In the field of industrial infrastructure, the service life and reliability of Aboveground Storage Tanks (ASTs) are critical. Ensuring the structural integrity of tanks is a critical aspect of maintenance, and corrosion mapping plays a significant role in this regard.
This paper discusses the state-of-the-art Guided Wave Beam Formation in Phases (GWPA) methodology for corrosion mapping in AST bottoms, offering insight into the future of tank integrity assessment.
The challenge of corrosion at the bottom of ASTs
Aboveground Storage Tanks are exposed to a multitude of environmental factors, making them susceptible to corrosion over time. The bottoms of these tanks, in particular, face the constant threat of deterioration due to the corrosive nature of the stored substances, moisture and external elements. Detecting and addressing corrosion in its early stages is imperative to avoid catastrophic failures and environmental hazards.
The evolution of corrosion mapping techniques
Traditionally, corrosion inspection on ASTs involves non-invasive methods such as visual inspection or the use of ultrasonic thickness gauges, and for greater coverage MFL which involves the use of a scanner which involves moving the equipment over the entire surface of the equipment. While these methods have proven to be effective to some extent, they often do not provide comprehensive, real-time data, especially in large tanks with complex geometries.
Advanced non-destructive testing technologies, such as “Phase Guided Wave Beamforming”, have revolutionized the corrosion mapping landscape. This methodology uses guided ultrasonic waves, allowing inspection of large areas of tank bottoms with high accuracy and from one location.
Understanding Phase-Guided Wave Beamforming
Phase Guided Wave Beamforming involves the generation of ultrasonic waves that travel along the surface of the tank bottom. These waves are strategically controlled and manipulated by arrays of phased array beamforming transducer elements, allowing precise mapping of material thickness and integrity, detecting areas of corrosion problems for corrosion control and mitigation.
These probes generate radar-like scans on plates and casings. Beam steering algorithms are used to create a focal beam, which can be automatically swept around the plate to detect wall loss, cracks and structural features. Instead of using a C-scanner for which the entire floor surface has to be swept, which involves time-consuming inspection of the structure, a quick evaluation can be performed from a single position with these probes.
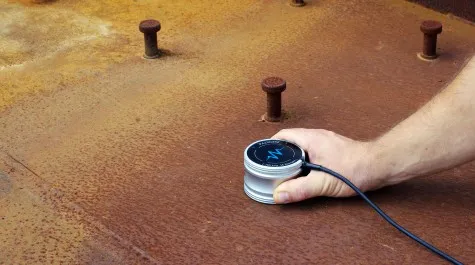
(Source: Guidedwave/Innovations Company)
As mentioned, one of the main advantages of this technique is its ability to cover large surface areas efficiently. Unlike traditional methods that can be time consuming and labor intensive, Guided Wave Phased Array Array (GWPA) provides a quick and comprehensive assessment of corrosion levels by mapping a large area of the tank bottom from one position, allowing for proactive maintenance strategies.
There are variants of the guided wave test in which phased array transducers are also used to scan smaller areas unidirectionally, but with better accuracy, such as short-range guided waves (SRUT).
An example of this technique is shown in the following video, courtesy of Guidedwave/Innovations Company.
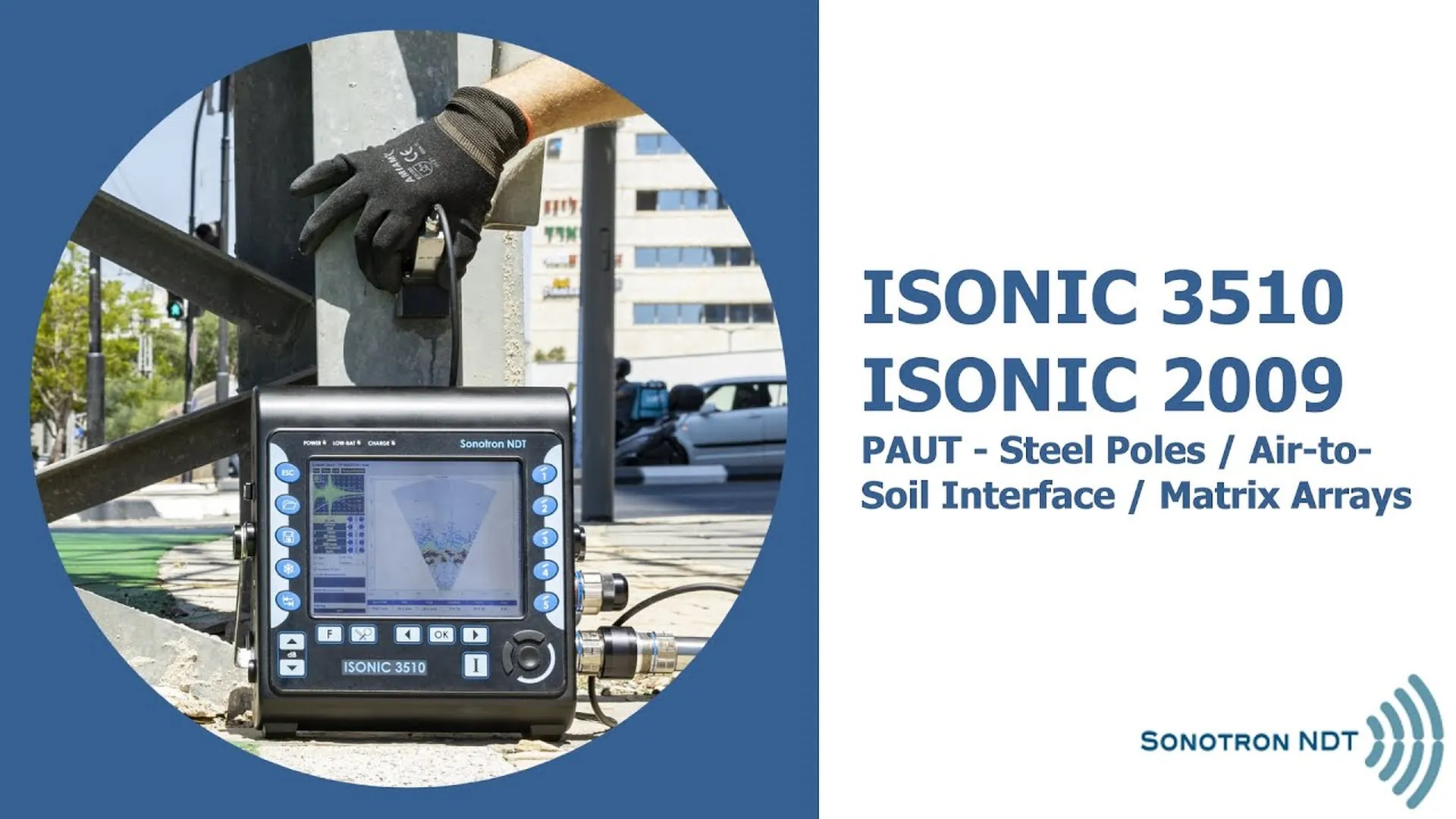
Benefits of Phase Guided Wave Beam Formation in Corrosion Mapping
- Comprehensive Coverage: Phase Guided Wave Beamforming ensures thorough coverage of the tank bottom, leaving no area uninspected. This holistic approach significantly improves the reliability of corrosion mapping results.
- Real-time data acquisition: The technique provides real-time data, allowing operators to quickly identify and address corrosion problems as they arise. This proactive approach minimizes downtime and reduces the risk of unexpected failures.
- Ability to inspect under coatings and in concealed areas: Does not require the removal of corrosion protection layers, which would substantially increase the cost of the test.
- Not sensitive to liquids on any of the plate surfaces: Dry surfaces are not necessary for the application of the test.
- Structural Health Monitoring (SHM): It is applicable to monitor the component over time and detect corrosion activities in the gestation phase.
Future perspectives
As industries continue to evolve, so do the technologies that support them. Phase Guided Wave Beamforming represents a significant advance in corrosion mapping for AST bottoms, providing insight into the future of tank maintenance.
With continued advances in sensor technologies, data analysis and artificial intelligence, the integration of Phase Guided Waveforming with these innovations promises even more sophisticated and efficient corrosion assessment methodologies.
Conclusion
In conclusion, the future of corrosion mapping for Aboveground Storage Tank bottoms looks promising with the advent of Phase Guided Wave Beamforming. The combination of comprehensive coverage, real-time data acquisition, ability to inspect beneath coatings and in concealed areas, structural health monitoring (SHM), among others, makes this advanced technique a cornerstone for ensuring the structural integrity and longevity of ASTs. As industries embrace these technological advances, the tank maintenance landscape is poised for a transformative journey toward greater safety and reliability.
References
- GUIDEDWAVE. Guided wave phased array plate/shell inspection system (beta); Accessed January 30, 2024. https://www.gwultrasonics.com/product/guided-wave-phased-array-for-plates-and-shells/
- HONGCHEN MIAO A, FAXIN LI. Shear horizontal wave transducers for structural health monitoring and nondestructive testing: A review; Accessed January 31, 2024. https://www.sciencedirect.com/science/article/abs/pii/S0041624X21000032
- PACIFIC NORTHWEST NATIONAL LABORATORY. NDE Technology Development Program for Non-Visual Volumetric Inspection Technology; Accessed January 21, 2024. https://www.pnnl.gov/main/publications/external/technical_reports/PNNL-26603.pdf