Introduction
Asset management includes the maintenance of equipment and systems in order to prevent failures and maintain operational continuity; or solve failures that require repair such as: problems in components, equipment or systems. Reliability is the result of effective sustainment or control, which measures the ability of a physical asset to perform as intended over a given period.
When we face operational problems, maintenance becomes the indispensable tool to solve and repair these difficulties. In contrast, reliability is directed at the effective functionality of the equipment, establishing its operation without setbacks. These two pillars come together to maintain the integrity of the assets and guarantee optimal performance over time.
However, in combination, the different technologies provide a powerful set of capabilities to obtain a comprehensive view of the health of industrial assets and production facilities.
What is maintenance?
It refers to the actions carried out to preserve or restore an element, equipment or infrastructure, so that it maintains proper functioning. Its proper implementation leads to longer asset life, lower frequency of failures, and safer and more efficient operation.
Adequate program planning, including schedules and monitoring techniques using specialized software, is necessary to avoid costly process interruptions.
These methodologies are effective in maximizing the performance and extending the useful life of equipment or facilities; detecting problems eliminates safety risks and hazards, improves equipment operability and ensures process efficiency.
Main types of maintenance
Maintenance management has evolved and proven its ability to help maintenance managers provide better optimization of the production plant at a lower cost.
A reliability-focused maintenance strategy employs reactive, preventive, predictive and proactive maintenance techniques in an integrated manner to increase the reliability in which a machine will operate consistently over a life cycle, (see diagram), providing a roadmap. to analyze and act on the root causes of equipment failures in search of greater asset reliability.
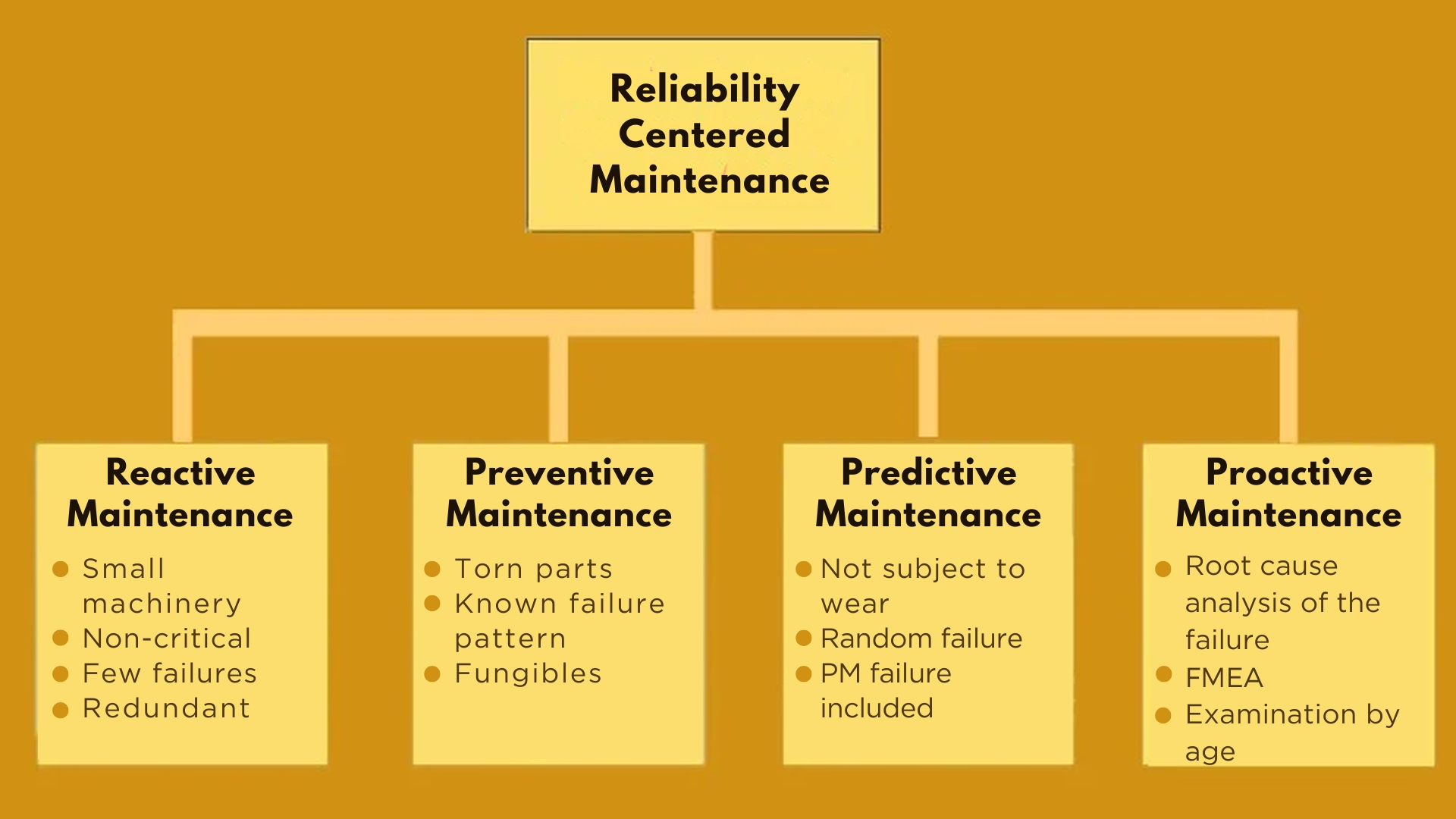
The integration of various techniques is necessary, since none of these, by itself, is sufficient to accurately understand the problems associated with more complex equipment.
Naturally, disruption to operations is inevitable when dealing with a wide variety of components, and solutions can often be challenging. However, leading companies implement RCM (Reliability Centered Maintenance) to prevent unexpected failures that lead to complicated maintenance, costly outsourcing, and lost production time.
Below are the main types used in the different industrial sectors:
- Corrective Maintenance (RM): It is carried out after an asset has failed and its objective is to restore the operability and functionality of the affected unit. It can be planned or unplanned. It is commonly applied to equipment that is not very expensive to replace or that does not pose a threat to operational continuity. Although it is essential for solving unforeseen problems, organizations often seek to balance it with preventive and predictive practices to reduce the frequency and severity of failures.
- Preventive Maintenance (PM): Refers to regularly performed and planned practices to maintain equipment, machines or systems in good condition. The main objective is to prevent failures or breakdowns in time. Some of its key features include: planning and scheduling, regular inspections, lubrication, replacement of worn components and calibrations. Due to its importance, it is a main part in the management of industrial assets.
- Predictive Maintenance (PdM): It is an advanced strategy, focused on predicting when a failure is likely to occur and correcting it before it happens. It is based on data obtained with the use of monitoring and analysis technologies that anticipate serious problems. Its features are: condition monitoring, data analysis, condition-based planning, among others. Unlike preventive, which is based on a schedule; In this program the actions are based on the conditions detected in the equipment.
- Reactive Maintenance (RM): It focuses on actions that are carried out only after a failure or breakdown occurs in an equipment, machinery or system. It is characterized by being a direct response to an already existing problem, instead of trying to prevent it beforehand. Its main characteristics are: reactivity, unplanned activities, unplanned downtime, high costs, etc.
Each has its own advantages and disadvantages. Preventive is the most effective to avoid failures, but it is also the most expensive. The corrective is the least expensive, but it is also the one that has the most impact on productivity. Predictive is an intermediate option that can help reduce costs and failures.
What is reliability?
It refers to a program, which is applied to guarantee the reliability of assets, systems and equipment. It is a measure of how well your repair efforts are being applied to ensure continuity of operations with minimal downtime.
Below, some concepts associated with a reliability analysis are defined:
- Failure Rate: Measures how often a system or component is likely to fail over a specific period of time. It is often expressed as the number of failures per unit of time.
- Mean time between failures (MTBF): It is the average time that a system or component can operate without experiencing a failure.
- Mean Time to Failure (MTTF): It is similar to MTBF, but is used specifically for systems or components that are repaired or replaced after a failure occurs.
- Availability: It is the measure of the proportion of time that a system or component is operational and available to perform its intended function. It is expressed as a percentage and takes into account both scheduled downtime for repairs and unscheduled downtime due to failures or other problems.
- Reliability: Evaluates the operability of a system or component to perform its intended function over a period of time, considering the probability and consequences of failure. A reliable asset is one that has little chance of failing and can be trusted to perform its intended job consistently.
An evaluation of these metrics provides valuable information about equipment reliability and helps optimize scheduled activities to increase uptime and reduce costs. Ultimately, achieving high reliability requires a comprehensive approach that includes preventive, predictive activities and asset management strategies.
Objective of maintenance and reliability
Initially, their objective is to guarantee the smooth and efficient operation of equipment, systems and facilities throughout their life cycle. With an ultimate goal of minimizing downtime, reducing costs and increasing the overall effectiveness of an organization’s operations.
A comprehensive program where maintenance and reliability interact helps companies ensure their assets perform at the highest level and continue to meet the needs of their customers and stakeholders.
Main pillars of maintenance and reliability
The most important ones are mentioned below:
- Resource optimization: It involves using available resources (human, financial, materials) in the most efficient way possible to carry out planned activities.
- Business processes: Include management systems and processes that support repair activities, such as work order management, planning and scheduling, and performance metrics.
- Workforce management: Encompasses practices and tools to manage and develop the workforce, including training, performance management and succession planning
- Materials management: Refers to the processes and systems used to process, acquire and store materials related to these activities, such as inventory management, suppliers and procurement strategies.
- Asset Management: Comprises strategies and practices for managing the organization’s physical assets, including precision strategies, performance management, and life cycle analysis.
- Performance management: Involves systems and tools to measure and analyze the performance of actions taken and activities carried out, including KPIs, data analysis and continuous improvement processes.
To achieve continuous asset performance, it is important to train the work team in charge of scheduling, monitoring and executing activities related to maintenance and reliability. Implementing an intelligent computerized maintenance management system (CMMS) allows you to manage the life cycles of elements with operational visibility and real-time monitoring.
Trends in maintenance and reliability
In the operational environment, time is synonymous with money for both business owners and leaders of these industrial departments. Therefore, today companies align themselves with the available trends:
- Digital transformation: Digitizing operations processes with modern CMMS programs is an opportune factor to achieve operational efficiency. Organizations are moving away from reactive methods and opting for proactive approaches to monitoring their critical equipment.
- Virtual technologies: Augmented reality (AR) and virtual reality (VR) are essential for on-site inspections, detecting anomalies in time. AR allows you to receive information in real time while inspecting equipment, facilitating timely actions. While VR offers a fully simulated environment, ideal for evaluating complex or dangerous scenarios without the risks associated with the real environment, thus improving personnel readiness and safety.
- Predictive analysis: The use of IoT devices, such as sensors, artificial intelligence and digital twins, has the function of identifying patterns and predicting the behavior of equipment to allow timely control with greater reliability.
- Workplace safety: Automating mechanical and redundant activities allows employees to focus on the most important aspects of their duties, improving the quality of work.
CMMS as improvement tools
A computerized maintenance management system (CMMS) is essential for companies to improve their maintenance processes. These provide a variety of occupations in relation to:
- Better planning and scheduling: These systems centralize work orders and programs, reducing downtime and optimizing workloads.
- Improved asset management: Monitor equipment performance, prevent breakdowns and optimize utilization.
- Improved inventory management: Ensure the right parts are available when needed, thereby reducing wait time in the event of an unplanned event.
- Optimized communication: Improves coordination between work teams, and allows a quick and effective response to emergency needs. Stakeholders can instantly and efficiently access relevant information about scheduled tasks and their schedules.
- Better data analysis: Enables deeper and more accurate evaluation of logs and metrics related to scheduled activities. This analysis not only reveals areas for improvement, but also provides detailed insight into asset performance trends and patterns.
- Automation of administrative tasks: Its main objective is to free up work resources, thus reducing the workload on repetitive tasks, providing time to execute strategic activities with greater added value within the organization.
- Reduce costs: They help companies reduce costs by improving efficiency and effectiveness.
These solutions allow you to streamline and optimize operations, increase equipment reliability and maximize uptime. With AI-based predictive capabilities, potential problems are identified early, avoiding costly failures.
Maintenance and reliability are essential to the efficient and continued operation of an organization’s assets and systems. Adopting technological trends and using tools such as CMMS make the difference in efficient industrial management.
Conclusions
This combination with a comprehensive approach is essential to achieve operational excellence in industries. Maintenance prevents failures and ensures operational continuity, while reliability evaluates the ability of assets to function predictably. Both are essential to achieve efficiency and reduce operating costs.
The adoption of technologies such as digital transformation and CMMS are necessary tools to improve the planning, scheduling and execution of maintenance and, therefore, asset management. Together, these elements are essential to optimize operations and maximize efficiency in any industry. These two methodologies are undoubtedly the secret to operational excellence in any industry.
References
Own source