Table of Contents
- The need for quality in the metalworking industry
- Fundamentals of Statistical Quality Control (SQC)
- Tangible benefits of implementing the CEC
- Practical steps for SCC implementation
- Innovation and adaptation: CEC in today's world
- Common challenges in the implementation of Statistical Quality Control
- Conclusions
- References
Statistical Quality Control (SQC) represents a fundamental tool to improve quality in manufacturing processes, especially in the metalworking industry, where precision and quality are imperative. This article will address the implementation of CEC in the metalworking industry, and how this methodology not only ensures compliance with rigorous standards, but also drives continuous improvement and operational excellence.
The need for quality in the metalworking industry is undeniable. Every component, from the smallest parts to the largest structures, must meet exacting standards to ensure safe, durable and efficient operation. A single defect can have significant consequences, affecting not only the quality of the final product, but also the company’s operating costs and reputation.
In this context, the implementation of the CEC is presented as a beacon that guides companies towards continuous improvement. It is not just a statistical methodology; it is a strategic approach that uses data to make well-supported, proactive decisions at every stage of the manufacturing process. Beyond simply meeting standards and tolerances, CEC seeks operational perfection, a perfection that translates into exceptional metal-mechanical products.
The need for quality in the metalworking industry
In the complex symphony of gears and metal structures that defines the metalworking industry, quality stands as the distinctive bell that guarantees not only functionality, but also customer confidence. Every component, from the tiniest to the most monumental, plays a crucial role in the integrity and performance of end products that drive our modern world.
The pressing need for quality in this sector is not simply a standard, it is a non-negotiable requirement. The durability of a structure, the efficiency of a machine, and even the safety of the end user depend directly on the quality of each metal-mechanical part. A single defect can have significant repercussions, either on the functionality of the product or on the safety of those who use it.
In a market where competition is fierce and customer expectations are increasingly high, metalworking companies are driven not only by necessity, but also by the obligation to offer superior quality products. Quality becomes the hallmark that not only ensures customer satisfaction, but also builds a company’s lasting reputation in the industry.
In this context, the effective implementation of Statistical Quality Control (SQC) emerges as a strategic response to address not only the need but also the demand for quality in the metalworking industry. In the following points, we will explore how the CEC becomes the compass that guides these companies towards excellence, transforming not only their manufacturing processes, but also their position in a market where quality is the most valuable currency.
Fundamentals of Statistical Quality Control (SQC)
In the very fabric of the innovative metal-mechanical industry, the fundamentals of Statistical Quality Control (SQC) stand as unshakable pillars to ensure excellence at every stage of the manufacturing process. A thorough understanding of these fundamentals is essential to take full advantage of this methodology that has become a beacon for continuous improvement and exceptional quality.
At its core, CEC is more than a set of techniques; it is a systematic approach supported by data that seeks to identify, control and improve variability in production processes. Every statistical method used, from control charts to process capability analysis, has a clear purpose: to raise quality by ensuring that each component meets the strictest standards.
Dr. Walter Shewart’s control charts are crucial visual tools in the CEC arsenal. They allow monitoring the variability in a process over time, as shown in the graph in Figure 1, where you can see how the value of a variable is plotted on a run chart over time and compared to the Upper and Lower Control Limits, proactively alerting you to any deviation that may affect the quality of the final product. By understanding and effectively utilizing these charts, companies can make informed and quick decisions to maintain consistency.
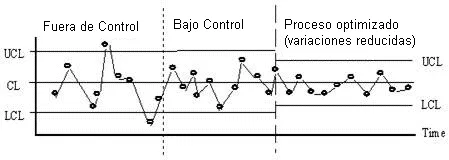
Capability analysis evaluates whether a process is capable of producing results within specified limits, as shown in Figure 2. This proactive approach not only ensures compliance with standards, but also drives optimization and the aspiration for excellence.
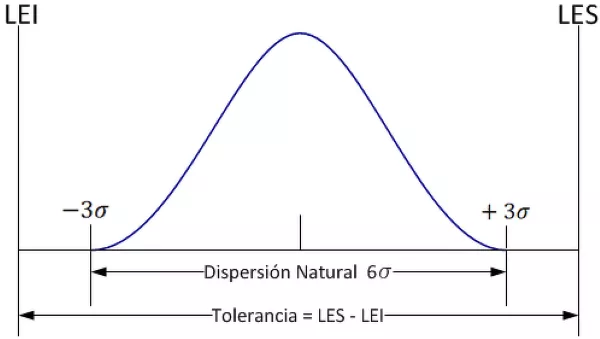
Tangible benefits of implementing the CEC
The implementation of Statistical Quality Control (SQC) in the metalworking industry is not only a strategic choice, but a vital step towards continuous improvement and operational excellence. The tangible benefits derived from this implementation not only impact the quality of the final products, but also redefine the efficiency and competitiveness of companies in this dynamic sector. Among the most notable benefits are the following:
- Reducing defects and increasing consistency: By analyzing and controlling process variability, companies can identify and address potential problems before they affect final product quality. This not only improves customer satisfaction by delivering more consistent products, but also reduces costs associated with rework and material waste.
- Resource and cost optimization: Effective implementation of CEC not only impacts quality, but also optimizes operational efficiency. By understanding and controlling process variability, companies can adjust their operations to make the most efficient use of available resources. This translates directly into cost reduction, which contributes to competitiveness in a market where efficiency is key.
- Continuous improvement and adoption of innovative practices: The CEC is not simply a static tool; it is a catalyst for continuous improvement. By identifying areas of opportunity through statistical analysis, companies can adopt innovative practices that go beyond existing standards. This not only keeps companies in step with market trends, but also allows them to stand out as innovation leaders in the metalworking industry.
- Rigorous compliance with standards and regulations: In an environment where compliance with standards and regulations is essential, the CEC acts as an uncompromising watchdog. It ensures that each metal-mechanical product meets specific requirements, which not only avoids potential legal sanctions, but also enhances the company’s reputation by demonstrating an unwavering commitment to quality and integrity.
Practical steps for SCC implementation
The transition to the successful implementation of Statistical Quality Control (SQC) in the metalworking industry requires a structured and conscious approach. Here we present practical steps that act as a guide, ensuring that every company can effectively embrace CEC and take full advantage of its benefits.
- Evaluation of current processes: Before introducing CEC, it is crucial to conduct a thorough evaluation of existing manufacturing processes. Identifying areas of variability and possible points of improvement provides a solid basis for implementation.
- Training of the CEC team: Forming a specialized CEC team is essential. Providing training to key team members ensures a thorough understanding of techniques and methodologies, facilitating the effective application of CEC in metalworking processes.
- Selecting the right CEC tools: Each company is unique, and the selection of CEC tools must be tailored to its specific needs. Identifying the right tools, such as control charts or capability analysis, is essential for effective implementation.
- Establishment of measurable goals and objectives: Defining clear and measurable goals and objectives is crucial to evaluate the success of the implementation of the CEC. Establishing key performance indicators (KPIs) allows for continuous monitoring and adaptation as needed.
- Gradual implementation and continuous monitoring: CEC implementation should not be abrupt. Introducing it gradually into the processes allows for a smooth transition. Continuous monitoring ensures that any deviations are addressed immediately, contributing to continuous improvement.
- Integration of modern technologies: Leveraging modern technologies, such as specialized CEC software or advanced data analytics, enhances the effectiveness of the implementation. Intelligent integration of technologies amplifies CEC’s ability to identify and address variabilities.
- Constant evaluation and adjustment: Successful implementation of the CEC does not end with its establishment. Conducting periodic evaluations and adjusting processes as necessary ensures that the methodology remains effective as operating conditions evolve.
By following these practical steps, companies in the metalworking industry can effectively adopt CEC, transforming their operations and positioning themselves as leaders in quality and efficiency, while taking giant steps on the road to organizational improvement.
Innovation and adaptation: CEC in today’s world
In the dynamics of the metal-mechanical industry, innovation is the key to stay ahead and Statistical Quality Control (SQC) is presented as a tool that not only adapts to the current times, but also drives innovation itself. In this regard, it is crucial to consider the following aspects:
- Integration of advanced technologies: The CEC has evolved with the incorporation of modern technologies. The integration of specialized software, advanced data analysis and real-time monitoring systems enhances CEC’s ability to identify and address variabilities more quickly and accurately.
- Process automation with CEC: Automation is a dominant trend in today’s metalworking industry. By using CEC in conjunction with automated control systems, companies can achieve greater consistency in production, reduce human error and accelerate data-driven decision making.
- Adaptation to Industry 4.0: In the era of Industry 4.0, the CEC is perfectly aligned with the principles of digitization and connectivity. Real-time data collection and analysis, together with the integration of intelligent sensors, enable more agile decision making and rapid response to process variations.
- Sustainability through CEC: Sustainability is a growing priority in the industry. By using CEC to optimize processes and reduce waste, metalworking companies not only improve quality, but also contribute to more sustainable practices, which resonates positively in an increasingly conscious marketplace.
The ability of the CEC to adapt to current times and embrace innovation not only strengthens its relevance, but also positions the companies that implement it as leaders in the industry.
Common challenges in the implementation of Statistical Quality Control
Despite the innumerable benefits that Statistical Quality Control (SQC) brings to the metalworking industry, implementation is not without its challenges. Recognizing and addressing these challenges proactively is essential to ensure a smooth transition and maximize the benefits of CEC. Some of the most outstanding challenges include:
- Resistance to change: Resistance to change is a common obstacle when introducing new methodologies. Some employees may show resistance due to fear of the unknown. In this regard, it is vital to provide clear communication about the benefits of SCC, offer comprehensive training and foster an organizational culture that celebrates continuous improvement.
- Complex data collection and analysis: Data collection and analysis can be overwhelming, especially when dealing with complex metal-mechanical processes. To address the above, it is advisable to implement specialized software tools and provide detailed training to ensure understanding and efficiency in data management.
- Lack of experience in statistical methodologies: Lack of experience in statistical methodologies can be a challenge, especially in companies that have not previously used the CEC, which is why it is advisable to hire external advice, provide specialized training and encourage collaboration between experienced teams and those who are learning.
- Integration with existing systems: Integrating CEC with established systems can present technological and compatibility challenges, for this it is recommended to conduct a thorough assessment of the existing infrastructure, work closely with IT teams and plan a phased implementation to minimize disruptions.
- Maintaining long-term relevance: Maintaining the relevance of the CEC over the long term can be a challenge in a constantly evolving business environment, which is why it is important to establish a system of regular review and updating, encourage continuous team participation and adapt to new technologies and emerging methodologies.
By proactively addressing these challenges, companies can prepare for a successful implementation of the CEC, ensuring that it becomes a solid pillar in their quest for quality excellence. In the following points, we will conclude our journey by exploring the key findings and offering a call to action for companies to dive into CEC implementation with confidence and determination.
Conclusions
CEC implementation not only meets standards; it raises quality to exceptional levels, positioning companies as leaders that not only meet expectations, but exceed them.
The CEC, in metal-mechanical processes, transforms challenges into opportunities for continuous improvement. Each fluctuation becomes a point of analysis and optimization, allowing companies not only to correct problems, but also to evolve towards more efficient and effective operations.
CEC’s ability to adapt to the modern era, integrating advanced technologies and embracing digitalization, ensures its relevance in a constantly evolving business environment. Industry 4.0 finds in CEC a strategic ally that not only adapts to digital transformation, but also drives efficiency and data-driven decision making.
Sustainability, increasingly high on the business agenda, finds in the CEC an ally in the reduction of waste and the optimization of resources. By contributing to more sustainable practices, the CEC not only improves quality, but also builds a path towards a more ethical and responsible operation.
References
Own source