Introduction
Special alloy pipes are an important topic in the industry, where reliability and performance are unwavering, as they play an important role in critical environments, where extreme conditions challenge the durability of the materials. This article will thoroughly explore special alloy pipes for critical services, their applications, properties, corrosion and low temperature resistance, associated norms and standards, as well as high-strength metals and high-temperature alloys.
What is a special alloy?
Specialty alloys represent a metallic fusion designed to withstand extreme environments, providing superior properties compared to conventional metals. These amalgams are synthesized by combining different elements, seeking to achieve specific characteristics such as resistance to corrosion, resistance to high temperatures and low temperatures.
Special metals: Alloy foundations
Specialty metals act as fundamental building blocks for creating special alloys. Titanium, nickel, cobalt and tungsten are the protagonists that, when combined, form exceptional alloys capable of resisting critical conditions, regardless of temperature.
Special alloys are distinguished by their ability to withstand extreme conditions, whether in corrosive environments, at high temperatures or under intense pressures. Corrosion resistance is especially crucial in the chemical industry, where exposure to aggressive substances can quickly deteriorate conventional materials. Additionally, these alloys offer exceptional durability, extending the life of pipes and reducing maintenance costs.
Special Alloy Pipe Applications
Special alloy pipes have diversified applications in industries ranging from chemical to nuclear. These become indispensable in systems where material integrity is essential to ensure safety and operational performance.
Chemical industry
In corrosive chemical environments, special alloy pipes exhibit corrosion resistance, reducing maintenance costs and ensuring long service life. The chemical stability of these alloys is significant for the transportation of aggressive chemicals.
nuclear industry
In nuclear applications, where radiation and extreme conditions are common, special alloy tubing is crucial to resist corrosion and wear. Its role in refrigeration and transport systems for fluids with nuclear traces guarantees safety and operational efficiency.
The implementation of special alloy pipelines in the nuclear industry not only improves safety and operational efficiency, but also supports efforts towards sustainability in power generation. Greater durability reduces the need for frequent replacement, thus reducing waste generation and optimizing the use of resources.
Oil and gas industry
In the oil and gas industry, where conditions are especially harsh, special alloy pipes are essential. They resist corrosion in highly aggressive environments and maintain their structural integrity under high pressure and temperature conditions, thus contributing to the efficiency and safety of hydrocarbon extraction, transportation and processing.
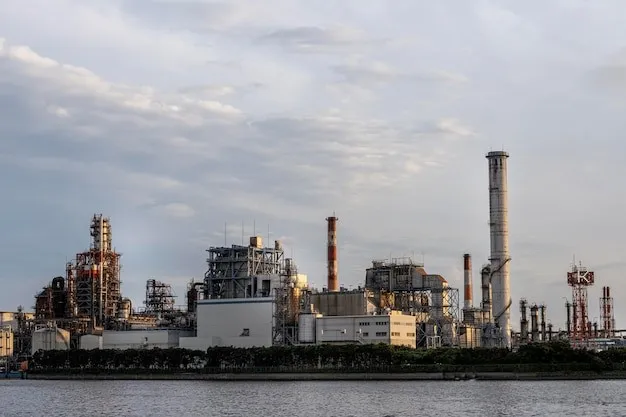
Properties of special alloys for pipes
Special alloys exhibit a unique combination of properties, highlighting mechanical strength, corrosion resistance and adaptability to different temperature ranges.
Mechanical strength
Special alloy pipes are known for their exceptional mechanical strength, making them ideal for withstanding heavy loads and high pressure conditions. This feature is essential in applications that require durability and structural strength.
When it comes to strength, alloy tubes are often considered superior. Due to their diverse composition, they can be tailored to meet specific strength requirements. This makes them ideal for applications where heavy loads or high pressures are a concern. Stainless steel tubes, although strong, may not match the custom strength of alloy tubes.
Corrosion resistance
Corrosion resistance is a critical property, especially in aggressive chemical environments. Special alloys form a protective layer that protects them from corrosion, significantly increasing their useful life and reducing operational risks. The chromium content gives it resistance to corrosion. Resistance can be demonstrated in reducing acids as well as against pitting attacks in chloride solutions.
Durability is a decisive factor, especially in industries where pipes are subject to aggressive conditions. Stainless steel is known for its corrosion resistance and durability, making it an excellent choice in such scenarios. Alloy tubes, although strong, may not offer the same level of corrosion resistance.
High temperature resistance
In environments with high temperatures, these pipes maintain their structural integrity and mechanical properties. According to the ASME code series B31.3, high-temperature tubing is commonly used in those applications where the service temperature reaches up to 1250°C (649°F), depending on its grade. In these temperature ranges, the steel, alloyed with Chromium and Molybdenum, provides adequate resistance for the demanding services that we have mentioned.
Chromium (Cr) increases ductility, hardening and corrosion resistance under elevated temperatures. For its part, Molybdenum increases the tensile strength of steel and its hardness at high temperatures.
Due to these characteristics, A335 pipe is commonly used in refining (Grades P5 and P9), in generation and petrochemical plants (P11, P22, P91) as well as in high temperature lines, reheating lines, distillation, cracking, units. coke, among other applications.
Low temperature resistance.
These alloys retain their toughness and resistance at extremely cold temperatures, such as in liquefied natural gas (LNG) applications and cryogenic plants. Pipes for low temperatures solve a diametrically opposite problem from the point of view of service conditions: The service temperatures of a pipeline steel below 0°C (32°F). The risk of embrittlement and crack propagation at high speeds is an important design consideration.
There are in the A333 and B31.3 standards grades for extreme conditions, suitable for cryogenic service around -196°C (-321°F MDMT according to ASME B31.3) and there are also more commercial grades, such as Grade 6, with minimum service temperatures of -46°C (-51°F), which has good ductility at low temperatures as a result of the controlled addition of Manganese (Mn) and Columbium (Niobium-Nb), whose application is particularly useful in plants of gas compression, especially in the steps prior to liquefaction.
Norms and standards for special alloy pipes
The quality and safety in the manufacture of special alloy pipes are supported by rigorous regulations and standards. Organizations such as ASTM, ASME, and API establish specific guidelines for the manufacturing, testing, and certification of these materials. Compliance with these standards ensures that pipes meet strength, durability and safety requirements across all temperature spectrums.
The standards applicable to high-strength steels are essential to ensure reliable performance under extreme conditions. Regulations such as API 5L for welded steel pipes are examples of guidelines that establish the necessary requirements for the manufacture of these materials, apart from other documents where additional properties are required. corrosion resistance and good performance at low and high temperatures as described below.
To ensure the integrity and quality of pipelines in highly corrosive environments, it is important to adhere to rigorous standards and regulations. Some key standards include ASTM A312 (austenitic stainless steel pipe), ASTM A790 (duplex and superduplex stainless steel pipe), and ASTM A358 (austenitic stainless steel welded pipe). Meeting these standards ensures that pipes will resist corrosion and maintain their structural integrity over time.
Extreme service conditions (high or low temperatures and/or pressures) represent special design challenges that require specific considerations for each type of material. In this type of applications, special alloys for pipes come into play. There are a variety of different grades in the ASTM A335 specification, each with different particular considerations, (P1, P2, P5, P9, P11, P12, P15, P21, P22, P24, P36, P91, P92, P122, P911) and for A333 (Grades 1, 3, 4, 6, 7, 8, 9, 10 and 11), each with grade-dependent chemical and mechanical properties.
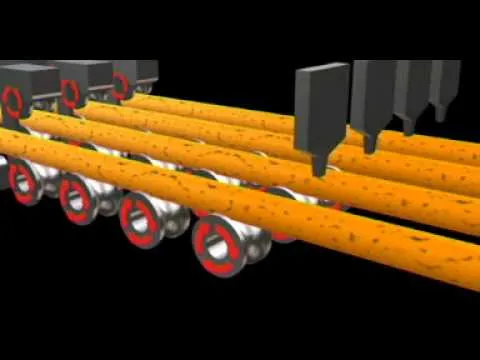
Seamless tube manufacturing process
Conclusion
Specialty alloy pipes prove to be the one-stop solution for critical environments, facing challenges from scorching temperatures to frigid conditions. Their ability to resist corrosion, maintain mechanical integrity, and adapt to different temperature ranges makes them essential elements in various industries. Compliance with norms and standards, along with the use of high-strength metals and low-temperature alloys, ensures excellence in materials engineering. These pipes not only meet technical requirements, but also contribute to safety and efficiency in the industrial landscape, demonstrating their resilience in all industrial environments.
Bibliographic references
- CHANGJIANG SEAMLESS STEEL PIPE MANUFACTURER. Alloy Tubes vs. Stainless Steel Tubes: A Comprehensive Comparison; Consulted on December 7, 2023;
- TECNACORP. Pipe in special alloys for high and low temperatures; Consulted on December 7, 2023; https://teknacorp.com/index.php/tuberia-en-aleaciones-especiales-para-altas-y-bajas-temperaturas/
- YENA ENGINEERING . A Clear Explanation of Different Types of Stainless Steel Pipes; Consulted on December 8, 2023; https://yenaengineering.nl/clear-explanation-of-different-types-of-stainless-steel-pipes/
- ANUP KUMAR DEY . Types of Pipe Materials and Their Selection / Metallic Pipe. Consulted on December 8, 2023; https://whatispiping.com/piping-material-selection/