Table of Contents
- PEC method fundamentals and industrial applications
- CUI at height: Operational impact and PEC response
- Integrating PEC with drones and robots for remote inspection
- PEC vs. Ultrasonic Testing in non-destructive evaluations
- Applying PEC to live pipelines and hot surfaces
- PEC benefits in risk based inspection (RBI) programs
- PEC innovation: From early devices to smart technologies
- Conclusions
- References
Introduction
Corrosion Under Insulation (CUI) represents one of the greatest challenges in the integrity management of industrial assets, particularly in elevated structures. This type of degradation occurs covertly, between the metal surface and thermal insulation, driven by the presence of moisture and aggressive environmental conditions. When CUI affects components located at height—such as vertical piping, columns, or systems mounted on elevated structures—its detection and assessment become significantly more complex, increasing operational risks and associated costs.
In industries such as petrochemicals, hydrocarbon refining, and chemical processing plants—where thermally insulated lines are prevalent—CUI in elevated areas has become a critical focal point for predictive maintenance strategies, as demonstrated by this analysis applied to atmospheric tanks. Conventional inspection techniques, such as contact-based ultrasonic testing or radiography, require direct access and, in many cases, full removal of the insulation, which is not only costly but also hazardous in hard-to-reach environments.
To address these limitations, the Pulsed Eddy Current (PEC) method emerges as an innovative and non-intrusive solution. Using electromagnetic sensors capable of penetrating insulation layers, PEC enables reliable evaluations from the external surface, even from a distance, thus opening new possibilities for remote and safe inspection at height and enhancing pipeline integrity in inaccessible areas.
PEC method fundamentals and industrial applications
What is Pulsed Eddy Current (PEC)?
The Pulsed Eddy Current (PEC) method is based on the principles of electromagnetic induction and magnetic field relaxation. In this technique, a transmitter coil emits a brief electromagnetic pulse onto the surface of a conductive material. This pulse induces Eddy currents (or parasitic currents) within the metal. Once the pulse ceases, the induced field decays over time, and this transient response is precisely what is captured and analyzed.
Unlike traditional Eddy Current methods that operate on continuous frequencies, PEC uses low-frequency pulses, enabling greater depth of penetration. This makes it ideal for inspecting metallic components covered by non-conductive materials such as thermal insulation, paint, concrete, fireproofing, or corrosion barriers. For this reason, PEC is a key tool in environments where removing coatings is hazardous, expensive, or technically unfeasible.
This technology has been validated within recognized non-destructive examination (NDE) standards, and its applicability in Risk-Based Inspection (RBI) programs is widely acknowledged due to its non-intrusive nature, repeatability, and compatibility with remote or robotic inspection systems, making it a valuable asset for pipeline integrity assurance programs.
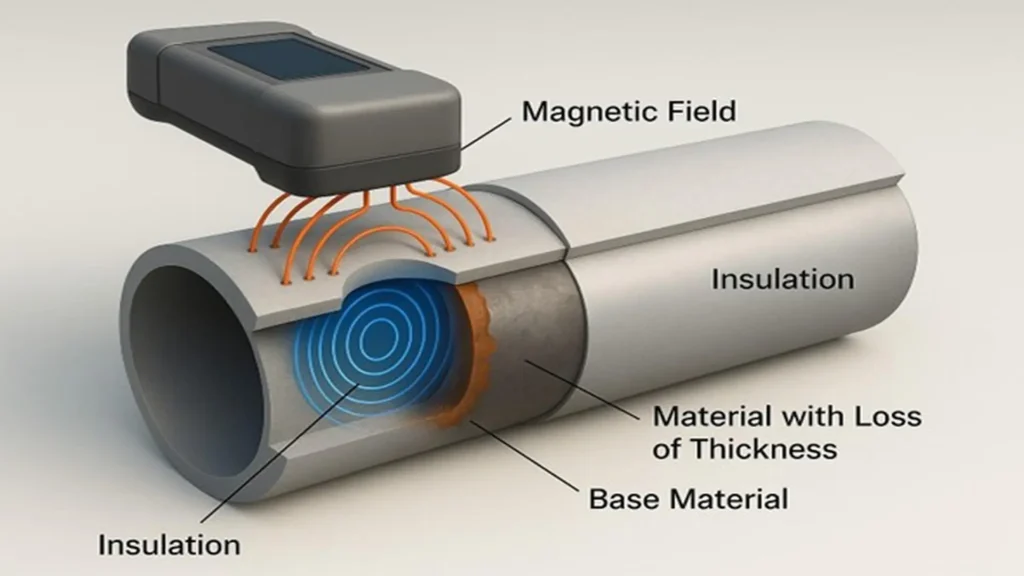
How do Eddy Currents work?
Eddy currents are electrical currents induced within a conductive material when it is subjected to a variable magnetic field. According to Faraday’s Law, this interaction generates circulating currents in the form of swirls distributed beneath the metal surface. The way these currents flow and decay over time depends directly on the material’s physical properties, such as its thickness, conductivity, and the presence of internal discontinuities.
By observing and analyzing this transient response, PEC systems can accurately infer conditions such as thickness loss, internal corrosion, trapped moisture, and other critical defects—without direct contact or the need for intensive surface preparation.
Why is it called “Pulsed Eddy Current”?
The name Pulsed Eddy Current accurately describes the method’s core principle:
- Pulsed: because it uses short bursts of magnetic energy instead of continuous waves.
- Eddy Current: because it generates and measures the response of the internal induced currents.
This approach allows for the collection of rich, precise data in complex materials or limited-access environments. Moreover, the transient signal can be analyzed using mathematical models and algorithms that interpret electromagnetic behavior for predictive structural assessment.
Application on insulated pipes and elevated areas
One of PEC’s greatest advantages is its ability to perform inspections on coated or hard-to-access components, such as:
- Pipes installed at height or on elevated racks
- Tanks with thermal insulation
- Covered vertical columns and structures
- Heat exchangers, trays, or ducts inaccessible by direct contact
These applications are particularly relevant in regulatory contexts such as those described in the comparison between API 570 and API 1169 standards. The pulsed eddy current system can be operated from elevated platforms, drones, or robotic arms, avoiding high-risk tasks and costly mechanical interventions.”.
Types of defects detectable with PEC
The system is capable of detecting or inferring the following common forms of deterioration:
- Thickness loss due to general or localized corrosion
- Corrosion Under Insulation (CUI) without removing the coating
- Accelerated degradation zones caused by trapped moisture
- Internal delaminations and non-visible discontinuities
- Minimum residual thickness conditions in critical piping
This data can be integrated into digital predictive maintenance systems, dynamic RBI platforms, and digital twins, all of which contribute to improved pipeline integrity management and decision-making.
CUI at height: Operational impact and PEC response
Corrosion Under Insulation (CUI) is a form of hidden corrosion that occurs when moisture penetrates the thermal insulation, creating a corrosive environment between the coating and the metal surface. In elevated installations—such as process columns, vertical ducts, or structural supports—this phenomenon worsens due to environmental conditions and the inherent difficulty of inspection and monitoring at height.
Industry studies reveal that between 40% and 60% of wall-thickness loss failures in insulated lines are caused by CUI, with a significant percentage occurring in elevated areas where access is limited. Conventional inspection operations at height typically require scaffolding, insulation removal, plant shutdowns, and pose safety risks to technical personnel—factors that negatively affect both cost and operational continuity.
In response to this reality, the use of PEC technology offers a viable technical solution. Thanks to its ability to penetrate coatings without direct contact, PEC enables the detection of wall-thickness loss without removing the insulation. When integrated with mobile platforms or automated devices, PEC becomes an effective tool for conducting remote inspections at height, reducing intervention costs, downtime, and human risk.
Integrating PEC with drones and robots for remote inspection
Accessing elevated equipment or hard-to-reach areas has traditionally been one of the main obstacles in inspection programs. Today, combining PEC technology with robotic systems and specialized drones provides a cutting-edge solution to this challenge. Among the most advanced tools are drones equipped with stabilized articulated arms and magnetic crawlers designed for vertical or curved metal surfaces. These systems are engineered to accurately position the PEC probe on insulated surfaces, even in extreme conditions of elevation or geometry.
In industrial settings such as refineries or thermal power plants, documented cases already exist of aerial inspections using UAV-type drones fitted with mobile arms carrying PEC probes. These allow scanning of previously inaccessible areas, avoiding scaffold assembly and reducing personnel exposure. Manufacturers such as Invert Robotics, Skyspecs, and DroneDeploy, in collaboration with PEC developers like Eddyfi Technologies, have demonstrated the technical and operational feasibility of these integrations.
Additionally, integration with digital visualization platforms enables real-time monitoring, secure data storage, and full traceability. This enables a more efficient, auditable approach that aligns with Integrity Management System (IMS) frameworks. Thus, the fusion of PEC with remote inspection technologies redefines the concept of safety and effectiveness in high-risk or geometrically complex areas.
PEC vs. Ultrasonic Testing in non-destructive evaluations
While Pulsed Eddy Current (PEC) and Ultrasonic Testing (UT) are complementary technologies within non-destructive testing (NDT), their physical principles and operational capabilities differ significantly. UT relies on the propagation of acoustic waves and requires direct coupling and contact with the inspected surface, making it highly precise but dependent on surface preparation and physical access. In contrast, PEC uses pulsed electromagnetic fields that do not require contact, allowing for the evaluation of components through thermal insulation or coatings without removal.
In terms of resolution, UT offers greater precision for detecting localized defects and obtaining point-specific thickness measurements. However, in scenarios involving thick insulation, restricted access, or operator risk, PEC stands out due to its remote scanning capabilities and resistance to adverse environmental conditions.
Therefore, PEC does not replace UT—it complements it, especially in CUI applications located in inaccessible areas or where insulation removal is impractical. An effective inspection strategy often involves using both technologies: PEC for pre-screening critical areas, and UT for detailed validation of zones with signs of degradation.
Applying PEC to live pipelines and hot surfaces
Yes, the PEC method can be applied to in-service pipelines operating at high temperatures, as long as the thermal limits of the equipment are respected. Next-generation PEC probes are designed to withstand temperatures up to 250 °C, depending on the manufacturer, making them ideal for inspections on hot lines without the need for plant shutdowns.
Field studies, particularly in the petrochemical industry, have demonstrated PEC’s effectiveness in assessing wall-thickness loss in thermally insulated, operating pipelines. This advantage translates into reduced operational costs, elimination of risks associated with direct contact, and preservation of operational continuity.
Unlike ultrasonic testing, PEC does not require coupling or direct contact with the metal surface, avoiding issues such as couplant evaporation or operator burn hazards. This feature makes PEC an optimal tool for hot integrity monitoring, without compromising safety or accuracy.
PEC benefits in risk based inspection (RBI) programs
The use of Pulsed Eddy Current (PEC) in Risk-Based Inspection (RBI) programs is transforming the way industrial assets are managed. One of its main benefits is the elimination of intrusive tasks such as insulation removal, which significantly reduces intervention costs and avoids operations that could disrupt plant continuity, while preserving and optimizing pipeline integrity throughout the asset lifecycle.
From an operational standpoint, PEC enables broader inspection coverage per shift, thanks to its ability to rapidly scan insulated surfaces without prior preparation. This allows more assets to be assessed using fewer resources and in less time.
From a safety perspective, PEC reduces personnel exposure to working at height or in hazardous zones, complying with the most demanding HSE (Health, Safety & Environment) standards.
Regarding its integration with RBI models, especially when aligned with guidelines such as those defined in the ASME B31.3 standard for piping systems, PEC not only feeds integrity databases with reliable wall-thickness data but can also be connected to advanced digital platforms that use artificial intelligence (AI) and machine learning (ML). These algorithms analyze large volumes of data collected by PEC and other sources to detect patterns, predict critical zones, and optimize future inspection planning. This synergy enhances data-driven decision-making and improves asset reliability throughout their lifecycle.
PEC innovation: From early devices to smart technologies
The development of Pulsed Eddy Current (PEC) technology has been driven by the critical need to detect corrosion under insulation (CUI) without resorting to destructive methods or direct intervention. Since its early applications in the early 2000s, several companies have led the technological evolution of this method, developing increasingly precise, portable, and remote-inspection-compatible equipment.
Among the pioneers is TSC Inspection Systems (UK), which introduced the first commercial PEC systems under the AMIGO brand, focused on inspecting insulated piping and metal components. Later, Eddyfi Technologies (Canada) acquired TSC and enhanced its capabilities by launching a new generation of devices such as Lyft®, a high-performance portable instrument that revolutionized CUI detection with its ability to map wall-thickness loss through insulation up to 100 mm thick.
Below is an official video by Eddyfi Technologies, a leading provider of advanced electromagnetic inspection solutions. This material showcases the Lyft® system in action—one of the most innovative PEC tools for detecting corrosion under insulation (CUI). The demonstration highlights how the equipment operates in real-world environments, its data acquisition interface, and the accuracy of its scans over coated surfaces. The video, owned by Eddyfi Technologies, complements this article by visually illustrating the high performance and applicability of the PEC method in demanding industrial operations.

PEC technology: Pulsed Eddy Current Probe.
Other relevant companies in the PEC ecosystem include:
- Innerspec Technologies (USA), which developed combined PEC and Guided Wave solutions for comprehensive inspections.
- Applus+ RTD (Spain and the Netherlands), which integrated PEC probes into robotic inspection solutions for elevated assets.
- ROSEN Group (Germany), which has adapted non-invasive electromagnetic technologies for buried pipelines and critical infrastructure.
Today, next-generation PEC systems are integrated with digital platforms, robotic scanners, and AI algorithms to enable predictive analysis of CUI-related degradation. This evolution illustrates how the industry has moved from exploratory manual solutions to smart, traceable, and connected tools, essential for advanced Risk-Based Inspection (RBI) programs.
Conclusions
Pulsed Eddy Current (PEC) technology represents a fundamental strategic advance for structural integrity through the use of efficient non-destructive inspections on isolated assets. Its ability to detect corrosion under insulation without disrupting operations significantly improves maintenance planning and execution, which is vital for industrial sectors where safety and operational continuity are priorities.
Integrating PEC into strategic maintenance plans optimizes resource allocation and reduces long-term costs by minimizing unexpected downtime and maximizing equipment life. Moreover, its compatibility with complementary techniques and digital predictive maintenance platforms amplifies its impact, strengthening Risk Based Inspection (RBI) models and favoring a more informed and efficient management.
The PEC methodology represents a strategic tool for decision making in industrial maintenance. Its adoption contributes to improve operational reliability and profitability, therefore, it represents a significant technique in the modernization of structural integrity programs.
INSPENET recommends exploring non-intrusive predictive maintenance methodologies such as advanced modal analysis. See the article: Modal Analysis with Piezoelectric Sensors Applied to CBM, an efficient solution for the early detection of failures in critical industrial components.
The future of structural integrity is here, and PEC is one of its key pieces.
References
- Eddyfi Technologies. (n.d.). Pulsed Eddy Current (PEC). Retrieved from https://www.eddyfi.com/en/technology/pulsed-eddy-current-pec
- Voliro AG. (n.d.). Voliro Drones Enhance High-Altitude Industrial Inspections. Unmanned Systems Technology. Retrieved from https://www.unmannedsystemstechnology.com/feature/voliro-drones-enhance-high-altitude-industrial-inspections/
- MISTRAS Group. (n.d.). Pulsed Eddy Current (PEC) Inspection Services. Retrieved from https://www.mistrasgroup.com/how-we-help/field-inspections/advanced-ndt/pulsed-eddy-current-pec/
- TÜV Rheinland. (n.d.). Pulsed Eddy Current (PEC). Retrieved from https://www.tuv.com/usa/en/pulsed-eddy-current-%28pec%29.html
- Applus+ RTD. (n.d.). INCOTEST: Corrosion Under Insulation Inspection Tool. Retrieved from https://www.applus.com/us/en/what-we-do/sub-service-sheet/incotest-corrosion-under-insulation-inspection-tool
- IRISNDT. (n.d.). Pulsed Eddy Current (PEC) – Advanced NDT Services. Retrieved from https://www.irisndt.com/services/advanced-ndt-services/pulsed-eddy-current-pec/
- Inspenet. (2024). Application of Advanced Technologies in Risk-Based Inspection (RBI) Programs for Atmospheric Tanks. Retrieved from https://inspenet.com/en/articulo/rbi-technologies-f