Table of Contents
- What are refractory materials?
- Classification of refractory materials by composition
- Monolithic vs. shaped refractories
- Ceramic fiber refractories: Efficiency and lightweight
- Bessemer process and refractory development
- What affects the durability of refractory materials?
- Chemical corrosion in refractory materials
- Application methods based on refractory type
- Refractory mortars: Effective bonding and sealing
- Quality control for refractory materials
- Innovations in refractory materials for boilers
- Reference standards
- Conclusions
- References
In high-temperature industrial environments, such as those found in furnaces and boilers, operational efficiency, safety, and equipment longevity depend directly on the performance of refractory materials. Designed to withstand extreme thermal conditions, chemical corrosion, and mechanical stress, these compounds retain their physical and chemical integrity even under severe thermal cycles.
Their application is crucial in industries such as steelmaking, petrochemicals, cement, and power generation. Understanding their classification, properties, emerging technologies, installation methods, and quality parameters is essential to optimize thermal performance and ensure the durability of thermal systems.
What are refractory materials?
These are non-metallic compounds that maintain their physical and chemical integrity when exposed to temperatures above 1,000 °C. Their primary role is to protect the internal structures of equipment like furnaces and boilers from heat, abrasion, and chemical reactions.
Refractory materials offer high resistance to both heat-induced degradation and mechanical damage, ensuring continuous and long-term operation. They are formulated based on the type of process, the nature of the materials handled, the operational atmosphere, and equipment demands.
Classification of refractory materials by composition
They are classified based on chemical composition and presentation format:
By chemical composition (pH-based)
- Acidic refractories: Primarily composed of silica (SiO₂). Stable in acidic environments but vulnerable to basic slags. Commonly used in glass furnaces and converters.
- Basic refractories: Contain oxides such as magnesia (MgO) and dolomite (CaO·MgO). Resistant to basic slags and widely used in the steel industry.
- Neutral refractories: Based on alumina (Al₂O₃), chromite, or carbon. These materials resist both acidic and basic environments and are suitable for various industrial sectors.
By presentation format
- Shaped refractories (bricks or blocks).
- Monolithic refractories (unshaped: castables, gunnables, rammables, shotcrete).
- Ceramic fiber refractories.
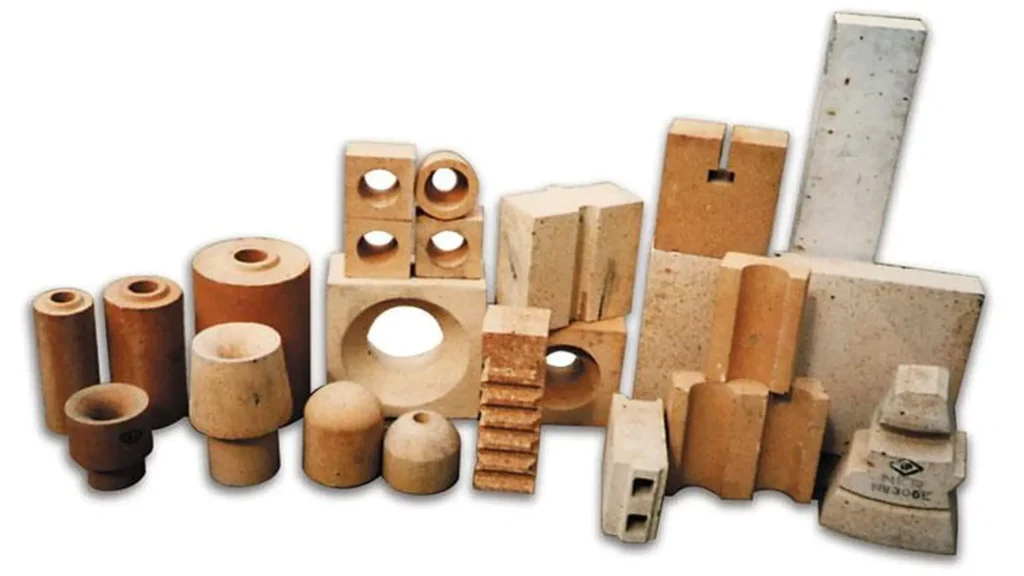
Monolithic vs. shaped refractories
Traditional shaped refractories come in the form of refractory bricks, while monolithic refractories are unshaped and applied and cured in situ.
Advantages of monolithic refractories
- Faster installation.
- Fewer joints (improved resistance to chemical corrosion).
- Adaptability to complex geometries.
- Easier localized repairs.
Advantages of shaped refractories
- High dimensional stability.
- Predictable thermal behavior.
- Long service life under static conditions.
The selection depends on equipment design, type of operation, and ease of maintenance, as well as thermal and mechanical stresses.
Ceramic fiber refractories: Efficiency and lightweight
Ceramic fiber refractories are advanced solutions for applications requiring lightweight thermal insulation. Made of alumina-silica fibers (Al₂O₃-SiO₂), they are available in various densities and forms: blankets, modules, panels, and papers.
Main features
- Low thermal conductivity.
- Excellent thermal shock resistance.
- High thermal reflectivity.
- Low thermal mass (rapid heat-up/cool-down).
They are widely used as inner linings in furnaces and boilers, especially in secondary or tertiary insulation layers, or in equipment with frequent thermal cycles. However, due to their lower mechanical and abrasion resistance, they are often combined with other refractory types.
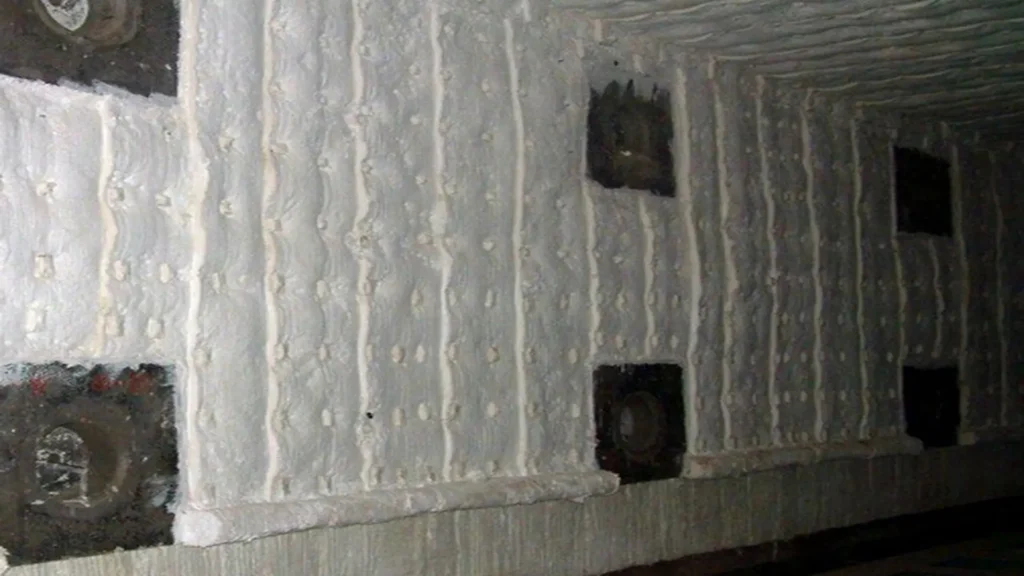
Bessemer process and refractory development
The Bessemer process, developed in the 19th century, revolutionized steel production by allowing the oxidation of impurities in pig iron through air blowing in converters. These reactions generated high temperatures and aggressive slags, demanding refractory materials that could withstand intense heat and chemical corrosion.
Initially, acidic silica refractories were used for low-phosphorus slags. However, when processing high-phosphorus pig iron, these basic slags quickly degraded the linings, prompting the use of basic refractories like dolomite and magnesia, which offered greater chemical and thermal resistance under harsher conditions.
What affects the durability of refractory materials?
Durability depends on more than just composition. Key factors include:
- Operating temperature: Sudden changes cause thermal shock and cracking.
- Mechanical pressure: Load and abrasion wear down the material.
- Chemical attacks: Chemical corrosion from slags, acidic gases, or alkalis weakens the structure.
- Thermal cycling: Frequent heating and cooling fatigues the refractory.
- Installation and curing quality: Especially for castables, improper curing reduces resistance.
Chemical corrosion in refractory materials
Chemical corrosion is a major degradation mechanism in industrial furnaces. It may include:
- Alkaline or acidic corrosion from gases or ash.
- Eutectic reactions with fluxes or slags.
- Oxidation of internal metallic phases.
Modern monolithic refractories use densified matrices, colloidal silica, and additives to reduce the penetration of aggressive agents, improving resistance to both thermal and chemical degradation.
Application methods based on refractory type
Shaped refractories
- Installed with refractory mortars.
- Require precise alignment and joint control.
- Mainly used in structural zones.
Monolithic refractories
- Casting: Poured into molds.
- Ramming: Hand or pneumatic compaction.
- Shotcrete: High-pressure hose application.
- Plastic installation: Hand-shaped and pressed onto surfaces.
Ceramic fiber refractories
- Mechanically anchored or adhered.
- Modular or overlapped installation.
Refractory mortars: Effective bonding and sealing
Refractory mortars are formulated mixes used to bond bricks or ceramic pieces and seal joints in high-temperature structures. Available in silica, alumina, or magnesia bases, they offer plasticity, heat resistance, and chemical corrosion resistance.
Common applications
- Bonding bricks in furnaces and boilers.
- Sealing joints and cracks in ceramic linings.
- Localized repairs of refractory structures.
Quality control for refractory materials
Quality control ensures that refractory materials perform reliably and last their intended lifespan. Controls are applied at various stages:
Receiving stage
- Verification of chemical composition certificates.
- Visual inspection for physical damage.
- Moisture, particle size, or cohesion tests for monolithics.
Installation stage
- Monitoring of water-to-material ratios.
- Mixing and application times.
- On-site tests for apparent density and porosity.
Drying and curing stage
- Thermal ramp control.
- Avoidance of thermal shock.
- Occasional non-destructive testing.
Operation stage
- Monitoring via thermography or visual inspection.
- Periodic wear evaluations.
Innovations in refractory materials for boilers
Recent innovations aim to enhance thermal efficiency, resistance, and reduce maintenance costs:
- Low Cement Castables (LCC) and Ultra-Low Cement Castables (ULCC): Monolithic refractories with ≤ 5% and ≤ 2% cement content, respectively, offering high density, low porosity, and excellent chemical resistance.
- Nanotechnology applied to alumina and silica matrices: Nanoparticles (e.g., colloidal silica) improve phase distribution, reduce porosity, and increase mechanical and thermal resistance.
- Self-healing refractories with microencapsulation: Refractories containing microscopic capsules that release compounds when cracked, sealing the damage and extending service life.
- Fast-drying, high-cohesion castables: Monolithic materials applied by casting or molding that cure quickly while maintaining strong internal adhesion and thermal shock resistance.
- Ceramic fibers with anti-abrasion coatings: Enhanced fibers with protective layers to resist mechanical wear while preserving insulation in demanding conditions.
Reference standards
- ASTM C401 – C1338: Physical tests and properties of refractory materials.
- API 936: Specification for the installation, inspection, and testing of monolithic refractories in furnaces and thermal equipment.
- ISO 12678-1 / ISO 1927: Standards for properties and testing of unshaped (monolithic) refractories
- ASME Boiler and Pressure Vessel Code (BPVC): Covers materials and heat-resistant linings for boilers and pressure vessels.
Conclusions
Refractory materials are essential to ensure the safe and efficient operation of industrial furnaces and boilers. Their proper selection, application, and quality control directly impact durability, thermal performance, and operational availability.
Today’s solutions, from monolithic and shaped refractories to ceramic fibers and nanotechnology-enhanced materials, enable industries to tackle challenges like chemical corrosion, thermal shock, and mechanical wear. A thorough understanding of their behavior, application techniques, and continuous condition monitoring is vital to maintaining efficient and sustainable thermal processes in modern industry.
References
- American Petroleum Institute. (2021). API Standard 936: Refractory Installation Quality Control – Inspection and Testing Monolithic Refractory Linings and Materials (3rd ed.). Washington, DC: American Petroleum Institute.
- INSPENET. (2023). Refractory materials in oil and gas. Retrieved from https://inspenet.com/en/articulo/refractory-materials-oil-and-gas/
- Okorder. (n.d.). Refractory ceramic fiber module for boiler insulation. Retrieved from https://www.okorder.com/p/refractory-ceramic-fiber-module-for-boiler-insulation_407633.html
- OpenPR. (n.d.). Refractory material market: Leading global companies. Retrieved from https://www.openpr.com/news/2575489/refractory-material-market-leading-global-companies