Table of Contents
- Introduction
- API RP 581: Risk-based inspection methodology
- Industrial robotic inspections
- Advantages of using robotics in the API RP 581 inspection methodology
- Innovation in inspection based on API RP 581 through robotics
- Improvements in the security of API RP 581 inspection with robotics
- Conclusion
- References
Introduction
The integration of robotics into the API RP 581 inspection methodology has improved the way inspections are performed, providing a series of technological advances and improvements in safety, efficiency, coverage and the quality of inspection data, which has led to more accurate and reliable assessments of equipment integrity. This recommended practice provides a quantitative framework for establishing risk-based inspection programs for static equipment such as pressure vessels, storage tanks, and process lines.
The arrival of robotic solutions in this field has positively altered the landscape, offering improved capabilities that align with the principles of Risk Based Inspection (RBI) under the criteria of this standard. In this article we will learn about the improvements of this transformation, highlighting the advantages, innovations and technological advances in robotic inspection.
API RP 581: Risk-based inspection methodology
This API Standard RP 581 provides guidelines for developing and managing risk-based inspections, specifically linked to the oil, gas and petrochemical industrial sectors. In the RBI methodology, risk is obtained by calculating the probability of failure (PoF) and the consequences of failure (CoF). The first is a computation that determines the probability that the equipment will fail at a defined time and the second classifies the severity of the consequences of that failure occurring. Risk metrics are determined through qualitative and quantitative data analysis.
This approach establishes guidelines for the development and supervision of risk-based inspections, in accordance with API Recommended Practice RP 580.
The following video is presented below, in order to reinforce the information contained in this article.
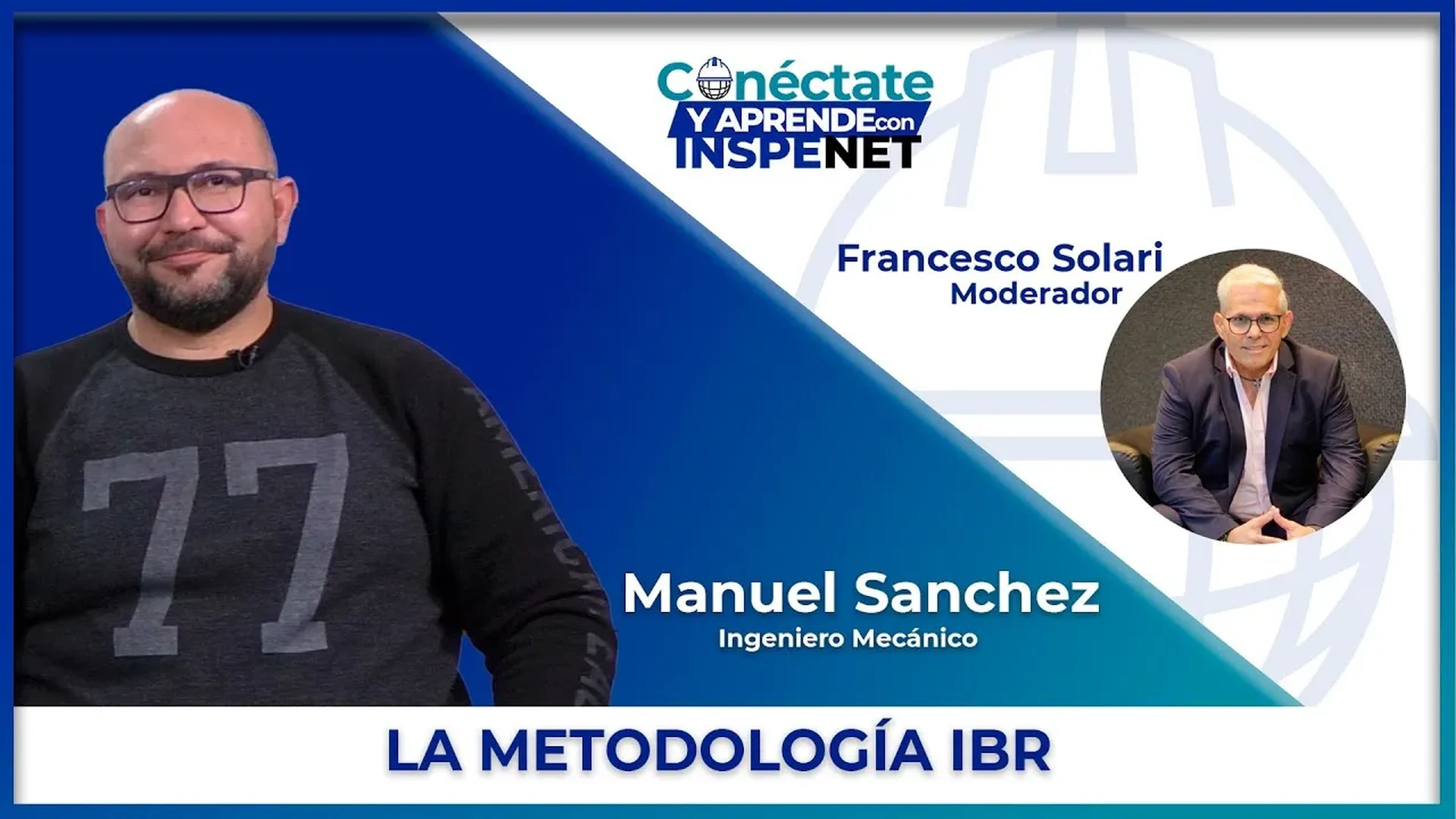
Video courtesy of Inspenet’s “Connect and Learn” program.
A fundamental aspect of an efficient RBI program lies in its consistency and repeatability. These programs are aimed at reducing risks through the implementation of inspection and management strategies that offer high reliability, which is influenced by factors, such as Non-Destructive Testing (NDE) methods used and the extent of inspection coverage. ; which help define confidence levels and evaluate how effective the program is in reducing risks associated with certain damage mechanisms and asset types.
With the results obtained through this methodology, the teams with the highest risks are prioritized, so that organizations allocate resources effectively and address the most critical problems first to mitigate potential dangers. This methodology not only takes into account the current condition of the equipment and its operating history, but also delves into the evaluation of the effectiveness of previously carried out inspections to improve risk management through periodic evaluations.
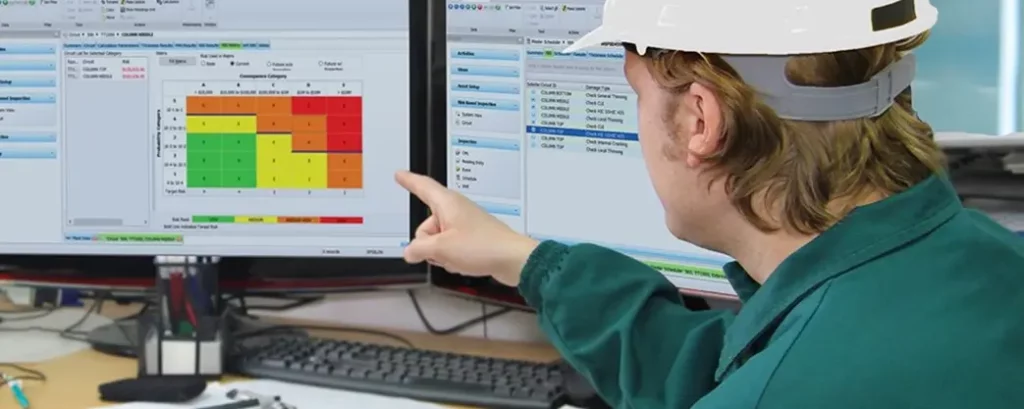
Industrial robotic inspections
These types of inspections refer to the use of intelligent electromechanical machines, designed to operate in mostly high-risk industrial environments, which carry out inspection and maintenance work. These robots, equipped with advanced sensors and vision systems, are capable of detecting defects, performing precise measurements, and ensuring the integrity of the components being evaluated. The maximum deployment of these cutting-edge technologies improves inspections.
The mechatronic design of this equipment allows for efficient operations that maximize accuracy and data collection during inspection periods. Currently, advances in electromechanical hardware and software are experiencing rapid growth in the field of robotics. These advances have led to innovations in the design and construction of robots, offering more practical solutions in various industrial sectors.
Currently, developments in robotic technology focus on machines that can definitively replace humans during inspections in hazardous environments. Robots are taking on the tasks of performing inspections at height, confined spaces, repetitive tasks, and places where you cannot survive for long periods (such as space, underwater, near hazardous materials).
Advantages of using robotics in the API RP 581 inspection methodology
Technological advances in inspection for industrial equipment in the oil and gas, and petrochemical sectors, have greatly contributed to the use of robotics in the API RP 581 inspection methodology; offering benefits that improve the reliability and efficiency of processes, including:
- Access and mobility: Robots are able to access and maneuver environments or assets that are not periodically inspected because they represent a challenge for human inspectors, such as confined spaces, heights, underwater inspections and tank bottoms in service. This improved accessibility leads to obtaining a more complete set of inspection data, ensuring a more specific inspection that adheres to the compliance standards of this API methodology.
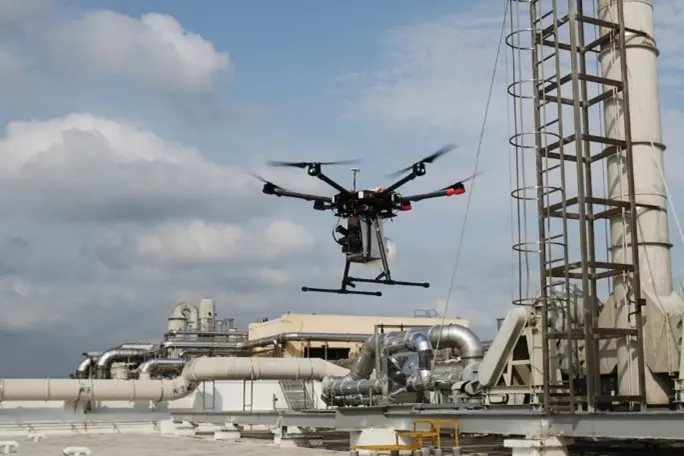
- Data density and quality: Robotic inspections improve the precision of evaluations, due to the density of data that can be obtained with high quality; which are used to identify and quantify a wide variety of damage mechanisms such as corrosion, wall thickness and deformations, which require the integrity of the equipment. This information is integrated with risk-based inspection software platforms and translates the data into current and predictive information that enables the development of an effective inspection program, including inspection methods, timing and coverage.
- Greater coverage and efficiency: Robotic technologies allow large areas to be inspected quickly and accurately. Having the ability to inspect large assets or serial assets provides an accurate view of asset conditions, providing greater levels of confidence.
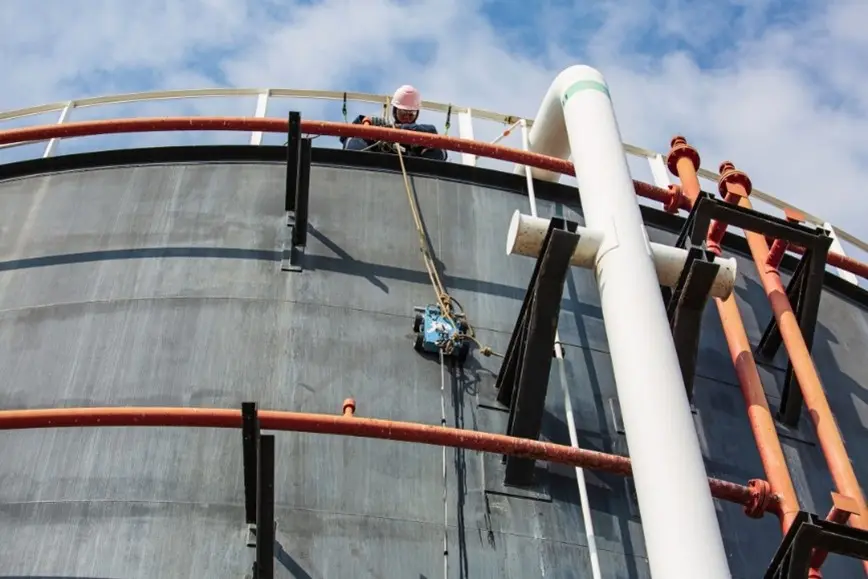
- Reproducibility and repeatability: The use of robotics ensures that inspections are repeatable, as robots can start and end scanning at the same locations. This leads to reproducible data that can be compared over time to monitor damage progression; a fundamental aspect to improve the general inspection risk assessment process in accordance with API 581 recommended practice.
The RBI methodology of API RP 581, benefited from the use of advanced robotic tools for its inspections, is a more effective management to guarantee the integrity and reliability of industrial equipment. By improving the effectiveness of inspections and, therefore, the accuracy of failure probability calculations, organizations generate optimized inspection and maintenance plans.
Innovation in inspection based on API RP 581 through robotics
Robotic innovation has marked an era regarding the ease of executing and processing industrial inspections, which are surpassing traditional methods in several factors:
- Advanced Sensing Technologies: Robotic systems equipped with state-of-the-art sensors and data acquisition tools offer an accurate view of asset conditions, aligning with RBI methodology requirements for data analysis and reporting.
- Automated data processing: Integrating robotics with risk-based inspection enables automatic processing and analysis of inspection data, streamlining the RBI process and improving decision-making capabilities for inspection and maintenance plans. that can be generated.
- High resolution imaging: Advanced imaging technologies used in robotic inspections provide detailed visualizations of asset conditions, detecting any anomalies or defects that provide greater precision in the collection of data used during API RP risk-based inspection 581.
- Machine learning and artificial intelligence: These algorithms in conjunction with robotics allow to extend the processing capabilities of data collected during inspections for the application of risk-based inspection by identifying patterns and predicting potential failures that can be prevented.
Optimization of RBI inspections using robotics and artificial intelligence
The incorporation of advanced robotic technologies along with artificial intelligence is transforming industrial inspection methodologies under the RBI approach defined by API RP 581. These advances enable more accurate data collection, automated data processing and more reliable predictive reporting, which improves maintenance, operational safety and long-term asset management decision making.
Companies like Gecko Robotics develop innovative solutions such as AIR (Artificial Intelligence + Robotics) technology and the Cantilever® platform, which integrate high-fidelity sensors with artificial intelligence algorithms. These tools allow to comprehensively assess the integrity of equipment, identify failure patterns and generate actionable information for immediate and strategic planning, optimizing resources and extending the life of industrial assets.
Improvements in the security of API RP 581 inspection with robotics
Robotics has significantly improved the safety aspects of API RP 581 Risk-Based Inspection. Remote monitoring and diagnosis capability, by using devices equipped with advanced technologies, inspections can be monitored and analyzed in real time from remote and secure locations, reducing the direct physical involvement of inspectors in high-risk areas. Remote monitoring and diagnosis simplifies industrial safety management, contributing to the creation of safer work environments.
Conclusion
Robotic inspections have a significant impact on the effectiveness and manner of applying the RBI methodology processes described in API RP 581. Regular monitoring of equipment will lead to a reduction in technical failures. This type of inspection provides complete data, allowing accurate identification and quantification of damage through greater coverage, data density, and secure access to risk areas. Consequently, this improves inspection confidence and the accuracy of probability of failure (PoF) calculations, meeting the requirements of the API RP 581 standard.
The integration of these technologies in RBI programs under the API RP 581 standard is increasingly common because it requires risk assessments, which leads to planning and implementing the best maintenance strategies for the benefit of efficient asset management. The future of inspections in various industries is destined to be increasingly influenced by these technological innovations, because it allows for more frequent and thorough inspections without increasing the risk to personnel, providing improvements in safety.