Introduction
In the complex industrial structure, where efficiency is an important aspect, reliability indicators represent essential elements for the optimal management of the operation and maintenance of industrial facilities. They measure the effectiveness of equipment performance and efficiency in maintenance management, assessing critical factors that underpin the organization’s ongoing success.
Through its implementation, these organizations will be able to count on a well-meshed and balanced system, building the basis for optimal performance. In this article, we will explore how these indicators not only measure, but also model the path to maintenance management that goes beyond the tool and becomes a vibrant system of industrial excellence.
What are reliability indicators?
Reliability indicators are crucial parameters in industrial maintenance management, being a key measure of the confidence placed in a company’s equipment and machinery. This term, essential to business viability in the age of globalization, refers to the probability that a system or equipment will operate without loss of function for a given period of time1.
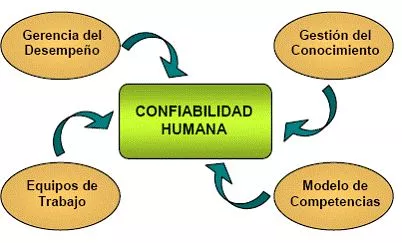
Reliability is broken down into four fundamental sources: human, process, equipment and design reliability. These indicators, in turn, make it possible to evaluate the operational performance of facilities, systems and components, providing the ability to implement specific plans aimed at improving maintenance operations. In essence, reliability indicators act as strategic parameters, providing fundamental insights to ensure the continuous and efficient performance of industrial resources.
What are the reliability indicators?
Average Time to Failure (TPPF)
Also known as “Mean Operating Time” or “Mean Time to Failure”, it is a fundamental indicator in the measurement of reliability and in the analysis of optimum asset performance. This indicator quantifies the average time during which a piece of equipment operates at its maximum capacity without experiencing interruptions within a specific period2, serving as an indirect reflection of system reliability.
In the field of maintenance, the TPPF is closely linked to other indicators, standing out as one of the most relevant indicators for assessing the reliability of repairable equipment. For this reason, maximizing the TPPF becomes a fundamental objective, since it implies reducing the frequency of failures and extending the useful life of the assets. A high TPPF indicates that the assets are highly reliable and have a lower probability of failure.
Among the essential practices for the improvement of the TPPF are preventive and predictive maintenance programs, regular inspections, records of maintenance activities, and the use of different monitoring techniques. Each of these practices can contribute to the optimal performance of industrial assets.
Time To Repair Average (TPPR)
This indicator evaluates the distribution of the time taken to restore an equipment or system to optimal operating conditions after a failure, within a given period of time3. Intrinsically linked to maintainability, it defines the probability of restoring a piece of equipment to operating condition within a specified time using prescribed procedures, TPPR reflects the effective execution of maintenance.
TPPR, being a measure associated with the ease of restoring damaged equipment, is fundamental in asset management, thanks to its ability to reveal the average time required to repair an asset post-failure. Its importance lies in minimizing downtime and optimizing repairs, indicating efficiency when TPPR is low, ensuring prompt reactivation of assets. TPPR improvement involves accurate planning, trained technical personnel and timely access to tools and spare parts.
Mean Time Between Failures (MTBF)
It is an essential component of reliability indicators for optimal performance, measurement and analysis of reliability for optimal performance, standing out as one of the most significant indicators in the field of industrial maintenance. This indicator quantifies the total mean time between each repairable equipment failure, providing an optimal tool for evaluating machinery.
By measuring the total uptime between failures, TMEF functions as an optimal tool for efficient asset management, allowing targeted interventions on each individual piece of equipment. A high TMEF indicates higher reliability and reduced failure frequency, thus contributing to the optimal performance of industrial assets.
To enhance the TMEF, it is imperative to identify the causes of equipment failures and then implement corrective and preventive actions4; additionally, it is of great importance to use quality spare parts.
Failure analysis is also highly relevant, as it provides insight into patterns and trends that could affect the asset’s performance. Efficient management of this indicator, applying it individually to each piece of equipment, facilitates specific interventions, thus optimizing maintenance strategies.
Backlog
The backlog comprises the accumulation of pending work, including preventive, corrective and predictive maintenance tasks that have not yet been completed, representing a challenge to operational efficiency. A high backlog can cause delays in critical tasks and extend response times to unforeseen failures or emergencies.
Reducing the backlog is essential to improve maintenance efficiency and ensure the availability of resources for critical activities. Effective backlog management involves setting priorities, allocating resources appropriately and employing scheduling and tracking tools. In addition, there is a need to improve communication and coordination processes within the maintenance department.
In summary, the backlog is translated as the “maintenance backlog“5 , being the time required to execute specific maintenance actions, such as corrective, preventive or predictive maintenance, quality inspections, improvements, among others, directly influencing the operability and reliability of the assets.
Availability and reliability
The availability of a piece of equipment consists of its capacity to be operational at a given time or during a specific interval4. This indicator is calculated considering other reliability indicators such as TPPF and TPPR, providing management with an overall view of the time in which the equipment can be expected to perform its designated function.
The efficient management of availability allows the evaluation of strategic alternatives to increase it, becoming an essential component in Maintenance Planning and Control (PCM). Optimizing availability is critical to ensure optimal performance and sustainable asset productivity.
On the other hand, the reliability of equipment refers to the probability that it will perform its function under specific conditions in a given period of time4. Reliability analysis for optimal performance, which examines equipment failures, can provide valuable information, including probability of failure, average time to failure and equipment life stage. A team that is one hundred percent reliable is one that has a survival probability equal to one.
Reliability, as a reliability measurement method, is evaluated through standards such as NBR 5462, being essential for Maintenance Planning and Control, which aims to ensure and improve the optimal performance of equipment, supporting operational efficiency and asset integrity.
Why are reliability indicators so important?
In the industrial environment, reliability indicators for optimum performance are essential elements that play a crucial role in the effective management of operations. These indicators allow to know the reliability index of the assets, having an impact on the management of industrial organizations through several benefits.
First, reliability indicators allow for a comprehensive assessment of asset performance and maintenance processes4. In other words, they provide objective data on the operating efficiency, availability, downtime and reliability of the equipment. With this degree of information, areas for improvement can be identified and corrective actions can be implemented to maximize overall maintenance performance.
In addition, these indicators facilitate data-driven decision making by providing clear and measurable metrics. Managers and supervisors can use this quantitative data to identify trends, compare performance against established objectives and make informed decisions. This not only prioritizes maintenance actions, but also allows for efficient resource allocation and optimization of maintenance processes.
Conclusions
Reliability indicators are the cornerstone of continuous improvement in industrial integrity. Constantly monitoring and measuring asset performance through these key indicators allows organizations to identify areas for improvement and optimization opportunities in the operations carried out.
However, achieving this will require the implementation of improvement strategies, such as the adoption of best practices, the development of predictive and preventive maintenance programs, as well as the training of personnel in new technologies and advanced maintenance techniques. In summary, reliability indicators are indispensable tools for achieving optimal and sustainable performance of industries.
References
- MINT. (2022, October 13). Reliability in industrial maintenance. Retrieved February 5, 2024, from https://mintforpeople.com/noticias/confiabilidad-mantenimiento-industrial/#%C2%BFQue_es_la_confiabilidad_en_el_mantenimiento_industrial.
- BSG Institute. (n.d.). Reliability Indicators Drivers in Maintenance Management. Retrieved February 5, 2024, from https://bsginstitute.com/bs-campus/blog/Indicadores-de-Confiabilidad-en-Mantenimiento-94.
- TRACTIAN. (sf). 8 maintenance indicators for asset management. Retrieved February 5, 2024, from https://tractian.com/es/blog/8-indicadores-indispensables-para-la-gestion-del-mantenimiento.
- Fracttal. (n.d.). 5 key indicators in the maintenance department. Retrieved February 5, 2024, from https://www.fracttal.com/es/guias-mantenimiento/indicadores-de-mantenimiento.
- Infraspeak. (2023, March 23). Maintenance indicators: 7 KPIs for effective management. Retrieved February 6, 2024, from https://blog.infraspeak.com/es/indicadores-de-mantenimiento/.