Autor: Ing. Euclides Quiñonez, 5 agosto 2023
Introduction
The operation and maintenance of a gas pipeline constitute necessary tasks to guarantee a safe and efficient supply of natural gas. These systems designed to transport gas, safely, from the production areas to its final destination, represent a highly important infrastructure in the gas supply chain, which is used for a variety of industrial applications, power plants, commercial and residential.
It is important to maintain a constant and safe flow to avoid interruptions that may affect the operation and savings of users and facilities. This denotes the great importance that must be given to the proper operation and maintenance of gas pipelines, applying the best practices and the necessary technologies to ensure their integrity, reliability, efficiency and continuous flow during their useful life cycle.
What is a gas pipeline?
Let’s start by defining a gas pipeline, which is a system of pipes of different diameters, used to transport gas from production wells to storage yards, industrial or residential facilities, for shipment at docks or across borders to export the product to different countries. countries. This process also includes three different types of systems which are:
- Collection: Collection of gas from production wells to facilities
- Transmission: They transport natural gas from facilities to ports, refineries, and cities across the country.
- Distribution: They consist of a large network that distributes the product to homes and businesses.
- General characteristics of gas pipelines
- Pipelines for these systems are built above ground, submerged in water, or buried 1.0 to 2.0 meters underground.
- Materials used: Gas pipelines are generally made of carbon steel, but distribution pipes are increasingly using plastics or compounds.
- Coating and Protection: For external corrosion protection of buried pipelines, various types of coatings are used, the most common being fusion-bonded epoxy or polyethylene heat shrink sleeves. For submerged pipes, cathodic protection, inhibitors and industrial coatings, and for pipes above ground, paint systems are used that are selected depending on the corrosiveness of the environment (Figure 1).
- Dimensions: The thicknesses, diameters and lengths depend on the purpose, the pressure, the flow and the distance between the production areas and the storage and distribution areas. To get an idea of a high-capacity gas pipeline, the longest in the world, is the Nord Stream 1 that runs from Russia to Germany, 1,224 km long, 48″ in diameter, 220 Bar pressure and a capacity of 55,000 million annual m3 of natural gas and the recently inaugurated Nestor Kirchner in Argentina is 573 km long, 36″ in diameter and a maximum square of 7,665 million m3 a year. In another word. The higher the pressure, the thicker, for a higher flow rate, a larger diameter.
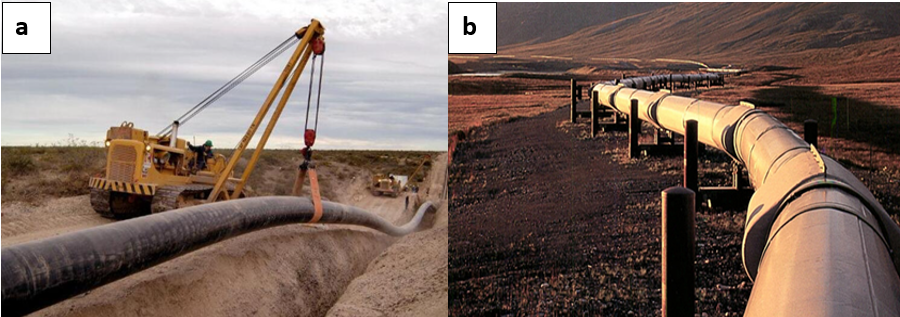
Gas pipeline risks
Gas pipelines are systems installed in different environments, each one with its very particular characteristics, such as pipes submerged in the sea, buried underground or exposed to the external air environment that cause different corrosion damage or mechanical damage to materials.
The most common risks are:
- Leaks and Explosions: A critical safety risk in the operation of gas pipelines is the possibility of gas leaks. These leaks can be dangerous if the gas accumulates in confined areas and combines with an ignition source, which could result in an explosion or fire (Figure 2).
- Supply Interruptions: Any interruption in the operation of a gas pipeline can cause problems in the supply of gas to communities and industries. This can affect heating, electric power generation and other processes that depend on gas.
- External Damage: Gas pipelines often traverse populated areas and diverse terrain. They can be damaged by corrosion, unauthorized excavation, nearby construction, or natural disasters such as earthquakes, floods, and landslides, with the consequences of safety risks and loss of continuous flow.
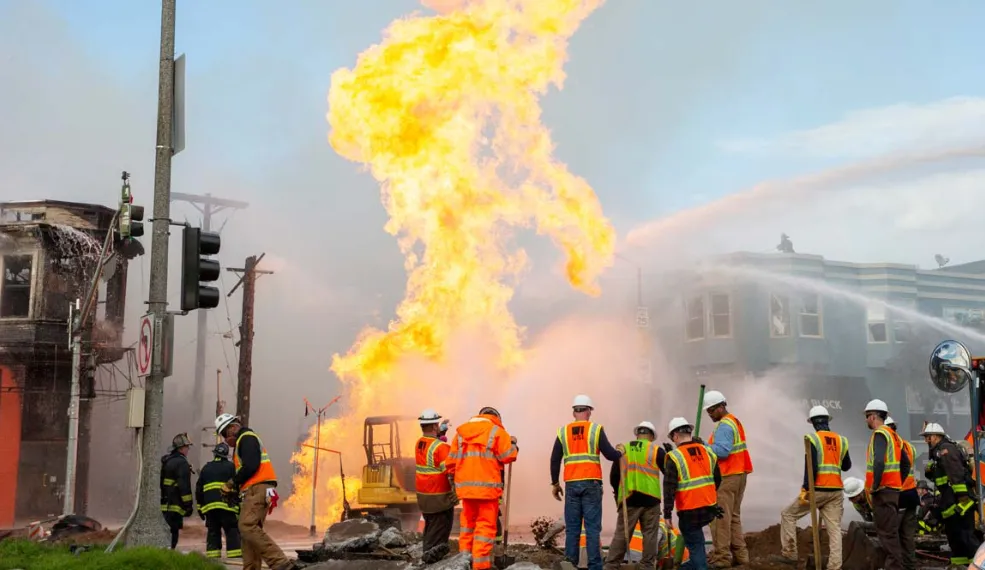
Operation and maintenance of a gas pipeline: How to avoid failures?
There are several mechanisms and methodologies that can be applied to minimize failures in gas pipelines, such as the following:
- Preventive maintenance: The durability and operational reliability of gas pipelines depends significantly on this type of maintenance; which implies scheduled inspections, non-destructive tests and integrity evaluations , repair of protective coatings, cleaning of the pipeline and the elimination of corrosion. Remote inspection technology, ultrasonic inspection with instrumented tools (Smart Pig) to measure thicknesses, autonomous robots, allows reaching difficult-to-access areas and evaluating the condition of the gas pipeline without interrupting its operation. To carry out all of the above, preventive maintenance plans, operation plans and frequent non-destructive inspections of the facilities must be prepared.
- safe operation: The operators of the gas facilities are responsible for and custodian of said facilities, therefore, they must know in detail and be trained to operate the equipment and accessories correctly and safely (Figure 3), controlling the operational variables of the systems, to avoid deviations that can cause failures. Likewise, teams must work with maintainers and inspectors so that inspection and maintenance plans are met.
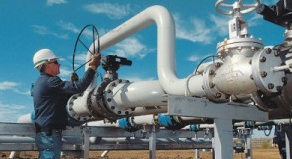
- Constant monitoring: Continuous monitoring is essential to detect any abnormality in the operation of the gas pipelines. Monitoring technology includes sensors distributed along the pipeline to measure pressure, temperature and other operational variables, and mobile gas leak detection equipment. Advanced monitoring systems can detect minute variations in this data and alert operators to potential problems. Real-time data analysis enables fast, informed decisions to avoid disruptions and maintain security.
Apply best practices and technologies
- Considerations from the design: The design of an installation is the fundamental basis to avoid or eliminate possible failure in the future. This is achieved by considering a good selection of materials, coatings and coatings in the design, with the installation of a monitoring system and cathodic protection, among others.
- Advanced Control Systems: Automation and advanced control systems allow for optimization of operation in real time, adjusting gas flows according to demand and changing conditions.
- Tecnologías de detección de fugas: El uso de drones para la detección de fugas de gas es cada vez más popular a medida que la tecnología se vuelve más avanzada y accesible (Figura 4). Los drones son una forma segura y confiable de detectar fugas en áreas de difícil acceso y ofrecen una serie de beneficios sobre los métodos tradicionales. Pueden llegar a sitios de difícil acceso y realizan mediciones precisas de las concentraciones de gas en el aire, lo que los hace ideales para identificar el origen de las fugas de gas. Esto permite una atención rápida y eficiente para evitar daños mayores.
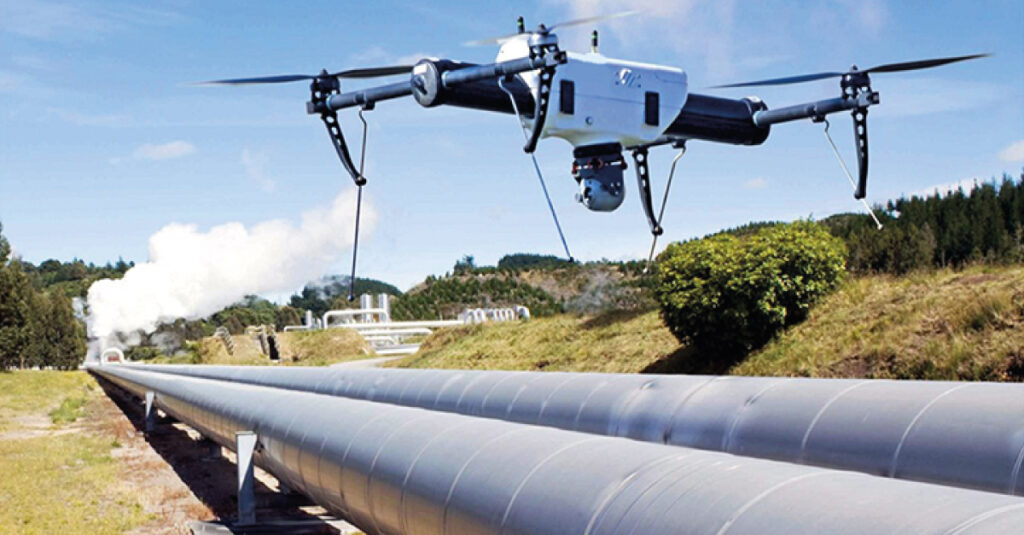
- Corrosion Management: Special coatings and cathodic protection systems in buried and submerged lines prevent corrosion and extend the useful life of the pipeline.
- Predictive Modeling: Use of mathematical models to predict the behavior and wear of gas pipelines, allowing more precise maintenance planning.
- Use reliability methodologies : There are several reliability engineering methodologies such as Reliability, Availability and Maintainability (RAM), root cause analysis (RCA), risk-based inspection (IBR), among others, allow us to prioritize systems and equipment, based on their global impact, understand the origin of failures to eliminate the causes and generate plans based on risk for equipment subject to pressure, among others.
- Incident Response: Despite preventive measures, incidents can occur. Therefore, well-established immediate incident response plans should be developed and available. This includes clear protocols for closing valves, evacuating affected areas, and coordinating with relevant authorities. Regular drills allow staff to be trained in crisis scenarios and improve preparedness for any eventuality.
Conclusion
The operation and maintenance of gas pipelines are necessary to ensure a continuous and safe flow of gas. Constant monitoring, preventive maintenance and effective incident response are essential in this process. Best practices and advanced technologies play a very important role in guaranteeing the integrity of assets and the efficiency of gas pipelines, ensuring their optimal operation throughout their useful life cycle. Likewise, continued commitment to safety and constant improvement are essential to maintaining the reliability of the continued supply of natural gas.