Table of Contents
- Global process of a crude oil refinery
- Physical separation processes (decantation, distillation)
- Transformation or conversion processes (alkylation, cracking)
- Purification or treatment process (desulfurization, dehydrogenation, desalination)
- Mixing process
- Auxiliary, storage and distribution processes
- Basic principles of the atmospheric distillation process
- Problems and solutions in atmospheric distillation
- Choice of materials and standards in the design of distillation towers
- Conclusions
- Bibliographic references
Atmospheric distillation, as a unit operation, represents the most prevalent separation procedure in the chemical process industry. It represents the dominant technology in various chemical process industries, especially those that demand the distillation of large volumes of fluids.
These industries include oil processing, petrochemical production, natural gas processing, liquefied gas separation, as well as the production of hydrocarbons and solvents, among others. Its greatest application is observed in the oil industry.
“Atmospheric distillation is implemented in approximately 95% of all separation processes worldwide. In the United States, more than 40,000 columns are used with an investment of 8,000 million dollars and an energy consumption equivalent to 15 to 54 million tons of crude oil per year, representing 15% of industrial energy consumption in the country”1. Therefore, distillation is one of the most studied unit operations in the entire history of the chemical industry.
This article will discuss the different refining processes that make up an oil refinery, focusing mainly on the atmospheric distillation process within the global crude oil processing scheme.
Global process of a crude oil refinery
The objective of this content is to provide, in general terms, a vision of the types of crude oil refining processes, as well as the operational sequence in which these processes are carried out2. Globally, it is possible to classify these processes as follows:
- Physical separation processes (decantation, distillation).
- Transformation or conversion processes (alkylation, cracking).
- Purification or treatment processes (desulfurization, dehydrogenation).
- Mixing processes.
- Storage and distribution processes.
These processes are integrated in the following way 2 :
Initially, the oil, stripped of its impurities, is subjected to a heating process in a furnace and is subsequently introduced into a distillation column operated at atmospheric pressure. In this column, the crude oil is separated into different components, including butanes and light gases, gasoline, heavy naphtha, kerosene, heavy diesel and residual crude oil; which is fed to another process called vacuum distillation, where a new separation is carried out, resulting in a higher stream of vacuum gas oil and residual heavy crude oil.
During the initial distillation processes, the separation of products does not alter the nature of the crude oil; The hydrocarbons that make it up are segregated according to their respective boiling points. In the vacuum column, heavy crude oil is obtained, which is directed to a thermal cracking or delayed coking unit, giving rise to the production of wet gas, coking gasoline, diesel oil and coke (residue).
Gasoils are used as feed for catalytic cracking or hydrogen cracking units. They fragment heavy molecules into compounds whose boiling temperatures correspond to the range of gasoline and distillate fuel. These processes constitute transformations, where hydrocarbon molecules are decomposed and, in some cases, combined through triggered reactions to obtain higher quality products.
The products derived from hydrogen cracking are saturated and the unsaturated products of catalytic cracking are saturated to improve quality through catalytic reforming or hydrogenation. Gasoline streams from the distillation columns, coke converter and cracking units are fed to a catalytic reformer to improve its octane rating. Reformed gasolines are used to create regular and special gasoline blends.
The wet gas from the distillation unit, coming from the coker and cracking units, is decomposed in the vapor recovery section, generating fuel gas, LPG (Liquefied Petroleum Gases, mainly propane), unsaturated hydrocarbons (propylenes, butylenes and pentenes), normal butane and isobutane.
This gas is used as a source of energy in the refinery’s furnaces. Normal butane is isomerized and, together with unsaturated hydrocarbons and isobutane from the vapor recovery unit, is introduced into the alkylation unit to produce alkylates that are mixed with gasoline to improve octane.
Middle distillates from distillation units, coking units and cracking units are combined with diesel fuels, jet fuels and heating fuels. Heavy diesel from the vacuum unit and reduced naphthenic or paraffinic crude oil are processed to obtain the bases necessary for lubricant preparation.
Below is a representative diagram (figure 1) and a brief description of the general process types of a refinery:
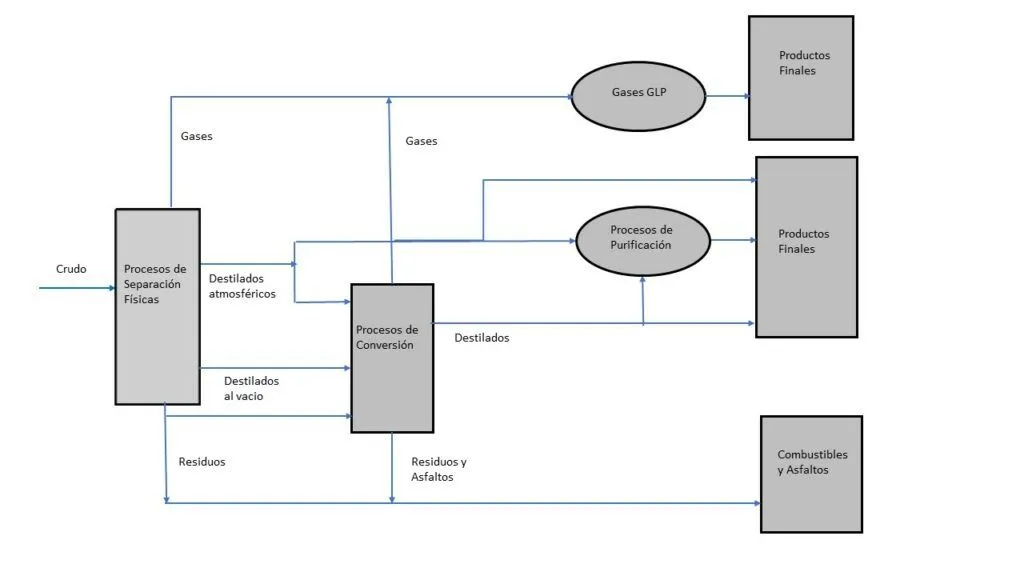
Physical separation processes (decantation, distillation)
Oil undergoes a physical fractionation process in atmospheric and vacuum distillation towers, breaking down into sets of hydrocarbon molecules with different ranges of boiling temperatures, known as “fractions.”
Transformation or conversion processes (alkylation, cracking)
They consist of fragmenting hydrocarbon molecules with the aim of improving quality. The most commonly used conversion methods to change the size and/or structure of hydrocarbon molecules are the following:
- Hydrocracking, thermal and catalytic cracking, coking and viscosity breaking.
- Alkylation and polymerization.
- Isomerization and catalytic reforming.
- Treatment.
Purification or treatment process (desulfurization, dehydrogenation, desalination)
It consists of removing impurities from oil such as water, inorganic salts, suspended solids, through desalination (dehydration), in order to reduce corrosion, plugging and the formation of scale in the equipment, and avoid poisoning of the catalysts in the process units.
Mixing process
This process involves mixing and combining hydrocarbon fractions, additives and other components to obtain products with specific performance properties.
Auxiliary, storage and distribution processes
The petroleum industry has various facilities and systems that support hydrocarbon processing operations, including heat generation, product movement and storage. These operations range from firefighting systems to laboratories and warehouses, providing essential support for refining activities.
Basic principles of the atmospheric distillation process
Distillation is a fundamental process in the refining industry, through which the separation of hydrocarbon components is achieved according to their different boiling points 3 . In the refinery, the desalted crude oil is preheated using heat exchanger systems.
Subsequently, it enters a direct flame furnace and is fed to the distillation tower near the bottoms, with pressure slightly above atmospheric and a temperature ranging between 343 ºC (650 ºF) and 370 ºC (700 ºF) to avoid clogging problems.
The crude oil is separated into fractions that, after further processing, will give rise to main products, such as liquefied petroleum gas, gasoline, diesel, fuel and special naphtha for the production of petrochemicals.
The lighter fractions of the crude oil are transformed into steam, ascending through the tower, where the temperature decreases with height. The heaviest fractions are recovered at the bottom of the tower and are called residue.
The distillation tower, a steel cylinder, contains horizontal plates that separate and collect the liquids, becoming lighter at higher altitudes. Each plate facilitates evaporation, condensation and contact between phases through perforations and an overflow system that maintains adequate liquid levels.
Each contact, called a stage, consists of a mixture of phases to promote rapid partitioning of the species by mass transfer, followed by phase separation. Condensed water inside the tower can cause corrosion to its internal components. The desired fractions are extracted from extraction plates, the height of which in the tower is determined during design.
During distillation, the light fractions are removed, leaving a heavy residue that will be subject to vacuum distillation. Consequently, in a “topping plant” light fractions of crude oil, such as gasoline and/or diesel, are obtained, for example, by distilling crude oil.
Initially, crude oil is fed at one or more points along the distillation column or fractionation column, as shown in Figure 2. Due to the difference in properties between the vapor and liquid phases, liquid flows down the column, while vapor flows up, coming into contact with liquid at each stage.
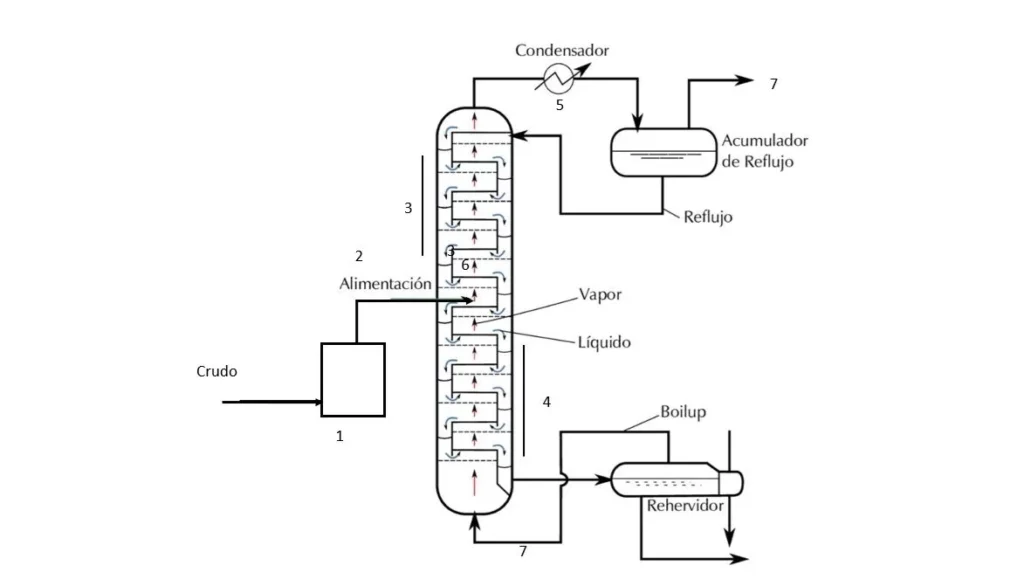
This overall flow pattern in a distillation column provides countercurrent contact of vapor and liquid at all stages through the column4. The liquid that reaches the bottom of the column passes through a reboiler, where it is heated to provide vapor called boilup that is sent back to the column, and the rest of the liquid is removed as bottom product5.
The vapor reaches the top of the column, where it cools and partially or completely condenses in the top condenser. Part of this liquid is returned to the column as reflux and the remainder of this liquid is removed as distillate, or top product.
The lighter components (lower boiling point) tend to concentrate in the vapor phase, while the heavier components (higher boiling point) tend to concentrate in the liquid phase. The result is a vapor phase that becomes enriched in lighter components and a liquid phase that becomes more concentrated in heavy components as they travel through the distillation column.
The overall separation between distillate and bottoms depends primarily on the relative volatilities of the components, the number of contact stages, and the ratio of liquid phase flow rate to vapor phase flow rate.
The energy required to separate the species is added as heat to the reboiler, where the temperature is higher. Also, heat is removed from the condenser, where the temperature is lower. This often results in high energy demand and low overall thermodynamic efficiency.
Problems and solutions in atmospheric distillation
The challenges inherent in an atmospheric distillation plant, with variability in the quality of the raw material being a common and critical aspect. The presence of impurities such as water and metals can trigger problems that affect the distillation process and reduce the efficiency of the plant.
- Water contamination
- Problem: The presence of water can cause corrosion, emulsions and complications in the distillation process.
- Corrective Action: Implement effective dehydration systems to remove water in the feedstock.
- High sulfur content
- Problem: High sulfur content can affect the quality of distillate products and require additional treatments.
- Corrective action: Carry out a desulfurization process prior to distillation to reduce the sulfur content.
- Presence of metals
- Problem: Metals in the raw material act as unwanted catalysts, affecting efficiency and reducing the useful life of the equipment.
- Corrective action: Use chemical treatments or demetalization processes to eliminate or reduce the presence of metals.
- Variability in composition
- Problem: Fluctuations in the composition of crude oil can affect the distribution of distillate products.
- Corrective Action: Perform ongoing composition analysis and adjust operating conditions as necessary.
- Organic impurities
- Problem: Presence of resins and asphalt that clog equipment and reduce plant performance and generate corrosion problems.
- Corrective Action: Implement efficient filters and separation systems to remove impurities before distillation.
Choice of materials and standards in the design of distillation towers
Atmospheric distillation, a fundamental process in the oil industry, requires special attention in the selection of materials used in the design of atmospheric distillation towers, in strict compliance with specific regulations. These aspects are necessary to prevent internal corrosion problems and ensure the long-term integrity of the installation, complying with safety and environmental standards.
The importance of these elements is detailed below, considering the regulations mentioned previously.
- Resistance to aggressive environments: The atmospheric distillation tower must operate under challenging environmental conditions, which requires a robust design and corrosion-resistant materials, complying with regulations such as API RP 939-C for protective coatings and ASME BPVC for vessels. pressure.
- Prevention of losses and contamination: Regulations such as API RP 571 guide the evaluation of corrosion damage, contributing to a design that prevents product losses and avoids contamination. Proper selection of materials under these guidelines is necessary to ensure corrosion resistance.
- Long life: Compliance with regulations, such as NACE SP0169 and SP0296, ensures recommended practices for cathodic protection systems, contributing to material selection and design that extends the useful life of the tower.
- Operational efficiency: The design and corrosion-resistant materials, according to ASME BPVC, guarantee operational efficiency, minimizing maintenance costs. Compliance with workplace safety regulations, such as OSHA, is essential to maintaining a safe and operational work environment.
- Compliance with regulations and standards: The incorporation of corrosion-resistant materials is important to comply with industrial safety regulations and standards, such as NFPA 30 for the safe storage of flammable liquids. Following these regulations avoids regulatory sanctions and guarantees a safe and environmentally responsible operation.
Conclusions
Preventing problems during atmospheric distillation is important to maintain the integrity of the process and ensure the quality of the resulting products. Variability in raw material composition, the presence of impurities such as water, sulfur and metals, as well as possible organic contamination, are common problems that could compromise efficiency and profitability.
Implementing preventive measures, such as dehydration, desulfurization systems and constant monitoring, is necessary to avoid corrosion, guarantee a homogeneous distribution of products and prolong the useful life of the equipment. Diligent attention to these aspects not only preserves operational integrity, but also contributes to long-term sustainable and profitable production in the crude oil refining industry.
Investment in a solid design and resistant materials, guided by specific regulations, is essential to prevent internal corrosion problems in atmospheric distillation towers. This approach not only protects the infrastructure, but also contributes to the efficient performance, sustainability and long-term operational security of the facility.
Under this context, we invite you to read the following content referring to corrosion problems and their control in crude oil atmospheric distillation systems.
Bibliographic references
- Luque S Rodríguez, Aurelio B. Vega Granda. “Advanced simulation and optimization in the chemical and process industry : HYSYS.”
- Crude Refining; consulted 12/31/2023: https://es.slideshare.net/WilderLoza/cesos-de-refinacion#2
- King, C. J. (1980). Separation processes . New York: McGraw-Hill.
- Perry, R.H. & Green, D.W. (2008). Perry’s chemical engineers’ handbook. New York: McGraw-Hill, 7 edition.
- Seader, JD, Henley, EJ, & Roper, DK(2011). Separation Process Principles: Chemical and Biochemical Operations. Hoboken, NJ: Wiley