Table of Contents
- What is a servomotor?
- How does a servomotor work?
- What are the main components of a servomotor?
- Operating principles and applications
- How to control a servomotor?
- What are the applications of servomotors?
- Servomotor predictive maintenance and diagnostics
- Advantages of using servomotors in control systems
- Comparison between servomotors and stepper motors
- Cost and maintenance considerations
- Conclusion
- References
Servomotors, often referred to simply as “servos”, are sophisticated electronic devices that function as rotary or linear actuators. They excel at rotating and precisely positioning various machine components with remarkable efficiency. What distinguishes servomotors from conventional motors is their ability to move at specific angles, speeds, and positions, a capability monitored by an integrated controller.
These compact, yet powerful devices are prized for their energy efficiency and high power output relative to their size. Servomotors find wide applications in industries requiring precise control of angular or linear position, velocity, and acceleration.
Manufacturing companies, in particular, rely heavily on servomotors to precisely position control surfaces and rotate objects at exact angles and distances. Their versatility and precision make them indispensable in automated production lines, robotics, and other applications that demand meticulous motion control.
The autonomous nature of servomotors, combined with their precision and efficiency, has made them a fundamental technology in modern industrial automation and control systems.
What is a servomotor?
A servomotor is a highly specialized actuator designed for the chronometric control of rotary or linear motion that allows precise control of angular or linear position, velocity, and acceleration. It consists of a motor coupled to a sensor for position feedback.
This feedback loop allows the servomotor to maintain essential control of its motion. This mechanism facilitates precise control of various components, making these devices crucial in applications where accurate positioning and smooth motion are required. They are used in applications where precision positioning is required, such as robotics, CNC machinery, and automated manufacturing.
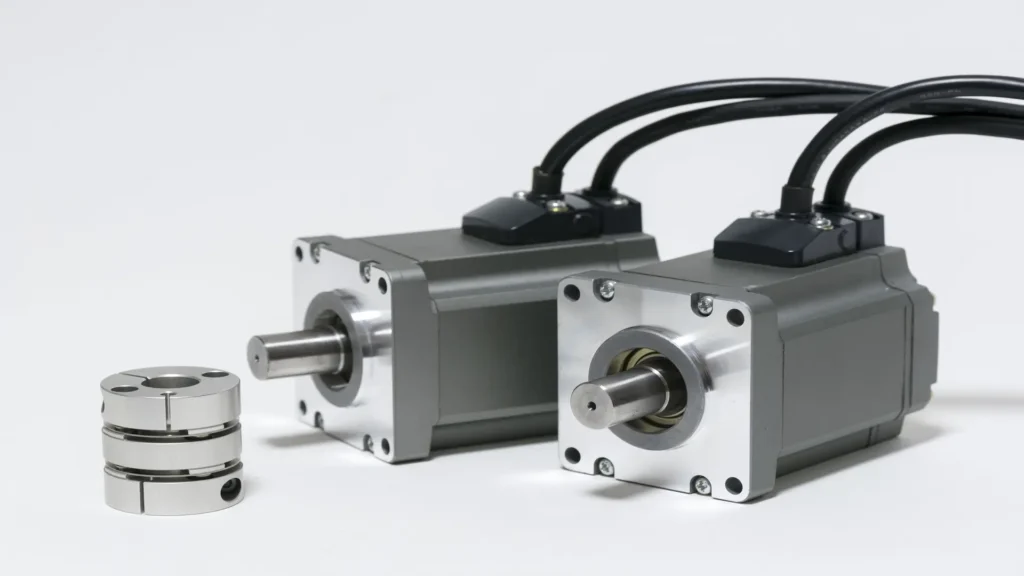
How does a servomotor work?
Servomotors are completely autonomous and turn different parts of the motor with incredible efficiency. What sets these machines apart is that the shafts of their motors can be moved to a specific angle, speed, and position (a capability that normal motors lack). This is done by the controller.
What are the main components of a servomotor?
Servomotors are made up of several key components, each crucial to the precise operation of the motor. Understanding these components provides insight into how servomotors deliver exceptional performance in automation and control applications.
I will now show you the most important components:
Motor (AC or DC): This is the primary source of mechanical power in the servo system. Whether AC or DC, the type of motor affects the application of the motor; AC is typically used for higher speed and power applications, while DC is preferred for more precise control. It determines the suitability of the motor for high-power or precision control applications.
Control circuit: Often considered the brain of the servomotor, this component processes incoming signals from the controller and sends commands to the motor. It determines position, speed, and torque based on the inputs received. It also ensures that the motor operates exactly as indicated by the input signals.
The servo drive acts as an intermediary between the motor and the control system: It receives control signals and supplies the motor with the power required to achieve the desired motion, adjusting voltage and current as necessary based on feedback.
Transmission gears: These are crucial for amplifying the torque output of the motor, enabling precise movements. The gears are connected to the motor shaft and help adjust the mechanical advantage according to requirements.
Servo amplifier: This component amplifies the signals from the control circuit, ensuring that they are strong enough to effectively drive the motor.
Encoder: Encoders are advanced feedback devices that provide detailed position or velocity information about the motor shaft to the control circuit. They can be incremental, providing relative position data, or absolute, providing specific position information at any time.
Power supply: Servomotors require a dedicated power supply to provide the electrical power necessary for operation. The specifications of this power supply depend on whether it is an AC or DC servomotor.
Cooling system: Depending on their application and environment, some servomotors include cooling systems to prevent overheating, which can affect performance and long service life.
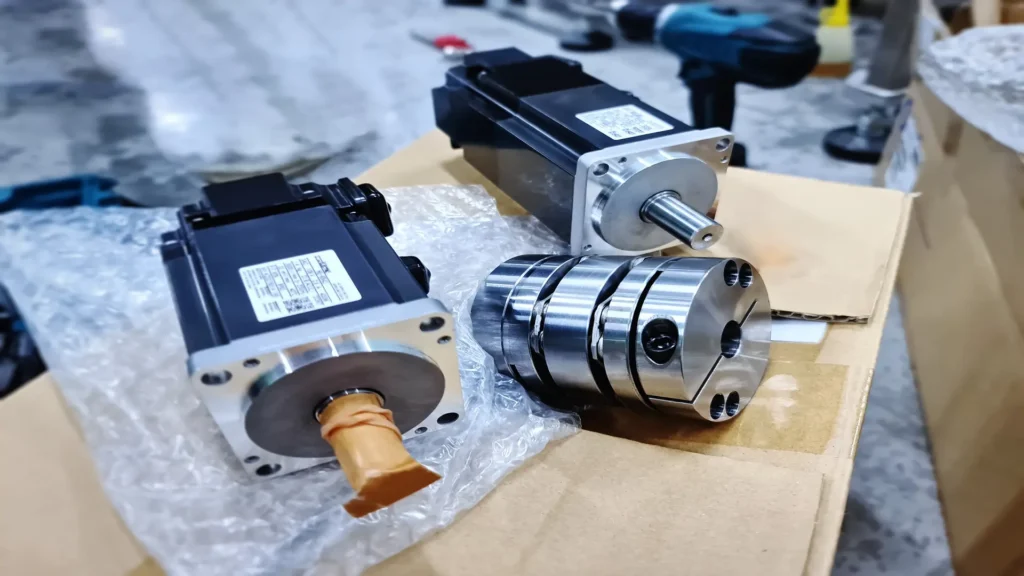
Operating principles and applications
They are critical devices for improving efficiency and accuracy in a variety of industrial applications. They are widely used in automation systems, where the ability to control motion accurately is crucial.
In CNC machinery, they drive the motions needed to cut, mill, and shape parts with exceptional precision. Similarly, in robotic arms used on assembly lines, servomotors provide the dexterity and repeatability needed to perform complex assembly tasks repeatedly without fatigue.
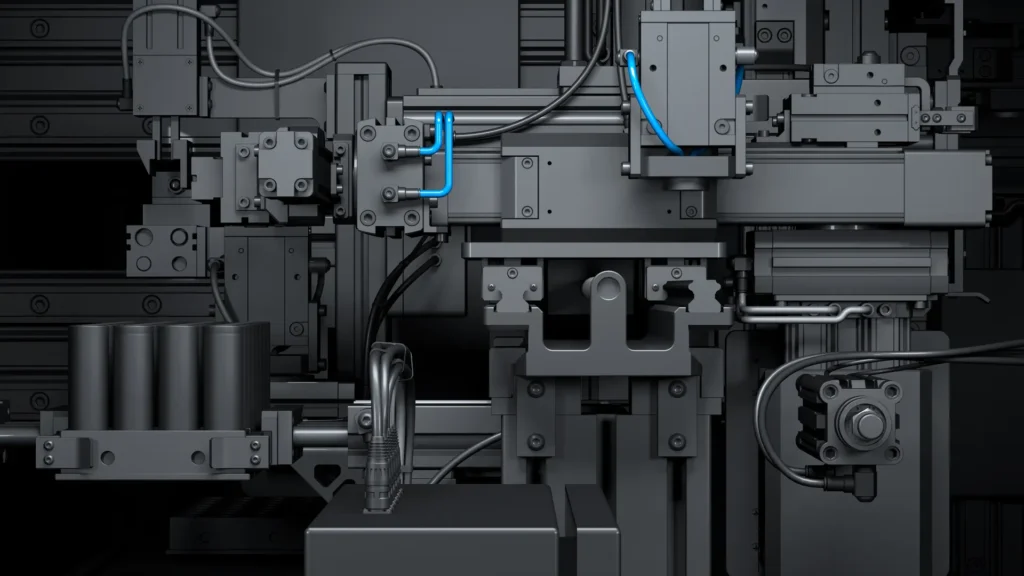
How to control a servomotor?
Controlling a servomotor involves several methods that ensure that its operations are accurate and efficient. Central to the operation of servomotors is the use of pulse width modulation (PWM), a technique that regulates motor motion using controlled digital pulses.
This modulation adjusts the angle of the motor shaft by varying the length of the pulse sent to the motor, which facilitates accurate positioning.
In addition, pulse trains (a series of on and off pulses) control the speed and position of the servomotor. These pulses are crucial in determining the angle and speed of rotation as a function of their frequency and duration.
What are the applications of servomotors?
Consumer electronics: In the consumer electronics sector, servomotors drive the improved functionality and user experience of many devices. For example, they are crucial in cameras for autofocus and image stabilization systems, making it easier to obtain sharp images even in dynamic conditions.
In-home entertainment systems, are used to operate complex mechanisms in video game consoles and virtual reality setups, providing realistic and responsive user interactions.
Specialized equipment: In the aerospace industry, they are used for the specific control of mobile aerodynamic devices, such as ailerons and rudders, which are vital for flight stability and maneuverability. In addition, as medical devices, they ensure the functionality of surgical robots, where they facilitate complex, minimally invasive procedures with a precision that human hands cannot achieve.
CNC machine applications for machining tasks
The application of servomotors in CNC (Computer Numerical Control) machines for machining tasks is, in fact, a crucial area where precision and efficiency are paramount.
CNC machines are widely used in manufacturing for their ability to produce complex parts with high accuracy and repeatability. Servomotors play a vital role in these machines, controlling multi-axis motion with precision.
Axis control: Servomotors are primarily used to control the motion of the machine axes (usually X, Y & Z, but sometimes include additional rotary axes). Each axis is driven by an independent servomotor, allowing precise positioning of the cutting tool or workpiece.
Contouring and complex path following: In operations that require following complex 3D paths (such as in mold making), the precise control and fast response of the servomotors enable smooth and accurate contouring. This is especially important in high-speed machining applications.
Servomotor predictive maintenance and diagnostics
Servomotor feedback systems provide valuable data for predictive maintenance and diagnostics. Monitoring parameters such as torque, temperature, and position errors can help identify, detect, analyze, and apply solutions to potential problems before they cause machine failure.
The use of servomotors in CNC machining has contributed significantly to the advancement of manufacturing technology. Their ability to provide high torque, precise positioning, and fast response has enabled the development of faster, more accurate, and versatile CNC machines.
As CNC technology continues to evolve, we are seeing trends such as direct-drive servomotors (which eliminate the need for gearboxes), more advanced control algorithms, and the integration of servo systems with IoT and Industry 4.0 technologies. These advances are further enhancing the capabilities of CNC machines, pushing the boundaries of what is possible in precision manufacturing.
Advantages of using servomotors in control systems
Servomotors are known for their precision control of position, speed, and torque, which makes them especially effective in applications where accurate and dynamic motion control is required.
First, they use real-time feedback to continuously adjust their performance according to the needs of the system. This means that they only consume the amount of power needed to accomplish the task at hand, reducing energy waste.
Unlike other motors, which can operate at constant speeds or without considering variations in load, servomotors adjust their power consumption according to instantaneous demand. It is have fast response and more efficient acceleration and deceleration control. This modulation capability allows optimal operating points to be reached and maintained more quickly, minimizing energy losses associated with transients or operation at less than ideal speeds.
Comparison between servomotors and stepper motors
Situations where it is preferable to use a servomotor
1. Applications requiring precise control of position, speed, and torque: Servomotors are ideal for applications where highly precise and dynamic control is needed, such as in industrial robots, CNC (computer numerical control) machinery, and automated manufacturing systems.
For example, in a robot performing assembly tasks, the servomotor enables smooth and controlled movements, adjusting speed and position in real-time to ensure accuracy in each task.
2. Systems requiring high speed and acceleration: They have the ability to reach high speeds and accelerations quickly and efficiently.
In applications such as high-speed printing presses or conveyor belts on production lines, servomotors allow rapid changes in speed without sacrificing accuracy or efficiency.
Situations where it is preferable to use a stepper motor
- Applications requiring incremental or low-cost positioning: Stepper motors are suitable for applications where simple, low-cost position control is required, such as 3D printers, plotters, or small automation devices. These motors allow precise motion control in incremental steps without the need for feedback sensors, which simplifies design and reduces costs.
- Applications with low to medium speed and constant torque: In situations where the speed is constant and the required torque does not vary significantly, such as in low-load linear positioning systems or labeling devices, stepper motors offer a simple and effective solution.
Cost and maintenance considerations
Evaluation of costs and maintenance needs between servomotors and stepper motors.
- Initial purchase cost: Are generally more expensive than stepper motors. This is mainly due to their more complex construction, which includes feedback devices (such as encoders) and more sophisticated control electronics. They have a simpler design, they are usually less expensive initially.
- Control system cost: Servo systems require more complex and expensive controllers due to their closed-loop nature. These controllers need to process feedback signals and make real-time adjustments. Controllers are simpler and less expensive, as they generally operate in open-loop systems.
- Installation cost: Servo systems often require more time and expertise to install and configure properly, which can increase installation costs. They are generally easier to install and configure, potentially reducing installation costs.
- Energy efficiency: Are generally more energy efficient, especially under varying load conditions. They consume only the energy required for the current load. They consume more energy, especially when holding a position, as they consume all the current even when not moving.
Conclusion
Servomotors, which provide extremely precise position and velocity control, are ideal for applications where accuracy and dynamic responsiveness are critical. Unlike stepper motors, which operate best in low to medium complexity applications and can dynamically adapt to load variations, making them particularly suitable for intensive and variable working environments.
Adaptability improves operational performance, and contributes to superior energy efficiency, It’s consume energy more optimally, avoiding overstress or underutilization. In addition, servomotors eliminate the need for additional components in the power transmission, such as gear reducers or gearboxes, which simplifies system design and reduces mechanical losses. This integrated approach reduces energy consumption and extends equipment life, reducing the need for frequent and costly maintenance.
Although they require a higher initial investment and more technical maintenance, their ability to provide precise control, adapt to varying load conditions, and operate with superior energy efficiency makes them the preferred choice for demanding applications requiring optimized long-term operation.
References
- https://www.linengineering.com/what-is-a-servo
- https://www.heidenhain.us/resources-and-news/servo-motors-for-cnc-machines/
- https://www.machinedesign.com/automation-iiot/article/21836868/stepper-and-servo-motor-tradeof
- https://www.a-m-c.com/the-university-outreach-program/
- https://labs.wsu.edu/robotics-and-automation/haptic-glove-with-servo-motors/