Table of Contents
A plant or maintenance shutdown is a period during which the plant is out of service, allowing maintenance tasks such as inspections, general repairs, replacements, machine redesigns (overhauls) to be carried out.
The Scope of Work for general maintenance in a refining or service plant shutdown in the industries: petrochemical, oil or gas, is the document where all the works to be carried out must be specified. In these industrial sectors, stops at regular intervals are common to carry out maintenance work, general repairs, substitutions, machine redesigns and new projects, in accordance with safety and environmental requirements.
The quality of this document will largely define the success of the Plant Shutdown and the established agreements.
With the content of this document, the planning, logistics, quantity and specifications of the materials, the strategies for purchasing materials and equipment, the necessary personnel, the machinery, the duration of the plant shutdown, are defined and proceeded. the critical path, and associated costs, among others.
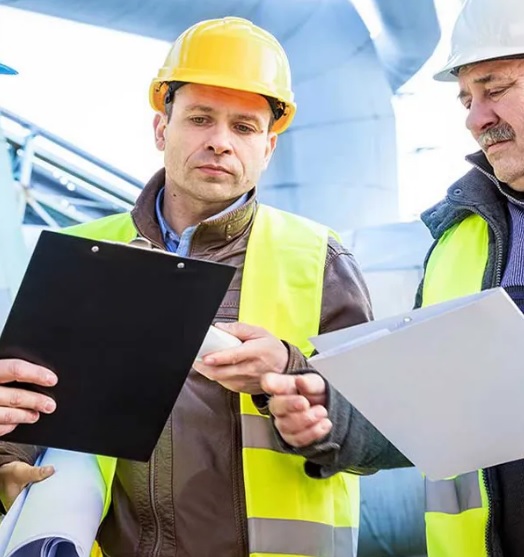
How to carry out a scope of work in a plant shutdown?
In order to achieve a good scope of work, in a plant shutdown, the recommendations generated during preventive or corrective maintenance, change management, recommendations from reinsurers, the inclusion of minor projectors, carefully review the post-mortem of the last stop.
The historical reports of the equipment, the technical notes generated after the last shutdown, the lessons learned and carry out a field evaluation of the current conditions of the equipment and piping of the plant or production unit.
The information collected in documentary and field research must be analyzed in detail by the responsible work team, in order to agree on the activities that must be included in the Scope of Work .
Finally, with the document already approved and the costs defined, a work execution strategy is submitted with its own resources or through contracting services. It is important to consider that, if necessary repairs to equipment or pipes are not included in the Scope of Work or in the planning, the consequences could be the following:
- Since the work was not included in the scope, it should not be executed: There is a risk of equipment or line failure during or after the start-up of the plant, with possible unwanted events, damage to facilities and people, unexpected stoppage of the plant, breach of commitment to customers, unforeseen expenses, loss of credibility in the work team and worst of all, possible fatalities.
- The work must be carried out even if it has not been included in the scope: This would give greater reliability to the facilities, but it would impact the work plan, unforeseen costs, changes in strategy and logistics, the possibility of non-availability of the necessary materials as well as the machinery and supplies required for the repair, extension of the stop execution time and possible breach of commitments with clients, among others.
In conclusion, to develop a scope of work of good quality, teamwork must be carried out, a thorough and detailed review of all associated documents and, additionally, interaction with plant operators, in order to have knowledge regarding provisional repairs to contain leaks due to broken pipes or equipment , which are not properly registered.
Finally, my experience in the field has allowed me to verify that the analyzes must be carried out in depth, and never superficially, no matter how simple it may seem, also not to rule out any suggestion and secondly, to keep professionally updated, by taking courses. , graduates, formal careers or self-taught development.