Introduction
Maximizing efficiency in rotating equipment is a fundamental element in various industries. Efficient rotating equipment leads to cost savings, extended equipment life, improved safety, increased productivity and better resource management.
For example, energy-efficient motors can improve system performance, reduce energy consumption and lower operating costs. Predictive maintenance techniques are crucial for detecting potential failures in rotating equipment, which in turn leads to increased reliability, minimizing downtime and improving safety.
Transforming the monitoring of rotating equipment
Rotating equipment, such as fans, pumps, compressors and turbines, represent critical components in a variety of industries, from manufacturing to power generation. However, as mechanical machinery, their inherent complexity makes them susceptible to failure.
Due to cost considerations, monitoring and predictive maintenance is often limited to the most critical rotating equipment, while less critical equipment often receives less attention.
To address how to diagnose and prevent failures in widely used but less critical rotating equipment, such as compressors or pumps, among others, ABB1 conducted a practical study. They adapted sensor technologies, machine learning and a software solution based on key indicators of the current status of the equipment to a pilot installation, as shown in figure 1.
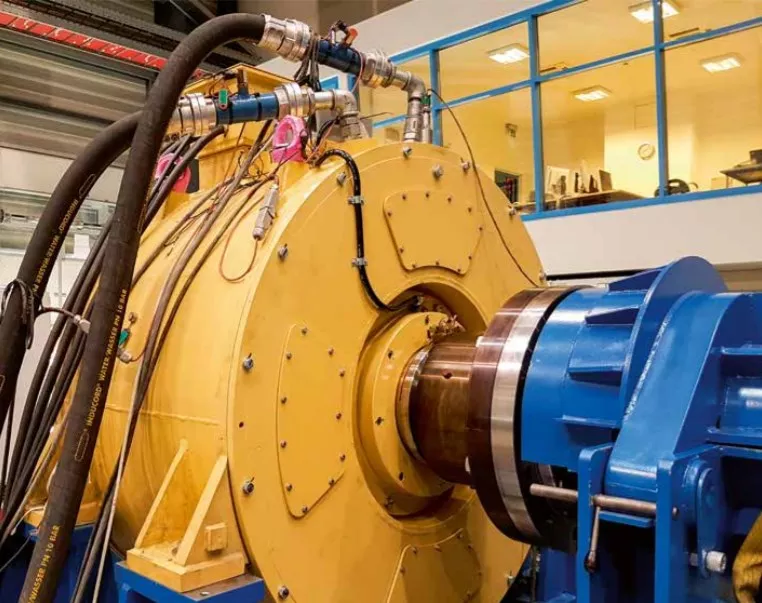
Vibration data was collected several times a day from 30 pumps, using a network of IoT devices to obtain data, the analysis of which provides important information. The tests applied with advanced technology allowed early detection of faults, achieving safe and reliable results in anticipation of potential failures, as well as reducing the time required to repair the asset.
Maximizing efficiency in rotating equipment: factors, challenges and solutions
Factors affecting efficiency
- Design: It is important to evaluate the design of rotating equipment and its components such as impellers, bearings, bearings and seals.
- Material selection: Suitable materials must be chosen for components to ensure durability, minimize friction and optimize performance.
- Maintenance practices: Periodic maintenance routines, including lubrication, alignment and balancing, should be performed continuously to preserve efficiency over time.
- Operating conditions: Factors such as: temperature, pressure, speed and load can impact the efficiency of rotating equipment and the challenges associated with operating under varying conditions.
- Environmental factors: The impact of environmental conditions, such as humidity, corrosion and contamination, must be evaluated, as they affect the efficiency and useful life of rotating equipment.
Challenges to optimize efficiency
- Demanding operating environments: Raise challenges and strategies, such as those present in oil rigs, marinas, chemical plants and mining operations, to overcome them.
- Infrastructure in an advanced state: It is necessary to consider the difficulties associated with maintaining efficiency in aging rotating equipment and the importance of modernization, renovation or replacement.
- Energy consumption: In order to balance efficiency improvements with energy conservation efforts it is significant to continuously analyze the energy consumption of rotating equipment.
- Reliability and safety: It is necessary to ensure reliability and safety in rotating equipment in order to optimize efficiency and safety in the processes.
Solutions to optimize efficiency
- Cutting-edge technologies: The use of advanced technologies such as condition monitoring and digital twins, integrated with preventive maintenance, can improve efficiency and minimize downtime.
- Performance improvement strategies: It is essential to include component redesign, material improvement, implementation of best maintenance practices and optimization of operating parameters.
- Training and skills development: The importance of providing training and skills development programs for operators and maintenance personnel to ensure proper operation and maintenance of rotating equipment.
- Sustainability initiatives: Sustainability initiatives, such as reducing carbon footprint and minimizing resource consumption, can drive efficiency improvements in rotating equipment.
Strategies for maximizing efficiency through asset optimization
Improving the design and implementation of predictive maintenance programs can significantly contribute to the optimization of rotating assets to maximize efficiency in a variety of technical ways:
- Reduced downtime: Through predictive maintenance, early detection of potential problems or failures in rotating assets is achieved, allowing maintenance to be scheduled proactively during planned downtime periods. This minimizes unplanned downtime and maximizes asset uptime.
- Optimization of maintenance intervals: In contrast to static maintenance schedules, predictive maintenance programs adapt to the actual condition of the equipment, allowing maintenance tasks to be performed only when necessary. This flexibility reduces unnecessary downtime and optimizes maintenance intervals to maximize asset efficiency.
- Maximizing asset efficiency: By monitoring key parameters and signals indicative of asset condition in real time, predictive maintenance programs provide valuable information to identify trends, patterns and anomalies. This allows operators to take proactive actions to optimize asset performance and efficiency.
- Advanced equipment condition monitoring: Through advanced technologies such as vibration analysis, thermography and oil analysis, predictive maintenance programs allow continuous assessment of asset condition. This detailed monitoring enables early detection of wear, degradation or impending failures, facilitating timely interventions to avoid costly breakdowns and maintain optimal asset efficiency.
- Cost optimization: Implementing predictive maintenance programs leads to savings by reducing costs associated with reactive or preventive approaches. By focusing resources on specific problems identified through predictive analytics, maintenance spending is optimized while maximizing the reliability and efficiency of rotating assets.
- Extending asset life: Proactively addressing potential problems through predictive maintenance helps extend the life of rotating assets. By identifying and resolving factors that contribute to wear and degradation at earlier stages, you minimize the risk of premature failure and ensure that assets operate at maximized efficiency for longer periods of time.
Conclusions
Each rotating equipment component demands particular operating and maintenance protocols to ensure its continued efficiency and reliability. Given their importance in manufacturing processes, their correct operation is vital to the success of various industries. Despite their crucial role, being mechanical systems, they are susceptible to potential complications.
Poor maintenance practices can lead to failure of rotating equipment, even those of robust construction. The absence of regular inspections, insufficient lubrication or postponement of maintenance tasks can result in premature failures and unplanned downtime. The implementation of predictive maintenance and condition monitoring strategies can mitigate these issues.
Despite the challenges inherent in rotating equipment, identifying and adopting preventive measures can significantly mitigate their negative impact. Regular maintenance, constant training and the use of advanced monitoring tools are critical aspects to address these challenges and ensure the durability and maximizing the optimal efficiency of rotating equipment.
References
- ABB; “Transforming condition monitoring of rotating machines”; 2019-06- 17; https://new.abb.com/news/detail/25556/transforming-condition-monitoring-of-rotating-machines; accessed 01 -03-2024.