Table of Contents
- Understanding emission sources from storage tanks
- What are safety and emission control systems in storage tanks?
- Safety devices for low-pressure storage tanks
- Systems for emission control in low-pressure storage tanks
- Standards to be considered in the reduction of storage tank emissions
- Safety measures
- Conclusions
- References
In refineries and oil terminals, gases from processed or stored products pose a hazard due to their explosive or lethal potential. It is essential to comply with environmental and safety regulations to effectively control these emissions. By design, tanks are equipped with venting systems, which allow the controlled release of vapors and maintain internal pressure close to atmospheric, thereby avoiding risks associated with storage tank emissions.
During storage in tank farms, the greatest problem of pollutant emissions to the atmosphere is encountered. Changes in temperature and pressure cause expansion and compression within the equipment, resulting in the emission of contaminant gas, which affects air quality and poses a health risk.
This article examines the main sources of storage tanks emission, safety devices, commonly used emission control systems, and key regulations to ensure safety and environmental protection in the hydrocarbon storage industry.
Understanding emission sources from storage tanks
Storage tanks, operating at atmospheric or low pressure, typically store volatile liquid products. These tanks are a significant source of various types of emissions, including methane, volatile organic compounds (VOCs), flash emissions, operational and breathing emissions.
One of the primary sources of emissions in these tanks is the evaporation of stored products, which is influenced by factors such as volatility, temperature, and to a lesser extent, internal pressure; there are also breathing emissions, which occur when the internal pressure of the tank varies with changes in ambient temperature, causing expansion and contraction of the air chamber inside the tank, facilitating the release of vapors. The loading and unloading process generates operational emissions due to the displacement of vapors in the tank’s void space.
Leaks from joints, valves, and connections, and failures in the seals of floating roof tanks contribute to emissions. Incidents such as significant leaks or catastrophic events also release large quantities of emissions. On the other hand, emissions caused by malfunctioning ventilation systems increase the risk between internal pressure and the gaseous composition of the tank. Similarly, cleaning and inerting the equipment generate emissions.
What are safety and emission control systems in storage tanks?
These are devices designed to manage and minimize the release of harmful gases and vapors in hydrocarbon or other product storage facilities. Given the high hazard nature of the storage industry, these systems are critical to ensure safe and environmentally responsible operations.
Effective emissions management in low-pressure storage tanks involves the use of specialized devices to regulate venting, preventing the emission of contaminant vapors that increase the risk of fire and cause economic losses due to product shrinkage. These systems function to regulate internal pressure and maintain the quality of the stored product, as well as reduce environmental pollution from hazardous compounds.
Hydrocarbon emissions from storage tanks are polluting sources of greenhouse gases; therefore, emission control in tanks includes automatic leak detection and vapor recovery systems that process VOCs before being released into the environment. These measures prevent atmospheric pollution and accidents and are necessary to maintain the operational integrity of storage facilities.
Safety devices for low-pressure storage tanks
These devices vary in function and design, depending on the specific needs of the facility and the stored product, and are intended to limit emissions into the atmosphere. Among the main safety devices are:
- Vent valves: These allow for the controlled release of vapors and gases into the atmosphere to maintain internal pressure within safe limits, preventing tank collapse due to vacuum or rupture due to excessive pressure. Various types of valves include pressure and vacuum, diaphragm, and ball valves.
- Flame arrestors: Installed on vent lines, these prevent an external flame from entering the tank, protecting against explosions in the presence of flammable gases.
- Emergency relief valve: Automatically activated to release excess pressure if other control systems fail, they provide safety against excessive pressurization.
- Level indicator: These devices monitor and control the liquid level inside the tank and prevent overfilling or excessive emptying, both scenarios that could lead to hazardous situations.
- Automatic leak detection: Designed to detect the presence of vapors or liquids outside the tanks and alert personnecl to take corrective and preventative measures.
- Secondary Containment barriers: Surrounding structures around the tank to contain the spread of spills or leaks, protecting the soil and groundwater from contamination.
Each of these devices is used for incident prevention and to ensure that low-pressure storage tanks continue to operate within established parameters.
The following video illustrates various types of safety devices and systems for storage tanks such as flame arrestors, pressure relief valves, and manometer gates, among others. Video provided by Storagetech.

Safety devices for storage tanks.
Systems for emission control in low-pressure storage tanks
Emission control systems or equipment are integral to safety measures, as they control, capture, or process Volatile Organic Compounds (VOCs) before they are released into the environment. This minimizes environmental impact, reduces the risk of flammability, and stored product loss, thus contributing to energy efficiency. Among the main ones mentioned below are the following:
- Vapor Recovery Unit (VRU): Captures vapors emitted by the volatile liquids stored, condensing or compressing them for treatment and reuse. Common VRUs are classified into two types, compressor and ejector. Their implementation depends on the volume of emissions and the type of vapor to be recovered.
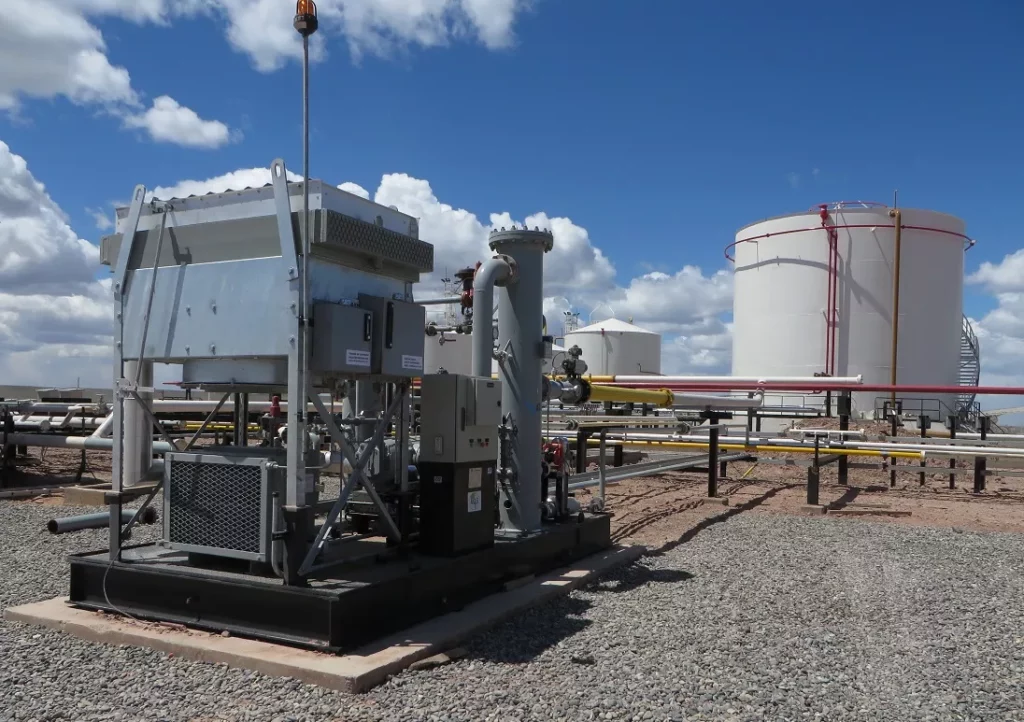
- Floating roof tanks: These tanks are designed with a floating roof that rises or falls with the liquid level, minimizing the space above the liquid surface and, therefore, limiting VOC emissions. This type of roof includes sealing systems, consisting of a primary and a secondary seal around the edge of the floating roof, which prevents vapors from escaping, improving emission management in tanks.
- Inert gas systems: Also known as blanketing, it is a system that involves replacing the air in the tank with an inert gas such as nitrogen, to maintain a protective layer of gas over the stored liquid, preventing oxygen ingress and reducing VOC emissions. This technique is particularly useful for tanks storing flammable liquids that operate at low pressure.
The following video shows how nitrogen blanketing works, a process used in various industries, especially in the storage or transport of liquids. It involves introducing a controlled flow of nitrogen gas into a storage container to displace or reduce the presence of oxygen. Video provided by Petrolsult.
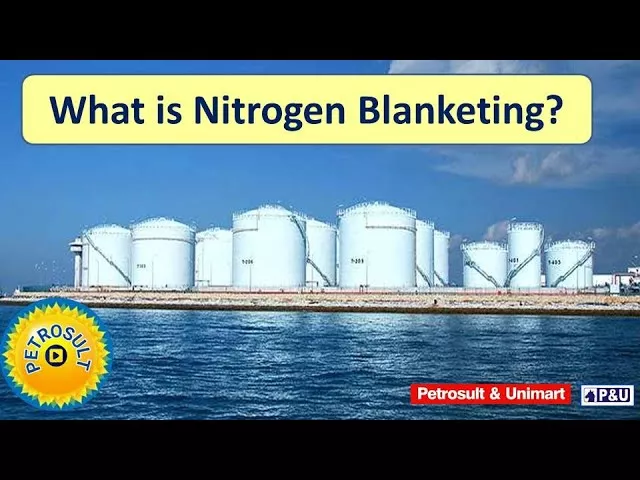
Inert gas system or nitrogen blanketing process in storage tanks.
- Activated carbon filters: These materials adsorb and retain VOCs and other contaminants present in the vapors emitted, thereby reducing pollutants. This process is based on the physical or chemical attraction between the activated carbon and the vapor contaminants. Typically, they are used in combination with other emission control equipment.
- Incineration systems: Destroy vapors and gases through controlled combustion. The main types are direct thermal incinerators, catalytic, and heat recovery incinerators.
- Continuous emission monitoring: The integration of digital tools into safety and emission control systems enables the detection and quantification of emissions in real time, alerting personnel in case of exceeding established limits, and allowing for operational adjustments.
The selection of an emission control system for storage tanks depends on the properties of the stored product, the size of the tank, applicable environmental regulations, and investment and operational costs.
Standards to be considered in the reduction of storage tank emissions
Emission reduction in storage tanks is part of environmental management in the hydrocarbon industry. Regulations include guidelines on tank design, emission control systems, and safe operations, issued by entities such as the American Petroleum Institute (API) and the Environmental Protection Agency (EPA). Below are the main ones:
- API 650, Welded Steel Tanks for Oil Storage: This is the primary standard for the design and construction of storage tanks at atmospheric or slightly above atmospheric internal pressures.
- API 2000, Venting Atmospheric and Low-Pressure Storage Tanks: Provides guidelines on venting systems that include vapor recovery aspects to maintain appropriate pressure inside the tank and prevent uncontrolled emissions.
- ISO 28300, Venting of Atmospheric and Low-Pressure Storage Tanks: Covers requirements similar to API 2000 and is oriented towards proper tank venting to avoid issues of over-vacuum and pressure.
- API Standard 276, Recommendations for Installation, Operation, and Maintenance of Vapor Recovery Systems: Provides detailed information on the design, installation, operation, and maintenance of VRS for storage tanks.
- ASTM D323, Standard Test Method for Vapor Pressure of Petroleum Products at 100°F: Provides a procedure for measuring the vapor pressure of petroleum products at a specific temperature, which is an important property for the safe handling, storage, and transport of these materials.
- ASTM D4738, Standard Test Method for Determining the Efficiency of Vapor Recovery Systems: This standard test method is used to evaluate the efficiency of VRS in capturing VOC emissions from storage tanks.
- NFPA 30, Flammable and Combustible Liquids: Includes requirements for vapor recovery systems in storage facilities for flammable and combustible liquids.
- EPA, HAP Emissions Control Standard for Crude Oil Storage Tanks: Sets requirements for controlling HAP emissions from crude oil storage tanks with a capacity of more than 10,000 gallons. Requires the implementation of controls such as floating roofs, vapor recovery systems, or vapor combustion systems.
- New Source Performance Standards (NSPS) – Subpart Kb: Regulates emissions from petroleum and derivative storage tanks.
Safety measures
Companies must be committed to legality, the environment, and enforcing sustainable industrial development. It is important to implement effective technological solutions tailored to each need, for effective emissions management in storage tank parks or terminals.
Strategies for controlling emissions in low-pressure storage tanks require compliance with safety protocols and features to protect personnel and organizational assets. Adequate ventilation, leak detection, an emergency response plan, and a fire prevention plan are essential to prevent incidents during processes.
Conclusions
As environmental standards solidify and awareness of sustainability increases, the world seeks unique and viable ways to control and reduce emissions, which is why effective control of storage tank emissions should not be underestimated. By adopting advanced technologies and flexible management strategies, facilities significantly reduce their environmental footprint while ensuring compliance with safety and environmental regulations.
Emission management systems in tanks, which include vapor recovery units, inert gas systems, and emission monitoring technologies, allow for the safe and efficient handling of harmful vapors that contribute to atmospheric pollution. In a regulated environment like storage tank parks, aware of the environmental impact they cause, effective emission control is a priority in all involved operations.
References
- https://tecamgroup.com/es/sectores/tank-storage/
- https://info.zeeco.com/hubfs/Zeeco-En_June_2020/pdf/article-Tank-Storage-Jul-Aug-2015.pdf?hsLang=en
- https://www.zeeco.com/products/vapor-recovery-units#:~:text=A%20vapor%20recovery%20unit%20(VRU,and%20during%20the%20loading%20process