Introduction
In the dynamics of the energy sector, plant shutdowns in the oil industry represent one of the most critical events for operators, as they can impact both operational efficiency and profitability of production facilities. Effective management of these shutdowns is not merely a maintenance issue but an economic strategy that can determine the long-term financial success of a company.
This article analyzes the economic impact of plant shutdowns in the oil industry, covering both scheduled and unscheduled shutdowns and the strategic importance in directing plant shutdown projects and maintenance programs.
What are plant shutdowns in the oil industry?
An industrial shutdown, also known as a plant shutdown, is a planned and scheduled process where production in an industrial facility is completely halted to perform maintenance, repairs, inspections, modifications, or improvements on plant equipment, machinery, and systems.
Types of plant shutdowns
Unscheduled shutdowns
In the industry, especially in oil and gas, these are critical situations that can significantly impact production, safety, and profitability. These interruptions occur unexpectedly and can be caused by a variety of reasons, such as:
- Mechanical failures: (e.g., pump deterioration in a refining installation causing automatic system shutdown)
- Human errors: Incorrect handling of tools or equipment by an operator leading to emergency plant shutdowns.
- Software failures: Problems in computer programs or software systems triggering undesired outcomes in process control.
- Natural disasters: Natural events such as hurricanes and earthquakes.
Scheduled shutdowns
Unlike emergencies, scheduled shutdowns are planned in advance and are part of regular maintenance planning. These shutdowns allow the plant to perform essential upgrades and preventive maintenance without compromising safety and continuous production, such as:
- Technological upgrades: Scheduled installation of new technologies to enhance plant efficiency. The following video shows the replacement of coke drums at the Petrobrazi refinery. Courtesy of OMV Petrom, the largest integrated energy producer in Southeast Europe.
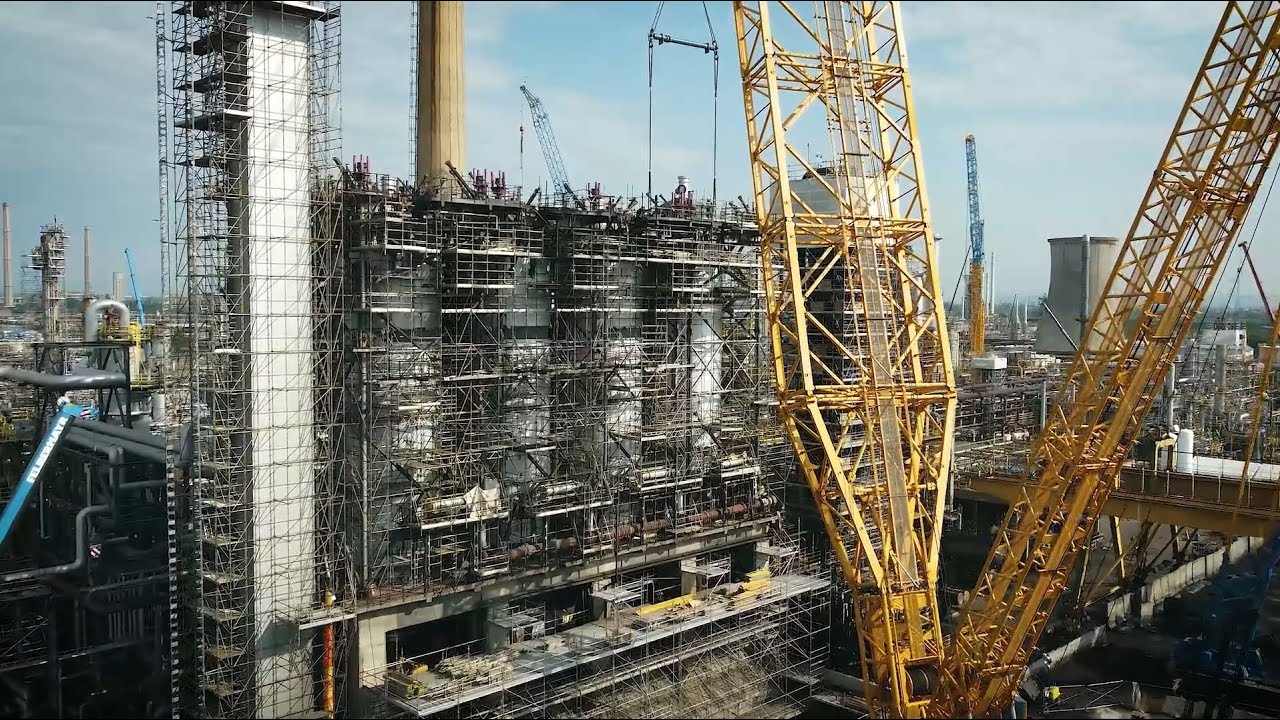
Coke drums replacement at Petrobrazi Refinery.
- Preventive maintenance: Scheduling shutdowns for boiler inspection and repairs to prevent unexpected failures and ensure continuous, stable operation.
- Comprehensive review: Scheduling shutdowns for thorough inspections.
Economic impact of plant shutdowns
The economic impact of plant shutdowns in the industry, particularly in critical sectors like oil, is a fundamental aspect that requires meticulous attention in both planning and execution. These shutdowns, whether scheduled or unscheduled, incur significant costs but are essential for safe and efficient facility operation.
Below, we delve into the detailed economic impact of both and why, despite their costs, they are crucial for the industry.
Impact of unscheduled shutdowns
Typically resulting from unforeseen failures or accidents, these represent a considerable economic risk for any industrial operation. The associated costs of these interruptions are manifold and can be exorbitant:
- Production Loss: When a plant unexpectedly halts production, every hour of downtime equates to direct revenue loss. In the oil industry, where production can be valued in millions per day, these losses quickly accumulate. It’s estimated that the oil and gas sector faces around 27 unscheduled shutdowns annually, with each incident costing between $10 million and $50 million in direct and indirect losses.
- Additional operating costs: Emergency repairs are generally more expensive than scheduled maintenance due to the need for quick response. This can include emergency labor costs, premium-priced spare parts, and, in some cases, fines for non-compliance with environmental or safety regulations. A survey of industry leaders revealed that 70% of plants lack an effective plan to respond rapidly to an unscheduled shutdown, exacerbating cost and downtime duration.
- Long-term impact: Failures causing these shutdowns can also have long-term repercussions on machinery, reducing its lifespan or compromising future efficiency, leading to further maintenance expenses and potential new interruptions.
New technologies, such as predictive analytics and condition-based maintenance, are beginning to be used to anticipate failures before they occur and thus reduce the frequency of these shutdowns.
Impact of scheduled shutdowns
Scheduled shutdowns, though costly, are calculated investments aimed at preventing costly and disruptive incidents that can result from maintenance neglect.
The costs and benefits include:
Investment in maintenance and upgrades: Scheduled shutdowns require investment in human and material resources to carry out planned maintenance, upgrades, and repairs. These costs are significant but necessary for plant optimization.
Prevention of major issues: The cost of not conducting scheduled shutdowns can be devastating. Catastrophic failures in critical equipment are not only more expensive to repair but can also result in accidents, injuries, or severe environmental damage, leading to legal liabilities and damage to the company’s reputation.
Plants implementing rigorous preventive maintenance experience up to 30% fewer interruptions in their operations compared to those that only react to failures.
Benefits in the long term: While the onset of a plant shutdown entails a significant financial outlay, the implemented improvements and breakdown prevention lead to enhanced equipment performance and process efficiency. This results in reduced operating costs and sustained production increase over time. Below are some of these benefits:
- Enhancement of operational efficiency: One of the most significant advantages of scheduled shutdowns is the opportunity to enhance plant operational efficiency. During these shutdowns, adjustments, and improvements to equipment and systems can be made that would not be feasible during normal operations. This includes instrument calibration, software system updates, and installation of new, more efficient technologies. The following image shows the maintenance or replacement of the thermal insulation of the piping and heat exchangers, improving the efficiency of this equipment in heat transfer by performing a plant shutdown.
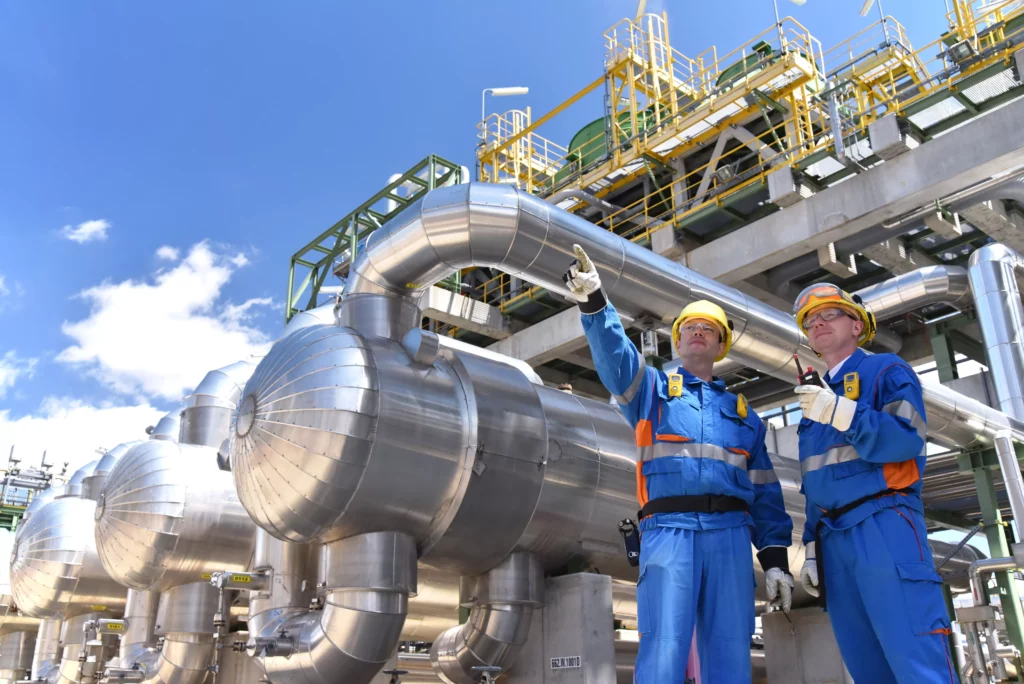
- Extension of equipment lifespan: Regular maintenance and scheduled repairs during plant shutdowns help extend the lifespan of critical equipment. Reviewing and repairing key components prevent accelerated deterioration that can result from continuous operation without proper maintenance. This not only helps avoid costly equipment replacements but also ensures that the plant can operate at full capacity without the risk of unexpected failures.
- Reduction of unscheduled downtime: By proactively identifying and addressing potential issues during a scheduled shutdown, the incidence of unscheduled downtime can be significantly reduced, which is much more disruptive and costly. Preventive maintenance and detailed inspections allow technicians to detect early signs of wear or failure, which can be rectified before they become major issues. This proactive approach to maintenance reduces unplanned downtime and improves overall plant reliability.
- Increased long-term profitability: Although scheduled shutdowns require an initial investment in terms of time and resources, the long-term profitability benefits are clear. With equipment operating more efficiently and reliably, and with fewer unexpected interruptions, the plant can maximize its production. Additionally, by reducing the frequency and severity of unscheduled shutdowns, significant costs associated with emergency repairs and production losses are saved. Increased operational stability also allows for better planning and optimization of operations, contributing to a more predictable and robust revenue stream.
Strategies to minimize the economic impact of plant shutdowns in the oil industry
The significance of plant shutdown project management and maintenance programs in the oil industry cannot be underestimated. These planned events are essential for maintaining facility functionality, safety, and efficiency, directly impacting long-term profitability and economic sustainability of businesses.
Effective plant shutdown project management
- Strategic planning: These plans should be aligned with immediate operational needs and long-term strategies, utilizing tools like Primavera P6 software or the CPM method to optimize times and resources.
- Coordination and execution: Effective planning during plant shutdown is crucial. This involves managing multidisciplinary teams, ensuring availability of materials and tools, and adhering to established schedules. Continuous communication across all organizational levels helps anticipate issues and adjust plans in real-time.
- Evaluation and continuous Improvement: After each plant shutdown, a thorough evaluation should be conducted to identify areas for improvement. This analysis helps refine future processes, maximize efficiency, and reduce costs. Lessons learned are vital for continuous improvement, enabling the company to better adapt to changing market and technological conditions.
Effective maintenance programs
- Well-designed preventive and predictive maintenance programs can help reduce the frequency and duration of unplanned plant shutdowns.
- These programs can extend asset lifespan and decrease long-term maintenance costs.
- Companies like ExxonMobil and Petrobras have successfully implemented maintenance programs resulting in significant downtime reduction and operational efficiency improvements.
By implementing effective plant shutdown project management and maintenance program strategies, oil companies can minimize the economic impact of plant shutdowns, enhance operational efficiency, and increase long-term profitability.
Conclusion
Plant shutdowns in the oil industry are a double-edged sword: essential for maintenance and safety, yet costly and disruptive. Effective management is not just about maintenance but a complex economic strategy that requires skill and foresight. Proper planning and efficient execution of shutdowns not only protect infrastructure and personnel but also maximize economic and operational efficiency.
Proper plant shutdown management directly impacts long-term profitability. By maximizing operational efficiency and reducing disruptions, companies can improve revenue flow and market position.
Well-designed plant shutdown project management and maintenance programs are essential. They encompass strategic planning, effective coordination during execution, and post-shutdown evaluation for continuous improvement. Leveraging advanced technologies like predictive analytics and condition-based maintenance can also reduce the frequency of unplanned shutdowns.
Discover how to optimize plant shutdowns today!
References
Own source