Table of Contents
- Types of pressure tests
- Advantages and disadvantages of hydrostatic and pneumatic tests
- Equipment needed for pneumatic and hydrostatic tests
- Pressure gauge and its importance in pressure testing
- Test pressure and design pressure: Key concepts
- Safety in pressure testing
- Standards and regulations in pressure testing
- Specific considerations in Pneumatic Testing
- How pressure tests can prevent failures in piping and industrial equipment?
- Pressure test application and success story
- Conclusions
- References
Pressure testing is a fundamental procedure in the industry to ensure the integrity and safety of piping systems and equipment subjected to various operational conditions. These tests allow for the evaluation of a system’s ability to withstand internal pressures higher than normal operating conditions, identifying potential weaknesses, leaks, or defects that could compromise its functionality.
In an industrial environment, where pipes and equipment are exposed to extreme pressures, variable temperatures, and corrosive atmospheres, pressure testing becomes a crucial pillar for ensuring operational reliability. Without these tests, the risks of catastrophic failures, such as ruptures or explosions, significantly increase, potentially leading to substantial economic losses, environmental damage, and most importantly, serious risks to personnel safety.
There are several types of pressure tests, with the most common being the hydrostatic test and the pneumatic test. The hydrostatic test uses water as the medium to generate pressure and is widely used due to its ability to accurately detect leaks. On the other hand, the pneumatic test uses air or inert gases and is applied in situations where the use of liquids is impractical or dangerous. These tests not only verify the structural integrity of the systems but also comply with international standards and regulations that govern safety in the industry.
Types of pressure tests
There are several types of pressure tests designed to evaluate the integrity of industrial systems under different conditions. The two most common and recognized in the industry are the hydrostatic test and the pneumatic test, each with its own procedures, applications, and considerations.
Hydrostatic test
The hydrostatic test is one of the most used techniques to verify the integrity of piping systems and equipment that handle liquids. This type of test involves filling the system with a liquid, commonly water, and then applying pressure until it reaches a level higher than normal operation, generally 1.5 times the design pressure. The goal is to ensure that there are no leaks and that the structure can withstand the pressure without permanent deformations.
The procedure for a hydrostatic test includes purging air from the system, gradually applying pressure, and conducting visual or instrumented inspections to detect leaks. This test is preferred in many cases due to the relative safety of water compared to high-pressure gases and its ability to reveal small defects in joints, welds, and materials of the system.
Pneumatic test
The pneumatic test, on the other hand, uses air or inert gases as the testing medium instead of liquids. This type of test is generally conducted in situations where the presence of water is undesirable or impractical, such as in systems where corrosion is a concern or in components that cannot be completely drained after the test.
Since gases are compressible and can store large amounts of energy, the pneumatic test presents higher risks than the hydrostatic test, especially if a system failure occurs. Therefore, additional precautions must be taken, such as using pressure relief devices and implementing safety zones for personnel. Despite these risks, the pneumatic test is indispensable in specific situations where the use of liquids is not feasible and is widely used in the aerospace, automotive, and environmental control industries, among others.
Both tests are essential to guarantee the safety and operability of systems under pressure, and their correct execution is crucial for preventing failures and accidents in industrial environments.
Advantages and disadvantages of hydrostatic and pneumatic tests
Hydrostatic and pneumatic tests have specific advantages and disadvantages that must be considered when choosing the appropriate method for evaluating the integrity of piping systems and equipment.
Advantages of the hydrostatic test
- Safety: Uses water, a virtually incompressible fluid, which minimizes the risk of explosions in case of failure.
- Leak detection: Highly effective for detecting small leaks since water does not compress, allowing for a precise evaluation of the system’s integrity.
Disadvantages of the hydrostatic test
- Corrosion: Can introduce moisture into the system, potentially causing corrosion if not properly drained and dried.
- Difficulty of water removal: In complex systems, it may be challenging to completely remove water after the test.
Advantages of the pneumatic test
- No introduction of moisture: Ideal for systems that should not come into contact with liquids, preventing corrosion.
- Ease of drying: Does not require extensive drying processes after the test, which is useful in certain systems.
Disadvantages of the pneumatic test
- Higher risk: Due to the compressibility of the gas, any failure can release large amounts of energy, increasing the risk of explosions.
- Increased precaution: Requires additional safety measures and stricter supervision due to the risks involved.
Equipment needed for pneumatic and hydrostatic tests
Pressure tests, both pneumatic and hydrostatic, require a series of specialized equipment to ensure the safety and precision of the procedure. This equipment is essential for applying, measuring, and controlling the pressure during the test, ensuring that the system can withstand the required operating conditions.
Equipment for hydrostatic tests
To conduct a hydrostatic test, the key equipment includes high-pressure pumps, pressure gauges, water storage tanks, and relief valves.
- High-pressure pumps: These are used to inject water into the system at the required pressure. They must be capable of generating pressure higher than the system’s design pressure to simulate extreme conditions.
- Pressure gauges: These instruments measure the pressure applied within the system and are essential for monitoring and recording pressure values during the test.
- Water storage tanks: Necessary to provide a clean water source in sufficient quantity to fill the system without interruptions.
- Relief valves: These are safety devices that automatically release excess pressure to prevent damage to the system during the test.
Equipment for pneumatic tests
In pneumatic tests, the essential equipment includes air compressors, pressure gauges, pressure regulators, and safety devices.
- Compressors: Responsible for supplying high-pressure air or inert gas to the system, and they must be capable of maintaining a constant flow during the test.
- Pressure gauges: Just like in hydrostatic tests, they are crucial for measuring and verifying that the pressure achieved corresponds to the test specification.
- Pressure regulators: These devices control the pressure supplied to the system, ensuring it does not exceed safe limits.
- Safety devices: Include safety valves and other mechanisms designed to protect the equipment and personnel in case of a sudden pressure release.
Pressure gauge and its importance in pressure testing
The pressure gauge is a critical component in any pressure test, as its main function is to measure and monitor the pressure applied within a closed system. During a pressure test, the accuracy of the pressure gauge is essential to ensure that the applied pressure meets the specified requirements and that the system can handle the simulated conditions without failures.
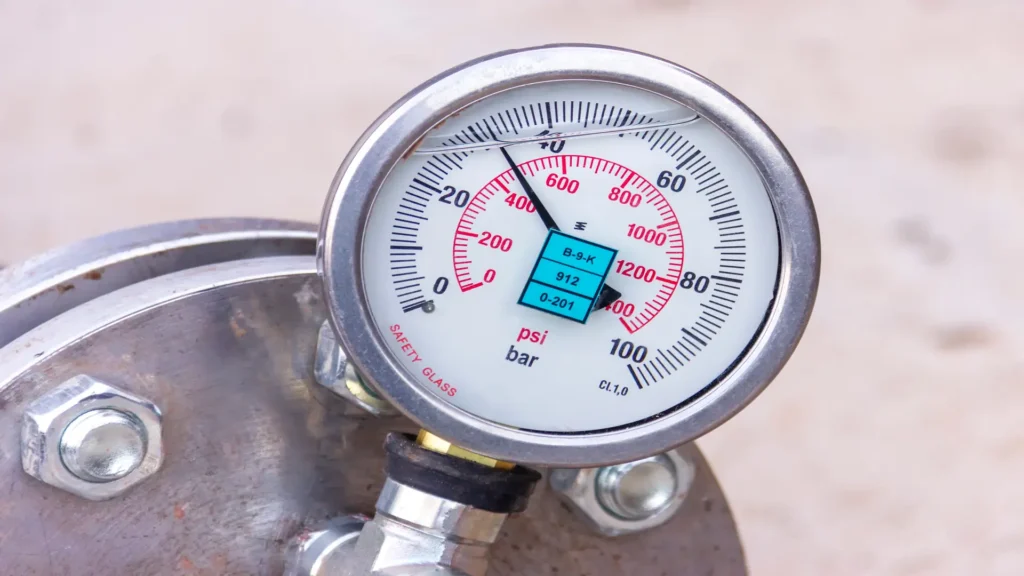
The pressure gauge works by measuring the force exerted by the fluid or gas over a specified area within the system, typically expressed in units such as bar, psi, or pascal. The gauge reading allows operators to adjust the applied pressure in real-time and ensure that safety limits are not exceeded, which is crucial to prevent damage to the system or possible accidents.
When selecting a pressure gauge, it is important to consider factors such as pressure range, instrument accuracy, and compatibility with the fluid or gas used. Pressure gauges should be calibrated regularly to maintain their accuracy, and it is recommended to use gauges with a clear and legible scale to facilitate data interpretation during the test.
Test pressure and design pressure: Key concepts
Test pressure and design pressure are two fundamental concepts in conducting pressure tests. Both are used to ensure that piping systems and equipment can operate safely under the pressure conditions they will encounter in their daily use.
Test pressure refers to the pressure to which a system is subjected during a pressure test, which is generally higher than the normal operating pressure to provide a safety margin. This pressure is applied to verify that the system does not present leaks or structural failures under extreme conditions. Test pressure is crucial because it ensures that the equipment can withstand pressures higher than those encountered during operation, providing an additional layer of safety.
On the other hand, design pressure is the maximum pressure a system is designed to withstand during normal operation. This value is determined during the engineering and design stage of the system, considering factors such as construction material, type of fluid or gas, and expected operating conditions. Design pressure is a critical parameter that guides not only the construction of the equipment but also the tests and certifications necessary to ensure its safety and performance.
In summary, test pressure verifies that the system can operate safely under design pressure and other more extreme conditions, ensuring the integrity of the equipment in its operational environment.
Safety in pressure testing
Safety in pressure testing is a critical aspect that cannot be underestimated, given the hazardous nature of the conditions under which these tests are conducted. The risks associated with pressure testing include the possibility of explosions, equipment ruptures, sudden energy release, and exposure to high-pressure fluids or gases, which can result in serious injuries or even fatalities.
To minimize these risks, it is essential to follow strict standards and recommended practices. Among the most recognized international standards are those from ASME (American Society of Mechanical Engineers) and API (American Petroleum Institute), which provide specific guidelines for the safe execution of pressure tests. Key practices include the proper calibration of pressure gauges, the use of pressure relief devices, and the implementation of exclusion zones for unauthorized personnel during the test.
Additionally, it is crucial to perform detailed pre-inspections of the system to be tested to identify potential weak points and use effective communication methods to coordinate the procedure among all involved parties. Training personnel in risk identification and management is also crucial to ensure that pressure tests are carried out without incidents.
Standards and regulations in pressure testing
Pressure testing standards are designed to ensure that these procedures are conducted safely and effectively, complying with international and local standards that regulate the integrity of piping systems and industrial equipment. These standards are vital for ensuring that the tests are executed according to best practices and that the results are reliable.
Among the relevant regulations are the ASME BPVC (Boiler and Pressure Vessel Code) standards, which offer a comprehensive framework for the construction, inspection, and testing of pressure vessels and piping. Additionally, API 510 (Pressure Vessel Inspection Code) and API 570 (Piping Inspection Code) provide specific guidelines for the inspection and testing of piping and equipment, ensuring they meet safety and performance requirements.
Compliance requirements include the certification of equipment and procedures, detailed documentation of test results, and ensuring that the tests are conducted by qualified personnel. Companies must strictly adhere to these regulations to avoid legal sanctions, ensure the integrity of the equipment, and protect the safety of personnel and the environment.
Specific considerations in Pneumatic Testing
Pneumatic tests require special attention due to the use of compressed gases, which present higher risks compared to liquids, such as greater accumulated energy and the potential for explosion in case of failure.
It is crucial to take special precautions such as the use of pressure relief valves to control pressure, the implementation of safety barriers to protect personnel, and ensuring that the entire procedure is supervised by highly trained personnel. These measures are fundamental to minimizing the associated risks and ensuring that the test is conducted safely and effectively.
How pressure tests can prevent failures in piping and industrial equipment?
Pressure tests are essential to prevent failures in piping and industrial equipment by identifying structural weaknesses, leaks, and defects in joints before the system enters operation. For example, a hydrostatic test can reveal small leaks in welds or joints that, if not detected, could cause ruptures or explosions under operating conditions. Similarly, a pneumatic test can detect failures in systems where the presence of liquids is undesirable. These tests are crucial to avoiding catastrophic accidents and ensuring structural integrity, protecting both people and industrial infrastructure.
Pressure test application and success story
Acuren’s success story on a 100-mile (160 km) pipeline exemplifies the importance of pressure testing to ensure structural integrity and restore Maximum Operating Pressure (MOP). The process began by purging and depressurizing the line with nitrogen, allowing the execution of cuts and replacements in critical sections.
Subsequently, a pressure test was performed on a thick-walled pipe at 3500 psig. Once the integrity was validated, the pipe was reconnected and filled with water, incorporating dye gas and leak detection tracer. Given the high level of pressure involved in this type of inspection, it is critical to define what procedure should be executed for high pressure leaks, ensuring that any anomalies detected can be safely managed.
A thermal stabilization was implemented prior to running the main hydrostatic test at 1700 psig, followed by a 4-hour verification test and a 4-hour leak test. Upon successful completion, the system was drained through charcoal filters, dried with methanol and finally charged with product. This case highlights the importance of careful planning, regulatory compliance and the application of advanced methodologies in the assessment of critical infrastructure in the hydrocarbon industry.
Conclusions
Pressure tests, both hydrostatic and pneumatic, are significant to ensure safety and efficiency in industrial systems under pressure. These tests allow early detection of failures, to prevent accidents, protect infrastructure and safeguard human life. Each type of test has its advantages and disadvantages, and the choice of the appropriate method depends on the specific characteristics of the system and the risks involved.
Implementing appropriate equipment, following strict standards, and adopting rigorous safety practices are essential for effective pressure testing. These tests ensure regulatory compliance, and reinforce confidence in the integrity of industrial systems, preventing failures and ensuring safe and reliable operation in challenging environments.
Perform pressure tests with accuracy and regularity, and ensure the integrity of equipment and pipelines under extreme conditions without compromising safety.
References
Own source