Table of Contents
- Introduction
- What is orbital welding, and how does it work?
- Process characteristics
- Operating principles
- Starting the welding process: Activate the system to start automated orbital welding
- Common applications of orbital welding in different industries
- Recent advances in orbital welding technology
- Preventive maintenance of orbital welding machines
- Regulations and standards governing orbital welding
- Advantages
- Limitations
- Conclusion
- References
Introduction
Orbital welding is a high-precision automated technique used to perform critical services in various industrial sectors due to its ability to produce consistent and superior quality joints. This article discusses this welding process, its applications, recent technological advances and the regulations that apply to its good performance, highlighting its relevance in critical environments such as the aerospace, pharmaceutical, food and energy industries.
What is orbital welding, and how does it work?
It is an automated welding process that uses the same principles as TIG (Tungsten Inert Gas) welding and is specifically designed to make high precision joints in tubes, pipes and circular shaped components. This method uses specialized equipment that moves the electrode (tungsten) along with the consumable wire and shielding gas, around the object to be welded in a circular path, achieving a uniform and consistent joint.Process characteristics
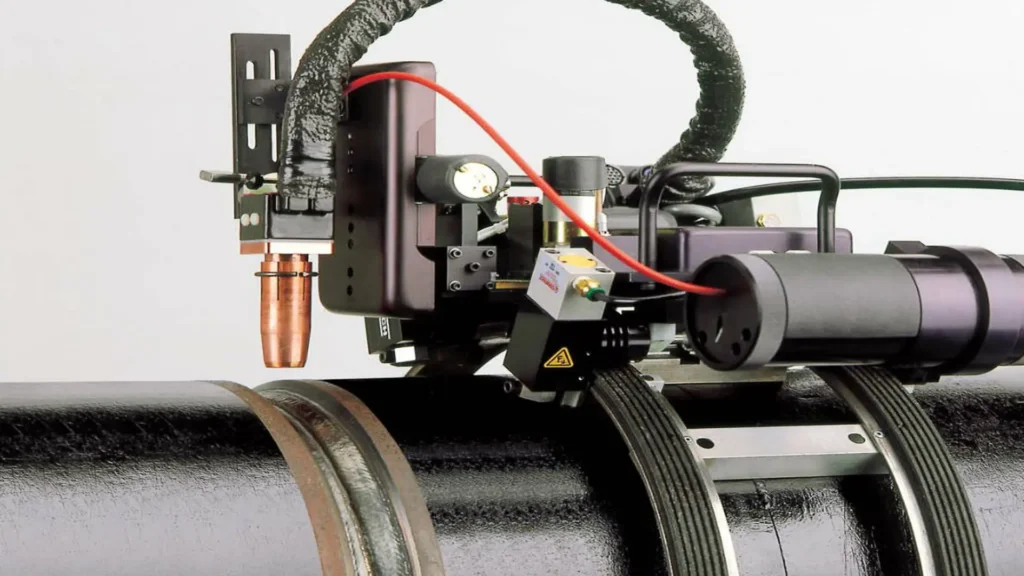
Process characteristics
- Full automation: Being fully automated, manual intervention is minimized, which significantly reduces human error.
- Precise control: Key welding parameters, such as speed, current and voltage, are automatically managed, ensuring consistent welding results.
- High repeatability: Perfect for projects that demand a high volume of consistent, high quality welds.
- Defect-free application: Its precision ensures minimization of common defects such as porosity, cracks or lack of penetration.
Operating principles
The orbital welding process automates the movement of the electrode for high quality and precision welds. It is used primarily in applications where quality standards are critical, such as the pharmaceutical, food, aerospace, and energy industries. The process is detailed below.
- Cleaning: Clean the surfaces to be welded to remove rust, grease, paint or any other contaminant.
- Tube cutting and preparation: Ensure that the ends of the tube are accurately cut and beveled (if applicable) for a perfect fit.
- Alignment: Align the pipes so that there are no unevenness or gaps between the pieces.
- Orbital head: Choose the orbital head compatible with the tube diameter.
- Shielding gas: Select a suitable shielding gas (such as high purity argon) to avoid contamination of the weld pool.
Welding parameters configuration and control
Orbital welding requires precise parameter settings to ensure a uniform and high quality weld. The main parameters to be set are described below:
- Welding current (amperage): It is adjusted according to the thickness of the base material and the diameter of the electrode. High amperage produces greater penetration, but may cause defects such as burns in thin materials.
- Arc voltage (voltage): Influences the length of the electric arc. Adequate voltage ensures a stable molten pool.
- Type of current: Direct current (DC) is common in materials such as stainless steel and nickel alloys, and alternating current (AC) is used for welding such as aluminum.
- Pulse frequency: Controls the heat cycle, reducing deformations and improving penetration in delicate materials.
- Spindle rotation speed: The orbital speed determines the time the electrode remains over each point of the joint. It should be adjusted according to the pipe diameter and material thickness.
- Shielding gas: The gas, usually argon or argon/helium mixture, protects the arc from contaminants during welding.
- Gas flow: Generally measured in liters per minute (L/min). Low flows can cause contamination, while high flows generate turbulence.
- Feeding of the filler material: The wire feed speed is set, synchronized with the spindle rotation speed and current.
- Programming the welding cycle: In this cycle, the number of strokes is programmed according to the thickness of the joints.
- Orbital head assembly: Install the orbital head around the tube, making sure it is tight and aligned. Connect the head to the control system to automate the rotational movement.
- Preliminary tests: Perform the following initial tests:
- No-arc simulation: Run a test without producing an arc to verify head alignment and operation.
- Fine adjustment: Correct any misalignment and adjust welding parameters if necessary.
Starting the welding process: Activate the system to start automated orbital welding
Control and monitoring: The following controls should be carried out
- Monitor in real time the welding through the control system, verifying that there are no interruptions in the power supply or in the movement of the head.
- Ensuring that shielding gas flows before, during and after welding to avoid oxidation.
- Finishing and cooling: Once the weld is completed, allow the material to cool in a controlled manner.
- Quality inspection: Perform visual inspection of the finished weld to identify surface defects and then apply non-destructive testing (NDT) methodologies or techniques such as X-ray, ultrasonic or liquid penetrant inspection to ensure the integrity of the weld.
- Final cleaning: Remove any residue that may have remained on the surface of the weld.
Common applications of orbital welding in different industries
- Aerospace industry: In the aerospace sector, where precision is critical, orbital welding is used to join materials such as titanium and light alloys. These materials are common in aircraft structures and hydraulic systems due to their strength and low weight.
- Pharmaceutical, food and beverage industry: The pharmaceutical industry demands sanitary and contamination-free joints in its piping systems. Orbital welding technology is ideal for achieving this goal, ensuring smooth internal surfaces and avoiding bacterial build-up that could compromise sterility, which meets ASME BPE acceptance criteria.
- Energy and oil sector: In the energy sector, this technique is used in high-pressure and fluid conduction systems. The quality of the joints made with orbital welding machines gives an extra guarantee to withstand extreme conditions, including high temperatures and pressure.
- Metalworking industry: In this building area it is widely used in the welding of pipes and their accessories and especially for the welding of plates with tubes for the manufacturing of heat exchangers and boilers.
The following video shows how to make an orbital weld for tube-to-tube joints. Source: Orbitalum Tools GmbH2.

Tube-to-tube-sheet orbital weld head TX.
Recent advances in orbital welding technology
- Automation and precision control: Recent advances have led to a higher level of automation in orbital welding technology, with systems capable of adjusting parameters in real time. This ensures consistent results even in complex applications.
- Sensor integration and real-time monitoring: The incorporation of advanced sensors allows for in-process defect detection and automatic adjustments, reducing the risk of failure and improving operational efficiency.
- Innovations in multi-process equipment: The latest equipment offers the ability to switch between processes such as TIG, MIG and plasma on the same machine, optimizing both project time and costs.
Preventive maintenance of orbital welding machines
Preventive maintenance is essential to ensure optimum performance, prolong service life and prevent failures during critical operations. This type of maintenance includes periodic inspections, adjustments and cleaning of key components. The main actions to be performed are described below:
- Welding head: Regularly clean the electrode guides and contact surfaces to avoid accumulation of metallic residues or spatter.
- Cables and connectors: Check and clean electrical and signal cables to ensure stable current flow and avoid interruptions.
- Cooling systems: Cleaning of water lines and coolers to prevent blockages that can cause overheating.
- Power supply: Check the condition of internal circuits, control panels and power supply systems for loose connections, loose or damaged components.
- Sensors and control systems: Check that the temperature, current and speed sensors are working properly, as they are critical to the process accuracy.
- Displays and controls: The operation of the user interfaces should be verified, and the necessary configurations adjusted.
- Guides and bearings: Lubricate and check the condition of moving parts to avoid wear that may affect the accuracy of the orbital head.
- Arms and supports: Inspect the fastenings and adjustment mechanisms to ensure a secure hold during the process.
- Electrodes and torches: Evaluate the condition of the consumables and replace them if worn or damaged.
- Cooling system check: Check coolant levels and cleanliness of ducts. Identify possible leaks or blockages in the system.
- Periodic calibration: Perform regular calibrations to ensure that welding parameters, such as current, voltage and rotational speed, meet manufacturer’s specifications and project needs.
- Recommended frequency: The frequency of preventive maintenance may vary depending on the intensity of use and the operating environment. However, it is recommended at least every 500 hours of operation.
Regulations and standards governing orbital welding
The orbital welding process is supported by a set of international standards that guarantee quality, precision and safety in its application. Among the most important is ISO 14732, which establishes the requirements for the qualification of operators and adjusters of automated welding equipment, ensuring that the personnel in charge have the necessary skills to handle this type of advanced technology. Likewise, since it is a welding process, all the standards that regulate quality, procedures, all the welding standards and procedures that guarantee the quality, safety and efficiency of welded joints, such as ASME Section IX and API 1104, are applied.
On the other hand, ISO 9606 and ISO 15614 standards complement this process by establishing guidelines for welder qualification and specific procedures for metallic materials. These standards ensure that welds meet the quality standards required in highly regulated industries such as the pharmaceutical, aerospace and food industries, where orbital welding is widely used.
Advantages
- Consistency: The welds are repeatable and uniform, reducing defects.
- High precision: Ideal for small diameters and critical joints.
- Increased process speed and efficiency.
- Automation minimizes human intervention, improving safety.
- Reduced waste due to efficient use of material and less need for rectification.
- Versatility for unique applications, such as a part that cannot be rotated, has poor visibility or is in an area that is difficult to access.
Limitations
- High initial cost: Orbital welding equipment is expensive.
- Strict preparation: Requires meticulous alignment and cleaning.
- Not suitable for all geometries: Designed primarily for cylindrical objects.
Conclusion
Orbital welding represents an innovative and efficient solution for various industrial applications that require a high level of precision and consistency. Technological advances in automation and monitoring have further expanded its scope, while international standards such as ISO 14732 ensure the quality and safety of the process. Driven by its ability to make reliable joints in critical environments, this technique continues to be a mainstay in demanding industries such as aerospace, pharmaceuticals and energy.
References
- https://www.demaquinasyherramientas.com/soldadura/soldadura-orbital-que-es
- https://www.youtube.com/watch?v=l4zCL8uU51s