Internal corrosion in pipes intensifies over time, decreasing the wall thickness of these assets, causing erosion failures, and clogging of pipes and fittings. Corrosion affects different types of metals that are used in various industrial plants, generating failures, defects and causing leaks. Few methods currently exist to detect these types of failures before they cause damage. The pipeline is usually repaired and re-inspected. The use of adequate technology can limit the impact of leaks in pipes and ducts, and bring significant savings to industrial operators.
As the infrastructure of these systems deteriorates, an increasing number of leaks begin to form that can cause environmental and human catastrophes, translating into high costs for companies. To combat this problem, some pipelines without leak detection systems are being retrofitted, while those with built-in detection systems are being reviewed and upgraded to improve reliability and performance. While it is understood that a leak detection system cannot reduce the probability of leak failure, the application of advanced technology in the field can help reduce the consequence of any leak significantly.
An ideal leak detection system should have the ability to:
» Detect leaks below 0.0001% (1 part per million).
» Specify the location of leaks at less than 1 meter.
» Generate zero false alarms.
» Be modern in existing pipes.
» Work under transient, stationary and shutdown conditions.
» Being a low-cost installation and maintenance system.
The reality of currently available technologies and techniques is somewhat different from an ideal system, but advances in the field continue to provide improvements. The largely available leak detection technologies can be divided into two groups:
» External methods that physically detect the presence of a leak.
» Internal methods that use field sensor outputs such as flow and pressure to infer a computationally based leak.
The most common ultrasonic inspection techniques involve the use of Free Waves (bulk waves) whose propagation mode is not affected by the boundary conditions of the inspected part. There are 2 types of free waves: longitudinal and transverse, and they are mainly used to inspect areas close to the transducer.
On the other hand, the guided waves (guided waves) propagate following the limits of the inspected piece, and therefore the geometry of said piece affects the mode of propagation (Figure 1). Unlike free waves, there are hundreds of types of guided waves with different speeds and frequencies in a given part geometry. The number of modes exponentially increases the complexity of the analysis, but also opens the door to countless applications of ultrasound.
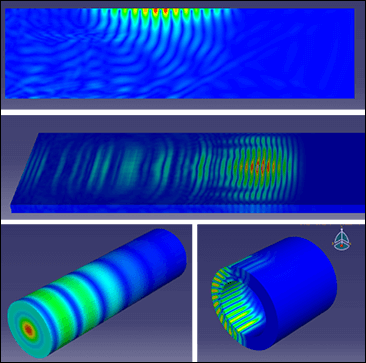
In this context, the research institute, Southwest Research Institute (SwRI) has created the next generation of transducers that use ultrasound guided wave technology to detect anomalies in pipes, allowing operators to prevent leaks in a preventive way.
Originally developed by SwRI in 2002, the technology is known as magnetostrictive transducer collar (MsT). The updated version has a flat and slim design, allowing it to be used on pipes in tight spaces. The new MST design also features eight sensors that give the transducer the ability to constantly monitor the condition of the pipeline and accurately identify and locate pipeline corrosion damage and faults in order to prevent leaks from occurring in the first place. place.
The device can withstand temperatures up to 400 degrees Fahrenheit in custom settings. The device uses the magnetostrictive sensor (MsS) developed by SwRI, which generates and receives guided waves that propagate along an elongated structure, guided by its limits. This technique allows waves to travel long distances with little energy loss. In some cases, hundreds of meters can be surveyed from a single location, although obstacles such as couplings would require an additional sensor.
“Instead of using one sensor to cover the entire circumference of a pipe, allowing only the axial location of an anomaly to be measured, we now have eight sensors on the transducer,” said SwRI staff engineer Sergey Vinogradov, who developed technology with staff engineer Keith. Bartels and other SwRI staff members. “Each of the sensors is independently connected to the electronics so that all possible guided wave signals can be acquired. Algorithms combine this information to better detect and locate the anomaly both axially and circumferentially, and corrosion growth can be monitored by examining data sets acquired over time.”
The MsS system can send data to a remote terminal through a wireless transmitter unit or through a wired connection. It is primarily designed for oil and gas transmission pipelines to prevent costly and damaging leaks before they start. However, the technology is versatile and has been used for other industrial sectors, such as those used for water, heating or chemical plants.
Bibliographic references: