Technological development is essential to unlock the opportunities that hydrogen can offer to energy systems. Focusing on innovation from the outset would help develop technological solutions tailored to priorities and conditions, in line with global energy and climate goals. It is necessary to have international investments for the development and advances in research aimed at promoting new technologies applied in different sectors in the future, acquiring experience and knowledge in equipment design. For example, the potential targets in terms of electrolysis in the manufacture of electrolyzers.
National hydrogen consortia and associations can play an important role in identifying future common commercial opportunities in Hydrogen in accordance with Research and Development (R&D) priorities, in order to optimize investment and maximize transfer of knowledge. Early attention to skills development could help generate opportunities and prevent future human resource shortage problems as the industry develops. Capacity building across the hydrogen value chain, such as equipment manufacturing, hydrogen production, infrastructure deployment and end uses, would bring additional benefits beyond emission reductions, such as economic development, and opportunities for The investors.
This coordination is also essential to ensure effective communication and understanding of these emerging technologies among potential consumers, service and financing providers, and society at large, as well as to manage expectations around their use. of these new energies. In order to make its products with more sustainable materials, limit and eliminate the use of toxic chemicals, and reduce the impact of its industrial and manufacturing processes on the environment and global climate change. A new responsible industrial era has arrived, where manufacturing and production are more efficient, greener, more efficient, involve less waste, and with new customers focused on the environment in protecting the planet for future generations.
In this context, business sectors are currently joining different projects linked to the use of hydrogen in order to decarbonize their activities. One of the great advantages of hydrogen is zero carbon dioxide emissions; in fact, in the case of using hydrogen in a fuel cell, the only resulting emission will be water, while, in the case of using it in internal combustion engines, it will certainly still present small emissions of nitrogen oxides. However, hydrogen is not a free fuel that can be extracted directly from nature. On the contrary, hydrogen is an energy product, that is, its production is subject to a production process that requires a certain amount of energy. In this way, although the use of hydrogen does not give rise to greenhouse gas emissions, obtaining it may have associated emissions depending on the process followed, the primary energy sources used and the post-processing.
At this point it should be noted that hydrogen will be as clean and zero emissions as its production process, and this is very important. For example, it will be useless to replace all vehicles with internal combustion engines for their fuel cell equivalent if the hydrogen supplied to these vehicles has been obtained by a more polluting route than the use of diesel or gasoline itself. Depending on the primary source of energy used to produce hydrogen, as well as the production processes used, it is possible to classify the hydrogen obtained by assigning a color scale, in what has been called the colors of hydrogen. , although it is not completely standardized, it is very widespread.
Processes and new technologies for the production of Hydrogen
Processes from natural gas
The main source of obtaining hydrogen is natural gas, formed mainly by methane. The combination of three factors: large world reserves, its relative low cost and its chemical composition, makes natural gas currently the most interesting source of hydrogen for the world market.
The process of extracting hydrogen from natural gas is known as reforming. In this process, carbon oxides are produced as a by-product in gaseous form, which constitutes its main disadvantage, since around 11 tons of CO2 are generated for each ton of hydrogen. Alternatively, there is a technology under development, methane pyrolysis, which gives rise to solid coal as a by-product, and in which 3 tons of carbon per ton of hydrogen are produced as waste.
- Methane reforming processes
Reforming of natural gas is based on the decomposition of the methane molecule to give rise to hydrogen and carbon oxides (CO and CO2). For this process to take place, a combination of three conditions is required16: high temperature (700-1,100 °C), the presence of a catalyst (nickel-based), and the presence of an oxidizing agent (water and/or air).
There are three production methods depending on the oxidizing agent
– Water steam: reformed with steam.
– Oxygen or air: partial oxidation.
– A combination of both: autothermal reforming (ATR).
The steam methane reforming process is the most widespread process, giving rise to the formation of a synthesis gas, through the following reaction:
CH4(g)+H2O(g)⟶3H2(g)+CO(g)
This is a strongly endothermic reaction that requires high temperatures of up to 1000 °C. Prior to the reforming process, it is essential to eliminate the traces of sulfur compounds present in the gas to avoid poisoning the catalysts, continuing with an optional pre-reforming whose objective is to break longer chain hydrocarbons such as butane or propane from so that the richness of methane is increased and the process is more efficient.
Partial air oxidation is mainly used to produce syngas from solid material such as coal or biomass. Autothermal reforming (ATR) consists of units in which both oxidizing agents, air and water, are used together. The injection of a controlled air content reduces external fuel consumption in the reforming unit because part of the heat needed to break down the methane comes from oxidation with oxygen. It is mainly used for the reforming of hydrocarbons, but it is also made from natural gas 1.
Regardless of the oxidizing agent, the current global hydrogen production process is based on 4 stages in series (see figure 1): natural gas desulfurization, reforming, gas displacement and hydrogen purification. Of all of them, the central unit of the process is reforming, but before entering the reformer, the natural gas goes through a desulphurization process, in which more than 99% of the sulfur contained in conventional gas is eliminated. After the desulfurization stage, a clean gas is obtained below 0.1 ppm of H2S. This process consists of two units: the first converts all the sulfur into its reduced form through hydrogenation and a cobalt-molybdenum-based catalyst; the second removes sulfur with a zinc oxide catalyst. Deculturation is a key step in reducing catalyst “poisoning” in reforming.
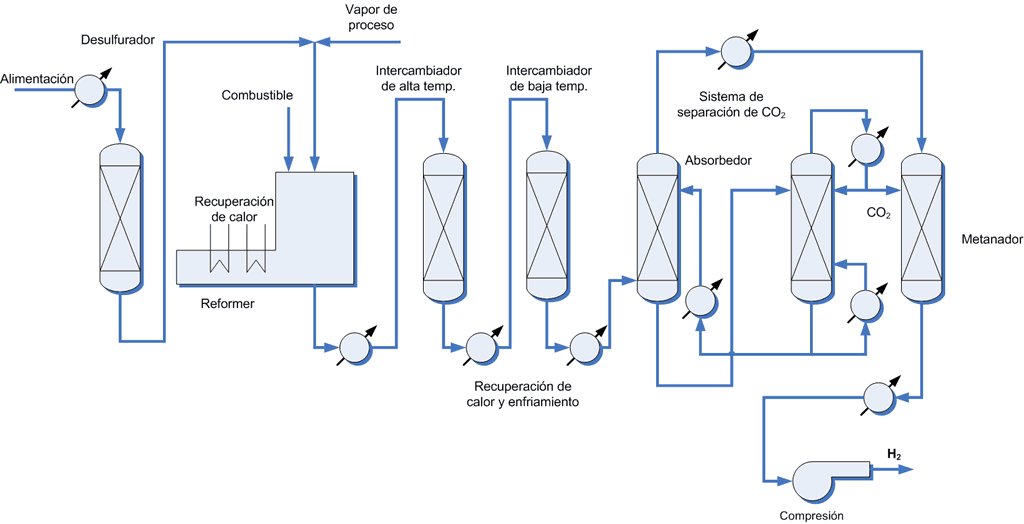
Once clean, the natural gas is mixed with water vapour, the temperature is increased to around 700-900 °C and it is introduced into a nickel-based catalytic bed. The high temperatures required in the reformer are achieved by burning an external fuel, be it part of the natural gas or another hydrocarbon. It should be noted that the modern facilities have made it possible to increase the energy efficiency of the reforming process by between 10-20%. Once the synthesis gas mixture (CO and H2) is obtained, it is passed to the displacement unit to convert carbon monoxide (CO) to carbon dioxide (CO2) and increase the final amount of hydrogen. The catalysts used in the displacement unit are based on iron, chromium and cobalt. This unit consists of two reactors in series: a first at high temperature and a second at a lower temperature.
Regardless of the oxidation process, the product obtained from reforming is a mixture of carbon dioxide (CO2) and hydrogen (H2), with traces of methane (CH4) and carbon monoxide (CO). To obtain a stream of pure hydrogen, a final purification stage must be carried out, that is, separation of the other compounds from the synthesis gas. This stage can consist of several units depending on the technology used with the aim of supplying high purity hydrogen at the end of the process.
- SMR Technology: Steam Methane Reforming (PSA) for Hydrogen Production
SMR is a cost effective and energy efficient method of hydrogen production. Thanks to in-house pressure swing adsorption (PSA) purification technology, high levels of purity can be achieved 1.
In the steam reforming process, a desulfurized hydrocarbon (natural gas, refinery gaseous effluent, liquefied petroleum gas or naphtha), raw material, is previously subjected to a thermal treatment and mixed with steam. Optionally, it can be pre-reformed before going over a catalyst in a dedicated steam reformer with top burners, to produce hydrogen, carbon monoxide (CO) and carbon dioxide (CO₂).
The CO, by vapor displacement, is converted to hydrogen and additional CO₂. The hydrogen is then separated using pressure swing adsorption.
-Pressure Swing Adsorption (PSA)
Pressure swing adsorption is a process in which individual gases are separated from a gas mixture. It is mainly used in chemical and petrochemical processes as well as in the steel industry, for example to recover hydrogen (H2) from coke or conversion gases, or to separate oxygen (O2) and nitrogen (N2) from air.
The adsorption process is based on the binding of gas molecules to an adsorbent material. The bed of adsorbent is specially selected as a function of the gas to be absorbed. Ideally, only the gas to be separated is adsorbed, while all others pass through the adsorption bed without being trapped. Adsorbents containing activated carbon or carbon molecular sieves and oxide adsorbents such as zeolite are often used. The purity of the adsorbed gas does not only depend on the adsorbent used, but also the temperature and pressure during the process are important.
The pressure swing adsorption process is divided into four stages (Figure 2), which occur in cycles:
Adsorption: Adsorption takes place at high pressure (up to 40 bar). The gas mixture passes through a bed of adsorbent. The adsorbent traps readily adsorbable gas molecules, while gas molecules that are not readily adsorbable or not adsorbable at all pass through the bed. The adsorbent traps readily adsorbable gas molecules, while gas molecules that are not readily adsorbable or not adsorbable at all pass through the bed.
Depressurization: Depressurization is the first step in the regeneration (desorption) of the adsorbent bed. As the pressure drops, the adsorbent bed gas molecules are released and the target gas is discharged from the adsorption tank.
Purge: The adsorbent bed is purged with the target gas to completely regenerate it.
Repressurization: It is done with the gas mixture or with the target gas until the conditions of the adsorption process are restored.
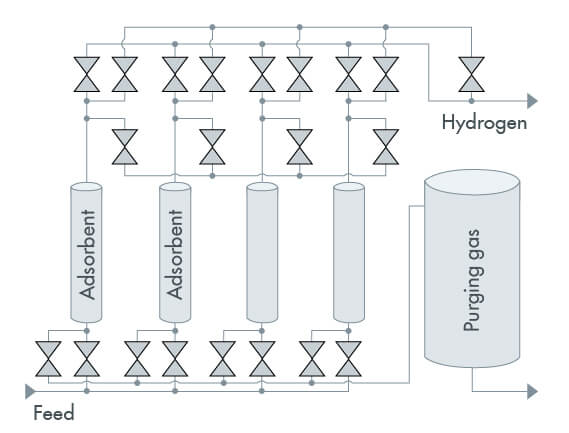
Pyrolysis process for hydrogen production
Pyrolysis of methane gas is an emerging technology that allows the decomposition of methane into hydrogen and carbon (see Figure 3). This process is also known as thermal cracking of methane or methane decomposition, and some authors call the hydrogen produced turquoise. In the gas pyrolysis process, it is produced in solid form by the following reaction:
CH4 (g) → 2H2 (g) + C (s)
Unlike reforming, this process does not require any oxidizing agent such as water or oxygen. In this way, no chemical compound is added that contains oxygen in its structure and that favors the production of carbon oxides (CO2 or CO). It is important to mention that this technology is still in the development phase.
- Microwave plasma assisted pyrolysis technology
Thermal cracking of methane can be done by applying energy from a microwave source. In this way, it has been possible to efficiently decompose a stream of CH4 into pure H2 and carbonaceous filaments, obviously in the absence of any carbon oxide (there is no oxygen in the reaction medium). It should be noted that the carbon residues, by-products of the reaction, provide added value to the H2 produced since they have excellent adsorption properties.
One way to carry out the decomposition of CH4 into its components (H2 and C) in a smoother way than the pyrolysis itself is by incorporating catalysts into the reactor (Figures 3). Catalysts lower the activation energy of the pyrolysis process and thus increase the rate of the hydrogen generation process. The most suitable catalysts to carry out this process are made up of nickel and iron particles, finely dispersed on inorganic supports of a mesoporous nature, for example. Al2O3 y SiO2. These types of systems produce H2, free of carbon oxides, and carbon filaments that end up deactivating the catalyst. The usual procedure for restoring the activity of the deactivated catalyst consists in gasifying the carbonaceous residue by treating it in air or in steam; Of these options, steam treatment is particularly attractive as the nickel remains in the metallic state and no further reduction treatment is required before reuse.
Production of Hydrogen by electrolysis of water.
Water electrolysis is a reliable technology, with many years of accumulated experience in the Industry, and with numerous suppliers of equipment and components (Figure 4). As a technology for obtaining hydrogen, it allows obtaining it of great purity. The cost is determined by the electricity used. And in any case, it is important to remember that the final cost of hydrogen in a given place will be conditioned by transportation and storage costs, as well as the benefits of intermediaries.
When the volume of hydrogen required in any application is moderate, hydrogen is obtained by electrolysis of water. The electrolytic reaction is carried out in an alkaline medium because the electrical conductivity increases in this medium. The hydrogen produced at the cathode must be purified as it contains oxygen impurities and a certain level of moisture. The hydrogen stream is dried with the aid of an adsorbent and oxygen impurities are removed with a DeOxo converter. In addition, oxygen is produced at the anode of the electrolyzer, the volume of which is half the volume of hydrogen, as corresponds to the composition of the water molecule. Most of the electrolyzers are of the tank type with the electrodes arranged in parallel. The heat released in the process is removed by recirculating water around the cells.
Hydrogen allows access to a wide group of primary precursors such as fossil fuels, nuclear energy and with increasing penetration of renewable energies (wind, solar, biomass). It is worth noting the fact that the hydrogen produced by electrolysis is of the order of 4.9-5.6 kWh for each m3 of hydrogen produced, which is at least two times more expensive than the hydrogen obtained by reforming natural gas.
Since conventional electrolyzers provide H2 at a high cost, other electrolytic processes have been developed.
One of them is vapor phase electrolysis. The reversible potential of the cell decreases with increasing temperature. Since the cost of electricity required in electrolysis to produce H2 from H2O is proportional to the electromotive force of the cell, the cost decreases with temperature. The cell is cooled because the process is endothermic and it is kept at a constant temperature by providing heat from the outside. This means that heat is electrochemically converted to H2 without going through a Carnot cycle. Thus, at 1,500 ºK the amount of thermal energy used in the thermo-electrochemical decomposition is 50% of the total. Under these conditions, the production cost is 50% lower than in the conventional process.
Another economic alternative for the production of H2 is provided by new types of electro-catalysts that are capable of reducing the overvoltage, which means a reduction in cost.
Equations:
In pure water, at the negatively charged cathode, a reduction reaction takes place, with electrons (e-) from the cathode giving up hydrogen cations to form hydrogen gas (the acid-equilibrated reaction medium). :
Reduction at the cathode: 2 H+(aq) + 2e- → H2 (g)
At the positively charged anode, an oxidation reaction occurs, generating oxygen gas and giving electrons to the anode to complete the circuit.
Oxidation at the anode: 2 H2O (l) → O2 (g) + 4 H+(aq) + 4e-
Reduction at the cathode: 2 H+(aq) + 2e- → H2 (g)
At the positively charged anode, an oxidation reaction occurs, generating oxygen gas and giving electrons to the anode to complete the circuit.
Oxidation at the anode: 2 H2O (l) → O2 (g) + 4 H+(aq) + 4e-
The same half reactions can also be balanced with the base listed below. Not all half reactions must be balanced with acid or base. Many do, such as oxidation or reduction of water that
appears here. To add half of the reactions these must be balanced with acid or base.
Cathode (reduction): 2 H2O (l) + 2e- → H2 (g) + 2 OH- (aq)
Anode (oxidation): 4 OH- (aq) → O2 (g) + 2 H2O (l) + 4 e-
Combining both reactions gives the same total decomposition of water into oxygen and hydrogen:
General reaction: 2 H2O (l) → 2 H2 (g) + O2 (g)
The number of hydrogen molecules produced in this way is twice the number of oxygen molecules. Assuming the same pressure and temperature for both gases, the hydrogen gas produced therefore has twice the volume of the oxygen gas produced. The number of electrons carried through water is twice the number of hydrogen molecules generated and four times the number of oxygen molecules generated.
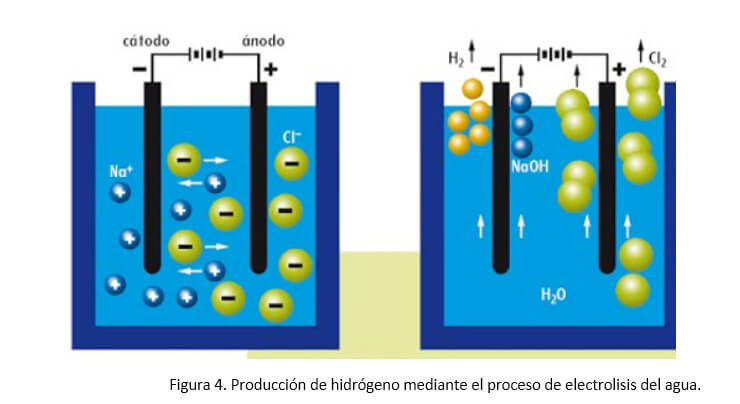