In recent years, advances in ultrasound technologies have been significant in the industry. The application of these technologies has made it possible to improve the efficiency and precision of industrial processes.
Industrial ultrasound is a non-destructive technique that uses high-frequency sound waves to detect and prevent failures in critical equipment , measure thicknesses, determine mechanical properties, and perform other measurements. In this technical article, the most recent advances in ultrasound technologies in the industry will be presented.
Technological advances in critical equipment
High frequency ultrasound
High frequency ultrasound has become one of the most important technologies in the industry. This technique is used to inspect materials and detect internal defects. The main advantage of this technique is that it can detect very small defects with high spatial resolution. The most recent advances in this Ultrasound technology include the use of high-frequency piezoelectric transducers, the use of multiple transducers of different frequencies, and the incorporation of advanced signal processing techniques. These improvements have allowed greater sensitivity and precision in the detection of defects in materials.
Ultrasound tomography
Ultrasound tomography is a technique that uses multiple transducers to acquire ultrasound data from different angles. An image reconstruction algorithm is then used to create a three-dimensional image of the object.
This technique is used in industry to inspect complex materials and components. Recent advances in this technology include improving image quality, reducing data acquisition time, and incorporating machine learning techniques to improve accuracy and processing speed.
The use of industrial ultrasound reflection-mode tomography has been investigated primarily with a small number of transducers, often only two. In a typical setup, one sensor is stationary while a second sensor rotates around a circular arc, taking a series of topographic measurements that are used to reconstruct an image.
While this arrangement allows measurements to be made from a large number of positions around an object (sometimes more than 100 positions), it is not fast enough to provide the real-time information required by many industrial processes. This technique describes a reflective mode ultrasound system with a circular array of 36 transducers that is capable of generating reconstructed images at an average of 30 frames per second.
Achieving this speed of image reconstruction requires intensive use of processing resources. An array of parallel processors is used for image frame reconstruction and data acquisition is assisted by a digital signal processor (DSP).
The results obtained by this system in the form of images, with a resolution of 100 × 100 pixels, show that good results can be obtained with ultrasonic tomography systems in the scanned configuration.
Total focusing ultrasound (TFM)
The total focusing ultrasound method or Total Focusing Method (TFM) is a recent technique for non-destructively evaluating equipment and structures. This method is based on the conventional Phased Array orientation and focusing methodology, but differs with the focusing being applied to all parts of the area to be inspected and not just to a fixed depth.
The hallmark of Phased Array ultrasound technology is its ability to focus on any position on a part under inspection applying delays, either on emission or reception, to synchronize the time of flight of short signals driven into the position of interest. In the sample focal area, the full width of the generated acoustic beam becomes smaller and the corresponding detection resolution increases dramatically.
The total targeting method is a natural extension of this ability. This produces a focused beam through the focusing of multi-element ultrasound (Phased Array) and its dispersion in each position over a region of interest in the area of the inspected piece; furthermore, only highly resolved focused data points are presented to the operator.
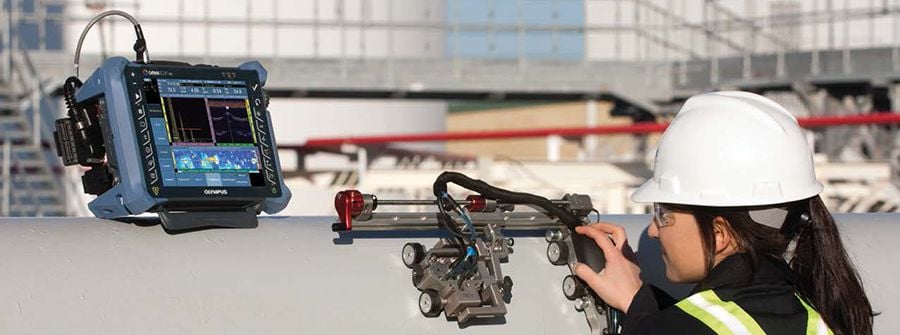
Often the region of interest consists of a uniform Cartesian grid of all required focusing targets. Obviously, achieving this focusing at each grid position, using the physical beamforming technique in a conventional manner, can be time consuming due to the period of physical acoustic propagation that is required to reach each position of interest.
Since typical ultrasound acoustic waves for NDT applications are linear, the result of physical beamforming, which results from the superposition of the current acoustic fields for all contributing elements at a specific aperture, can be mimicked by a subsequent acquisition process based on the data set from the Full Matrix Capture (FMC) .
Recovery of the FMC data set requires recording the signal from all the elements that make up the received aperture while an acoustic emission is generated for each individual element included in said emission aperture. As such, the FMC data set is made up of multiple elemental A-scans based on all combinations of the sent and received elements.
Shear wave ultrasound
Shear wave ultrasound is a technique used to measure the elasticity and density of materials. This technique is used in the industry to assess the integrity of components. The most recent advances in this technology include the use of high-frequency piezoelectric transducers and the incorporation of advanced signal processing techniques. These improvements have allowed greater precision and sensitivity in the measurement of the mechanical properties of materials.
Shear wave ultrasound technologies is a technique that consists of using predefined angles to identify subsurface anomalies that are not directly below the transducer itself. Defects in materials or welds reflect ultrasonic energy back to the transducer and are presented as A-scans where operators can analyze relevant component integrity information.
Short-range wave ultrasound
It is a technique of applying guided ultrasonic sound waves that uses special types of probes. When the guided waves strike the discontinuities, the mode converted sound is reflected and received by the transducer.
The main benefit of this technique is that it can be used to detect corrosion in plates and pipes that are inaccessible due to support structures, braces, corbels, saddles, feet, critical tank areas, under insulation or other types of obstructions in the path of the region of interest. Another application is steel structures covered or surrounded by concrete.
A specially designed ultrasonic transducer is used to generate short-range guided waves. The probe is generally scanned over a region that is easily accessible and free of surface irregularities, looking in the direction of the region of interest that is generally inaccessible due to supporting structures or the pure geometry of the test object. The scanning range of this technique is up to two meters.
Integration of ultrasound with other inspection systems
In industry, it is often necessary to use several different inspection systems to assess the quality of equipment and components. The most recent advances in ultrasound technologies have allowed the integration of ultrasound systems with other inspection systems, such as infrared cameras, X-rays and computed tomography. This allows a more complete evaluation of materials and components and a greater precision in the detection of defects.
For in-service inspection of orbital welds on pipelines and equipment operating at temperatures up to 200°C, two different non-destructive testing methods and respective inspection systems can be combined to cover the detection of all possible faulty weld conditions. . The system combines ultrasonic and eddy current techniques with dedicated approaches to deal with high temperature conditions.
Phased array ultrasound is employed to search for volumetric defects within the weld bead, while eddy currents are used to search for surface and subsurface cracks. Phased array ultrasonic results showed the effectiveness of the cooling mechanisms and that the effects of temperature on sound attenuation can be easily compensated up to 200 °C. Eddy current results show almost no influence when temperatures are raised up to 300 °C.
High power ultrasound
High power ultrasound is a technique that uses high amplitude ultrasound waves to activate chemical and physical processes in materials. This technique is used in industry for cleaning, welding, melting, and other applications. The most recent advances in this technology include improving energy efficiency and reducing processing time. In addition, techniques for controlling the power and frequency of ultrasound waves have been developed to optimize the activation process.
High power ultrasound continues to be developed, particularly when applied to fluids and multiphase media (gases or liquids with particles, drops or bubbles in suspension and/or porous solids with fluids inside); For which, a new type of ultrasonic power generator for fluid applications (stepped plate transducers) has been developed that presented excellent performance and directionality characteristics.
Using this new type of generator, a series of applications of high-intensity ultrasound in multiphase media have been researched and developed, such as: the precipitation of fine particles in industrial fumes, the elimination of foams, the dehydration of food, the drying of pasta in the extraction of minerals, the washing of textiles and the atomization of liquid layers.
Conclusions
The most recent advances in ultrasound technologies have made it possible to significantly improve the efficiency and precision of industrial processes. The sensitivity and precision of defect detection, the quality of the images, the processing speed, the integration with other inspection systems and the use of machine learning techniques and power and frequency control are some of the main advances in this area. .
Sources
- https://sonatest.com/blog/understanding-propagation-mode-total-focusing-method-tfm-1#:~:text=The %20Total% 20Focusing %20Method% 20(TFM,the %20image% 20as %20it% 20should .
- https://www.zetec.com/es/how-fmc-and-tfm-work-together-for-more-effective-ultrasonic-inspections/
- https://www.olympus-ims.com/es/phased-array-ultrasound-as-a-replacement-for-radiography/