Quality assurance in the manufacture of pressure vessels is an important process to ensure safety, reliability, and compliance with industry standards. Pressure vessels, which are used to store gases or liquids under high pressure, are subject to strict regulations due to the potential risks associated with their failure.
This article outlines various strategies for quality assurance in the pressure vessel manufacturing process, covering aspects from design and material selection to inspection and testing.
Comprehensive design and engineering
Compliance with Standards and Codes: Why ASME is so significant for pressure vessel manufacturing?
The first step in quality assurance is to ensure that the pressure vessel design complies with recognized standards and codes. Organizations such as the American Society of Mechanical Engineers (ASME) provide guidelines that dictate the design, materials, construction, and testing of pressure vessels. Compliance with these standards ensures that the vessel can withstand the pressures for which it is designed and reduces the risk of failure.
Specifically, Section VIII, describes the rigorous guidelines covering the design, fabrication, inspection, and testing processes that pressure vessels must undergo before they are considered safe1.
Engineering analysis
A thorough engineering analysis is essential to identify potential failure points and optimize the design. This includes Finite Element Analysis to simulate stresses and strains under operational conditions. By understanding the mechanical behavior of the vessel, engineers can make informed decisions to improve its strength and durability.
Material selection and certification
The selection and certification of the right material in the manufacture of products, as well as the right choice of materials, improves the performance, durability, and sustainability of a product. They offer specific properties that are ideal for certain applications. On the other hand, choosing the wrong materials can lead to performance problems, premature failure, and negative environmental effects.
Choosing the right materials
Material selection is significant in the integrity of pressure vessels, so that they can withstand high pressures, temperatures, and corrosive environments. Common materials include carbon steel, stainless steel, and various alloys.
The choice depends on the specific application and operating conditions. The selection of materials in the manufacture of pressure vessels is a critical factor that directly influences their durability, performance, and suitability for specific applications1.
Certification of materials
To ensure the quality of materials, manufacturers must obtain materials from certified suppliers and require material test reports. These reports provide detailed information on the chemical composition and mechanical properties of materials, ensuring that they meet the required specifications.
Specialized manufacturing processes
Welding procedures
Welding is the process used in the manufacture of pressure vessels, whereby high-quality welds are ensured by making use of qualified welding procedures and using certified welders.
Pressure vessel welds must meet code requirements and specific inspections, and they must be free of defects. The more weld passes required, the more difficult it is to make each pass look perfect. There is also a greater chance of defects requiring rework.
Rework and associated downtime costs time and money, and excessive failed welds could cause a fabrication shop to lose its ASME U certification.
This stamp certifies that the shop produces pressure vessels that meet ASME2 guidelines.
Precision machining and assembly
Precision machining and assembly are necessary to achieve the required tolerances and fit of components. Advanced machining techniques and quality control measures must be implemented to avoid deviations that could compromise the integrity of the vessel.
Rigorous inspection and testing
Non Destructive Testing (NDT)
NDT methods are used to inspect the integrity of pressure vessels without causing damage. Common NDT methods include:
- Radiography (RT) testing: Uses X-rays or gamma rays to detect internal defects.
- Ultrasonic Testing (UT): Uses high-frequency sound waves to identify flaws.
- Magnetic Particle Testing (MT): Detects surface and near-surface defects in ferromagnetic materials by applying a magnetic field and ferrous magnetic particles.
- Liquid Penetrant Testing (PT): Reveals surface cracks and porosity in non-porous materials by applying high capillary liquids with dyes for better detection.
Hydrostatic and pneumatic tests
Pressure vessels are subjected to hydrostatic and Pneumatic tests to verify their resistance and tightness. This type of test consists of filling with pressurized water to a level above its operating pressure. Pneumatic tests use air or inert gases and are performed at lower pressures because of the potential dangers due to the enormous energy that can build up in the system, where a sudden failure can cause a huge explosion.
The following video shows hydrostatic testing and Pneumatic, a procedure designed to test the strength and leakage of piping systems, boilers, gas cylinders pressure vessels etc. to confirm that they will function correctly, even under extreme conditions. Tests are also required after repairs and shutdowns to validate whether the equipment/piping can be successfully returned to operation. Source: PIPING MANTRA Platform.
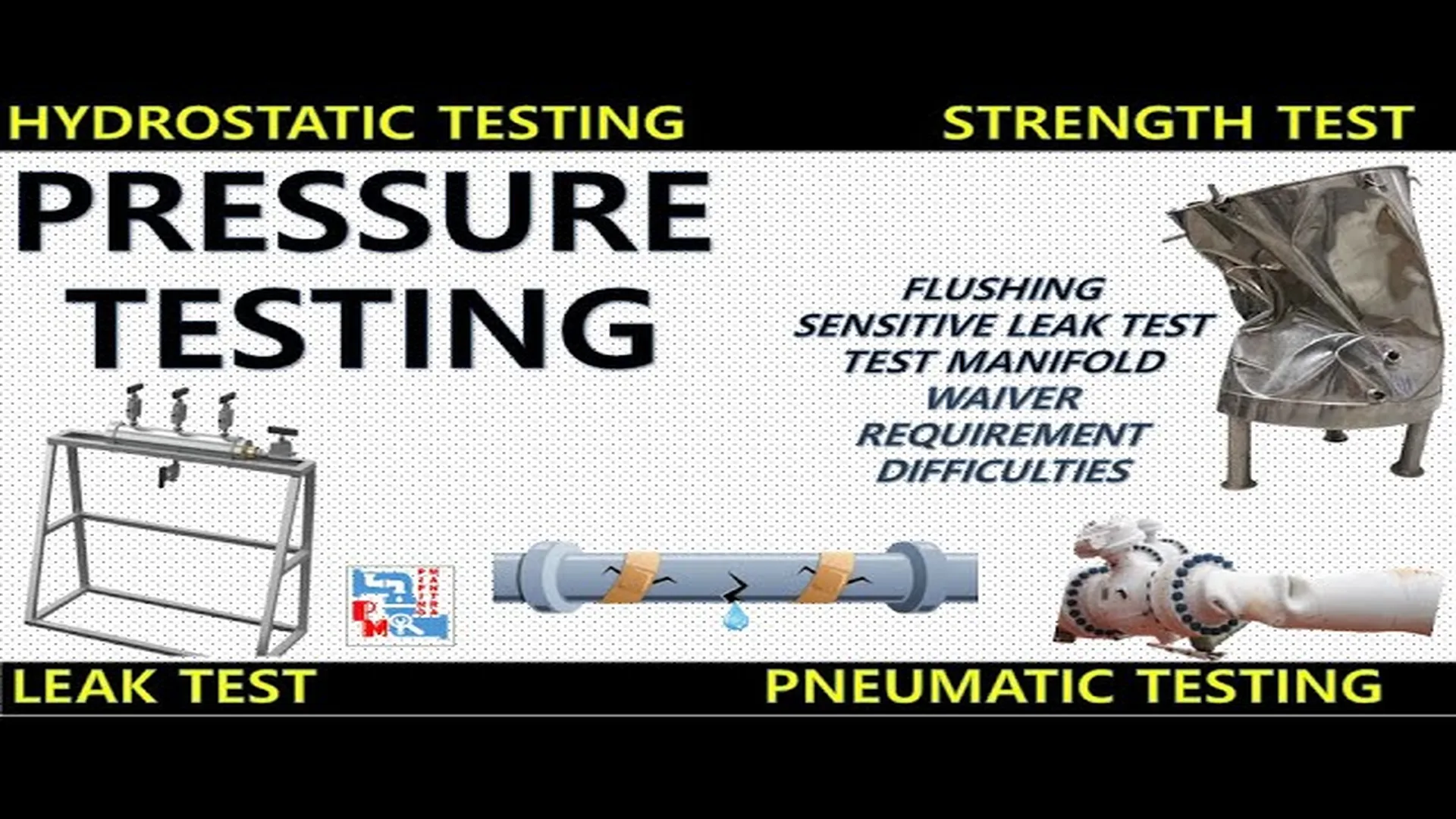
Procedure for testing resistance and leakage in pressure vessel systems.
Quality control documentation
Quality Assurance Plan (QAP)
A QAP describes the procedures and responsibilities for quality assurance throughout the manufacturing process. It includes details on design verification, material inspection, manufacturing methods, and test protocols. Adherence to the CAP ensures a systematic approach to quality assurance.
Traceability and record-keeping
Maintaining detailed records and traceability of materials, processes, and inspections is essential. This documentation helps identify the root causes of any problems and facilitates compliance with regulatory requirements. It also provides a basis for continuous improvement.
ASME Stamp
Following the rules and standards set by the ASME Code ensures the highest quality, integrity, and reliability of pressure vessels under this code, which gives customers peace of mind when purchasing a reliable and safe product, guaranteed in writing.
Upon successful completion of all requirements, pressure vessels receive an ASME stamp, which serves as a clear indicator of ASME BPVC compliance. The specific type of stamp, such as U-Stamp or R-Stamp, depends on the intended application and use of the vessel3.
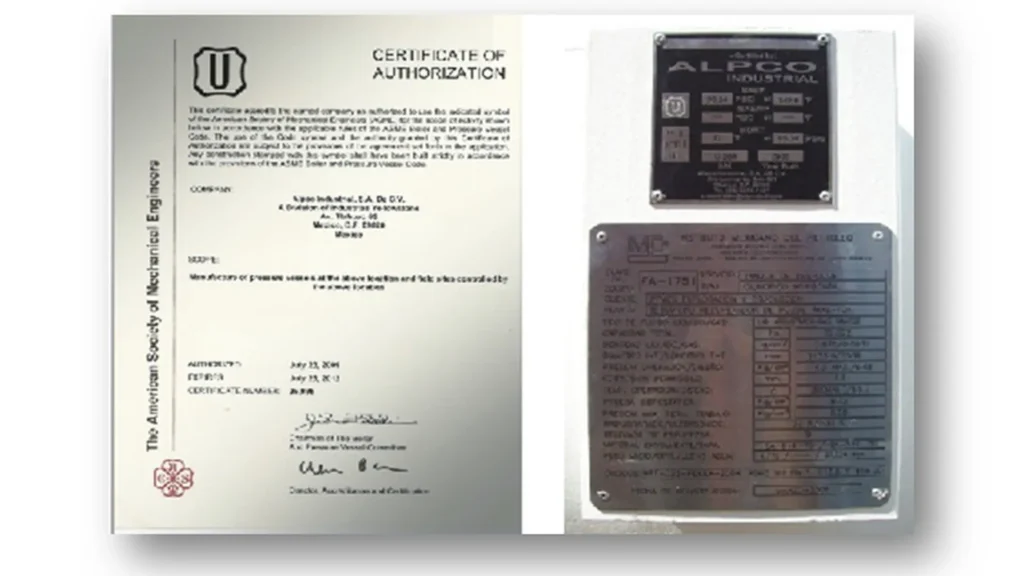
Upon successful compliance with all requirements, pressure vessels receive an ASME stamp; which clearly indicates compliance with the ASME Boiler and Pressure Vessel Code ASME Boiler and Pressure Vessel Code (BPVC). The specific type of stamp mark, such as U-Stamp or R-Stamp, depends on the intended application and use of the vessel.
Continuous improvement and training
Employee training and certification
Continuous training and certification of employees involved in the manufacturing process is crucial. This ensures that they are up to date with the latest standards, techniques, and safety practices. Trained and knowledgeable personnel are better equipped to maintain high-quality standards.
Personnel qualification and certification processes include personnel performing welding, non-destructive testing, weld inspection, and assembly process monitoring, among others.
Implementation of lean manufacturing principles
Lean manufacturing principles focus on reducing waste, improving efficiency, and improving product quality. By adopting lean practices, manufacturers can optimize processes, minimize defects, and deliver high-quality pressure vessels.
Stakeholder collaboration
Supplier quality management
Establishing strong relationships with suppliers and ensuring they meet quality standards is vital. Regular audits and performance assessments help maintain the quality of materials and components supplied.
Customer feedback and compliance
Engaging with customers to understand their requirements and feedback is important for continuous improvement. Ensuring compliance with customer specifications and regulatory standards builds trust and enhances the reputation of the manufacturer.
Conclusions
Quality assurance in pressure vessel manufacturing is a multifaceted process that requires meticulous attention to detail at every stage. From design and material selection to manufacturing and testing, each step plays a crucial role in ensuring the safety and reliability of the final product.
By implementing comprehensive quality assurance strategies, manufacturers can meet regulatory standards, satisfy customer requirements, and mitigate the risks associated with pressure vessel failures. Continuous improvement, employee training, and collaboration with stakeholders are essential components of a robust quality assurance program that ensures the production of high-quality pressure vessels.
References
- BAKER INDUSTRIES. Pressure Vessel Fabrication Process: Compliance Standards and Design Best Practices; Accessed 11 June 2024.
- DAVID JESCOVITCH, JOHN LIMBERIS. Multiple Pass Welding on Pressure Vessels Requires Proper Preparation and Cleaning; Accessed 12 June 2024. https://mexico.weilerabrasives.com/La-soldadura-de-pases-multiples-en-recipientes-a-presion-requiere-una-preparacion-y-limpieza-adecuadas.
- ACCRE SURVEYING SOLUTIONS. Pipeline inspection with the Sniffer4D drone gas detector; Accessed 12 June 2024. https://grupoacre.es/inspeccion-de-tuberias-con-el-detector-de-gas-para-dron-sniffer4d/.