the home and as a result of a frequent inspection program, help to better estimate the life of the pipes compared to fixed monitoring instruments (e.g. contact thermocouples), since the latter only measure at certain points of the home.
Maintenance of buildings and facilities
Thermography is valuable in maintaining the integrity of buildings and facilities. It can identify insulation deficiencies, moisture infiltration and structural problems that can compromise building performance and safety. By detecting temperature variations in walls, ceilings and HVAC systems, infrared thermography helps facility managers optimize energy efficiency, prevent structural damage and ensure occupant comfort.
Process monitoring
In industrial processes, maintaining optimal operating conditions is critical to efficiency and product quality. Thermography is used to monitor the temperature of various process components, such as boilers, heat exchangers and piping, to ensure that they operate within safe and efficient parameters. Any deviation from normal temperature patterns may indicate potential problems that require immediate attention.
On the other hand, during process monitoring using infrared thermography, problems can be detected during the operation of the process units, such as obstruction in pipelines, failures in the opening or closing of valves, detachment of internal refractory in pipelines and pressure vessels, among others. A special application of thermography is the monitoring of fuel gas pipelines for leak detection, for which special thermographic cameras are available for this application.
Best practices for implementing thermography in predictive maintenance
Selection of suitable equipment
Choosing the right thermographic equipment is essential for accurate and reliable inspections. Factors to consider include camera resolution, temperature range, field of view, wave type and sensitivity.
- Resolution: Higher resolution cameras provide more detailed images, while a wider temperature range allows for versatile applications.
- Field of View (FOV): The field of view is determined by the camera lens; for close-up work, you need a lens with a wide-angle FOV (45° or greater). For long distance work, you need a telephoto lens (12° or 6°)1.
- Wave type or spectral range: Shortwave thermal imaging cameras are used for inspecting pipes in radiant areas of furnaces through flames, medium wave for detecting combustible gas leaks and long wave for exterior surfaces.
- Sensitivity: Sensitivity is essential for detecting small temperature variations that may indicate problems at an early stage.
Training and certification
Proper training and certification are essential for personnel performing thermographic inspections in order to demonstrate the competence of the personnel performing these inspections and their reliable results. Technicians should be familiar with infrared theory, camera operation, area of application and data interpretation.
Certification programs, such as those offered by the Infrared Training Center (ITC), exclusive to this test method, or the American Society for Nondestructive Testing (ASNT), ensure that technicians have the skills and knowledge necessary to perform accurate and reliable inspections.
Inspection programs
Thermographic inspections must be carried out through an inspection plan where evaluations are performed with the appropriate frequency for each component to be inspected. The frequency of inspections depends on factors such as equipment criticality, operating conditions and historical data. Regular inspections help track temperature trends over time, allowing early detection of emerging problems, estimation of component life and proactive maintenance planning.
Data analysis and reporting
Effective nondestructive data analysis and reporting are crucial to take advantage of the results of thermographic inspections. Advanced software tools can help analyze thermographic data, identify trends and generate actionable information.
Complete reports should include thermograms, temperature data and recommendations for corrective actions. Clear and concise reporting ensures that maintenance teams and decision makers have the information they need to take appropriate action.
Integration with other predictive maintenance technologies
The integration of thermography with other predictive maintenance technologies, such as: vibration analysis, ultrasound testing and oil analysis, provides further information on the condition of the equipment. Combining multiple data sources improves the accuracy and reliability of predictive maintenance programs, enabling more informed decision making and optimized maintenance strategies.
If the temperature is noticeably different from previous readings, facilities can use other maintenance technologies (vibration, motor circuit analysis, airborne ultrasound and lubricant analysis) to investigate the source of the problem and determine the next course of action2.
Conclusion
Thermography is a fundamental technique in predictive maintenance, through its use we obtain early detection of problems, non-destructive inspections, complete evaluations and significant cost savings. By integrating thermographic inspections into maintenance programs, organizations can improve equipment reliability, minimize downtime and improve overall operational efficiency. As technology advances and training programs become more accessible, the adoption of thermography in predictive maintenance is expected to grow, driving innovation and excellence in asset management.
References
- TELEDINE FLIR. Thermal camera specifications you should know before you buy; Accessed on July 01, 2024. https://www.flir.com.mx/discover/professional-tools/thermal-camera-specs-you-should-know-before-buying/
- FLUKE. Thermal imaging in preventive maintenance programs; Accessed July 03, 2024. https://www.fluke.com/en-us/learn/blog/thermal-imaging/preventive-maintenance