Table of Contents
- What are steam compressors?
- Contribution to energy efficiency
- What are the main industrial applications of steam compressors?
- Recent innovations in the steam compressor field
- Energy efficiency in industry: The role of steam compressors
- What factors influence the energy consumption of a compressor?
- Future trends in steam compressor use
- Conclusions
- References
Steam compressors are key components in the quest for industrial energy efficiency by optimizing energy use and reducing waste. In the industrial and mining environment, the generation of compressed steam is critical to the optimal functioning of operations. Choosing the right compressor can have a significant impact on product quality, energy efficiency and operational safety.
They raise steam pressure from low to high pressure steam, facilitating significant energy savings and contributing to the overall sustainability of industrial operations. Capture and reuse waste heat that would otherwise be lost to the atmosphere.
The purpose of this article is to explain what steam compressors are, how they work and highlight their impact on improving energy efficiency in industrial processes, highlighting their key role in sustainability and optimization of energy consumption.
What are steam compressors?
Compressors in general are mechanical devices designed to increase the pressure of a gas by reducing its volume. They are used in multiple industrial applications, from refrigeration systems to manufacturing processes, gas transportation and power generation. Steam compressors are designed to recover low-pressure vapor and deliver it at a higher pressure for reuse.
Operating principle of a steam compressor
It is based on the compression of a gas (usually steam) by reducing its volume, which increases its pressure and temperature. This process is performed by a mechanical device that applies energy to compress the gas. The following image shows an animated representation of the operation of a steam compressor.
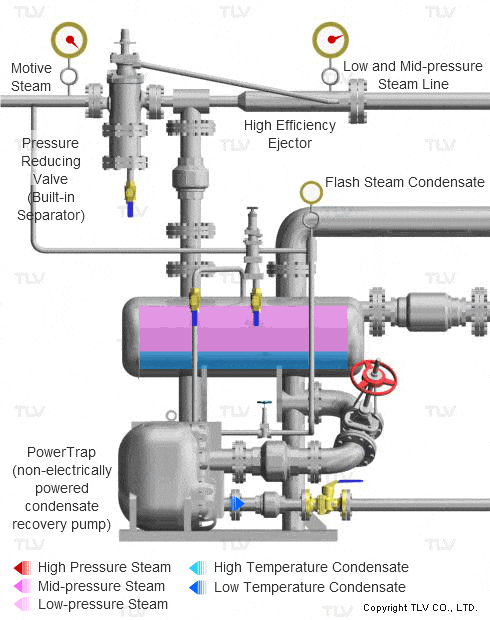
The compressor compression process is explained in the following steps:
- Intake: The compressor draws in gas or air from the surrounding environment through an intake valve.
- Compression: Gas or air is compressed by reducing the volume of the compressor chamber. Compression can be achieved through the use of pistons, rotors, impellers or vanes.
- Discharge: The compressed gas or air is then discharged through a discharge valve at a higher pressure than the inlet pressure.
- Cooling: The compression process generates heat, which can cause damage to the compressor and reduce efficiency. To prevent this, most compressors have a cooling system that removes heat from the compressed gas or air before it leaves the compressor.
The compression process increases the energy of the steam, to be used in industrial applications such as power generation or heating.
Steam compressor types
There are several types, but the most common are:
- Reciprocating compressors: They use pistons to compress the steam, increasing its pressure by reducing the available volume.
- Centrifugal compressors: They use the centrifugal force generated by a rotor to increase the steam velocity and, by means of a diffuser, increase its pressure.
- Screw or rotary compressors: Compress steam by means of the movement of two intermeshing rotors, which reduce the volume of gas trapped between them.
Steam compressor specifications and capacities
Centrifugal steam compressors are designed to handle large volumes of steam at high pressures. Typical specifications for these compressors are:
- Flow rate: 80 m³/h to 2000 m³/h
- Pressure range: 2,2 bar to 40 bar
These specifications allow the use in different industrial applications, representing versatile equipment adaptable to various process requirements.
Contribution to energy efficiency
Modern compressors are essential for improving energy efficiency1 in industrial processes. Their advanced design minimizes energy losses, optimizes power consumption and improves overall system performance. For example, in HVAC (heating, ventilation and air conditioning) systems, variable speed compressors adjust their operation according to demand, significantly reducing energy consumption.
In addition, technologies such as high-efficiency compressors and heat recovery systems take advantage of the heat generated during compression, increasing the sustainability of industrial processes.
Steam compression is a fundamental process in the optimization of various operations, from distillation to fluid heating, which are among the most energy-intensive processes in industry. In addition, steam compressors act as integrators, bridging gaps between different systems and minimizing energy losses that often occur in disconnected configurations.
Steam compressors represent a significant advancement in compressor technology because their operating system offers cleaner, more efficient and lower maintenance solutions for industries that require high quality steam compression. As the technology continues to advance, it is likely to become increasingly prevalent in a variety of industrial applications.
What are the main industrial applications of steam compressors?
Steam compressors have various industrial applications, especially in those sectors where the compression of gases or vapors is essential for production processes. Some of the main applications include:
- Heating plants: Steam compressors are used in industrial heating systems, where high-pressure steam is used to heat large facilities or manufacturing processes.
- Power generation: In power plants, steam compressors are essential to maintain the thermodynamic cycle of the steam generator, allowing the compression and expansion of steam in turbines to produce electricity.
- Refrigeration and air conditioning systems: Used in refrigerant compression systems, where vapor is compressed and then condensed to transfer heat.
- Chemical and petrochemical processes: In industries such as petrochemicals, steam compressors are used to compress gases such as methane or propane, which are needed in the production of chemicals and plastics.
- Food and pharmaceutical industry: In the sterilization and drying of products, steam compressors are used to generate high-pressure steam, which is applied to process or preserve food and medicines.
Steam compressors are used in all cases where steam with a higher pressure must be generated from existing steam using low pressure steam, especially when recovering excess low pressure steam and converting it into usable high pressure steam, the high pressure steam must be compressed to a higher pressure level without installing an additional boiler unit.
Recent innovations in the steam compressor field
In recent years, innovations in steam compressors have focused mainly on improving their energy efficiency and incorporating advanced technologies to optimize their operation. Some of the main innovations include:
One of the most important innovations in industrial energy efficiency is energy recovery in steam compressors. During the compression process, a considerable amount of energy is released as heat. Recovery systems are designed to capture this thermal energy and reuse it, significantly improving the plant’s energy efficiency.
For example, recovered heat can be used in secondary processes such as water preheating, space heating or in additional power generation cycles using steam turbines. This approach reduces primary energy consumption, and lowers operating costs by taking advantage of resources that would otherwise be wasted.
In addition, recovery systems are a key tool for meeting sustainability goals2 by helping to reduce greenhouse gas emissions. Leading companies in the industry have reported energy savings of up to 20% by integrating these solutions into their operations. This shows that steam compressors are not only essential in production processes, but also in corporate sustainability strategies.
Some key aspects of this technology are outlined below:
Integrally geared design: Some modern centrifugal steam compressors use an integrally geared design. This allows optimal speed selection for each compression stage, resulting in higher efficiency and a more compact overall design.
The following is an overview of the integrated geared compressor. Courtesy of: Atlas Copco Compressor Technique.

Steam compressor with integrated gearing.
Advanced control systems: The most upgraded models are equipped with sophisticated control systems that allow precise operation and monitoring. For example, the Maestro Universal control panel used on some models provides an integrated web server for constant monitoring and control.
Variable speed compressors: These compressors adjust their operating speed according to demand, which reduces energy consumption during periods of low load, avoiding unnecessary energy use.
Energy recovery systems: The integration of systems that capture waste heat generated during the compression process, allowing it to be reused in other industrial processes, contributing to greater energy efficiency.
Advanced materials: The development of lighter, stronger and lower friction materials has improved the operating efficiency of compressors, reducing energy losses and extending their service life.
Oil-free operation: Many of these machines now operate without oil, which eliminates the need for oil extraction filters and reduces the risk of contamination in the compressed steam. This is particularly important in industries such as pharmaceuticals, where steam purity is critical. These types of oil-free compressors have become an important innovation in this field, as they offer several advantages over traditional oil-lubricated designs.
Energy efficiency in industry: The role of steam compressors
Steam compressors are essential for optimizing energy consumption in industry, especially in energy-intensive sectors such as petrochemicals, power generation and manufacturing. Their main contribution lies in their ability to compress steam to specific pressures to maximize its usefulness in key industrial processes.
The energy efficiency of this equipment depends on several factors, such as their design, the materials used and the technology they incorporate. Modern compressors are designed to minimize energy losses through mechanisms such as variable speed control, which adjusts compressor operation to system demand in real time. This adjustment significantly reduces energy consumption by avoiding unnecessary operation or operation at suboptimal loads.
In addition, the implementation of intelligent monitoring systems allows industries to identify inefficient operating patterns, perform predictive maintenance and ensure that compressors are operating at their optimum. This not only reduces operating costs, but also improves sustainability by reducing the carbon footprint.
What factors influence the energy consumption of a compressor?
Steam compressors are essential for optimizing energy consumption in industry, especially in energy-intensive sectors such as petrochemicals, power generation and manufacturing. Their main contribution lies in their ability to compress steam to specific pressures to maximize its usefulness in key industrial processes.
The energy efficiency3 of this equipment depends on several factors, such as its design, the materials used and the technology incorporated. Modern compressors are designed to minimize energy losses through mechanisms such as variable speed control, which adjusts compressor operation to system demand in real time. This adjustment significantly reduces energy consumption by avoiding unnecessary operation or operation at suboptimal loads.
In addition, the implementation of intelligent monitoring systems allows industries to identify inefficient operating patterns, perform predictive maintenance and ensure that compressors are operating at their optimum. This not only reduces operating costs, but also improves sustainability by reducing the carbon footprint.
The energy consumption of a compressor depends on several factors, among which the following stand out:
- Compressor efficiency: Newer, well-designed compressors tend to be more efficient, reducing energy consumption. Compressors with technologies such as variable speed and advanced materials are more efficient.
- Operating conditions: Steam inlet temperature and pressure, as well as output demand, affect compressor performance. Operating outside optimum design conditions increases energy consumption.
- Compressor maintenance and condition: A compressor that is not properly maintained or has worn components, such as seals or pistons, can generate leaks and friction, which increases energy consumption.
- Control technology: Compressors with intelligent control systems, which adjust speed and operation according to actual demand, optimize energy use, reducing consumption during periods of low load.
- Compressor type: Centrifugal, reciprocating or rotary compressors have different efficiencies depending on the type of operation and workload. Centrifugal compressors, for example, are more efficient at high loads, while reciprocating compressors can be less efficient due to their intermittent cycling.
- Energy recovery: The integration of systems to recover the heat generated during compression makes it possible to reuse this energy, reducing the need for external energy sources, which has a positive impact on overall consumption.
These factors determine the energy consumption of a compressor and, therefore, its impact on operating costs and the sustainability of the industrial process.
Future trends in steam compressor use
Technological developments are setting a new direction for steam compressors, geared towards greater sustainability and efficiency. One of the main trends is the development of hybrid systems that combine steam compressors with other technologies, such as heat pumps or cogeneration systems, to make the most of waste heat from industrial processes.
In addition, the integration of real-time monitoring systems and predictive analytics, thanks to Industry 4.0, is transforming the way this equipment is managed. This not only makes it possible to anticipate failures, but also to optimize operational performance and reduce energy consumption.
Another relevant trend is research into new materials and coatings that improve the durability and thermal efficiency of compressors. These advances are designed to operate under extreme conditions, reducing wear and energy losses.
Finally, as part of the energy transition, steam compressors are adapting to more sustainable applications, such as carbon capture and thermal energy storage. These applications position compressors as a key component in the industrial systems of the future, aligned with global emission reduction targets.
Conclusions
Steam compressors represent a key element in the quest for greater energy efficiency in industry. Their ability to optimize the use of heat in industrial processes contributes significantly to reducing primary energy consumption and pollutant gas emissions. This positive impact translates into economic benefits for companies and progress towards environmental sustainability.
Today, technological innovations are transforming this equipment, adapting it to the current demands of the industry. From integration with intelligent systems to their application in sustainable processes such as carbon capture, steam compressors continue to evolve to meet global energy challenges.
It is important to adopt strategies that maximize the potential of this equipment, combining its use with efficient operating practices and proper maintenance. More than just a technical component, steam compressors are a strategic tool for the transition to a more efficient, profitable and environmentally friendly industry.
References
- https://www.atlascopco.com/content/dam/atlas-copco/compressor-technique/gas-and-process/documents/TMI_MVR_key_to_steam_energy_upgrade_within_a_polyolefin_plant.pdf
- https://www.digitalrefining.com/news/1007777/decarbonizing-process-heat-with-industrial-heat-pumps-and-steam-compressors
- Xiaohong Yin , Xinli Wang, Shaoyuan Li , Wenjian Cai; “Energy-efficiency-oriented cascade control for vapor compression refrigeration cycle systems”; Energy Volume 116, Part 1, 1 December 2016, Pages 1006-1019.