corrosion in pipes is some of the major challenges in the oil and gas process industries, causing unplanned shutdowns and limiting operational performance. It is important that operators monitor the risk of corrosion and erosion and its impact on the condition of assets.
Currently, companies offer a wide variety of cutting-edge equipment for measuring corrosion and erosion, in order to offer the best data for a comprehensive understanding of the risks of these phenomena. Operators use this data to make more informed decisions, thereby maximizing plant performance, safety and profitability.
It is a considerable industrial problem, because it can cause accidents (breakage of a piece) and, in addition, represents a relevant cost. Furthermore, it is estimated that every second five tons of steel are dissolved in the world, coming from a few nanometers or picometers, invisible in each piece, but which, multiplied by the amount of steel that exists in the world, constitutes a significant amount.
In this context, the most innovative technologies for monitoring corrosion in pipes in the industry will be addressed.
Technological innovations in pipe corrosion monitoring
1. High sensitivity ultrasonic technology
In the world of corrosion integrity, it is understandable that the key to effective corrosion control lies not only in monitoring, but also in the constant maintenance of equipment that provides important data to safeguard people and assets. In this sense, the internal corrosion monitoring equipment, developed by AXESS, has earned global recognition as the standard for excellence in internal corrosion control.
AXESS, a world leader in corrosion monitoring technology, offers the revolutionary SONOWALL 70 (figure 1), or its equivalent, which employs highly sensitive ultrasonic technology. This non-intrusive instrument provides continuous corrosion and erosion monitoring, setting the standard in precision and reliability1.
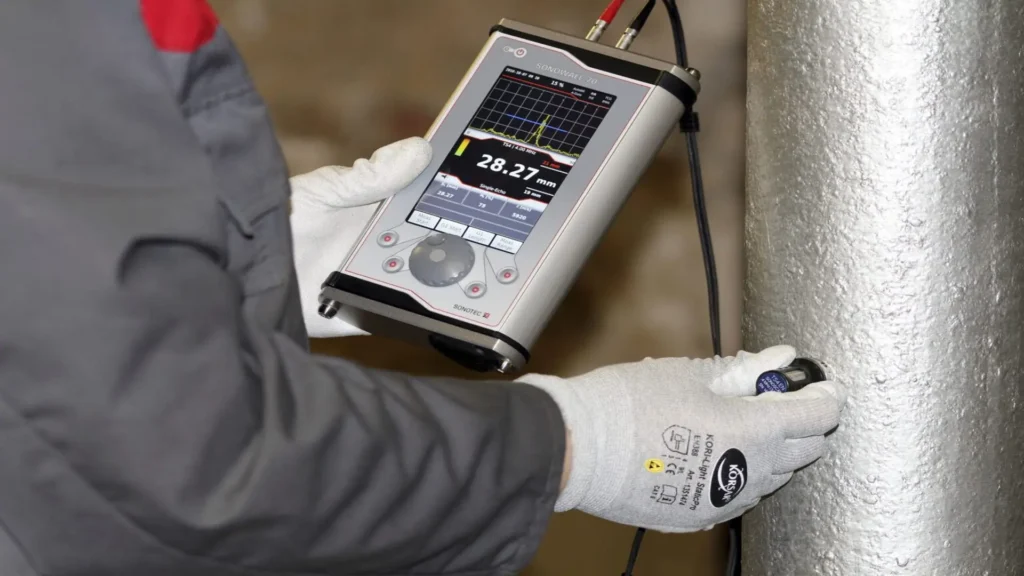
The versatility of the system allows the connection of several transducers from a single point, facilitating periodic measurements of wall thickness with the corresponding date and time, or for more critical applications. Additionally, the ability to automatically collect and store continuous measurements from a single transducer ensures detailed and effective monitoring.
Featured corrosion monitoring products from AXESS
- Environmental Corrosion Monitors: Designed to evaluate and record changes in environmental conditions that could affect corrosion.
- Corrosion rate probes: Provide accurate measurements of corrosion rate, allowing proactive intervention.
- Test tubes for measurement and abrasion of Fluids: Equipped to evaluate corrosion in environments with aggressive and abrasive fluids.
- Ultrasonic Thickness Measurement System: Uses advanced technology to accurately measure wall thickness, vital for corrosion assessment.
With a regular maintenance plan and consistent utilization of components and spare parts supplied by leaders in the field, internal corrosion monitoring equipment can be kept in operation for extended periods without interruptions in production. This approach not only ensures equipment durability, but promotes safer, more secure operations.
Advanced technology ensures a continued commitment to asset security and integrity. Research and innovation in corrosion monitoring advances towards a future where protection against corrosion becomes a solid guarantee.
2. Advanced corrosion measurement methods
In today’s industry, the importance of minimizing downtime and costs associated with repairs due to corrosion. For this reason, a complete line of specialized corrosion monitoring equipment, designed for a variety of materials and dimensions, is necessary.
This comprehensive range of instrumentation not only provides timely alerts on potential structural damage, but also enables detailed analysis of system corrosivity, identifying changes in process parameters and their effects on corrosive conditions2.
In the following video, the company MORKEN GROUP, specialized in the supply, shows us the installation of products for corrosion monitoring and chemical injection.
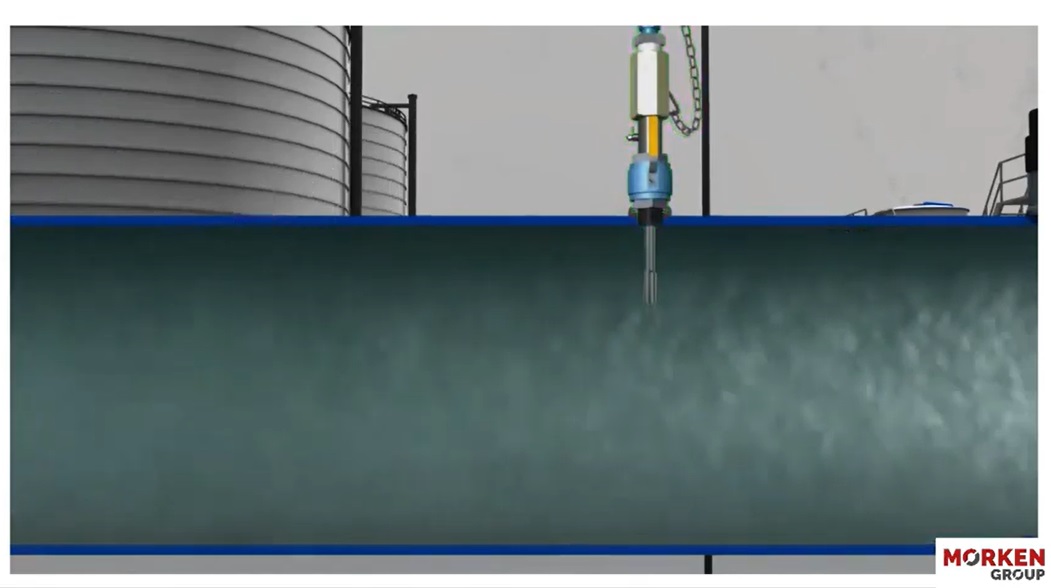
Monitoreo de la corrosión en tuberías.
Pipeline corrosion monitoring video courtesy of Morken Group2.
Electrical resistance test tubes and retractable coupons
They are used depending on the time of measurement of the corrosion rate3.
- Long-term corrosion: Using coupon weight loss method, adapting to various materials and dimensions according to specific needs. will give a corrosion rate value (MPY), based on the
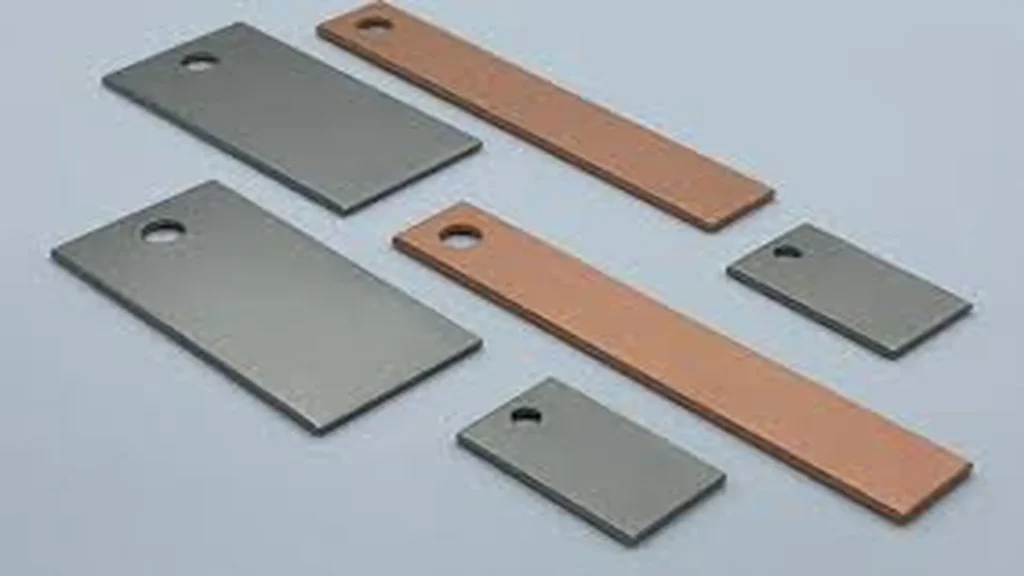
The weight loss technique is the simplest and best known of all corrosion monitoring methods. This technique is based on the exposure for a given time of a sample (coupon) of the same material of the monitored structure, in the same corrosive environment to which the structure is exposed. The measurement obtained from the coupons when analyzed is the weight loss that occurs in the sample during the period of time to which it has been exposed, expressed as corrosion rate.
The simplicity of this measurement is such that the coupon monitoring technique is the basic method used in many corrosion inspection programs. This technique is extremely versatile because weight loss coupons can be fabricated from any commercially available alloy. In addition, by using the appropriate geometric design, a wide variety of corrosion phenomena can be studied.
2. Short-term or instantaneous corrosion: Use of electrical resistance or linear polarization probes to evaluate short-term corrosion, providing instantaneous results for fast actions.
Electrical resistance (ER) specimens can be considered “electronic” corrosion coupons. Like coupons, E/R specimens provide a measurement of the metal loss of an element exposed to a corrosive environment, but unlike coupons, the magnitude of the metal loss can be measured at any time, at any frequency required, while the specimen is in-situ and permanently exposed to the process conditions.
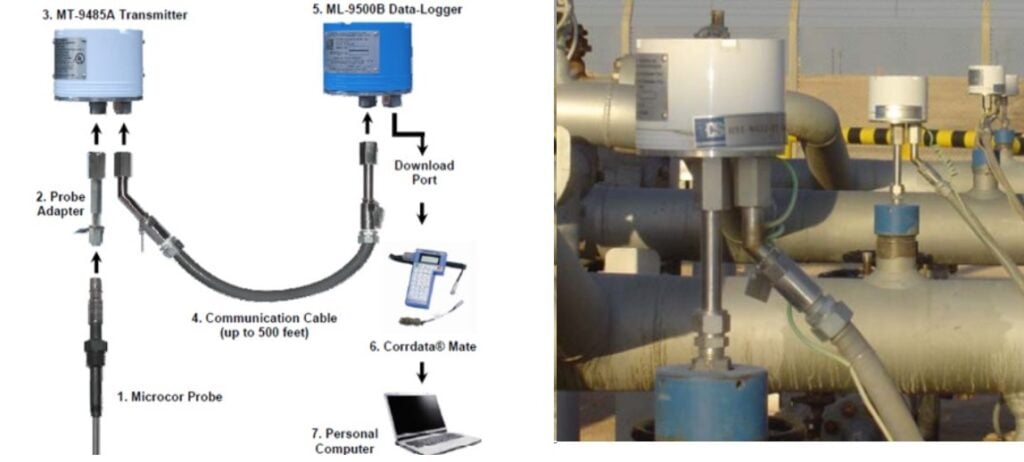
Accurate diagnosis and effective control:
- Identification of specific problems: Detailed diagnosis of particular corrosion problems, identification of underlying causes and determination of control parameters, such as pressure, temperature, pH and flow rate.
- Evaluation of prevention/control techniques: Effective measurement of the effectiveness of the corrosion prevention and control techniques applied to the system.
Wide pressure range:
These systems are configured to cover a wide range of pressures, spanning up to 6000 psi. This capability ensures that the equipment is versatile and able to adapt to a wide range of operating environments, from standard conditions to high pressure applications.
Corrosion monitoring systems not only ensure the prevention of costly damage, but are also ensuring effective asset management, with key information to maintain the integrity of your plant efficiently and cost-effectively to keep facilities in optimal operating condition. .
3.- Online corrosion monitoring equipment
Non-invasive systems to monitor corrosion using software for analysis and interpretation of remote data and solutions (figure 4,a,b,c) 4. “
Online Corrosion Monitoring: Online monitoring systems are designed to deliver your data, it is the simplest and most cost effective method for the needs. Offers an integrated remote process monitoring solution.
Cellular Corrosion Monitoring: For more remote locations, we offer flexible cellular and satellite options. Data can be sent from our range of instruments directly to your networked DCS, a cloud-hosted dashboard, email notifications, SMS and coordinates, GPS.
Database: Software available on the web for storing information or from any device connected to the Internet. For analysis of coupons, test tube data, non-intrusive pressure and temperature sensors and alarm programming by email and SMS
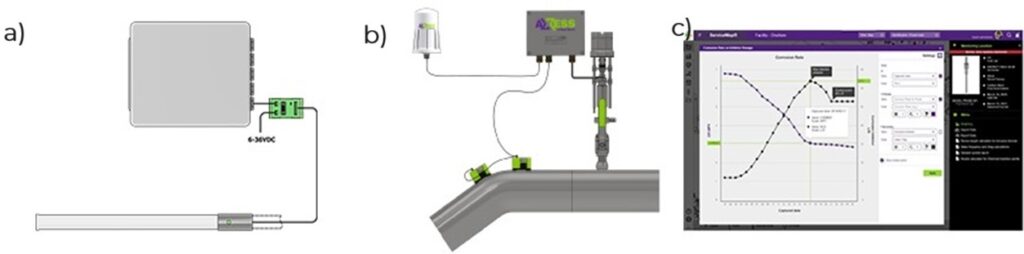
Importance of corrosion monitoring
Corrosion monitoring is essential to provide timely alerts on material degradation, allowing timely implementation of control strategies. This approach not only reduces the costs associated with major repairs, but also contributes to maintaining safe operations, avoiding potential adverse consequences.
It facilitates the optimization of maintenance programs by allowing precise interventions based on the actual condition of materials. This results in a more efficient management of resources and a significant extension of the useful life of assets, maximizing the initial investment.
Corrosion monitoring is not only an advanced technical practice, but a safeguard for sustainability, safety and efficiency in various industries. Its rigorous implementation not only preserves assets and resources, but also contributes to the development of safer and more sustainable operations in the long term.
Conclusions
Technologies for monitoring internal corrosion in industrial pipes represent a fundamental pillar in the efficient and safe management of assets in various sectors. These advanced techniques not only offer the ability to accurately detect and evaluate corrosive processes, but also provide advantages by enabling the implementation of preventive strategies.
The implementation of advanced systems, such as ultrasonic thickness gauges and specialized data analysis, not only allows proactive monitoring of potential damage, but also enables efficient planning of maintenance activities, thus reducing the risk of unscheduled downtime and optimizing operational resources.
The adoption of corrosion monitoring technologies not only raises safety and reliability standards in industrial facilities, but also contributes to operational efficiency and long-term sustainability. The ability to anticipate and address corrosion problems in a timely manner not only protects investments, but also promotes more responsible and sustainable practices in the management of industrial infrastructures.
References
- Corrotex, “Internal corrosion monitoring” consulted on November 12, 2023, https://corrotek.cl/service/monitoreo-de-corrosion-y-seguro/
- Morken Group, “Asset monitoring and control” Accessed November 12, 2023, https://morkengroup.com/monitoreo-de-la-corrosion-e-inyectores-quimicos/
- Dichem, “Corrosion monitoring equipment” Accessed November 13, 2023. http://www.oisa.com.ec/equipos-para-monitoreo-de-corrosion.html
- Integral Solutions, “Corrosion Monitoring”, Accessed November 14, 2023, https://vcsolucionesintegrales.com/productos-corrosion/