Hydrogen has excellent properties as an energy vector and is widely anticipated as the fuel of the future. One of the key challenges in moving towards an economy based on this resource is finding effective solutions for the transport and storage of hydrogen , due to corrosion, specifically due to the diffusion of this compound in its atomic form towards the internal surface of the steel. .
One of the key challenges in moving towards a hydrogen-based economy is finding effective solutions for hydrogen transportation and storage, as corrosion is a significant concern in this process.
This article provides an updated assessment of the progress made in creating materials resistant to corrosion caused by hydrogen diffusion, especially during the transport and storage of this gas.
The transport and storage of this chemical element plays a fundamental role in the development and viability of the hydrogen-based economy. The logistics related to this element entails the creation of a transportation infrastructure that is both safe and affordable, which involves the installation of gas pipeline networks, gas pipelines and means of transportation that allow its distribution in a liquid state, which in turn , guarantee its availability and accessibility.
The problem for the transportation and storage of hydrogen
In a world where energy is one of the critical problems, hydrogen emerges as a solution. However, the use of this resource as a vehicle for energy poses particular challenges, and one of the most notable is its negative impact on metals, known as “fragilization by this phenomenon” (FPH)1.
This deterioration of mechanical properties, which triggers the appearance of cracks, represents a significant threat to the transport and conservation of this substance and, therefore, to its use under optimal safety conditions.
Another problem that can arise is hydrogen-induced cracking (HIC), Hydrogen Induced Cracking (HIC)2, see Figure 1, resulting from the combined action of a tensile stress and hydrogen in the metal. This element, produced on the surface of the metal by a chemical reduction reaction, diffuses into the metal and causes cracking in the medium.
Alloys that exhibit high strength, such as those with a tensile strength equal to or greater than 1,034 MPa (150,000 psi), are more susceptible to this type of fracture compared to lower strength alloys.
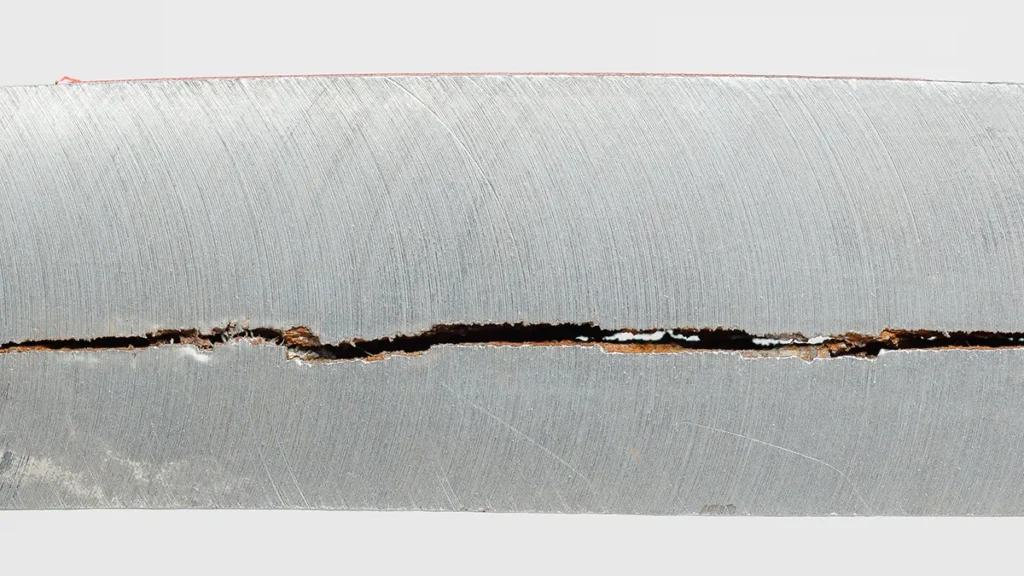
When atomic hydrogen comes into contact with steel, it is absorbed by the crystalline structure and diffuses through inclusions in the steel, and there reacts to form gaseous H 2 molecules. This process generates an increase in pressure within the steel due to the molecular hydrogen generated; and as a result, small cracks form inside; which can go unnoticed, causing internal damage to the material.
These tiny cracks have an elongated morphology that tends to be oriented in the rolling direction of the steel3 (figure 2). As new cracks are generated and existing cracks continue to grow, these cracks may eventually become interconnected. This process of crack formation and expansion progressively damages the steel, causing the material to fracture even under loads that are below its original design capacity.
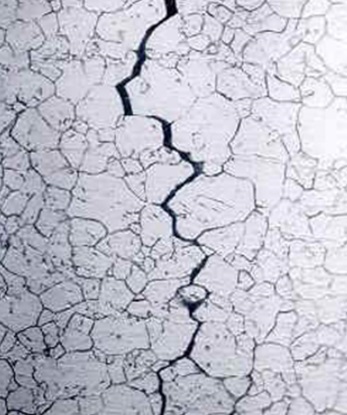
The impact of hydrogen on steel is an internal phenomenon that, over time, can compromise the structural integrity of the material. Resulting in internal damage that weakens the resistance of the steel and can put the safety of structures and components built with this material at risk.
In this context, Storage tanks and transportation pipes must be specially prepared to resist high pressures, tensions and efforts, coupled with the permeability of this compound that affects the mechanical properties of the steel. And they represent a serious problem for use as an energy vector.
The solution
When the transport and storage of hydrogen is considered as an energy potential, the fracturing of the metal by the aforementioned corrosion process becomes a problem. The storage tanks, pipes and valves used in these applications are frequently made of steel. Because this substance is a promising option in the search for cleaner and more sustainable energy sources, it is necessary to address this embrittlement problem effectively.
Below are some new technological innovations in development for the control of corrosion by diffusion of atomic hydrogen in the metal.
Composite materials and carbon steel alloys
In this context, currently, materials manufactured from carbon fiber composite materials and steels, both carbon and stainless, are mainly used to transport hydrogen, depending on the specific conditions of this gas, such as its temperature, pressure, humidity and impurities.
It is widely known that certain types of steel, when in contact with this compound, can suffer hydrogen embrittlement, which causes a loss of its mechanical properties, causing material failure due to cracks. To mitigate this problem, various strategies are currently applied, which mainly include oversizing of components and the application of surface coatings to delay the absorption of H2 in the steel.
Therefore, in the design of H2-related infrastructure, it is important to take into account the composition of stainless steel. Increasing the proportion of chromium and nickel in the alloy can be effective in preventing hydrogen-induced embrittlement, which in turn improves ductility and corrosion resistance.
The American Society for Testing and Materials (ASTM) regulations establish a minimum requirement of 10% nickel in the composition of 316 stainless steel, although to meet the specific demands of hydrogen, it is considered more appropriate the use of higher quality 316 stainless steel, with a minimum content of 12% nickel. In this sense, Swagelok stainless steel products meet this specification by guaranteeing a minimum 12% nickel content.
Hybrid metal structures
This is the H2MAT4 project directed by the Mondragon Unibertsitatea University, which aims to develop the materials of the future intended for the transport of hydrogen. The research consists of searching for solutions in the field of protective materials against corrosion used in the transport and storage of this compound as a source of energy.
The main focus of the project is on the synthesis, production and evaluation of multilayer structures as an alternative solution for H2 embrittlement, loss of ductility and acceleration, fatigue in ducts, in order to replace the stainless steel currently used in hydrogen transportation applications.
Hybrid metallic structures are components that combine different types of materials and alloys, taking advantage of the advantages of each one to meet specific requirements for resistance, durability and weight. They are made up of multiple layers of metallic materials, composites or coatings, designed in such a way that Each layer plays a specific role in corrosion protection, mechanical resistance and hydrogen permeability.
For example, they could include highly corrosion-resistant outer layers, middle layers that provide structural stiffness and reinforcement, and inner layers that prevent hydrogen penetration and minimize embrittlement. The combination of these layers allows the creation of structures that overcome the limitations of conventional materials and guarantee optimal performance.
Nanocomposites to protect pipelines when transporting H2
The development of these chemical compounds called nanocomposites5 emerges as a resource that can be applied to the interior walls of pipes to make them safe for the transport and storage of hydrogen.
The surface treatment process acts as a passivating barrier on the interior walls of the pipes. This barrier acts as a protective shield that prevents H2 molecules from penetrating the pipe material, controlling the diffusion of hydrogen (H) atoms towards the internal surface of the metal, preventing “hydrogen embrittlement”. Which is one of the main problems that affect the integrity of the pipes. The application of nanocomposites eliminates this risk and guarantees the durability and safety of the infrastructure
The advanced nanocomposite eliminates the costs associated with the fabrication and installation of new hydrogen-specific pipelines by allowing the use of existing pipeline networks.
It can be applied in situ to existing pipelines, unlocking the ability of millions of miles of infrastructure to transport safely. The application of these compounds eliminates the massive costs of new H2 infrastructure, connecting the world to this clean gas through lines already in use.
Finally, as this element chemical is consolidated as a key energy source in the transition towards a more sustainable future, it is important to consider the development of corrosion-resistant materials as a fundamental pillar in the search for safe and efficient solutions for the transport and storage of hydrogen.
Advances in materials science open a promising path, in the optimization of alloys, the application of innovative coatings and the exploration of nanocomposites represent technological solutions that overcome the challenges inherent to hydrogen embrittlement and corrosion. Ultimately, this progress not only ensures the safety and reliability of hydrogen infrastructure, but also contributes to the advancement of the energy transition that is transforming the world.
Conclusions
Transporting hydrogen as an energy source presents a unique set of challenges, related to corrosion issues, specifically hydrogen embrittlement; Therefore, the compression and management of this type of structural damage is essential to ensure the durability and reliability of steel applications in the field of this gas as an energy source.
As we move towards a more sustainable future, solving these issues is important to ensure the safety and efficiency of these technologies in the future. The combination of suitable materials and effective mitigation strategies is essential to overcome these obstacles and realize its full potential as a clean and renewable energy source.
References
- “Hydrogen fragility.” Metallurgy for engineers. 18-12-2020.
- BORN; Basic Corrosion Course, “Forms of Corrosion: Recognition, Mechanisms and Control”. NACE International; 01/15/04, Page 5:45.
- Herbert H. Uhlig, R. Winston Revie; “Corrosion and corrosion control” Fourth edition.
- H2MAT Project; “The materials of the future for hydrogen transportation”; MONDRAGON UNIBERTSITATEA University” https://www.mondragon.edu/es/-/proyecto-h2mat-desarrollara-materiales-futuro-transportaran-hidrogeno . Consulted on October 20, 2023.
- Taha-Tijerina, Jaim; “Synergistic effect of nanocoatings for protection against corrosion and wear of steel surfaces.” Research Engineer and tech. [online]. 2019, vol.20, n.4, 00004.