The goal of this article is to compare plasma cutting with other cutting methods by analyzing their efficiency, precision, and industrial applications. This analysis aims to highlight the advantages and disadvantages of each method, enabling professionals to select the most suitable option based on specific project requirements.
The importance of this topic lies in how the choice of cutting method impacts surface finish quality, cutting precision, and operational efficiency. Plasma cutting, laser cutting, and mechanical methods have substantial differences in terms of material penetration capabilities, edge control, tolerances, and operating and maintenance costs. Understanding these aspects is key to optimizing performance and minimizing costs in complex industrial processes.
Principle of plasma cutting operation
Plasma cutting is a thermal cutting method that uses a high-temperature ionized gas (plasma) to melt and remove material from a metal object. The process starts by generating an electric arc between an electrode and the metal to be cut, which raises the gas (such as air, argon, or nitrogen) to ionization temperature, turning it into plasma. This plasma reaches temperatures of up to 20,000°C, allowing fast cuts on conductive materials like steel and aluminum. The ionized gas expels the molten metal at high speed, resulting in a quick and efficient cut.
In terms of cutting precision and efficiency, plasma cutting is faster on thick materials than other methods, such as mechanical Cutting, and offers a good cost-benefit ratio compared to laser cutting. However, its precision is slightly lower than that of laser cutting, making it more suitable for rapid cuts with less emphasis on fine finishes. This method is ideal in high-demand industrial applications, such as heavy machinery manufacturing or metal structures.
If you want to learn how plasma cutting works, I invite you to watch the following video. Courtesy of: Hypertherm Asia Pacific.
Comparison of cutting methods: Plasma cutting, laser cutting, and mechanical cutting
- Plasma cutting: Is highly efficient for thick materials, especially conductive metals such as steel, aluminum, and copper. This method uses a jet of ionized gas reaching high temperatures, enabling quick cuts without requiring high pressures or prolonged processing times. In terms of edge quality and cutting tolerance, plasma offers good results, although it is less precise than laser cutting for fine finishes. Tolerance is acceptable for most industrial applications that require speed over extreme precision. However, it is more limited in fine details and high-quality finishes.
- Laser cutting: This is the preferred method when high precision and quality surface finish are required for thin and moderately thick materials. This method uses a concentrated laser beam to achieve very fine, detailed cuts. The result is a clean and precise edge, ideal for applications that demand high-quality standards, such as electronic components or delicate parts in precision industries. However, operational and maintenance costs are higher than plasma and mechanical cutting due to advanced equipment technology and the need for high-purity gases.
- Mechanical cutting (saw, shear): Like saws and shears, are traditional techniques still used in specific applications due to their simplicity and low operational cost. They are effective for thin materials or low-precision applications where speed and surface finish are not critical. However, compared to thermal cutting methods, mechanical methods have significant limitations in terms of precision, speed, and versatility. Although their use has decreased with thermal technologies’ evolution, they are still suitable for sectors like construction and non-conductive material cutting operations.
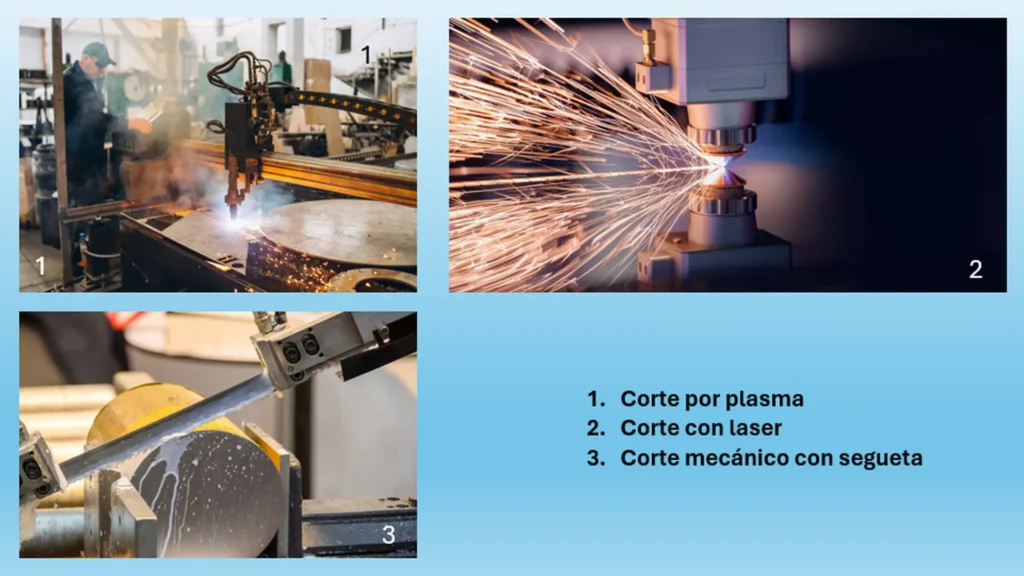
Advantages of plasma cutting compared to other methods
Plasma cutting offers several advantages in speed and efficiency over other methods. Compared to mechanical cutting (such as saws and shears), plasma enables much faster cuts, especially on thick materials, significantly reducing processing time. In addition, compared to laser cutting, plasma cutting is less expensive to operate and maintain. It does not require high-purity gases or such specific spare parts, which lowers operating costs.
Another advantage is its versatility in industrial applications. Unlike lasers, which work best on thin and uniform materials, plasma cutting does not depend heavily on conductivity or material thickness. This feature allows it to cut a wide range of metals and thicknesses, from thick sheets to complex structures, making it an ideal choice for industries like automotive, construction, and heavy machinery.
Analysis of precision and edge quality
Laser cutting is the most precise method for industrial applications requiring fine cuts and strict tolerances. Its concentrated laser beam allows detailed cuts with clean, uniform edges, which is essential in sectors demanding high precision, such as electronics and automotive component manufacturing.
- Surface finish quality and burrs: Laser cutting provides superior surface finish quality, often without visible burrs, reducing the need for post-processing. In comparison, plasma cutting, although effective and fast, can produce some burrs on the edges, especially on thicker materials, which may require additional finishing to achieve a clean edge.
- Tolerances and cut consistency: Laser cutting maintains tighter tolerances and greater consistency in cuts, making it ideal for applications requiring repeatable precision. While plasma cutting has slightly wider tolerances, it is still suitable for applications where extreme precision is not a priority, such as metal structure construction. In these cases, plasma’s speed and efficiency outweigh the need for strict tolerances, making it ideal for high-demand industrial environments.
Use cases and selection of cutting method
In general industrial applications, the selection of the cutting method depends on factors such as material type, thickness, operating cost, and required precision. For thick materials, especially conductive metals like steel and aluminum, plasma cutting is an effective option due to its speed and ability to cut thick parts. In contrast, for thin materials or pieces requiring fine, detailed finishes, such as precision components in sectors like electronics or automotive, laser cutting is preferred for its ability to achieve clean edges and tight tolerances. On the other hand, mechanical cutting, although more limited in precision, remains a viable option for straight cuts on sheets and materials where cost efficiency is crucial, such as support and structural manufacturing.
In the Oil & Gas sector, cutting methods are also chosen based on the need for resistance and precision under extreme conditions. For example, plasma cutting is frequently used for high-resistance pipelines and oil and gas transportation systems, where speed and on-site cutting capability are essential. For high-precision components, such as valves and flow systems in refineries, laser cutting ensures quality and precision finishes. In constructing supports and mounting platforms, mechanical cutting is suitable for its simplicity and low cost, ideal for structural support components on platforms and refineries.
Conclusions
Choosing the appropriate cutting method is crucial for optimizing both precision and operational efficiency in industrial settings. Each technique—plasma, laser, and mechanical cutting offers unique advantages tailored to specific needs. Plasma cutting stands out in high-thickness and high-demand applications, where speed and low operational cost are priorities. In turn, laser cutting is unbeatable in precision and finish quality, ideal for parts requiring strict tolerances. Finally, mechanical cutting remains a viable option in low-precision operations, providing reliability and economy for support structures.
In the Oil & Gas sector, the importance of these methods is even greater. From high-resistance pipelines cut with plasma to precision components processed with lasers, each technique helps ensure critical systems’ integrity and durability. Understanding each method’s characteristics and limitations allows professionals to make informed decisions, maximizing efficiency, reducing costs, and ensuring performance in complex and demanding projects.
References
Own source