The fundamental role of blowers in boiler cleaning goes beyond the physical removal of deposits. These blowers are highly efficient and designed to ensure complete application to all heat transfer surfaces, including hard-to-reach areas and complex geometries. This is achieved through strategic positioning and maneuvering of the blower nozzles, often facilitated by advanced control and automation systems.
This article provides an analysis of the periodic cleaning of industrial boilers to remove accumulated deposits of soot, ash, and other particles from the internal surfaces of the equipment, through the use of soot blowers.
Most common types and problems in industrial boilers
What is a boiler?
Industrial boilers are devices with a wide range of applications, from power generation to industrial processes such as the manufacture of chemicals, textiles, and foodstuffs, among others. Their main function is to convert water into steam through the use of heat generated by the combustion of fossil fuels, biomass, or the use of electrical energy.
Types of industrial boilers
Depending on the relative position of the fluid to be heated and the combustion gases, boilers are classified as follows1:
Water-tube boilers: In these boilers, the fluid to be heated circulates inside the tubes, while the combustion gases circulate outside (figure 1a). They are used when high working pressures (> 22 bar) are required to heat small volumes of water. Thanks to the high velocity of the water, heat transfer is efficient, allowing a high steam production capacity.
Pyro-tubular: In this type, the combustion gases circulate inside the tubes, which are submerged in water (figure 1b). They are used when the working pressure is less than 22 bar, allowing large volumes of water to be heated and better adapting to fluctuations in steam demand.
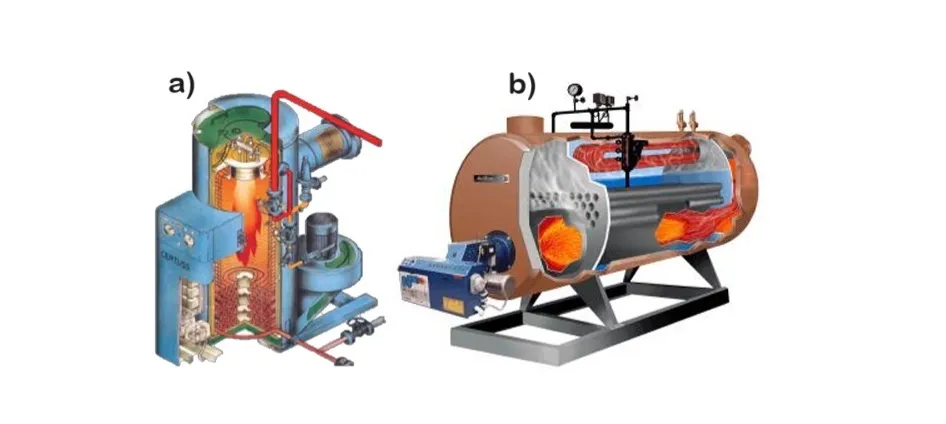
Industrial boilers operate with fuels: natural gas, oil, coal, biomass, and electric power. The choice of fuel and boiler construction materials depends on the specific application and operating conditions. Fossil fuels, such as natural gas and oil, are common due to their high efficiency and availability.
Common problems in industrial boilers
One of the most common problems in industrial boilers is the accumulation of residues, which can include ash, soot, and slag2. These residues are formed as by-products of fuel combustion and can be deposited on the internal surfaces of the boiler, affecting its performance and efficiency. The accumulation of residues has several negative effects: reduced thermal efficiency, increased fuel consumption, and safety risks. Debris acts as an insulator, decreasing heat transfer and increasing fuel consumption.
The accumulation of material deposits on the internal surfaces of steam-generating equipment, such as scale, sludge, and fouling agents, on the heat transfer surfaces of boilers (figure 2)2 can have detrimental consequences, such as overheating and accelerated corrosion rates. These conditions often lead to unplanned shutdowns, resulting in significant economic losses and productivity interruptions.
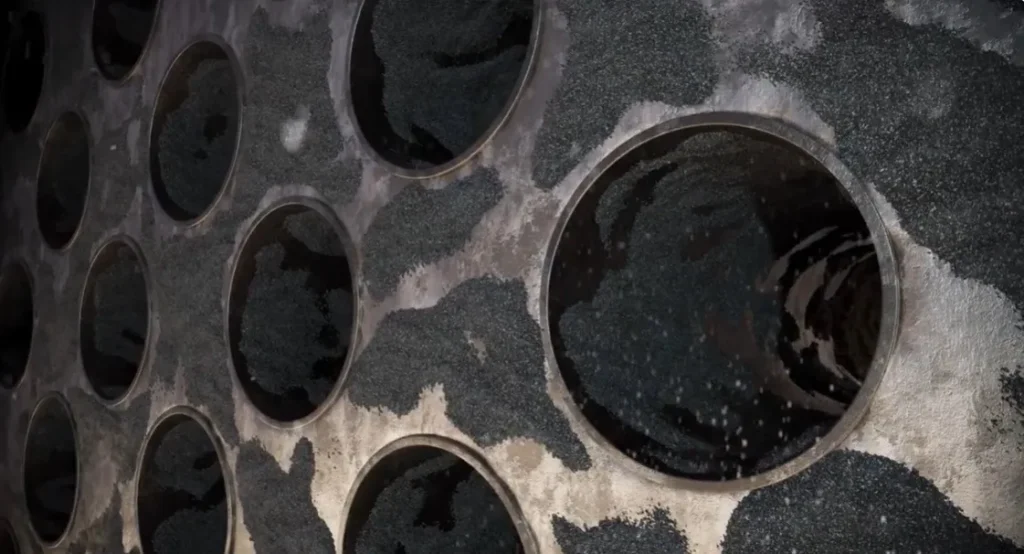
In order to maintain boilers in optimal conditions, it is necessary to carry out regular cleaning operations to remove deposits of ash and soot from combustion. The deposits are separated from the gases along the entire boiler circuit and adhere to the heat exchange surface, impeding heat transfer and progressively obstructing the gas passage sections.
In this context, soot blowers are devices that allow cleaning efficiently with steam or compressed air, while the boiler is in operation, the surfaces of the pipes by removing dry ash and soot deposits. They also remove incrustations from the stagnation areas.
What is a soot blower?
A soot blower is a device for removing soot that is deposited on the furnace tubes of a boiler during combustion. Soot build-up can reduce efficiency and present a fire hazard. Short gasket life is the main cause of failure.
The main function of blowers in boiler cleaning is to generate and deliver high-velocity jets of a cleaning medium, usually air, steam, or a combination of both, through a network of strategically placed nozzles. These high-pressure jets impinge on dirty surfaces, dislodging and removing adhering deposits through a process known as soot blowing.
Effective control and monitoring of key boiler components and associated parameters are essential to ensure safe, reliable, and efficient boiler operation while meeting regulatory requirements and minimizing environmental impact.
Compared to other precipitation reactions, such as calcium phosphate formation, scale crystallization is a slower process. This results in the formation of well-defined crystals and the accumulation of a hard, dense, and highly insulating material on the metal surface of the pipes. Some forms of scale are extremely persistent, resisting both mechanical and chemical removal methods.
Sludge refers to the accumulation of solids that precipitate in the boiler water or enter the boiler water as suspended solids. These sludge deposits can be hard, dense, and tough. When exposed to high temperatures, such as during draining of a hot boiler, sludge deposits often burn in situ. Sludge deposits hardened in this way can be as problematic as scale.
Below is a video explaining the operation of soot blowers. Courtesy of Aerovit.

How do soot blowers work?
Blowers in boiler cleaning of industrial
Industrial boiler cleaning involves the removal of deposits adhering to the internal surfaces of the boiler, such as the tubes, combustion chamber, and economizer. While conventional approaches involve manual, chemical cleaning methods, these can be labor-intensive, time-consuming, and pose risks to workers. In contrast, advanced blower systems provide a highly efficient, automated solution for boiler cleaning, thereby improving process safety and efficiency.
Soot blowers are essential components in boiler systems, particularly in coal-fired power plants and industrial boilers. They are designed to remove soot, ash, and other particulate build-up from heat transfer surfaces within the boiler, such as superheater, reheater, and economizer tubes.
To evaluate the effectiveness of the blowdown, steam can be directed towards an impingement plate in the main steam line. This technique is especially common in high-pressure boilers that generate superheated steam to drive turbines. Successive steam blows are applied until erosion caused by solid particles on the impingement plate is no longer visible. The duration of the blowing process varies but is generally about 24 hours unless chemical cleaning has been carried out beforehand, which can considerably reduce the blowing time required.
Improving operating efficiency with soot blowers
Soot acts as a thermal insulator, increasing the amount of energy required for boilers to reach their optimum operating temperature. As mentioned above, soot build-up internally increases energy consumption, generating high costs that no company wants to bear.
The fuels that feed the boilers produce various by-products that coat the heating surfaces, including soot, ash, and slag. These residues can deposit on walls, screens, and superheaters, decreasing energy efficiency and increasing operational risks. Soot blowers are essential tools for maintaining energy efficiency and ensuring safe operation.
As with any rotating equipment, effective sealing of soot blowers is critical. Leakage of flue gases and particulates from the boiler cavity can create occupational and safety hazards. Implementing an effective mechanical sealing system can reduce the maintenance required and ensure safe operation.
Conclusions
Maintaining a boiler cleaning routine is significant for optimizing the performance and prolonging the life of boiler systems in power plants. Ash accumulation and the formation of slag deposits inside boilers decrease operating efficiency, as they act as insulators that reduce heat transfer, forcing more fuel to be used to maintain the same energy output. This problem increases operating costs and increases emissions, which generates more environmental pollution.
Off-line cleaning, while requiring a scheduled plant shutdown, can be more thorough and allows for additional boiler servicing and maintenance. On the other hand, on-line cleaning offers the advantage of not interrupting plant operation, which is crucial for maintaining continuity of power supply.
References
- https://m.riunet.upv.es/bitstream/handle/10251/104064/Barrera%3BBetoret%3BCastell%C3%B3%20-%20Aspectos%20b%C3%A1sicos%20relacionados%20con%20el%20funcionamiento%20de%20una%20caldera.pdf?sequence=1&isAllowed=y#:~:text=El%20principio%20b%C3%A1sico%20del%20funcionamiento,a%20los%20puntos%20de%20consumo.
- https://www.aerovit.dk/es/productos/soplador-de-hollin-aerovit/