Industrial ultrasonic technology has come a long way from its early use in material analysis and thickness measurement. Over time, it has evolved continuously, enabling significant advancements in the inspection and evaluation of components across a wide range of industries, from manufacturing to medicine1.
Ultrasonic devices can detect objects, measure distances, perform deep cleaning, assist in industrial manufacturing, and enhance healthcare. Their applications continue to expand thanks to improvements in ultrasonic component manufacturing, offering less invasive and more cost-effective alternatives.
What is industrial ultrasound used for?
Ultrasonic testing is widely used in the industrial sector to:
- Detect cracks, porosity, and internal defects in metal, plastic, or ceramic parts without damaging them.
- Measure thickness and wear in pipes, vessels, equipment, and machinery.
- Perform condition monitoring to detect leaks, cavitation in pumps, lubrication failures, among others.
- Conduct quality control in welding processes and ultrasonic cleaning.
These applications are critical in industries such as energy, petrochemical, aerospace, automotive, and shipbuilding.
Historical evolution of industrial ultrasonic
From its origins as an experimental technique to its integration with artificial intelligence and robotics, industrial Ultrasonic has undergone continuous innovation in service of non-destructive testing (NDT).
The first steps
In 1880, brothers Pierre and Jacques Curie discovered piezoelectricity, the foundation of modern Ultrasonic2.
In 1912, following the Titanic disaster, Lewis Fry Richardson proposed using ultrasonic echoes to detect underwater objects—an idea that gained traction during World War I. In 1917, Paul Langévin and Constantin Chilowsky developed the first high-power piezoelectric ultrasonic generator. Starting in 1924, Dr. S. Y. Sokolov applied ultrasonic waves to material inspection. During World War II, both German and Soviet teams developed ultrasonic devices for military purposes. In 1948, the Krautkramer brothers refined the technology for industrial inspection.
Flaw detection equipment
During the 1940s, World War II spurred the development of non-destructive inspection technologies, including industrial ultrasound. Ultrasonic flaw detectors became an essential tool used to assess the integrity of structural components used in aircraft and military machinery. These devices were relatively rudimentary compared to today’s technologies, but they ushered in the era of ultrasonic inspection.
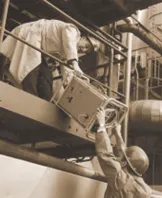
Technical advancements and new applications
During the 1950s and 1960s, ultrasonic transducers were significantly improved, increasing their resolution and sensitivity. The development of ceramic piezoelectric materials and advances in electronics allowed for more accurate measurements, better defect localization, and higher efficiency in NDT. These improvements enabled detection of smaller defects and assessment of thinner materials3.
Industrial applications
By the late 1960s, Ultrasonic was applied to welding evaluation in thermoplastic materials, enhancing manufacturing processes for electronic, medical, and packaging components. Ultrasonic testing became a standard technique for assessing welds, equipment, and critical structures in sectors like energy, aviation, petrochemicals, and marine construction.
Innovations in the 1980s and 1990s
During this period, ultrasonic inspection evolved with the introduction of more precise and automated technologies, including:
Phased Array Ultrasonic Testing (PAUT)
This method marked a major leap by using multiple transducers to electronically steer and focus ultrasonic beams, enhancing inspection of complex geometries.
Total Focusing Method (TFM)
Enabled high-resolution image reconstruction in targeted areas, improving defect detection and characterization.
Time of Flight Diffraction (TOFD)
Based on diffraction of ultrasonic waves at discontinuities, it uses two transducers placed on either side of the weld—one transmitting, one receiving. TOFD captures diffracted waves at the tips of defects, allowing precise calculation of their height and location, even for very small flaws.
Laser Ultrasonic (LU)
A cutting-edge approach in NDT, LU generates ultrasonic waves via laser pulses on the material surface, eliminating physical contact and couplants. Ideal for inspecting complex geometries or extreme environments, LU holds great potential for remote automation and aerospace or nuclear applications.
Automated inspection systems
Simultaneously, advances in automation enabled the development of robots for ultrasonic testing, capable of operating in complex environments, such as inside pipelines. These systems perform precise scans in variable geometries, generating real-time data, reducing risks for personnel and increasing the efficiency of predictive maintenance.
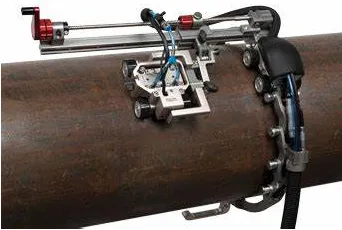
Advances in digital electronics
Digital advancements have revolutionized industrial Ultrasonic, enhancing signal acquisition, processing, and analysis. Control panels now feature intuitive interfaces and integration with data management platforms.
The Internet of Things (IoT) and Big Data have further driven this evolution. Modern systems offer secure cloud storage, real-time auto-backup, and wireless communication for instant reporting and advanced analysis.
IoT is redefining ultrasonic inspections by enabling continuous monitoring via embedded sensors, shifting from periodic assessments to condition-based diagnostics.
Finite Element simulation
Finite Element Modeling (FEM)4 has become a key tool in designing ultrasonic transducers and optimizing inspection techniques. Engineers can simulate ultrasonic wave propagation in materials and components, predicting their behavior in various scenarios. This capability has significantly enhanced the sensitivity and resolution of ultrasonic testing.
Technological innovations
- Digitalization and IoT integration: Modern systems incorporate digital acquisition, intuitive displays, and cloud storage, enabling remote monitoring and real-time reporting—key in predictive maintenance strategies.
- Artificial intelligence and machine learning: AI algorithms process ultrasonic data to optimize interpretation and reduce false positives. They also assist in planning automated inspections using CAD models and identifying subtle defects through optimized beamforming.
- Advances in transducers:
- CMUTs (MEMS-based transducers): Smaller, cost-effective, with high signal-to-noise ratio—ideal for automotive and electronics
- GaN transducers: Broaden bandwidth: suitable for turbine and high-temperature component inspection.
- Dual-element probes: Combine pulse-echo and pitch-catch modes, improving inspection of composite materials.
- Enhanced PAUT and TFM:
- PAUT remains standard for weld and complex geometry inspection.
- TFM now supports multi-width, multi-mode imaging (longitudinal, shear, surface), increasing sensitivity to surface and deep cracks.
- Robotics and 5G: Autonomous PAUT-equipped robots with 5G connectivity inspect tanks, pipelines, and ship hulls—aligned with Industry 4.0 and the NDE 4.0 concept, integrating sensors, networks, and advanced data analytics.
- Simulation and Big Data: Finite Element Simulation continues to refine transducer design and TFM strategies. Meanwhile, massive data collection enhances algorithms and enables failure prediction before issues arise.
The future of industrial ultrasonic
Artificial intelligence and machine learning
These technologies enable:
- AI algorithms to detect subtle flaws and reduce false positives.
- Adaptive beamforming and CAD integration to optimize inspection planning.
- Autonomous robotic systems combining vision and Ultrasonic to detect leaks and arcs in industrial pipelines with nearly 99% accuracy.
Real-time and portable ultrasonic
Advances in hardware and software have enabled the development of real-time ultrasound systems and handheld devices, giving inspectors the ability to perform ultrasonic testing in the field more efficiently. Portable systems are particularly useful in predictive maintenance applications, where fast and accurate on-site inspections can be performed.
Connectivity and communication
Fast, secure sharing of ultrasonic data is now possible thanks to advanced communication tech. Test results can be uploaded to the cloud for expert review, securely stored, and accessed for future reference—streamlining decision-making and real-time collaboration.
Connected devices and IoT
Cloud-integrated systems using IoT enable real-time analysis, backups, and operational condition assessment. Predictive maintenance strategies now reduce downtime and operating costs by up to 30%.
Advanced transducers
- CMUTs (MEMS): Compact with superior signal-to-noise ratio—ideal for handheld devices.
- GaN transducers: Offer wider frequency ranges for high-temperature components.
- Dual-element probes: Enhance layered composite material inspection.
Next generation Phased Array and TFM
- PAUT enables electronically controlled illumination and improved accuracy in welds and complex structures.
- TFM moves towards multidirectional imaging combining longitudinal, shear and surface modes.
Robotics and 5G
- Ultrasound-equipped mobile robots enable inspection of pipelines, tanks and ship hulls.
- 5G connectivity facilitates instant data transmission to the cloud, empowering NDE 4.0 strategies.
Challenges and risks
- High costs of advanced equipment like PAUT and inspection robots.
- Need for highly trained personnel to operate systems and interpret complex data.
- Ensuring data quality: precise sensors, ongoing calibration, and algorithm validation.
- Cybersecurity for cloud-connected and industrial networked devices.
Conclusions
Industrial Ultrasonic has evolved from a basic flaw detection method into a critical tool in non-destructive testing and industrial manufacturing. Advances in transducers, electronics, simulation, and scanning have significantly improved its precision and efficiency.
Today, with AI integration, portability, and IoT connectivity, ultrasonic technology supports automation, optimizes predictive maintenance, and enables real-time remote inspections. Its adaptability to complex environments and contribution to operational integrity firmly establish it as a vital technology across multiple industrial sectors.
References
- Krzysztof J. Opieliński; “Special Issue on Ultrasound Technology in Industry and Medicine”; Applied. Sciences; 2023 , 13 (3), 1455. https://www.mdpi.com/2076-3417/13/3/1455
- https://www.nde-ed.org/NDETechniques/Ultrasonics/Introduction/history.xhtml
- https://es.wikipedia.org/wiki/Ultrasonido
- https://iopscience.iop.org/article/10.1088/1757-899X/657/1/012011