Introduction
Corrosion works 24 hours a day, 365 days a year, and does not require a quote to do its job, do you?
Have you established how much you have to invest annually to replace parts and structures due to corrosion damage? If he had adequately prevented, how much could he have
be part of your profit, or what portion of your potential profit was lost to corrosion?
Can you really turn some of the corrosion losses into profit?
What is the most difficult thing about the fight against corrosion?
From the moment of their manufacture, metals show an inherent tendency to react with the environment in which they are found (atmosphere, soil, water, etc.). The process is natural and spontaneous: corrosion is thermodynamically unavoidable. Each year between 10-20% of the world’s metal production is lost.
Normally corrosion losses are classified as:
- direct
Related to breakage and/or complete replacement of equipment and
costs of protective measures. Examples:
• Repair and Maintenance.
• Materials with greater chemical resistance.
• Application of coatings.
• Conditioning, packaging and preservation.
• Use of skilled labor. - indirect
• Related to lack of production due to temporary unemployment,
leaks-losses or contamination of products.
• Penalties for non-delivery, damage to third parties, etc.
• Loss of reliability and image of the company before third parties.
To combat corrosion, it is very important to know the mechanisms that produce it and the most appropriate means of control. Due to ignorance, expensive materials and products are used, which are not the most indicated to prevent corrosion problems.
In this sense, it is necessary to identify the different mechanisms of damage and forms of failure as corrosion manifests itself. How and where does it occur? How are they influenced by the environment? Geographical location, is it marine or rural? What emissions are generated by neighboring facilities (macro-environment)? the component is located (microenvironment), the mechanical stresses to which the failing components are seen
exposed (vibrations, tensions, etc.) and even know how the differences in the conditions of the metal surface on the same component (presence of oxide crusts, partially painted, etc.) and variations influence the corrosion progress. or heterogeneities of the environment in which it is exposed (a submerged or buried part and another exposed to the atmosphere, temperature differences, etc.)
Of all the media in which materials can be involved, it is estimated that atmospheric aggressiveness, depending on the levels of contamination, is responsible for more than 50% of corrosion losses. It is convenient to take into account that most of the structures, equipment, tanks and containers are exposed to the atmosphere, so it is very important to characterize the environment where the facility is located (macroenvironment) and the space within the facility. (microenvironment) in which each component is exposed. In short, it ends up being the sum of several effects.
The corrosion specialist must deal with structural corrosion phenomena:
• Exposed to diverse atmospheres and in which they are combined
marine, industrial, etc.
• Submerged in different types of water or fluids, which
from dock pilings to the inner side of pipes,
tanks or containers that transport and/or contain fluids.
• Buried in different types of soils and in very
heterogeneous as in the case of filling zones.
It has to be considered where it is possible that differences in chemical compositions, humidity and contamination levels, climatic variations and mechanical stresses, environmental conditions of the installations can be observed: industries, marine environments, populations that discharge different types of
of sewage. Whoever works in corrosion prevention must develop a broad vision of all the possible influences on each component of the installations. Analyze for each structure, pipes, equipment, tanks and/or containers of the installation its potential to be damaged by corrosion, avoid failure and define what is the way to prevent it, or rather minimize it and how to monitor our effectiveness in protecting them .Most corrosion damage can and should be monitored and inspected with a variety of methodologies, seeking to control its progress. For each medium and type of corrosion there are protection methods, so you must be very accurate in your selection and careful in your installation or application.
There are protection systems that range from the occupation of designs with recognized manufacturing codes, the selection of appropriate materials for the specific service, following good cleaning practices between services, taking care to preserve facilities out of service, using coatings, corrosion inhibitors, cathodic protection and, in some cases, combinations of some of the above.
If we move within an industrial or commercial installation, we could observe that the coating that behaves very well in one area of the installation is not effective in another area, even when used on the same type of material. Not all mechanisms of corrosion damage are due to
the same conditions, nor can they be minimized with a single protection system.
The phenomenon of corrosion in the reinforcing steel of concrete structures is seen daily; It is found that there are corrosion phenomena under the thermal insulation coatings that are so widely used in the industry and, in some cases, those responsible for maintenance realize with surprise
that stainless steels are not ultimately stainless, depending on the medium where they are exposed.
The fight against corrosion is a multidisciplinary team work, but above all a highly organized team based on a strategic plan that allows us to minimize corrosion processes, implementing a protection, monitoring and information management system, without us having to work 24 hours a day, 365 days a year.
Most of the time we just let things happen, can I turn some of the corrosion losses into profit? Carrying out periodic inspections can minimize the damage caused by corrosion.
Strategic plan to monitor corrosion damage
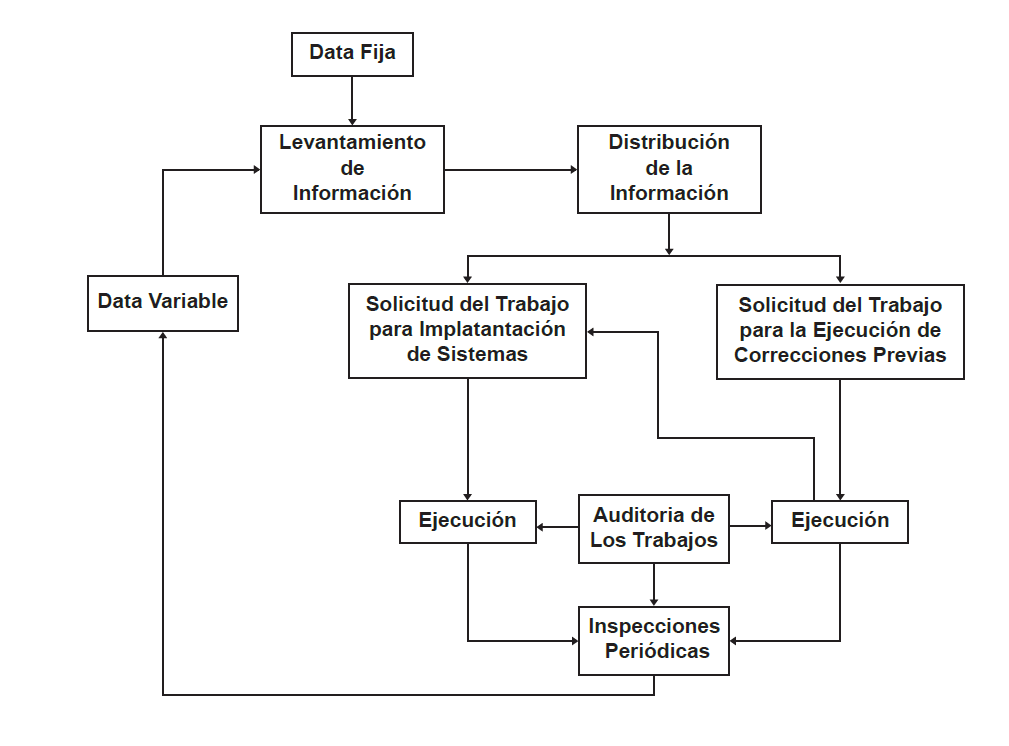
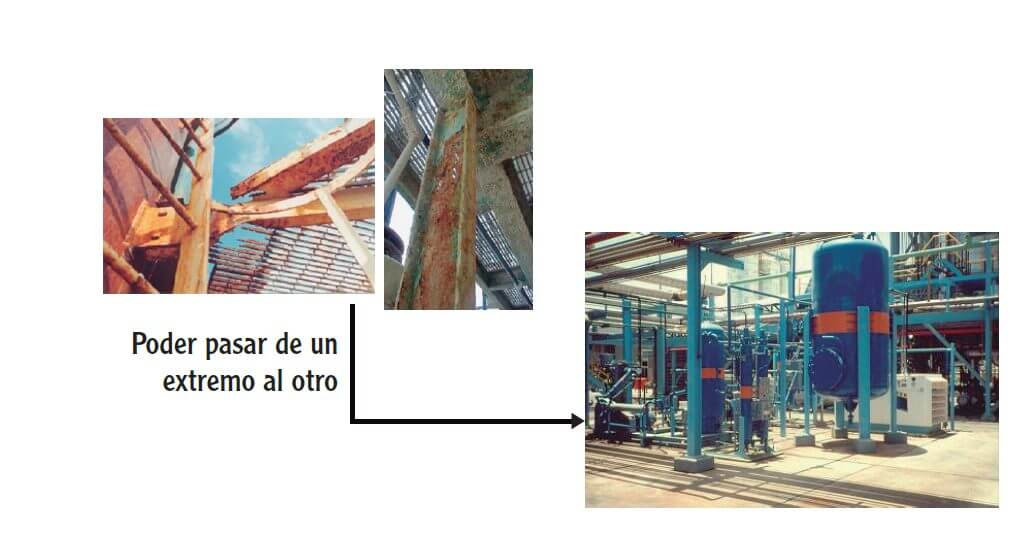
Some examples of the different corrosion damage mechanisms and failure modes
Localized Corrosion:
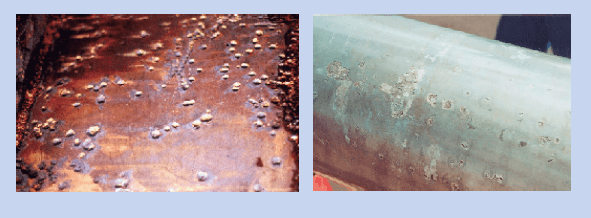
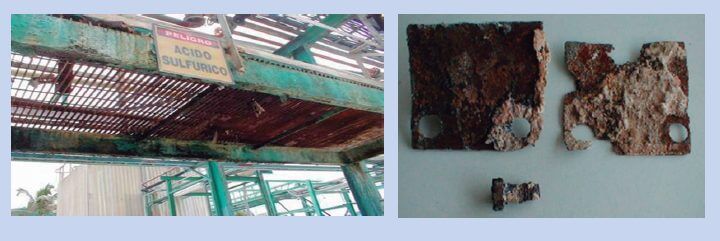
Severe corrosion attack in an acidic environment, due to poor sealing of the container
of sulfuric acid storage in the area of a water plant.
Corrosion-erosion damage:
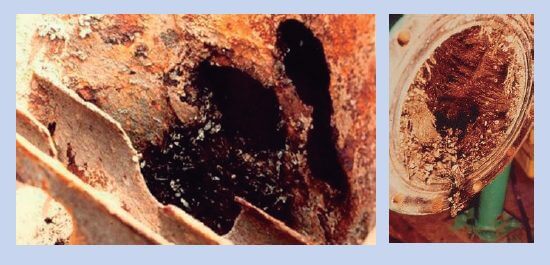
Corrosion-erosion damage: left, in the suction of a seawater circulation pump of
cooling for a thermoelectric plant, due to the effect of suspended solids in the water and
biomass growth that generates corrosion under deposits and aggressive substances; right,
growth of bio-organisms that generate corrosion problems by various mechanisms.
Stress corrosion cracking:
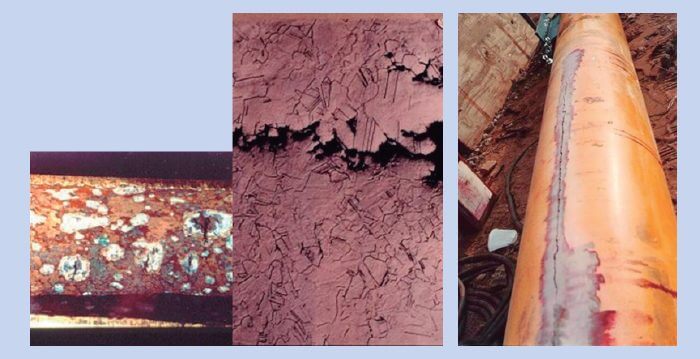
Stress corrosion cracking: left, cupro-nickel tubes in the condenser of a thermoelectric turbine due to the effect of high concentrations of H2S (nearby wastewater discharges); right, a stainless steel pipe, recently installed in a petrochemical plant, due to stresses during the transport and storage process.
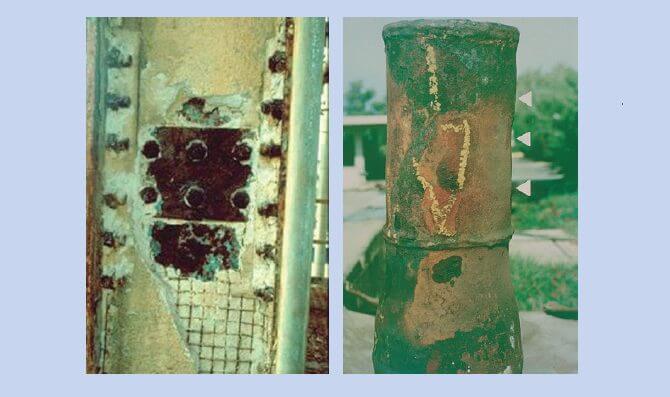
Left, corrosion under fire retardant coating; right,
corrosion in thermally insulated pipe.
Corrosion represents the common enemy, against which we must fight in order to achieve more efficient production processes, with greater profitability and an increasingly cleaner environment.
Conclution
The fight against corrosion must be based on a strategic plan organized by a multidisciplinary team with the aim of minimizing the damage caused by corrosion, implementing a system of protection, monitoring and information management, in order to avoid economic losses in the replacement of structures, pipes, equipment, and other costs, difficult to detect, associated with indirect losses due to product spills, risk of accidents in oil pipelines, and stoppages of industrial plants, etc. Generating great disasters to the productive sector, to humanity and environmental deterioration.