Introduction
In the ever-evolving energy and manufacturing sectors, the demand for safe, reliable and efficient operations has never been greater. Non-destructive testing (NDT) methods have become essential to ensure the integrity of materials and systems in these industries. One advanced imaging technique that is gaining prominence is neutron radiography, with applications in nuclear power, oil and gas (exploration and drilling), and renewable energy, also playing an increasingly important role in manufacturing processes.
By providing high-resolution images of the internal structure of various materials, neutron radiography is transforming the way industries ensure quality, detect faults, and optimize operations.
What is neutron radiography?
Neutron radiography, also known as neutron imaging, is a non-destructive testing technique that uses low-energy neutrons (thermal neutrons) to create detailed images of an object’s internal structure. Unlike X-rays or gamma rays, which interact primarily with denser materials such as metals, neutron radiation interacts more strongly with lighter elements such as hydrogen. This makes neutron radiography especially useful for examining materials that are difficult to inspect with conventional methods.
Neutron radiography can image materials with high hydrogen content such as water, oil, rubber, plastics, and even explosives. Some common sources of neutrons for this technique include nuclear reactors, particle accelerators, and radioisotopes such as Californium-252.
Applications in the energy industry
Atomic energy
In the nuclear power industry, neutron radiography is used to inspect critical components such as fuel rods. A fuel rod, which contains fissile uranium pellets, must have an even distribution of pellets inside it. Any broken or deformed pellets can generate erratic behavior inside a nuclear reactor, which could compromise safety. Neutron radiography allows thorough inspections of these fuel rods without disassembly, ensuring their structural integrity prior to use.
Turbine engine parts
Turbine engines used in power plants and aircraft engines rely on complex cooling channels to maintain safe operating temperatures. Neutron imaging has proven particularly useful for inspecting these cooling channels, as it can detect residual core material or internal imperfections that could affect the performance and lifetime of turbine components.
For this purpose, tracers (labeling method) or isotopes (doping method) are introduced into the channels, both elements with a high neutron cross-section (high neutron interaction probability) that allow to obtain an accurate picture of the cooling systems, helping to prevent overheating or mechanical failure.
In gadolinium contrast labeling, which has an extremely high neutron cross section, a batch of turbine blades is washed in a gadolinium-rich dye solution. The gadolinium can then be rinsed from the blades, except for any amount of dye deposited on ceramic fragments trapped in the cooling channels1. Running the assay yields an image where the condition of the internal cooling channels can be clearly visualized.
Oil and gas
In the oil and gas industry, neutron radiography is used in geological studies to evaluate the behavior of fluids through borehole rock samples. This process is crucial for understanding rock porosity and fluid saturation, both key factors in determining the feasibility of oil extraction.
Using the advanced radiographic technique of Computed Tomography (CT), neutron radiography images are obtained to simulate forced flow conditions of steam, water, or oil through rock samples, allowing engineers to optimize extraction techniques for maximum efficiency.
Green hydrogen
Green hydrogen, produced by electrolysis powered by renewable energy sources, is an emerging solution for sustainable energy. Neutron radiography is an invaluable tool in the inspection of electrolyzers, which are crucial for hydrogen production. By visualizing the internal components of electrolyzers in real time or in near-operational conditions, neutron radiography can detect material defects or inefficiencies in the system. This helps optimize the production process, ensuring reliable generation of green hydrogen and reducing operating costs.
Lithium-ion batteries
Lithium-ion batteries are essential for energy storage in renewable technologies and electric vehicles. This non-destructive radiagraphic method allows the characterization of batteries, providing information on lithium redistribution, electrolyte consumption and gas formation during operation.
Recent studies2 have combined X-ray and neutron computed tomography (CT) to analyze the performance of a Duracell lithium-ion cylindrical cell during discharge. X-ray CT shows internal structural details, differentiating the nickel grid from the current collector (Figure 1a), while neutron CT reveals key electrochemical processes, such as lithium-ion transport and electrolyte decomposition (Figure 1a). Fundamental information for optimizing battery performance and lifetime.
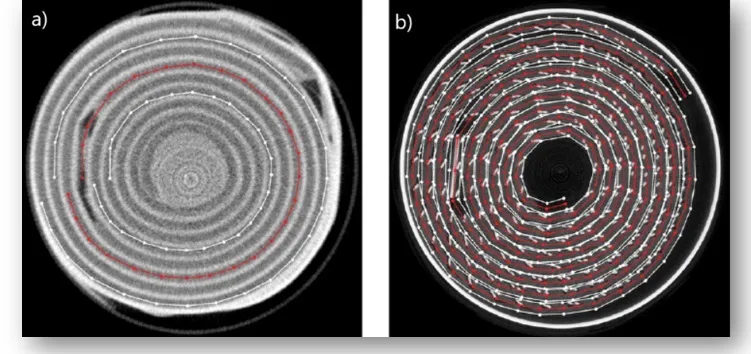
Innovative manufacturing applications
Inspection of components manufactured by additive manufacturing
Additive manufacturing, commonly known as 3D printing, has revolutionized the production of complex components in several industries, including aerospace, automotive, and energy. Neutron radiography plays an important role in the quality assurance of these components. Unlike traditional inspection methods, which can have difficulty penetrating dense materials or complex geometries, neutron imaging can reveal internal defects, such as voids, cracks, or incomplete layers, without damaging the part. This makes it an ideal tool for verifying the integrity of 3D-printed components used in demanding applications.
Submerged Arc Welding (SAW) Inspection
Boron has an extremely large neutron cross section which makes it useful as a contrast agent in neutron imaging, among other things. In the submerged arc welding (SAW) process, the welding flux, which contains large amounts of boron, attenuates neutrons compared to metals such as copper. This makes neutron imaging useful for evaluating the quality of welds and ensuring that no undesirable flux residue remains in a welded part2, thus complementing X-ray or gamma radiography for weld joint quality assessment.
Inspection of military defense components
In the weapons industry, neutron radiography has great application in the quality assurance of munitions, armaments, or components of weapons and defense systems. Neutron radiography can reveal flaws and defects in objects such as ammunition, missile payloads, ejection mechanisms, and other critical components with high failure costs without dismantling them.
Composite materials inspection
Composite materials, which are widely used in the manufacturing industry for their strength and lightweight properties, are difficult to inspect using conventional methods, including radiographic techniques using X-rays or gamma rays. Neutron radiography excels in this application because it can penetrate dense composite structures and, at the same time, reveal internal features that might go undetected by X-rays. This is particularly useful in industries such as aerospace, where the integrity of composite materials is critical to ensure the safety of aircraft components.
Today, composite components are being manufactured by 3D printing, in particular in the aerospace industry, and it has been increasing due to its ability to build complex designs more efficiently and with less waste than traditional subtractive methods. This is where neutron radiography complements X-ray. Applied together, the two can give two halves of the complete image. Neutron radiation is especially useful for boron composite materials due to the high cross-section of boron.
The future of neutron radiography
As industries continue to demand more sophisticated non-destructive testing methods, neutron radiography is destined to play an even more important role in the future. Several key trends are shaping the future of neutron radiography:
- Digital enhancements: Advances in digital detection technology are improving the resolution and speed of neutron radiography, allowing larger volumes and more complex components to be inspected with greater accuracy.
- Portable neutron sources: The development of portable neutron sources is expanding the accessibility of neutron radiography, enabling on-site inspections in industries such as oil and gas, energy, and aerospace.
- Increased automation: Automation of the neutron radiography process is reducing the need for manual intervention, making the technique more cost-effective and scalable for large-scale industrial applications.
- Hybrid imaging techniques: The combination of neutron radiography with other imaging techniques, such as X-ray and infrared, is opening up new possibilities for more complete inspections, particularly in complex systems where multiple types of defects may be present.
Conclusions
As the energy and manufacturing industries face increasing demands in terms of safety, efficiency, and sustainability, neutron radiography is emerging as a revolutionary tool. Its unique ability to provide detailed, non-invasive inspections of critical infrastructure is helping companies operate more safely, reduce costs, and protect the environment.
In the energy sector, neutron radiography is optimizing the inspection of nuclear fuel rods, turbine engine parts, and lithium-ion batteries, while in the manufacturing industry it is ensuring the quality of 3D printed components, welds, and composite materials. As industries continue to innovate and evolve, neutron radiography offers a clear path to safer, more efficient, and reliable operations.
This NDT technique is not just a tool for today: it is an essential component of the future of both energy production and high-tech manufacturing.
References
- WILLOW ASCENZO. Neutron Radiography and Turbine Bladest; Accessed October 15, 2024. https://www.qualitymag.com/articles/96564-neutron-radiography-and-turbine-blades
- Ralf F. Ziesche, y colaboradores; “4D imaging of lithium-batteries using correlative neutron and X-ray tomography with a virtual unrolling technique”; Nature Communications 11, Article number: 777 (2020); https://www.nature.com/articles/s41467-019-13943-3#auth-Ralf_F_-Ziesche-Aff1-Aff2
- PHOENIX. Boron As A Neutron Imaging Contrast Agent; Accessed October 16, 2024. https://www.phoenixneutronimaging.com/insights-and-updates/boron-as-a-neutron-imaging-contrast-agent