Liquid penetrant inspection is a type of non-destructive testing that is used to detect and identify discontinuities present on the surface of the materials examined, which may lead to future failures of the same. This technique, based on the phenomenon of capillarity, allows to quickly and reliably reveal: cracks, folds, defects, on any component (ferrous and non-ferrous) regardless of the geometry and material of the piece. Generally it can be used for the inspection of ferrous materials when magnetic particle inspection is difficult to apply, in some cases it can be used on non-metallic materials.
The applications of this technique are wide, and range from the inspection of critical parts such as: components in the Oil & Gas industry, aeronautics, etc. Metallic materials, glazed ceramics, plastics, porcelain, electrochemical coatings, among others, can be inspected.
The procedure consists of applying a colored or fluorescent liquid to the surface under study, which penetrates any discontinuity that may exist. After a certain time, the excess liquid is removed and a developer is applied, which absorbs the liquid that has penetrated the discontinuities and outlines their outline on the developer layer. Figure 1 shows the steps to follow in this procedure.
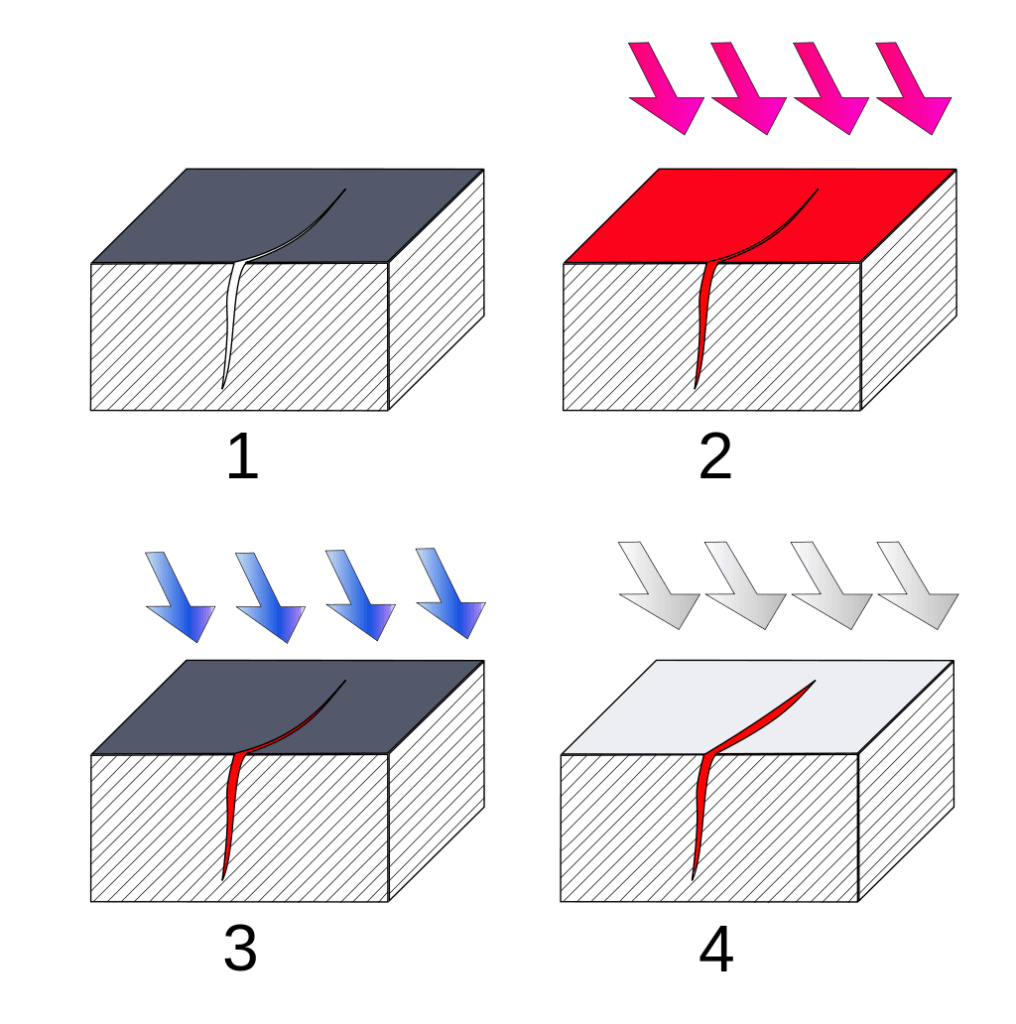
Figure 1: 1. Cutting of a material with a crack; 2. The surface of the material is covered with penetrant; 3. Excess penetrant is removed; 4. Developer application to make the defect visible.
The dye penetrant inspection technique requires consistency and precision in the application process and reliable products so that the inspector, engineer, or technician can have the confidence to detect all defects and flaws. The more repeatable the inspection, the higher the level of confidence an inspector gains.
The Testek Group provides NDT professionals, engineers and technical inspectors with a variety of consumable chemical products: WhaleSpray Crack 1, Crack 2 and Crack 3, developed and tested to maximize test reliability, covering each and every of the needs of dye penetrant inspection professionals.
WhaleSpray Penetrating Dyes: Crack 1, Crack 2 and Crack 3.
WhaleSpray covers each and every one of the needs of professionals in the area of inspection of industrial assets, offering a series of chemical products for this sector. One of the WhaleSpray product families is the formulation and production of a variety of penetrating dyes in Spray form: Crack 1, Crack 2 and Crack 3 (figure 2); which consists of a range of products that allow inspections, tests and evaluations to be carried out on various materials or components to detect imperfections and discontinuities without damaging or destroying them, thus achieving a lengthening of the useful life of structures and equipment.
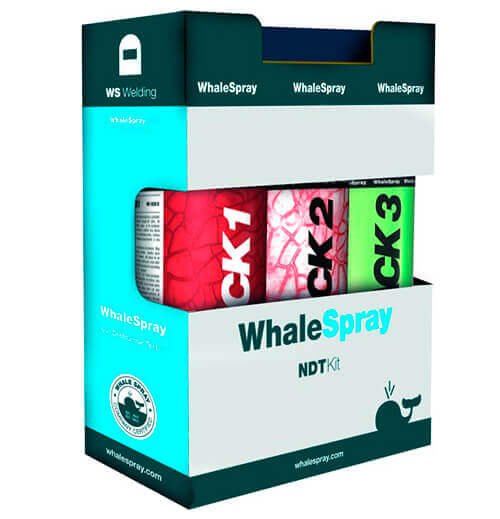
Characteristics and advantages of penetrating dyes: Crack 1, Crack 2 and Crack 3
CRACK 1 Red Penetrating (figure 3)
Intense red color penetrant in aerosol format; which, together with Crack 2 and Crack 3, allows to locate discontinuities, pores, fissures and imperfections in the treated surfaces. Its main characteristics are easy removal with both water and solvents, its high effectiveness and sensitivity even with natural light, high penetration and capillarity, it complies with the specifications of ASTM E 165 and has a sensitivity level ISO 3452 Level 2.
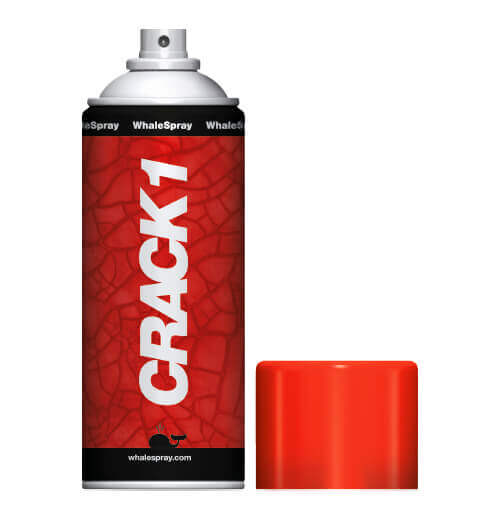
Advantages and features:
- Removable with water and solvents.
- It works with natural light.
- Excellent penetration characteristics.
- High capillary action optimized.
- Very good wetting on surfaces.
- Cleans up quickly saving time and water.
- Very low liquid consumption thanks to its low viscosity.
- Meets ASME section V specifications regarding content of sulfides, chlorinated and halogenated solvents.
- Sensitivity level ISO 3452 Level 2.
CRACK 2 White Developer (figure 4)
White color developer in aerosol format, used to create a contrast that allows detecting discontinuities, pores, fissures and imperfections on surfaces treated with Crack 1 and Crack 3. Its main characteristics are easy removal with water or solvents, its high effectiveness and sensitivity even in natural light, a high capacity to reveal defects, complying with specifications. of AMTE V and excellent and homogeneous spraying.
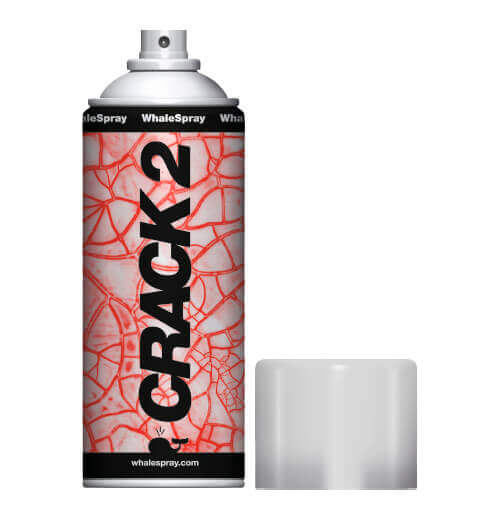
Advantages and features:
- Removable with water and solvents.
- It works with natural light.
- Excellent defect revealing characteristics.
- Ultra fast drying time.
- Very good spray on surfaces.
- Cleans up quickly saving time and water.
- Meets ASME section V specifications regarding content of sulfides, chlorinated and halogenated solvents.
CRACK 3 Cleaner (figure 5).
Cleaner in aerosol format, exclusively formulated to obtain optimal results in cleaning the entire NDT process, in conjunction with Crack 1 and Crack 2, allowing the operator both to prepare the piece to be treated, eliminating contaminants and debris, and for subsequent cleaning. after trial.

Advantages and features:
- Highly effective removal of contaminants, penetrants and developers.
- Unique in the market pressurized with CO 2 , giving a 98% active product.
- Ultra fast drying time.
- Very good spray on surfaces.
- Manufactured with a 360º valve for application in any position.
- Meets ASME section V specifications regarding content of sulfides, chlorinated and halogenated solvents.
Technical application procedure.
1 Thorough cleaning of the surface with Crack 3.
In order to eliminate all types of impurity or contamination, prior to the test, an exhaustive cleaning of the surface to be treated must be carried out with Crack 3 Cleaner.
2 Drying after cleaning
Once the cleaning has been carried out and in order not to create a conflict between products, the cleaner should be allowed to evaporate before carrying out the next step.
3 Crack 1 red penetrant application.
When the piece is dry and at a temperature between 4 ºC and 52 ºC, apply Crack Red Penetrant 1, covering the desired surface to be treated.
4 Allow Crack 1 to penetrate cracks and imperfections.
From WS we recommend letting Crack 1 act for 10-20 minutes, before starting the next step to obtain optimal results.
5 Remove excess Red Crack 1 penetrant.
To do this, soak an absorbent cloth with Crack 3, or failing that, water and proceed to rub the surface until most of the Crack 1 is removed.
Consider that an excess of solvent can completely remove the Red Penetrant.
6 Crack 2 white developer application.
Once the excess of Crack 1 has been removed, apply a film of White Crack 2 Developer to the entire surface where the test is being carried out. As it evaporates quickly, it is not necessary to force dry it.
7 Expect Crack 2 to reveal all the cracks and imperfections.
Depending on the degree of sensitivity that you want to obtain, development times can range from 10 minutes to 4 hours, despite the fact that the defects begin to be seen directly when Crack 2 is applied.
8 Allow Crack 1 to penetrate cracks and imperfections.
In those cases where residual penetrant or developer could interfere with subsequent processes or service requirements, it is recommended to perform a thorough cleaning with Crack 3 cleaner, or alternatively with water.
Below is a video courtesy of Grupo Testek, with the steps to follow for the application of this product.
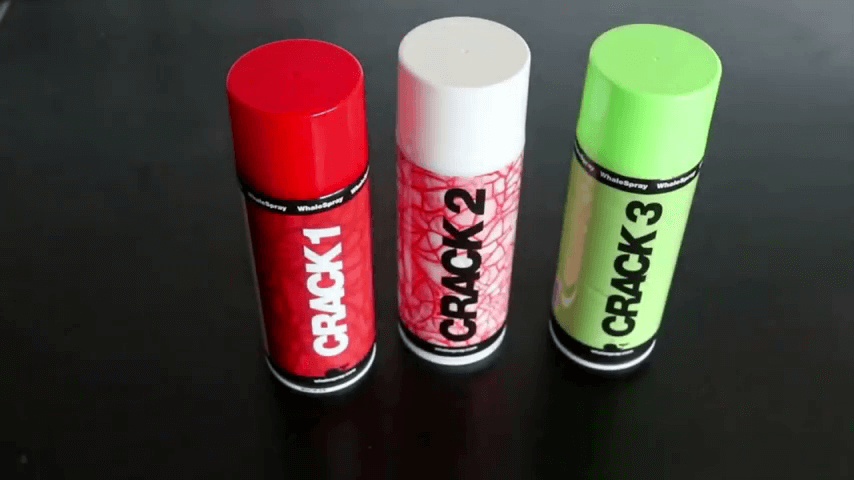
WhaleSpray Dyes Product Results
In figure 6, you can see 3 samples of welded metal parts; which were treated with penetrating dyes (M1: WhaleSpray Brand), (M2: Brand 2) and (M3: Brand 3).
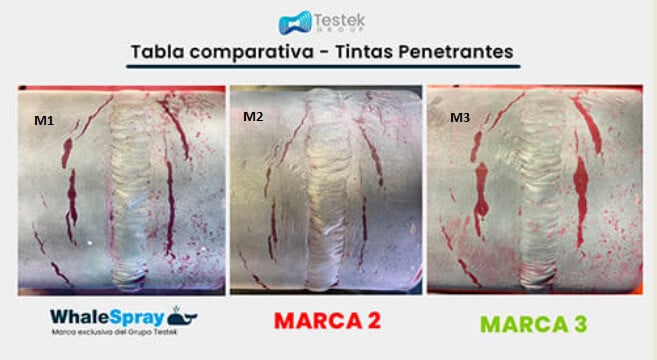
In the image it can be seen that the piece M1 treated with WhaleSpray dye, shows better definition of discontinuities, defects and anomalies detected on the surface; as well as, a greater sensitivity and better contrast between the surface and the indication of the discontinuities with respect to the M2 and M3 marks. You can see how the Whalespray penetrating inks expose the cracks with a more intense red color. Mark two, unlike mark three and Whale spray, does not show cracks or smaller ones in detail. Mark 3 expands your ink more, but can be counterproductive as the ink should ideally show the crack without much color expansion.
The results obtained with Crack1, Crack2 and Crack3 from WhaleSpary, indicate that with this range of products reliable, fast and profitable tests and evaluations can be obtained on various materials or components to detect imperfections and discontinuities without damaging or destroying them; helping to extend the useful life of assets. The detection of these problems is important because more accurate, faster and reliable inspections can be carried out.
Finally, it is important to note that WhaleSpary penetrating dye products comply with the following certifications: ASME SEC V, ASTM: E-165, E-1220, E-1414, among others.
Conclution
The extensive use of the dye penetrant technique in different metallic and non-metallic materials must be reliable in terms of sensitivity. This reliability lies not only in the correct execution of the technique but also in the use of good quality products that comply with standards and codes. With WhaleSpray’s range of Crack 1, Crack 2 and Crack 3 dye penetrants, reliable test results are achieved, covering each and every need of inspection professionals. Avoiding future failures that can cause problems whose solution would become more complex, or irreversible damage to industrial assets.
Bibliographic references
https://www.testekndt.net/producto/penetrantes-rojo-crack-1-ws-1820-s/