Table of Contents
- What is a Slug Catcher?
- Types of Slug Catchers
- What Is a Slug Catcher composed of?
- Damage mechanisms in slug catchers
- Inspection and maintenance strategies
- Mitigation and maintenance strategies
- Conclusions
- References
- FAQs
- What is the function of a slug catcher in gas processing facilities?
- How do you choose the right type of slug catcher for a facility?
- How often should slug catchers be inspected?
- Are slug catchers affected by corrosion under insulation (CUI)?
- How can design optimization improve slug catcher reliability?
- What happens if a slug catcher fails?
In the oil and gas industry, the efficiency and safety of production processes are crucial. One essential component in this environment is the slug catcher or liquid slug separator, a device designed to handle specific phenomena in gas and oil flow lines. This article explores in depth the damage mechanisms that can affect liquid handling systems in gas plants, such as slug catchers, and emphasizes the importance of design optimization to ensure reliability and operational efficiency.
What is a Slug Catcher?
This type of static equipment is used in natural gas processing plants to separate and temporarily store condensates and other liquids that may be transported along with natural gas through pipelines. These “gas slugs” or liquid surges can be caused by changes in flow velocity, pressure fluctuations, or irregularities in the terrain’s topography through which the pipelines run.
This intermediate separator collects slugs and promotes uniform gas flow toward processing facilities. This not only improves process efficiency but also protects downstream equipment, such as compressors and dehydrators, from potential damage.
To better understand how a slug catcher handles these slugs in real-world operations, watch this short video animation: Source: Ed McIntosh.
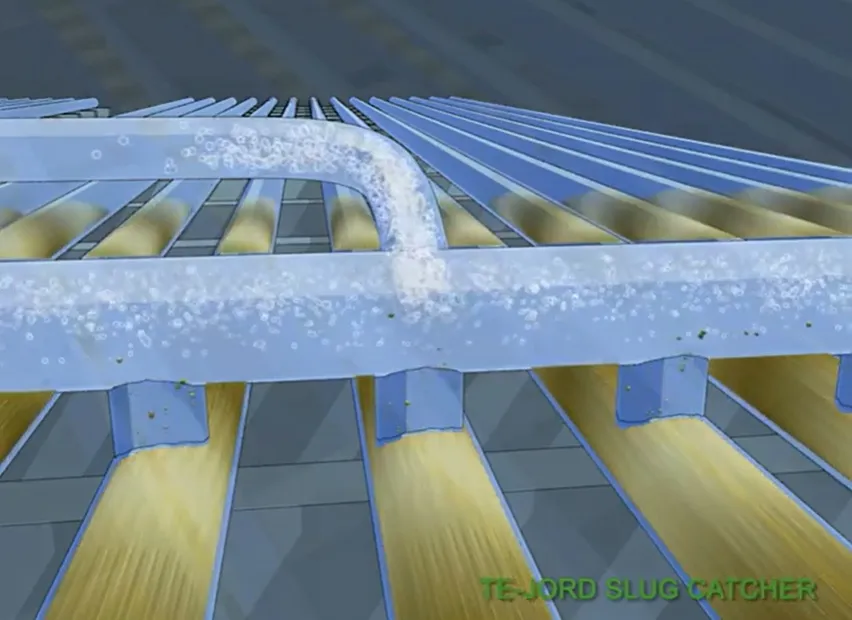
Animated operation of a Harp-Syle “Slug Catcher.
Types of Slug Catchers
1. Vessel-Type: The vessel-type separator operates as a basic two-phase separation unit. While the separation efficiency is not critical for a buffering system, the vessel’s volume certainly is. It must be large enough to accommodate substantial liquid slugs generated by a pipeline—especially during pigging operations. Since oil and gas pipelines typically operate under high pressure, the vessel must also be designed to withstand a high design pressure.
2. Finger-Type : The finger-type slug catcher offers a cost-effective solution to the challenge of designing a large high-pressure vessel. Instead of a conventional vessel, it uses sections of large-diameter piping to provide the required buffering volume. Since it is structurally easier to design piping to withstand high pressure compared to vessels, this design is advantageous. However, a large number of pipes is needed to provide sufficient volume, resulting in a larger footprint.
3. Parking Loop: The parking loop slug catcher combines features of both the vessel and finger types. It uses a vessel for basic gas-liquid separation, while the liquid buffering volume is provided by pipes shaped in a parking loop configuration. From these looped pipes, the liquid is slowly drained toward downstream processing equipment.
In the following image you can see one of the above mentioned types known as: Finger type.
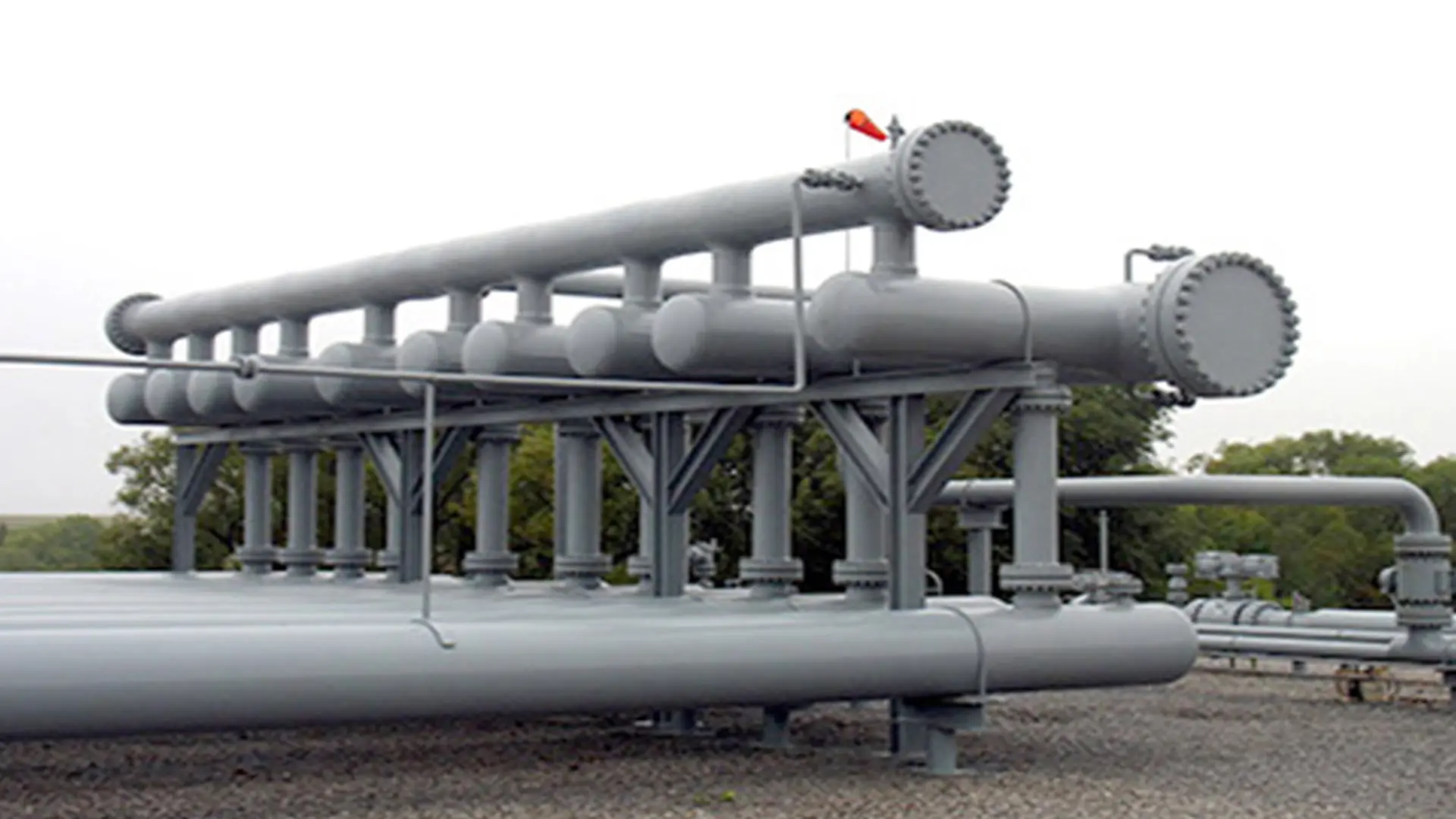
What Is a Slug Catcher composed of?
The configuration of this buffering system may vary depending on design specifications and application requirements, but it generally includes the following main components:
1. Separation Vessel or Main Body
- Main structure: This is the largest component of the buffering system, designed to withstand the pressure and volume of incoming slugs. It can be a large horizontal vessel or a series of parallel pipes (finger-type).
- Separation internals: These include baffles, impact plates, and other internal devices designed to enhance the separation of gas and liquid phases.
2. Inlet and Flow Distribution
- Inlet piping: Directs the gas and liquid flow into the slug catcher.
- Distributors: Help evenly distribute the incoming flow within the slug catcher.
3. Drainage and liquid collection systems
- Drains: Allow controlled removal of accumulated liquids.
- Liquid storage vessels: Temporarily store the separated liquids before they are processed or disposed of.
4. Gas outlet
- Gas outlet piping: Directs the separated gas to the next process or facility.
- Control Valves: Regulate the outgoing gas flow and maintain the desired operating pressure.
5. Control and monitoring systems
- Instrumentation: Includes pressure, temperature, and level sensors to monitor internal conditions.
- Control systems: Allow for automated operation and adjustment of process parameters.
6. Safety systems
- Pressure relief valves: Pressure, integrated into the safety system, play a crucial role in protecting them from overpressure scenario.
- Gas and liquid detectors: Alert operators of leaks or abnormal levels.
7. Accessories and supports
- Structural supports: Provide stability and physical support to the equipment.
- Insulation: Maintains temperature and protects against corrosion under insulation (CUI).
8. Auxiliary connections and valves
- Isolation and maintenance valves: Facilitate maintenance and repair operations.
- Connections for instrumentation and sampling: Allow for sample collection and additional instrumentation hookup.
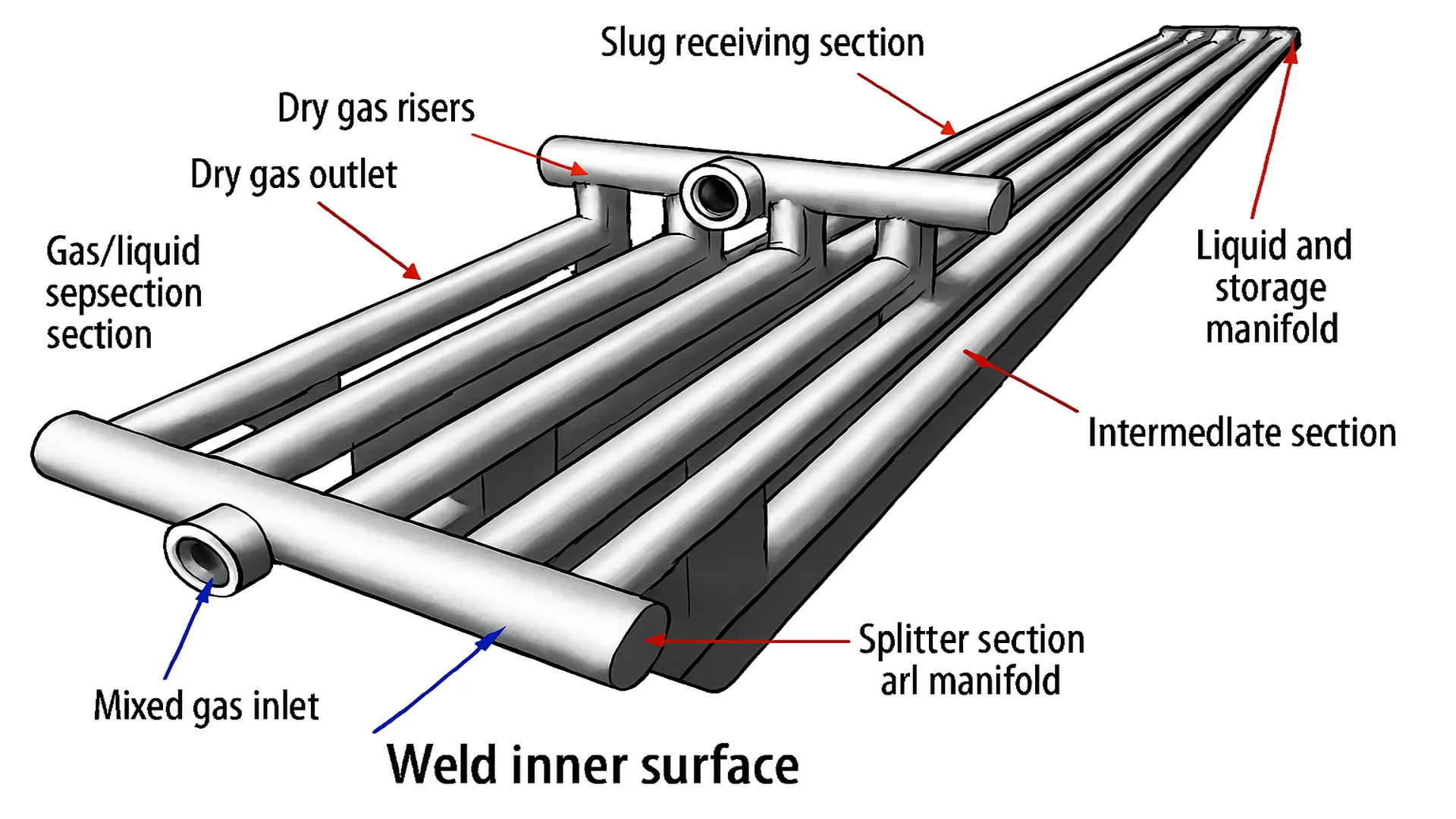
Damage mechanisms in slug catchers
1. Corrosion
Corrosion is one of the primary threats to this type of equipments. It can be accelerated by the presence of CO₂, H₂S, and water in natural gas. Internal corrosion may weaken the walls of the buffering system, potentially leading to structural failures. Corrosion under insulation (CUI) is also a concern, where moisture accumulates beneath the insulation layer, causing damage that is not externally visible.
2. Erosion
Erosion is caused by solid particles present in the gas and liquid flow, which impact the internal surfaces of the separator. Over time, this can lead to wall thinning and eventually to failures. Erosion is particularly problematic in areas where the flow direction or velocity changes.
3. Vibration fatigue
They are subject to vibrations caused by the pulsating flow of gas and liquids. These vibrations can induce fatigue in the materials, especially at connection points and welds. Vibration fatigue may result in crack formation and, eventually, catastrophic failure.
4. Slug impact damage
The slugs entering the buffering system can have significant mass and velocity, potentially causing impact damage. This is especially true if the buffering system design has not adequately accounted for the expected slug dynamics.
5. Design and fabrication issues
Inadequate design can be a major source of problems. This includes not only the size and shape of the separator system but also the selection of materials and the configuration of internal components. Moreover, fabrication errors—such as defective welds—can become critical failure points.
Inspection and maintenance strategies
Design optimization should be performed early in the engineering phase to ensure structural integrity and operational efficiency under variable flow conditions. Inspections and maintenance of a buffering systemare essential to ensure its safe and efficient operation in a gas processing facility. These activities focus on preventing, identifying, and correcting potential problems that could affect the performance and integrity of the equipment. Below are the most applied inspection and maintenance types for this equipments:
Routine inspections
- External Visual Inspection: A visual inspection is typically the first line of defense, used to identify corrosion, leaks, and external damage such as insulation, coating, and paintwork.
- Instrumentation and control systems inspection:
- Verify the correct functioning of sensors, transmitters, control valves, and alarm systems.
- Inspection of connections and accessories:
- Examine valves, flanges, gaskets, and other components for signs of leakage or wear.
Detailed periodic inspections
- Internal inspection:
- Requires a plant shutdown to access the internal components of the slug catcher. It focuses on identifying corrosion, erosion, impact damage, and verifying the integrity of welds and internal structures.
- Non-Destructive Testing (NDT):
- Techniques such as ultrasonic testing, radiography, magnetic particle inspection, and dye penetrant testing are used to detect cracks, corrosion, and weld defects without compromising the equipment.
- Wall thickness measurement:
- This measurement helps assess any reduction in wall thickness due to corrosion or erosion, providing critical data for evaluating equipment lifespan and risk.
- Cleaning and flushing:
- Involves removing sediment, debris, and liquid buildup that could lead to corrosion or blockages if left unchecked.
- Replacement or repair of worn components:
- Includes replacing valves, gaskets, and other elements subject to wear over time to ensure continued safe operation.
- Upgrading corrosion protection systems:
- May involve applying new coatings, paints, or implementing cathodic protection systems to extend the service life of the buffering system.
- Instrument calibration:
- Ensures the accuracy of pressure, temperature, and level measurements, which are vital for safe and efficient operation.
- Trend analysis and historical data review:
- Monitoring data over time allows operators to anticipate potential failures and schedule interventions before issues escalate.
- Modeling and simulation:
- Simulating various operating conditions helps evaluate the behavior of the this equipments and anticipate performance or integrity concerns.
Emergency response
- Safety system testing:
- Regular checks of pressure relief valves and leak detection systems are essential for ensuring readiness in case of abnormal events.
- Emergency drills and training:
- Personnel should be properly trained and prepared to respond effectively to emergency scenarios involving the separator system.
Documentation and records
- Maintenance and inspection logs:
- Keeping a detailed history of inspections, findings, and corrective actions is essential for compliance and operational transparency.
- Updating manuals and procedures:
- Maintenance procedures should be regularly updated to reflect current regulations, standards, and technological improvements.
All inspections and maintenance activities on separator systems should be performed by qualified personnel and in accordance with industry standards such as those set by API (American Petroleum Institute) and ASME (American Society of Mechanical Engineers). The frequency and scope of these actions depend on several factors, including the type of the buffering system, operating conditions, surrounding environment, and the equipment’s maintenance history.
Mitigation and maintenance strategies
1. Corrosion monitoring and analysis
Implementing real-time corrosion monitoring systems and conducting periodic analyses can help identify and mitigate corrosion before it causes significant damage. To learn more about how these failures manifest and are detected in industrial equipment, check out our article: https://inspenet.com/en/articulo/asset-corrosion-failure-analysis/
2. Erosion control
Using erosion-resistant coatings and optimizing design to reduce areas of high flow velocity can significantly lower the risk of erosion over time.
3. Anti-Vibration design
Incorporating design features that minimize vibration—such as supports and dampers—and performing fatigue analysis can extend the service life of the equipment.
4. Design optimization
The design of this equipment should be tailored to the specific characteristics of the gas and liquid flow. This includes using fluid dynamics simulations to anticipate and mitigate slug-related impacts.
5. Preventive inspections and maintenance
Regular inspections and preventive maintenance are essential to detect and address issues before they escalate into critical failures.
Conclusions
In the vast and complex landscape of the oil and gas industry, slug catchers stand out as critical components whose efficiency and safety are foundational to managing production processes. This article has explored the core principles behind their operation, the various design types, and most importantly the challenges tied to their maintenance and performance in the field.
From vessel-type designs to the innovative finger-type configurations and hybrid parking-loop systems, each approach addresses specific operational needs and faces unique technical hurdles. A deep understanding of these systems reveals not only the intricate engineering involved but also the critical importance of implementing robust inspection and maintenance strategies to ensure optimal functionality.
The second half of this analysis delved into common damage mechanisms such as corrosion, erosion, vibration-induced fatigue, slug impact damage, and design or fabrication flaws. If left unaddressed, these issues can lead to catastrophic failures. Hence, the importance of rigorous preventive and predictive maintenance cannot be overstated.
Mitigation strategies from corrosion monitoring to advanced design optimization—are not merely precautionary steps. They are essential practices to extend equipment lifespan and maintain operational safety. Ultimately, this article serves not only as a technical guide for professionals in the field but also as a reminder that excellence management reflects a broader commitment to efficiency, safety, and sustainability in the oil and gas industry.
References
- https://www.tfes.com/resources/technical-library/5-project-metrics-to-assess-if-you-need-a-finger-or-vessel-slug-catcher/
- https://enggcyclopedia.com/wp-content/uploads/2023/06/vessel-slug-catcher.jpg
FAQs
What is the function of a slug catcher in gas processing facilities?
It collects and separates liquid slugs from natural gas pipelines, preventing downstream damage and ensuring stable flow into processing units.
How do you choose the right type of slug catcher for a facility?
The selection depends on factors such as: Pipeline pressure and diameter, frequency and volume of slugs, available footprint,cost considerations; vessel-type units are compact but expensive at high pressure; finger-type and parking loop designs offer more scalable solutions.
How often should slug catchers be inspected?
Routine visual inspections may occur quarterly, while internal inspections and NDT are typically done annually or during scheduled shutdowns, following API and ASME standards.
Are slug catchers affected by corrosion under insulation (CUI)?
Yes. Since many slug catchers are insulated to maintain temperature, moisture trapped beneath insulation can lead to undetected corrosion, requiring periodic external and internal checks.
How can design optimization improve slug catcher reliability?
Design optimization uses fluid dynamics simulations and stress analysis to: Minimize erosion-prone zones, reduce vibration risks, improve drainage and liquid separation efficiency. It ensures the slug catcher is tailored to specific operating conditions.
What happens if a slug catcher fails?
Failure can result in: Gas flow disruptions, damage to critical downstream systems (compressors, separators), environmental and safety hazards. That’s why predictive and preventive maintenance is critical.