Table of Contents
- What is radiographic testing?
- Timeline of radiographic testing
- Key advantages of digital radiography
- Applicable standards in industrial radiography
- Innovation, AI, and technologies in NDT radiography
- Applied technologies and leading manufacturers
- Applications in non-industrial sectors
- Conclusions
- References
Radiographic testing is a non-destructive inspection technique that allows internal defects to be visualized without the need to cut or compromise the functionality and integrity of the material. Since its origins in the 19th century with the use of photographic film, it has evolved into highly efficient digital methods.
This article provides a comprehensive overview of radiographic testing, from its physical principles to the latest technologies such as computed radiography/digital radiography, artificial intelligence, automated radiographic inspection, and portable systems.
What is radiographic testing?
Radiographic testing is a non-destructive inspection technique that uses ionizing radiation to visualize the internal structure of a solid object without modifying it. When an X-ray or gamma ray passes through a material, its intensity decreases differentially depending on the density, thickness, and homogeneity of the element. An internal discontinuity, such as a crack or pore, reduces attenuation and generates visible contrast in the detection medium.
Physical fundamentals
The central physical principle is the law of exponential attenuation of radiation. This law states that as radiation passes through a solid, its intensity decreases exponentially. Any void, inclusion, or internal defect alters this attenuation, generating a detectable contrast in the image.
How traditional radiography is performed
In classic radiography, the system consists of an emitting source (such as an X-ray tube or a gamma source such as Ir-192 or Co-60), the object to be inspected, and a silver halide film placed on the opposite side of the source. After exposure, the film is developed using a series of chemical baths.
The result is a grayscale image, where darker areas indicate greater radiation transmission and the presence of internal discontinuities. This process requires controlled environmental conditions and careful handling.
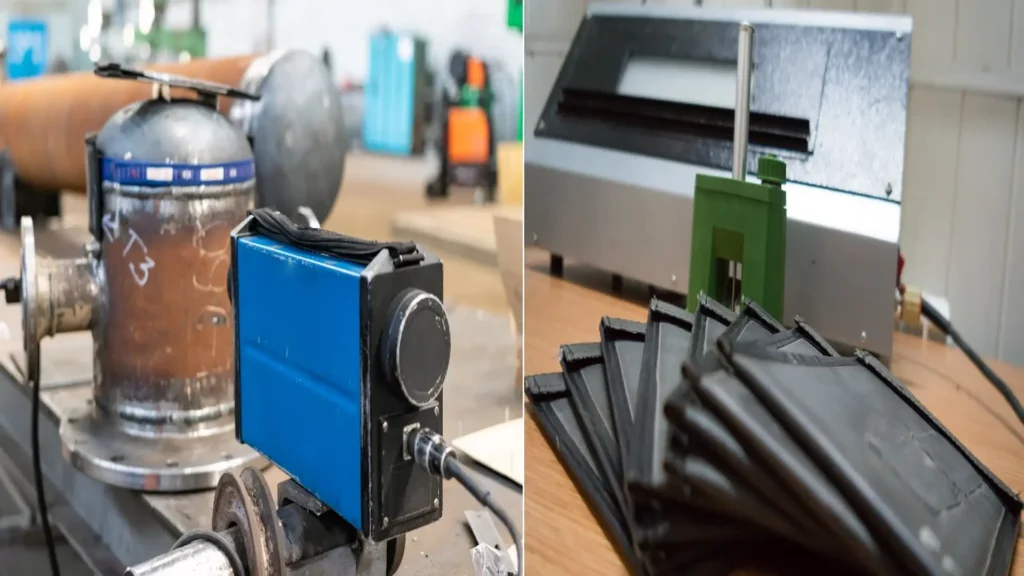
How digital radiography is performed
In modern systems, the same physical principle applies, but with digital means. In computed radiography (CR), photostimulated phosphor plates are used that store the energy received during radiation and are then scanned by a laser to form the image.
In direct digital radiography (DR), flat detectors directly convert radiation into digital signals in real time, eliminating the need for scanning. Both methods allow brightness and contrast to be adjusted, zooming to be performed, and images to be stored in digital systems with full traceability.
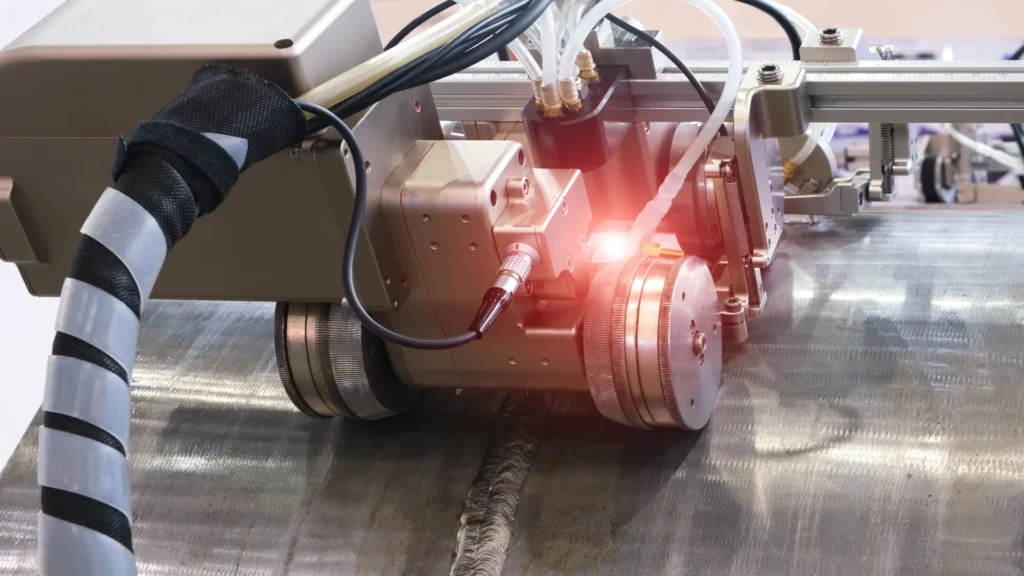
Radiation sources and detectors
- Classic radiography source: X-ray tubes, iridium-192 (Ir-192) and cobalt-60 (Co-60)
- Traditional detectors: Silver halide radiographic film.
- Modern systems: Phosphor plates (CR) and digital flat panel detectors (DR).
Most common defects detected by radiography
- Porosity (scattered or clustered)
- Slag or tungsten inclusions
- Internal cracks
- Laminations or lack of bonding
- Lack of fusion or incomplete penetration
- Shrinkage cavities or metal segregations
These irregularities manifest as variations in the optical density of the digital or analog image, facilitating their identification, classification, and documentation according to established regulatory criteria.
Timeline of radiographic testing
The history of industrial radiography is a technical chronology that reflects how scientific curiosity was transformed into an indispensable industrial tool. The main milestones and technologies are highlighted here:
- 1895 – The initial discovery: On November 8, 1895, at the University of Würzburg, Germany, Wilhelm Conrad Röntgen discovers X-rays. This discovery marked a turning point, allowing non-invasive visualization of the interior of opaque objects; his first experiments included simple metal components.
- 1896–1920s – First applications and development of film: In less than a year, X-rays were already being used to inspect metal components in the mechanical and railway industries. During the 1920s, companies such as Kodak (Type K, Type A films) and DuPont (Patterson-B, Patterson-S) developed films optimized for metals, improving image resolution and contrast.
- 1940s–1960s – High energy and portability: With World War II came linear accelerators and betatrons for high-energy X-rays, useful for inspecting thicker metal structures. In the 1960s, portable gamma sources such as Iridium-192 and Cobalt-60 were introduced, facilitating field inspections, especially on industrial pipelines.
- 1980s–1990s – The dawn of the digital age: The digital transition began in the 1980s with the introduction of computed radiography, which replaced conventional film and eliminated the need for chemicals. Standards such as ASTM E2033 began to standardize this technique. In the 1990s, direct digital radiography became established with the arrival of flat panel detectors, allowing instant capture without scanning and with higher resolution.
- 2000s–2019 – Digitization, standardization, and advanced analysis: During this period, companies such as Carestream NDT and Fujifilm optimized digital systems, reducing exposure times and improving operational efficiency. Standards such as ISO 17636-2 for digital radiography in welds and DICONDE for archiving and traceability were established. DR systems became more compact and software evolved with measurement tools, automated analysis, and contrast enhancement.
- 2020s–Present – Automation and Artificial Intelligence: Industrial radiography is being integrated with AI, machine learning, IoT, and autonomous systems. Companies such as 3E NDT, Waygate, and Vidisco integrate AI and machine learning algorithms for real-time analysis, including non-destructive inspection by drones and robotics. Standards such as ASTM E1030 and ASME Section V support the new era of digital X-ray inspection.
Classic vs. digital radiography
Feature | Conventional X-ray | Digital X-ray (CR/DR) |
Capture medium | Silver halide film | PSP plates (CR) /Flat detectors (DR) |
Processing | Chemical development in darkroom | Digital, no chemicals or darkroom |
Time to obtain results | Slow (manual) | Immediate (DR) / moderate (CR) |
Traceability | None or limited | Complete (DICONDE) |
Image manipulation | Fixed | Digital adjustments without loss of quality |
Reuse | No | Yes (CR), DR without consumables |
Radiological exposure | Higher dose | Lower (more efficient sensors) |
Key advantages of digital radiography
The transition from traditional to digital radiography has introduced technical, operational, and analytical improvements that optimize NDT inspection at all levels. The main advantages include:
- Complete traceability using standard formats such as DICONDE
- Reduced radiation exposure thanks to more sensitive sensors
- Higher spatial resolution and ability to detect subtle defects
- Immediate processing and real-time visualization, with the ability to review images remotely, facilitating remote audits and technical collaboration.
- Elimination of chemicals and reduced environmental impact
- Compatibility with automated inspection systems and AI analysis software
- Secure digital storage, quick search, and historical comparison
- Integration with asset management and predictive maintenance platforms
- Digital thickness measurement even on components with coatings or insulation
- Automated quantification of porosity and discontinuities with image analysis
- Improved repeatability and reduced human error by standardizing processes
Applicable standards in industrial radiography
The reliability of radiographic testing, both conventional and digital, depends directly on compliance with international standards and regulations such as ASTM and ISO, specifically:
- ASTM E1030 / E1742: General radiographic examination and examination of metal castings.
- ASTM E2446 / E2736: Technical evaluation and classification of CR and DR systems.
- ISO 17636-1 / 17636-2: Radiographic testing of welds with film (part 1) and digital (part 2).
- DICONDE (Digital Imaging and Communication in Nondestructive Evaluation): Standardizes the storage, analysis, and traceability of digital NDT images.
Compliance and technical accreditation
The precise application of standards is a requirement for the certification of NDT technicians. Inspectors who perform radiographic inspection tasks must be qualified under globally recognized schemes, such as:
- ASNT SNT-TC-1A: Defines requirements for training, experience, and evaluation of NDT personnel.
- ISO 9712: Regulates certification at levels I, II, and III in NDT testing, including radiography.
The training required for these levels includes technical knowledge, radiation protection principles, image reading, and application of standards. Accreditation bodies are the guarantors of the technical competence and regulatory compliance of inspectors, ensuring that they have the necessary skills to apply techniques effectively and, above all, safely.
Innovation, AI, and technologies in NDT radiography
Industrial radiography has seen major advances in image capture, resolution, and quality, along with technical improvements in data analysis, interpretation, and management processes. These developments are shaping a new generation of non-destructive testing (NDT) characterized by high precision, efficiency, and reliability.
Automation with artificial intelligence
- Current algorithms enable:
- Automatic detection of defects (cracks, porosity, lack of fusion).
- Classification based on regulatory criteria.
- Reduction of human error and standardization of results.
- Automatic optimization of exposure parameters.
Connectivity and Industry 4.0
- Digital Twin: Use of 2D/3D images to create predictive virtual models.
- IIoT: Online monitoring of the status of radiographic equipment.
- Remote audits with DICONDE: Access to reports and validation from anywhere.
Applied technologies and leading manufacturers
Innovative solutions that include state-of-the-art hardware and software have taken radiographic inspection to new levels of precision and versatility:
- Carestream NDT: A pioneer in direct (DR) and high-energy digital detectors. It has innovated with flexible panels such as the INDUSTREX HPX-ARC series, which offer high resolution and low power consumption.
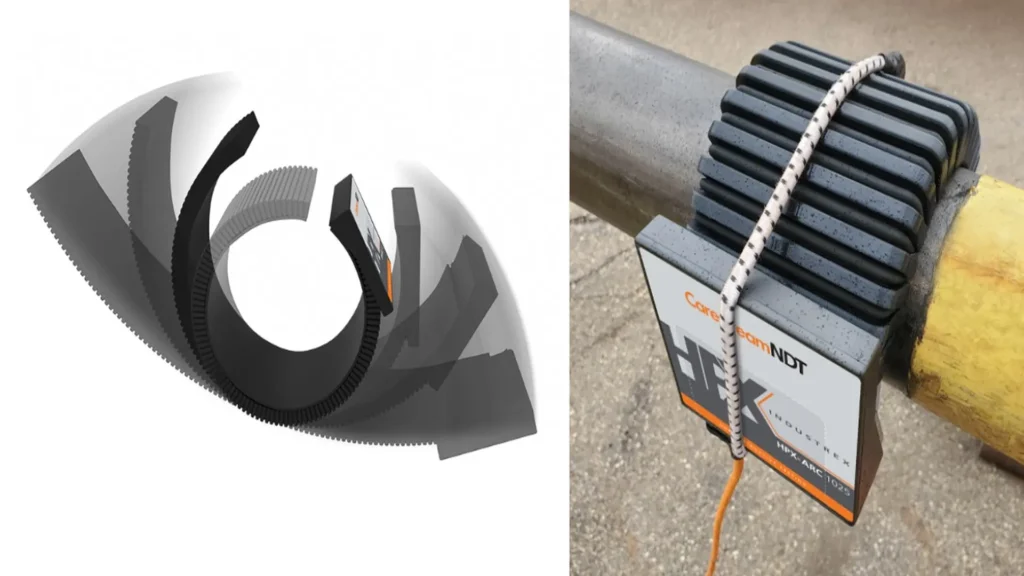
- Waygate Technologies (part of Baker Hughes): Specialists in portable digital detectors (DXR), CR scanners, and processing software (Rhythm Insight, Flash).
- Vidisco Guardian 12 Elite: Wireless DR system allows for cable-free inspections, with battery power, Wi-Fi connectivity, and augmented remote viewing.
- Fujifilm FCR and DR: Wide range for progressive transition from traditional to digital.
- D-CR 35 NDT from DÜRR NDT: High-resolution CR scanner with D-Tect X software and DICONDE compatibility for high-performance CR.
- Xpress Flex from 3E NDT: Flexible panel that adapts to curved surfaces, eliminating edge losses and allowing complete captures without repositioning. Systems such as XpressScan + XVU from 3E NDT automate sequential scans, stitching images together for continuous panoramic views. The following video presents a demonstration of 3E NDT’s digital radiography solutions.
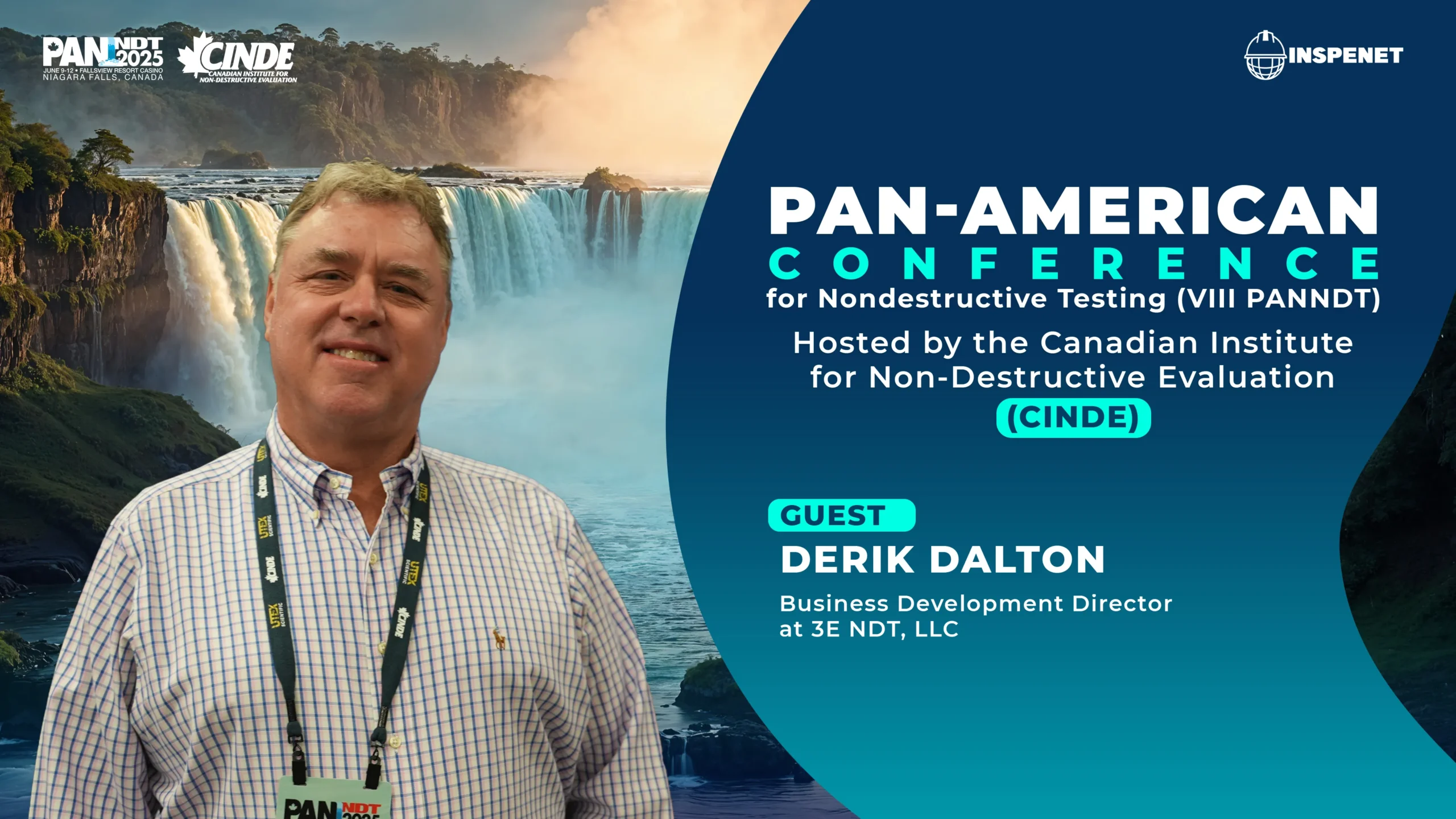
Flexible and adaptable panel, “Xpress Flex” for radiographic testing of welds.
Applications in non-industrial sectors
Industrial radiography has transcended the technical environment to be used in fields such as:
- Art and archaeology: It allows conservators and archaeologists to perform non-invasive studies to examine the internal composition of artifacts, paintings, and sculptures without causing damage.
- Forensic medicine: Analysis of bone structures, concealed objects, and remains without the need for direct manipulation.
- Electronics: Evaluation of BGA soldering, microchips, and internal connections in PCBs.
- Additive manufacturing: Radiographic inspection of 3D-printed parts to detect porosity and subsurface defects.
Conclusions
Industrial radiography, consolidated after decades of technological evolution, has remained a fundamental technique in non-destructive quality control. Radiographic testing, with its effectiveness in detecting internal discontinuities without compromising the structural integrity of the component, makes it an essential tool in industrial sectors with high reliability requirements.
With the adoption of high-precision sensors, digital platforms, artificial intelligence, and international standards, industrial radiography aligns with the principles of reliability, sustainability, and efficiency demanded by 21st-century industry. From laboratories to oil fields and archaeological sites, its evolution continues to set the standard for modern non-destructive testing.
References
- Carestream. (n.d.). NDT Solutions. https://www.carestream.com/en/us/nondestructive-testing-ndt-solutions
- DÜRR NDT. (n.d.). What is CR Technology? https://www.duerr-ndt.com/products/computed-radiography/what-is-cr-technology.html
- Espectrometría. (n.d.). Radiografía Industrial – Avances y Aplicaciones en la Industria Moderna. https://espectrometria.com.mx/radiografia-industrial-avances-y-aplicaciones-en-la-industria-moderna/