Process equipment such as heat exchangers, towers, drums, furnaces and boilers in refining plants typically become less efficient over time, because during the operational period incrustations are deposited inside them, causing a decrease in operating efficiency below their design value and compromising the quality of the processes; that is why the cleaning of process equipment is key to higher productivity.
The optimal functioning of the static process equipment in the production management of a refinery is fundamental since it directly affects its capacity to operate in a safe, efficient and sustainable manner. Periodic cleaning of equipment is a necessity to restore and maintain the operability of the systems in the refining processes.
In addition, cleanliness is also a prerequisite for inspections and maintenance work. In the following sections, we will discuss the importance of process equipment, causes of fouling, types of process equipment cleaning and applied cleaning technologies.
Main process equipment and its importance
Refinery equipment is used indefinitely in processes to convert crude oil into useful products such as gasoline, diesel fuel, lubricants, liquefied petroleum gas and other derivatives. The main static equipment that make up the systems in a refinery include heat exchangers, towers/columns, drums/separators, filters, furnaces, boilers and others.
In refining plants, each of these pieces of equipment has a direct influence on the operational efficiency of the processes. Initially, furnaces have the function of supplying energy-efficient heat to various process streams, heating the crude oil before it enters the distillation units to facilitate chemical reactions during conversion; heat exchangers transfer heat between fluids to either heat or cool process streams where temperature controls must be precise.
The distillation towers fractionate the components of crude oil and other hydrocarbon mixtures based on their different boiling points through controlled vaporization and condensation processes, where the more volatile components are separated from the less volatile ones, in order to obtain a variety of derivatives; the drums store and separate liquids and gases in different stages for further processing, while the boilers generate steam at high pressure and temperature for various processes and power generation. There are also other important equipment such as filters, reactors, coke drums and storage tanks.
Most common causes of fouling
Fouling in oil refineries tends to be more complex compared to other processing facilities, mainly due to the intensive use of carbon steels. These materials are protected against corrosion by the formation of protective films formed under certain pressure and temperature conditions; however, during normal or adverse operation, these layers can peel off, forming deposits or scale in the operating systems.
The causes of fouling related to refining processes commonly come from one or more factors, such as: reaction and corrosion products, hydrocarbon compounds, organic polymers, coke residues and carbon matter, inorganic salts, scale, process additives, sediments or loose residues. Some equipment or parts of equipment where these types of dirt can be found are described below:
Corrosion fouling is found in almost all high temperature areas including heat exchanger tubes, transfer lines, bottom of distillation towers; and generally contain iron sulfide and chlorides. Meanwhile, in the low temperature sections such as the tops of the distillation towers and condensation equipment, a mixture of iron sulfides is present.
Reaction products can foul equipment for a variety of reasons. For example, sulfur vapors produced by hydrogen sulfide from high-temperature sulfur plants deposit a layer of sulfur that solidifies. Loose debris is usually found in the form of fine catalysts, pieces of spray coatings, fragments from organic coatings, corroded sections of vessel internals or pump internals.
Hydrocarbon compounds are made up of oily residues, sludge and viscous residues; these are often the main constituents of fouling in storage tanks and separator drums. Coke residues and carbon matter are produced by the thermal degradation of various hydrocarbons; they are commonly deposited in the exchanger tubes and lower sections of distillation towers.
Organic polymers cause fouling in the tubes of the preheating exchangers of crude oil distillation units and in naphtha hydrotreating units; they also contribute to the fouling of the tubes of direct-fired heaters. Organic polymers decrease heat transfer in the affected equipment and act as binders for corrosion products and salt deposits.
Process fouling deposits are caused by wash water injection, process steam, or water leaks from cooling systems. In crude oil distillation equipment, desalination tends to cause scale deposition in preheater exchangers and crude oil heater tubes. Deposits of inorganic salts that are related to the process originate with certain reaction products.
Corrosion inhibitors, additives or neutralizers, are recognized as contaminants of process equipment in areas near their injection point. For example, fouling occurs when undiluted inhibitor is injected into a superheated steam line, or into a reflux line and ends up deposited on top of a distillation tower. Sediments enter the crude oil distillation units and contribute to the fouling of preheating exchanger tubes and desalination vessels.
Why is process equipment cleaning important?
During operations most process equipment gets dirty from various causes, so process equipment cleanliness is important because it ensures operational efficiency, safety, product quality and regulatory compliance in industrial operations. Deposits and fouling accumulated during operation are unavoidable, which is why refinery process equipment requires periodic cleaning as part of maintenance programs and sometimes for operational emergencies.
The cleaning of process equipment is to restore its capacity by removing accumulated residues or adhered incrustations that compromise heat transfer, obstruct the fluid, block systems, generate corrosion, minimize operational efficiency, diminish the quality of finished products or increase the risk of accidents. In addition, this practice is mandatory to perform the inspections that determine the mechanical integrity of the same.
Fouling or scale deposits can cause heat transfer problems, such as fouling of the tubes in the convection zone of crude preheater furnaces, as shown in Figure 1, can cause significant overheating of the process1.
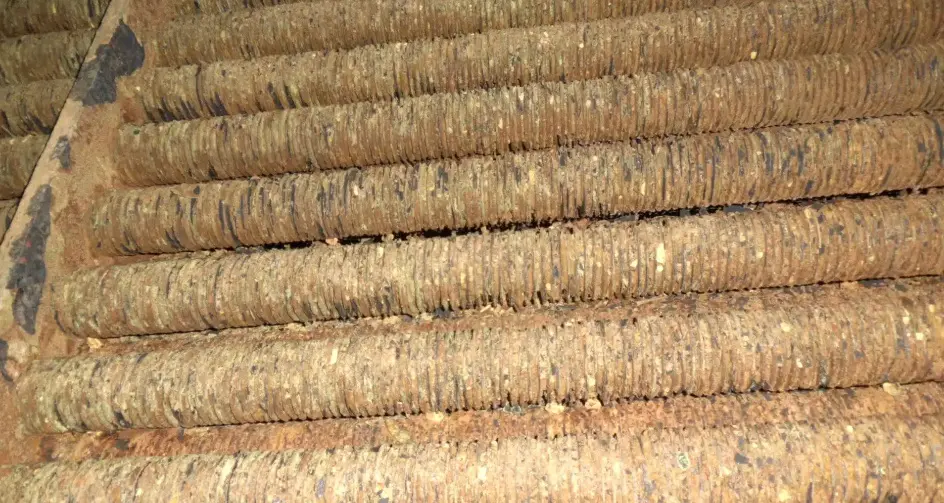
Therefore, periodic cleaning of process equipment is only one of many necessary maintenance operations that must be planned and carried out at scheduled intervals; to obtain better process performance and optimize energy consumption.
Cleaning of inspection equipment
The process equipment is flooded with steam and washed with water before opening to the atmosphere. The air in the steam or wash water accounts for the presence of various deposits on the internal part of the same, which is why cleaning of process equipment for inspection and maintenance purposes is necessary for the safe entry of personnel.
These are activities that must be performed under approved procedures that address sediment removal, neutralization, dilution and disposal of hazardous chemicals, as well as venting of toxic vapors to appropriate containment media.
Cleaning process equipment for inspection and Non Destructive Testing (NDT) ensures an accurate assessment of its condition and performance. It is required to remove debris that may hide defects such as cracks, corrosion or wear, allowing a detailed inspection and preventing future failures. In addition, it facilitates maintenance, improves operational safety and extends equipment life.
Types of equipment cleaning
Different refinery equipment requires specific cleaning methods. These methods are adapted to the needs and types of deposits to be removed in the equipment. Among the most common types of equipment cleaning are:
High pressure water cleaning (hydroblasting): The force and flow refers to the pressure and amount of water needed to remove solid deposits and scale that damage the equipment; the material to be removed will determine which tool should be used with this type of cleaning. This method is widely used for its efficiency, and is probably the most effective means of removing coke residues.
In this context, below is a video showing how to carry out heat exchanger cleaning using high-pressure jetting systems, courtesy of Falch Company.
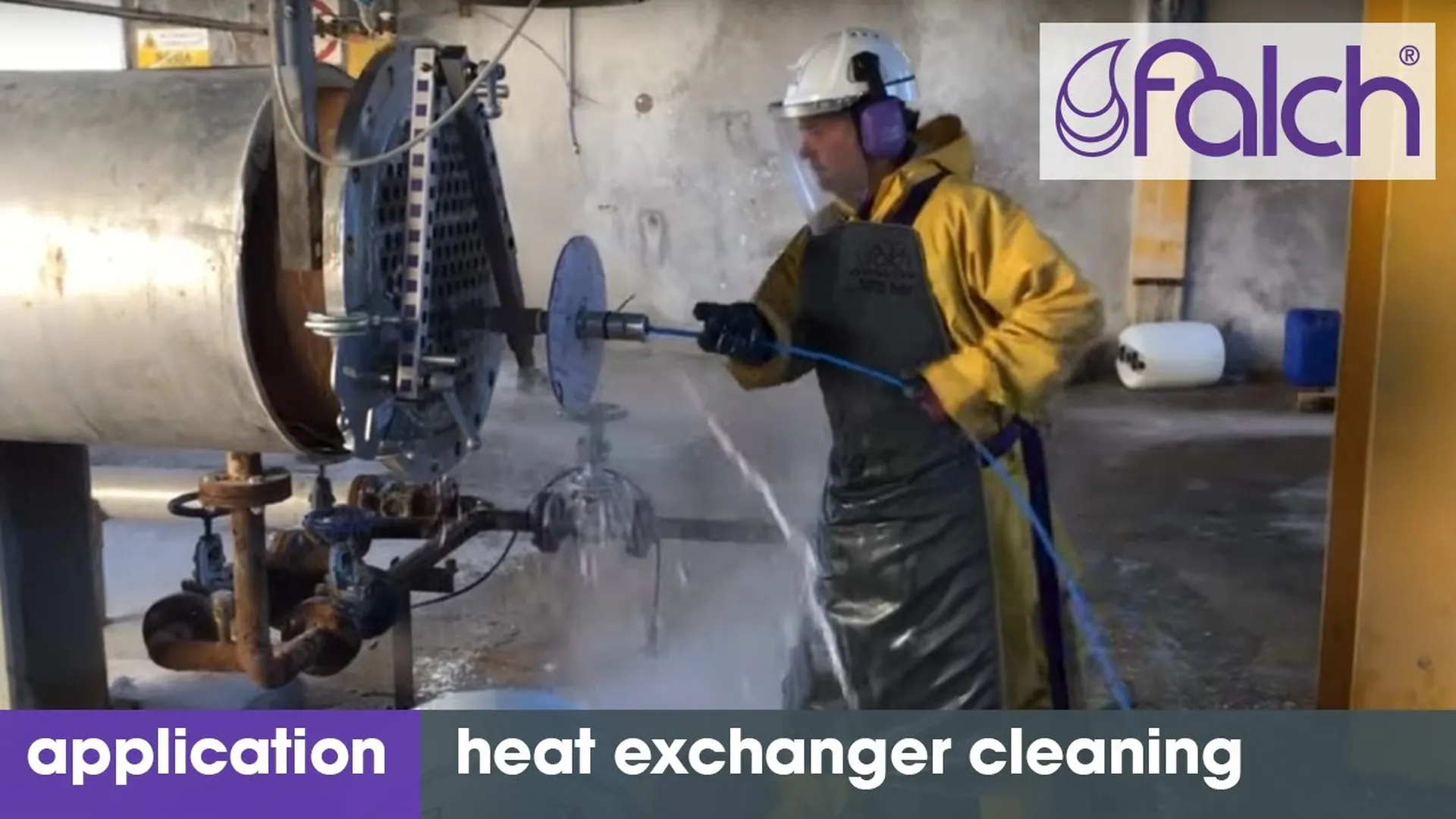
Limpieza profesional de intercambiadores de calor con sistemas de chorro de alta presión.
Chemical cleaning: Specialized chemicals are used to break down and remove deposits and organic and inorganic particles that accumulate over time on the internal surface of the equipment, in most cases applied to heat exchangers, boilers, pressure vessels. This type of cleaning requires specialized equipment and the chemicals used are often hazardous and corrosive, requiring strict adherence to safety protocols and standards.
Steam cleaning: Steam cleaning uses high temperature steam to dissolve and remove greasy and oily deposits. This method is effective for deep cleaning and disinfection, making it the primary choice for certain types of refinery equipment. Steam is also used to clean containers contaminated by organic substances by applying solvents in vapor phase.
Immersion cleaning: Consists of completely submerging the components or parts of an equipment in a chemical bath or cleaning solution. It is effective in removing residues, coke deposits, incrustations and other contaminants. The solution used varies depending on the type of dirt and equipment material, including alkaline, acid, solvent or specialized detergent solutions. Immersion allows deep and uniform cleaning of complex and difficult to access surfaces.
Air cleaning: Involves the use of compressed air to remove loose particles and dust from equipment surfaces, it is a preliminary step in various cleaning procedures, preparing the equipment for more intensive cleaning methods. It is also used in industrial collectors, for cleaning the filter box, thus avoiding filter saturation.
Mechanical cleaning: Used to remove solid particles, hard incrustations, residues and other types of physical contamination that require cleaning methods where physical force is applied during the process. Such is the case of mechanical pigging where a tool called pigs is used to remove and eliminate coke and carbon deposits from inside the pipes.
Special cleaning: Special cleaning encompasses techniques such as ultrasonic, cryogenic and foam cleaning. These methods require specialized knowledge and equipment, but offer specific cleaning solutions. Figure 2 shows the application of one of these types of cleaning for heat exchanger tubes.
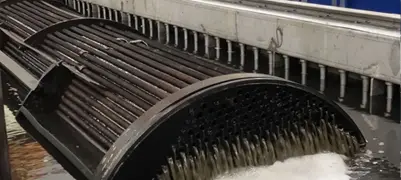
Many process equipment cleaning operations involve the combination of two or more types of equipment cleaning to obtain the required result; as in the case of ovens where a high temperature steam-air mixture is applied to decarbonize the ducts and pipes, this process removes coke and carbon deposits from the internal area of the pipes.
Implementing appropriate products and practices during this process, complying with operational specifications and predetermined processes, ensures the effectiveness of the cleaning for the specific objectives established.
Cleaning technologies
For the cleaning of the convection section of combustion heaters, a robotic technology was developed by the company Tube Tech3, to achieve a cleaning where these equipments reach their maximum performance. Due to their configuration, this equipment is difficult to clean, as most traditional cleaning methods do not reach the total area to be cleaned. Access to clean the deep and between the banks of finned pipe rows was not achieved as it was until now.
This robotic cleaning technology can deep clean between rows of convection tubes with square and triangular arrangement, obtaining a high level of cleanliness and improved cleaning time. This type of robotic cleaning technology replaces traditional cleaning techniques including: chemical cleaning, water pressure washing, abrasive blasting and dry ice blasting, because it can remove extremely hard deposits deep inside each row of pipes and also provide inspection reports before, during and after cleaning.3 .
Below is a video on robot cleaning technology, courtesy of Tube Tech International.
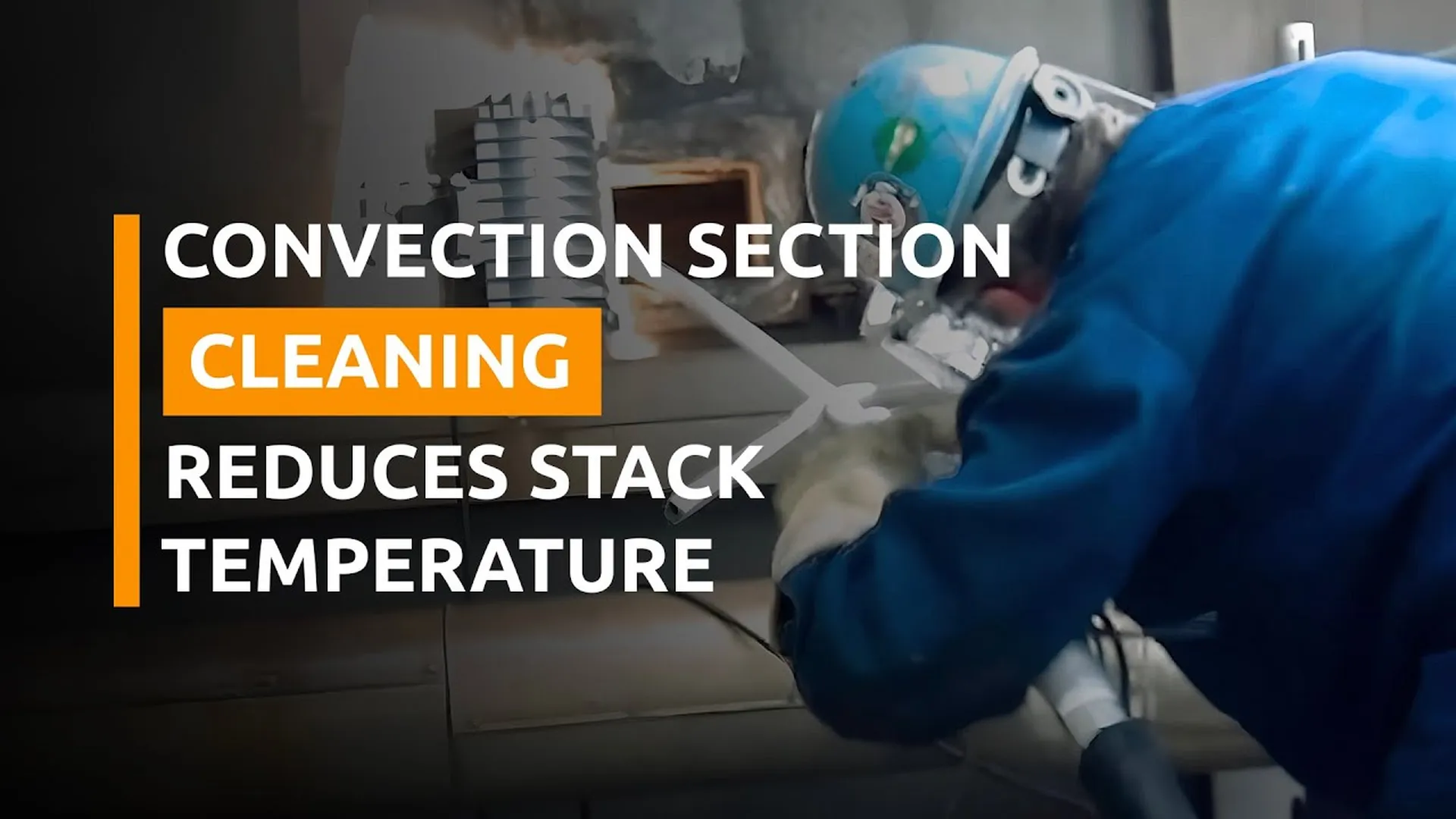
Limpieza de la sección de convección de calentadores de combustión/hornos de Tube Tech.
The same company has improved its cleaning technologies with the recent launch of the Rover Mark 7 system, an innovative robot for cleaning the convection area of heaters4, which is capable of remotely removing more than 90% of the fouling found in this area. Developed in the United Kingdom, this system has two patents, including a wheel system and a deflector and traverse system, which allow it to crawl on and through intermediate pipe support plates.
The new automated Rover uses Lidar technology to detect distances and detect blockages or obstructions. Live HD images provide the operator with real-time feedback, as well as the ability to use images and video for reporting and analysis4.
Safety measures
Process equipment cleaning methods typically present numerous hazards to the personnel involved and the facility. The hazards vary depending on whether the activity is performed with the plant in service, during a shutdown, on site or in workshops, but in general there are potential fire and explosion hazards due to flammable gases evolved during operations, reactions between certain process residues and cleaning chemicals.
Other potential hazards include falls and bodily injuries caused by improper use of equipment and tools, exposure to toxic gases and chemicals, which are deployed during cleaning operations. In the context of plant operations, it is necessary to adopt adequate safety measures to minimize the possibility of incidents during or arising from cleaning activities.
The multiple security measures must be constantly reviewed and updated by the personnel involved prior to the start of any activity. There is no inherent reason why the cleaning of process equipment should be any less safe than any other maintenance operation.
Conclusion
The cleaning of process equipment in refining plants is a necessary operation that goes beyond the simple elimination of residues; it is a practice that improves the operational efficiency of the systems, allows the integral inspection of the equipment, maintains quality standards in the refined products and generates safety in the work environment.
As the industry continues to evolve, the implementation of effective and safe process equipment cleaning practices, supported by advanced technology, will remain a necessary requirement for the success and sustainability of refining operations.
References
- IGS; “Increasing Furnace Efficiency With Hot Convection Cleaning”; https://integratedglobal.com/case_studies/increasing-furnace-efficiency-with-hot-convection-cleaning/; accessed 20 February 2024.
- Clean As New; https://cleanasnew.com/faq, accessed 20 February 2024.
- Tube Tech International; https://www.youtube.com/watch?v=mNM50U_kKWo; accessed 18 February 2024
- IGS “Tube Tech Launches Mark 7 Convection Section Cleaning Rover”; https://integratedglobal.com/igs-tube-tech-launches-convection-section-cleaning-rover/