Introducción
En la compleja estructura industrial, donde la eficiencia es un aspecto importante, los indicadores de confiabilidad representan elementos esenciales para la gestión óptima del funcionamiento y mantenimiento de las instalaciones industriales. Miden la efectividad del desempeño de los equipos y la eficiencia en la gestión de mantenimiento, evaluando factores críticos que sustentan el éxito continuo de la organización.
Por medio de su implementación, estas organizaciones podrán contar con un sistema bien engranado y equilibrado, construyendo la base para un rendimiento óptimo. En este artículo, exploraremos cómo estos indicadores no solo miden, sino que también modelan el camino hacia una gestión de mantenimiento que va más allá de la herramienta y se convierte en un sistema vibrante de excelencia industrial.
¿Qué son los indicadores de confiabilidad?
Los indicadores de confiabilidad constituyen parámetros cruciales en la gestión del mantenimiento industrial, siendo una medida clave de la confianza depositada en los equipos y maquinaria de una empresa. Este término, esencial en la viabilidad empresarial en la era de la globalización, se refiere a la probabilidad de que un sistema o equipo opere sin pérdida de función durante un periodo determinado1.
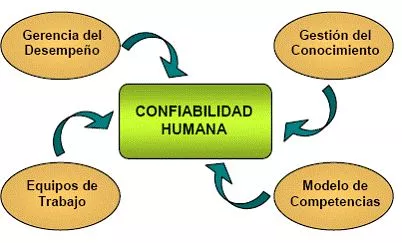
La confiabilidad se desglosa en cuatro fuentes fundamentales: la confiabilidad humana, de procesos, de equipos y de diseño. Estos indicadores, a su vez, permiten evaluar el comportamiento operacional de instalaciones, sistemas y componentes, brindando la capacidad de implementar planes específicos destinados a perfeccionar las operaciones de mantenimiento. En esencia, los indicadores de confiabilidad actúan como parámetros estratégicos, proporcionando insights fundamentales para garantizar el rendimiento continuo y eficiente de los recursos industriales.
¿Cuáles son los indicadores de confiabilidad?
Tiempo Promedio para Fallar (TPPF)
También conocido como “Tiempo Promedio Operativo” o “Tiempo Promedio hasta la Falla”, constituye un indicador fundamental en la medición de confiabilidad y en el análisis del rendimiento óptimo de los activos. Este indicador cuantifica el tiempo promedio durante el cual un equipo opera a su máxima capacidad sin experimentar interrupciones dentro de un periodo específico2, sirviendo como un reflejo indirecto de la confiabilidad del sistema.
En el ámbito del mantenimiento, el TPPF se vincula estrechamente con otros indicadores, destacándose como uno de los indicadores más relevantes para evaluar la confiabilidad de equipos reparables. Por tal razón, la maximización del TPPF se convierte en un objetivo fundamental, ya que implica la reducción de la frecuencia de fallas y la prolongación de la vida útil de los activos. Un TPPF elevado señala que los activos son altamente confiables y tienen una menor probabilidad de sufrir fallos.
Entre las prácticas esenciales para el mejoramiento del TPPF, se encuentran los programas de mantenimiento preventivo y predictivo, las inspecciones regulares, los registros de actividades de mantenimiento, y el empleo de diferentes técnicas de monitoreo. Cada una de estas prácticas puede contribuir al rendimiento óptimo de los activos industriales.
Tiempo Promedio para Reparar (TPPR)
Este indicador evalúa la distribución del tiempo empleado para restaurar un equipo o sistema a condiciones operativas óptimas tras una falla, dentro de un lapso determinado3. Intrínsecamente vinculado a la mantenibilidad, define la probabilidad de restituir un equipo a condiciones operativas en un tiempo específico mediante procedimientos prescritos, el TPPR refleja la ejecución efectiva del mantenimiento.
El TPPR, siendo una medida asociada a la facilidad de restablecer equipos perjudicados, es fundamental en la gestión de activos, gracias a su capacidad de revelar el tiempo promedio necesario para reparar un activo post-falla. Su importancia radica en la minimización del tiempo de inactividad y la optimización de las reparaciones, indicando eficiencia cuando el TPPR es bajo, asegurando la pronta reactivación de los activos. La mejora del TPPR implica una planificación precisa, personal técnico capacitado y acceso oportuno a herramientas y repuestos.
Tiempo Medio Entre Fallos (TMEF)
Se trata de un integrante esencial de los indicadores de confiabilidad para rendimiento óptimo, la medición y el análisis de confiabilidad para el rendimiento óptimo, destacando como uno de los indicadores más significativos en el ámbito del mantenimiento industrial. Este indicador cuantifica el tiempo total medio de buen funcionamiento entre cada fallo en un equipo reparable, proporcionando una herramienta óptima para evaluar maquinarias.
Al medir el tiempo total de buen funcionamiento entre cada fallo, el TMEF funciona como una herramienta óptima para la gestión eficiente de activos, permitiendo intervenciones focalizadas en cada equipo de manera individual. Un TMEF elevado indica una mayor confiabilidad y una frecuencia de fallas reducida, contribuyendo así al rendimiento óptimo de los activos industriales.
Para potenciar el TMEF, es imperativo identificar las causas de las fallas que presentan los equipos para luego implementar acciones correctivas y preventivas4; adicionalmente, es de gran importancia el utilizar repuestos de calidad.
Los análisis de fallas también poseen una alta relevancia, debido a que por medio de ellos se pueden comprender los patrones y tendencias que podrían afectar el desempeño del activo. La administración eficiente de este indicador, aplicándolo individualmente a cada equipo, facilita intervenciones específicas, optimizando así las estrategias de mantenimiento.
Backlog
El Backlog comprende la acumulación de trabajo pendiente, abarcando tareas de mantenimiento preventivo, correctivo y predictivo que aún no han sido completadas, representando un desafío para la eficiencia operativa. Un Backlog elevado puede generar demoras en tareas críticas y extender los tiempos de respuesta ante fallas o emergencias imprevistas.
Reducir el Backlog es esencial para mejorar la eficiencia del mantenimiento y asegurar la disponibilidad de recursos para actividades fundamentales. La gestión efectiva del Backlog implica establecer prioridades, asignar recursos de manera adecuada y emplear herramientas de programación y seguimiento. Además, se requiere mejorar los procesos de comunicación y coordinación dentro del departamento de mantenimiento.
En resumen, el Backlog se traduce como el “retraso en el mantenimiento”5, siendo el tiempo necesario para ejecutar acciones específicas de mantenimiento, como correctivo, preventivo o predictivo, inspecciones de calidad, mejoras, entre otras, influyendo directamente en la operatividad y confiabilidad de los activos.
Disponibilidad y confiabilidad
La disponibilidad de un equipo consiste en su capacidad de estar operativo en un instante dado o durante un intervalo específico4. Este indicador se calcula considerando otros indicadores de confiabilidad como TPPF y TPPR, proporcionando a la gerencia una visión global del tiempo en el que se puede esperar que el equipo cumpla su función designada.
La eficiente gestión de la disponibilidad permite evaluar alternativas estratégicas para aumentarla, convirtiéndose en un componente esencial en el Planeamiento y Control del Mantenimiento (PCM). La optimización de la disponibilidad es fundamental para garantizar un rendimiento óptimo y una productividad sostenible de los activos.
Por otro lado, la confiabilidad de un equipo se refiere a la probabilidad de que cumpla su función bajo condiciones específicas en un periodo determinado4. El análisis de confiabilidad para el rendimiento óptimo, que examina los fallos de un equipo, puede proporcionar información valiosa, incluyendo la probabilidad de fallo, tiempo promedio para fallo y la fase de la vida útil del equipo. Un equipo que es ciento por ciento confiable es aquel que tiene una probabilidad de supervivencia igual a uno.
La confiabilidad, como un método de medición de confiabilidad, es evaluada mediante normativas como la NBR 5462, siendo esencial para el Planeamiento y Control del Mantenimiento, que tiene como objetivo garantizar y mejorar el desempeño óptimo de los equipos, respaldando la eficiencia operativa y la integridad de los activos.
¿Por qué son tan importantes los indicadores de confiabilidad?
En el ámbito industrial, los indicadores de confiabilidad para rendimiento óptimo son elementos esenciales que desempeñan un papel crucial en la gestión efectiva de las operaciones. Estos indicadores permiten conocer el índice de confiabilidad de los activos, llegando a impactar la gestión de organizaciones industriales a través de diversos beneficios.
En primer lugar, los indicadores de confiabilidad permiten una evaluación exhaustiva del rendimiento de los activos y los procesos de mantenimiento4. Es decir, proporcionan datos objetivos sobre la eficiencia operativa, la disponibilidad, su inactividad y la confiabilidad de los equipos. Con este grado de información, se pueden identificar áreas de mejora y aplicar medidas correctivas que maximicen el rendimiento general del mantenimiento.
Además, estos indicadores facilitan la toma de decisiones basadas en datos al ofrecer métricas claras y medibles. Los gerentes y supervisores pueden utilizar estos datos cuantitativos para identificar tendencias, comparar el desempeño con objetivos establecidos y tomar decisiones fundamentadas. Esto no solo prioriza acciones de mantenimiento, sino que también permite asignar recursos de manera eficiente y optimizar los procesos de mantenimiento.
Conclusiones
Los indicadores de confiabilidad son la piedra angular de la mejora continua en la integridad industrial. El monitorear y medir constantemente el desempeño de los activos a través de estos indicadores clave permite a las organizaciones identificar áreas de mejora y oportunidades de optimización en las operaciones llevadas a cabo.
No obstante, para conseguirlo será necesaria la implementación de estrategias de mejora, como la adopción de mejores prácticas, el desarrollo de programas de mantenimiento predictivo y preventivo, así como la capacitación del personal en nuevas tecnologías y técnicas avanzadas de mantenimiento. En resumen, los indicadores de confiabilidad son herramientas indispensables para alcanzar un rendimiento óptimo y sostenible de las industrias.
Referencias
- MINT. (2022, 13 de octubre). La confiabilidad en el mantenimiento industrial. Consultado el 5 de febrero de 2024, de https://mintforpeople.com/noticias/confiabilidad-mantenimiento-industrial/#%C2%BFQue_es_la_confiabilidad_en_el_mantenimiento_industrial
- BSG Institute. (s.f.). Indicadores de Confiabilidad Propulsores en la Gestión del Mantenimiento. Consultado el 5 de febrero de 2024, de https://bsginstitute.com/bs-campus/blog/Indicadores-de-Confiabilidad-en-Mantenimiento-94
- TRACTIAN. (s.f.). 8 indicadores de mantenimiento para la gestión de activos. Consultado el 5 de febrero de 2024, de https://tractian.com/es/blog/8-indicadores-indispensables-para-la-gestion-del-mantenimiento
- Fracttal. (s.f.). 5 indicadores clave en el departamento de mantenimiento. Consultado el 5 de febrero de 2024, de https://www.fracttal.com/es/guias-mantenimiento/indicadores-de-mantenimiento
- Infraspeak. (2023, 23 de marzo). Indicadores de mantenimiento: 7 KPIs para una gestión eficaz. Consultado el 6 de febrero de 2024, de https://blog.infraspeak.com/es/indicadores-de-mantenimiento/